Dimpling has become the preferred first step in transmission electron microscope (TEM) specimen preparation for three reasons.
Firstly, it significantly reduces the time needed for final thinning to electron transparency (the time saving is particularly useful when the final polishing step is comparatively slow, as is the case in ion polishing).
Secondly, the electron transparent area will consistently form at the center of the specimen disc, and as a result, less X-ray shadowing will materialize during energy dispersive X-ray spectroscopy (EDS) analysis, and less specimen movement will be seen throughout tilting.
Finally, the thick, supportive rim of material formed during dimpling makes the handling of fragile TEM specimens significantly easier.
Dimpling Ductile Materials
Gatan is frequently asked by its customers to offer procedure guidance for dimpling ductile materials, such as pure metals and solders. The common issue that arises is that the cutting rate is relatively low compared to that achieved with harder materials such as metal oxides and semiconductors.
This is due to the fact that the polishing grit (typically diamond or aluminum oxide) gets embedded in the soft material during dimpling, and then the dimpling wheel is ground away instead of the specimen.
Using cubic boron nitride (CBN) as the polishing compound offers a solution to this problem. CBN particles are rounded in shape and do not embed themselves easily in the materials being polished.
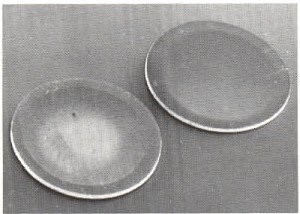
Figure 1. SEM image of a 316 stainless steel TEM specimen disc after grinding (left) and polishing (right) with CBN. Image Credit: Gatan Inc.
Recommended Procedure
Gatan recommends that the starting thickness of the ductile material should be in the range of 100 – 150 µm. Use the model 659 Disc Punch from Gatan to cut 3 mm diameter specimen discs from this material.
Install a 15 mm or 20 mm diameter phosphor bronze wheel onto the model 656 Dimple Grinder, then dimple the 3 mm discs using 4 – 6 µm CBN grit down to a thickness of around 10 µm.
Fit a felt wheel and proceed with polishing, first with 4 – 6 µm, and then with 0 – 2 µm CBN grit until all of the coarse marks formed during grinding by the 4 – 6 µm grit have been eliminated.
Sperm whale oil acts as a good substitute lubricant to prevent the CBN paste from drying out throughout the grinding and polishing steps.
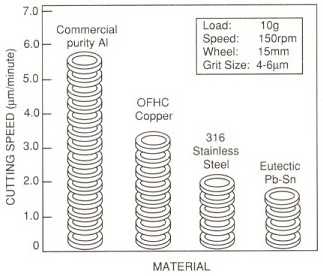
Figure 2. Dimpling rates for some common ductile materials using CBN paste. Image Credit: Gatan Inc.
Measurement of Cutting Rates
Thinning of aluminum, stainless steel, copper and a Pb-Sn eutectic solder was conducted from about 100 to <10 µm with 4 – 6 µm CBN paste, a dimpling load of 10 g, a wheel speed of 150 rpm and a wheel diameter of 15 mm.
The bar graph displays the different cutting rates acquired. The CBN cuts soft materials at about 2 – 6 µm a minute, which is equal to the rate that diamond cuts silicon under comparable conditions.
Gatan offers CBN paste in convenient 5 g syringes.
- 0 – 2 µm CBN: 656-04-010
- 4 – 6 µm CBN: 656-04-01 1
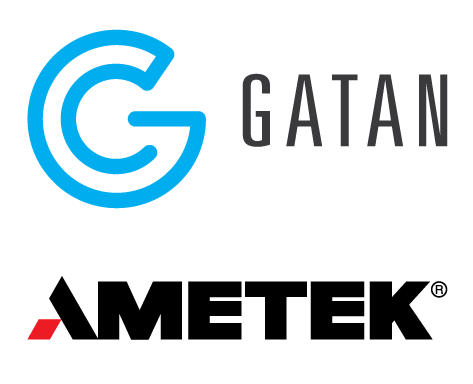
This information has been sourced, reviewed and adapted from materials provided by Gatan, Inc.
For more information on this source, please visit Gatan, Inc.