Sponsored by GGBJan 14 2022
Conventional compressor bearings - for example, leaded-bronze, rolling element or bi-metal bushings - will be significantly affected by wear in marginally lubricated environments at bearing locations within compressor applications.
Utilizing metal-polymers offers a unique advantage due to their self-lubricious nature, as they can be a more reliable solution in those particular environments. They also offer a number of other benefits, including their lead-free nature, facilitating a reduction in noise levels, and decreasing friction when compared to other journal bearings.
The variety of assembly clearances on offer compared to the classic bearing styles is one of the greatest barriers when incorporating metal polymers into the design of an application due to their impact on efficiency levels.
By modifying system design and/or sizing operations to control clearances, metal polymers have been utilized in compressor designs offered to customers. This article outlines a range of differences in metal-polymers versus traditional compressor bearings in terms of system design, structure and performance.
The operation of compressors is heavily dependent on the mix of lubricants and refrigerants in air conditioning and refrigerant systems comprising a range of other parts. In theory, the loads and speeds experienced could result in hydrodynamic lubrication in the majority of compressor applications.
It should be noted that mixed-film and boundary lubrication often arises in a number of circumstances, including:
- The start-up process
- The shut-down process
- Compressor oil "wash out" from gas migration occurring
- A decrease of lubricant viscosity as a result of refrigerant dilution
The length of time in which boundary or mixed lubrication conditions may occur is reliant on the system design utilized to obtain steady-state flow.
The reliability and performance levels of traditional compressor bearings - for example, leaded-bronze, rolling element or bi-metal bushings - are highly contingent on lubrication conditions.
Utilizing boundary and mixed-film lubrication applications allows for contact between mating surfaces and can lead to greater friction and unnecessary wear.
By comparison, metal-polymer bushings possess a vital advantage due to their self-lubricious nature, as contact between mating surfaces does not cause high levels of wear or friction. Metal polymers can facilitate more dependable lubrication options in those specific conditions.
The utilization of metal-polymer bushings has been part of the commercial compressor application sector for around the last two decades but remains a comparatively novel idea for much of the industry.
The commercial achievements of metal polymers involved overcoming specific design hurdles that arose from their differences with classic compressor bearings. This article focuses mainly on metal-polymer differences in relation to system design, structure and performance.
Metal-Polymer Structure
Metal-polymer bushings usually comprise a multi-layer composite structure consisting of:
- A rigid steel backing
- An intermediate – often bronze – mesh or porous layer
- A polymer overlay that has been impregnated onto the intermediate layer
The polymer overlay will usually consist of PTFE (polytetrafluoroethylene) for most compressor applications, along with a range of fillers.
The mixture of PTFE and fillers is what will determine the innate performance properties of the bushing, for example, a metal-polymer bushing with an intermediate layer consisting of porous bronze material (Figure 1).
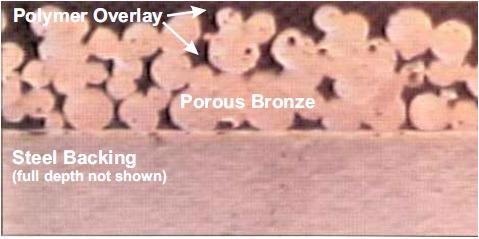
Figure 1. Cross-section of typical metal-polymer bushings. Image Credit: GGB
Metal-polymer bushings are usually produced in a two-step process from a material that has been manufactured in strip form. This strip will include some sort of adhesion of the intermediate layer to the steel backing, as well as impregnation of the polymer material.
The strip form material can be slit and wrapped into a bushing, with the finished dimensions intended to be incorporated by means of a press-fit into the housing in order to obtain a pre-determined installed inner diameter. This type of bushing is known as a split bushing, as unlike a cast bronze or metal bushing, it is not a full cylinder.
The accuracy of the final bushing dimensions is dependent on the manufacturing and measurement capabilities. Normal total tolerance on the final wall thickness of the bushings can be in the range of 20 to 45 μm, dependent on the strip thickness.
This tolerance is for typical parts, though greater tolerance control can be achieved in certain circumstances.
System Design
In the majority of applications, the design of the bearing system is largely determined by the clearance between or within the shaft and bearing surface. In compressors, this clearance can be crucial to efficiency. There are variations in typical clearances when traditional compressor bearings and metal-polymer bushings are compared.
Typical Clearance Range of Metal-Polymers
The surface of the polymer itself is a key element in defining bearing performance. Processing capabilities restrict the extent of the tolerance that can be controlled due to the composite structure.
The accurate formation and measurement of bushing comprised of a bronze steel and polymer composite is not always easy and is constantly being analyzed for improvement.
As of now, machining is not on offer for PTFE based metal polymers.
The slender layer of polymer lying on top of the intermediate bronze structure can be a vital component in the performance potential of the bearing surface. If this layer is machined away, it results in a bronze/polymer matrix which may offer reduced performance when compared to a full polymer surface.
There is a noticeable difference between standard metal-polymer bushings and typical drawn-cup needle bearing clearances (Table 1). The clearances were determined from ISO H7 and N6 shaft and housing fits, though precise clearance range figures may vary depending on the manufacturer.
Table 1. Clearance Range Comparison (µm)
Shaft Size [mm] |
Needle |
Metal Polymer |
Max |
Min |
Max |
Min |
10 |
55 |
10 |
85 |
5 |
20 |
75 |
15 |
115 |
10 |
30 |
75 |
15 |
125 |
10 |
40 |
85 |
20 |
135 |
15 |
50 |
85 |
20 |
160 |
15 |
Bi-metal or bronze bushings are not featured because they usually undergo machining after installation. Clearance can then be kept within a much tighter range as a result.
Higher-precision needle bearings are obtainable where the clearance range has to be decreased. Bi-metal and rolling element bearings can hold tighter tolerance ranges, though this might not be a consideration in applications utilizing metal polymers.
Commercial Compressor Applications
Metal-polymer bushings have been employed in compressor applications for the last twenty years, facilitating improvements in performance and reliability.
There are variations in the clearance ranges utilized for the traditional compressor bearings when compared to the metal-polymer bushings that took their place in reciprocating and axial-plate compressors (Table 2 and Table 3).
Table 2. Reciprocating clearance range comparison (µm). Source: GGB
Shaft Size [mm] |
Bronze |
Metal Polymer |
Max |
Min |
Max |
Min |
40 |
50 |
40 |
115 |
40 |
45 |
55 |
45 |
120 |
45 |
Table 3. Axial-plate compressor clearance range comparison (µm). Source: GGB
Shaft Size [mm] |
Needle |
Metal Polymer |
Max |
Min |
Max |
Min |
17 |
65 |
15 |
90 |
15 |
Each manufacturer will have its own compressor design, so the required clearance ranges may be different. For example, commercial scroll clearances for a given shaft size may have a range of clearances for metal polymers (Table 4).
Table 4. Scroll compressor clearance range (µm). Source: GGB
Shaft Size [mm] |
Customer A |
Customer b |
Max |
Min |
Max |
Min |
28 |
115 |
30 |
140 |
50 |
32 |
120 |
35 |
140 |
50 |
40 |
130 |
45 |
160 |
80 |
Metal polymers can be operated efficiently and effectively at greater clearance ranges than needle or bi-metal bearings. Some have demonstrated that the range must be modified to ensure appropriate performance.
Employing a metal polymer instead of a classic compressor bearing will necessitate analysis to establish the best possible clearance range to ensure the best performance.
Performance
The performance of metal-polymer bushings in compressors depends not on clearance alone but also on the ability of the material to tolerate the temperatures, loads, speeds and levels of corrosive attack which occur in these applications.
Common bearing failures in compressors consist of fatigue, wear and cavitation. Polymer bearing science has facilitated combining fillers in PTFE, allowing metal-polymer manufacturers to produce materials that can handle fatigue and wear to levels that match and even exceed those of traditional compressor bearings.
The self-lubricating nature of the material in boundary and marginal lubricated conditions plays a large role in this. While levels of cavitation resistance are not equal to that of bi-metals, they are sufficient for compressor bearing conditions.
Two samples of PTFE-based metal-polymer and leaded bronze bushing were analyzed to compare their wear resistance (Figure 2). Each of the leaded bronze bushings and one metal-polymer bushing underwent identical testing conditions. The speed and load for the second metal-polymer sample was doubled.
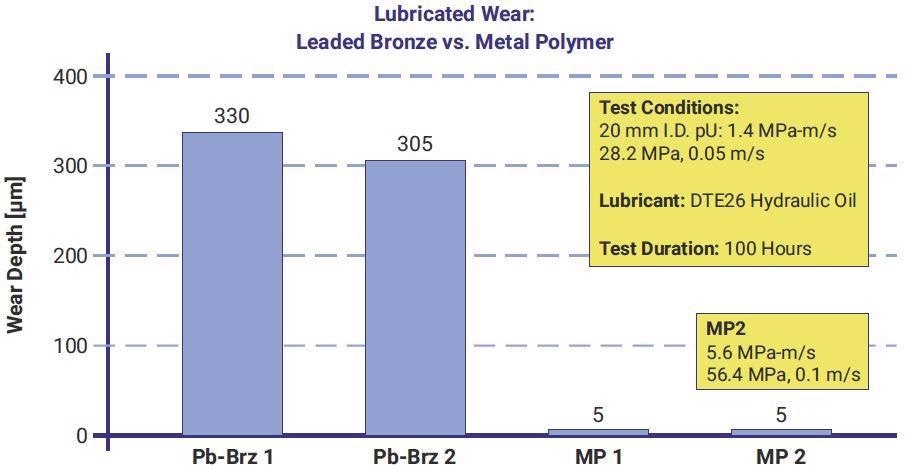
Figure 2. Lubricated wear of leaded bronze vs. metal-polymer bushings with test conditions. Image Credit: GGB
The results indicate that the wear resistance of the metal-polymer bushing was markedly superior compared to the leaded bronze bushing, even at double the speed and load.
Hydrodynamic Lubrication in Metal-Polymer Bushings
Standard hydrodynamic calculations in journal bearings can be employed to assist in establishing film generation and with a variety of other important factors in bearing design.
A unique phenomenon can occur under certain conditions within metal-polymer bushings, where the bearing surfaces have a lower modulus than bronze, bi-metal or steel.
At higher loads, elastohydrodynamic lubrication (EHL) conditions may arise, producing greater film thicknesses when compared to traditional journal bearings in the same conditions.
Compliance of the polymer surface is believed to distribute the load more effectively and to increase the thickness of the film.
It should be noted that even in situations where poor film generation occurs, the metal-polymer bushing maintains an advantage due to the lubricating abilities of its PTFE surface.
Maintaining Efficiency with Metal-Polymer Bushings
The increased range of installed tolerances offered by metal-polymers means the prime focus for improving or maintaining efficiency lies in the design of the compressor.
These increased ranges can lead to mating parts within the compressor malfunctioning as a result of high tolerance stack-ups, causing power consumption to rise or output to drop.
Appropriate testing and investigation of changes within the compressor – along with changes in bearing design – has gone some way in counteracting this.
Shaft and housing dimensions can be engineered to reduce the range of tolerance to the capability limits of the manufacturer. Ongoing research involving metal-polymer bearing manufacturers is exploring options for reducing product tolerance ranges.
Metal-polymers can also undergo a sizing operation – burnishing – can be performed after bushing installation. This process entails pushing through a sizing tool of a specific diameter.
Where the bushing's inner diameter is less than the sizing tool, it will cause compression in the polymer overlay to compress, leading to a reduction in the tolerance range of the installed ID.
The compression of polymer material can unfavorably affect performance when the interference is too high, as each PTFE/filler material will react to sizing operations in different ways. Information can be obtained from metal-polymer manufacturers for their proprietary products.
The findings of a study into effective clearance upon efficiency can be seen below (Figure 3).
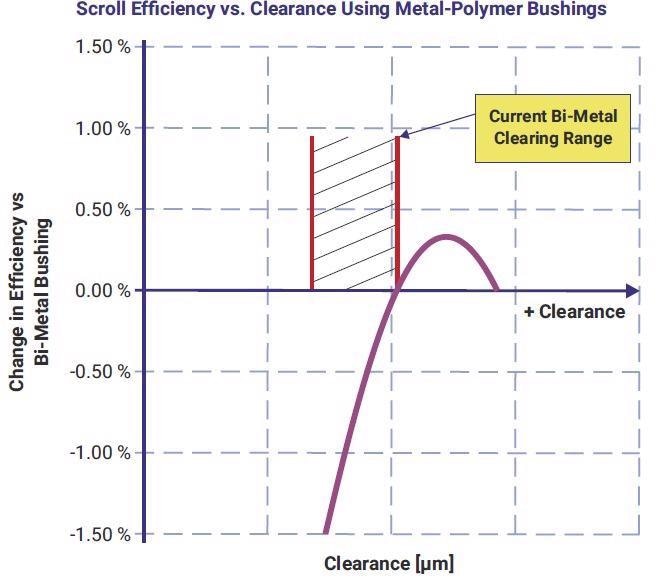
Figure 3. Metal-polymer efficiency vs. bi-metal efficiency over a particular clearance range. Image Credit: GGB
The study was carried out by a scroll compressor manufacturer that analyzed the performance of a metal-polymer bushing compared to a machined bi-metal bushing in a range of clearances. An increase in efficiency over a clearance range superior to that necessary for the bi-metal bearing was found.
More studies and other types of investigations are needed to fully comprehend the nature of performance within the polymer bushing in compressor system design. This will allow manufacturers to fully understand the mechanisms that help run and sustain performance in compressor applications that utilizes metal-polymer bushings.
As every design is unique, each one will need its own testing and investigation process.
Conclusion
When designed properly, metal polymers can deliver greater reliability in bearing systems in comparison to classic journal bearings. As a natural lubricant, PTFE can provide superior resistance to heat and friction in instances of marginal and boundary lubrication.
Polymer surface compliance offers improved management of misalignments compared to classic compressor bearings, facilitating greater system compliance with tolerance stack-ups in compressor design.
Employing metal polymers as direct replacements for classic compressor bearings is not advisable due to the differences in functionality at a range of clearances.
Ongoing discoveries in polymer sciences may result in the development of a metal-polymer with the ability to be machined at installation, facilitating the control of clearances.
Metal-polymers also offer modern material technology, allowing the development of more robust, reliable bushing products capable of keeping up with innovations facing the compressor industry – lead-free, 13 SEER, CO2 – better than conventional bi-metal, bronze or rolling element products.
Acknowledgments
Produced from materials originally authored by Christopher D. Small from GGB.
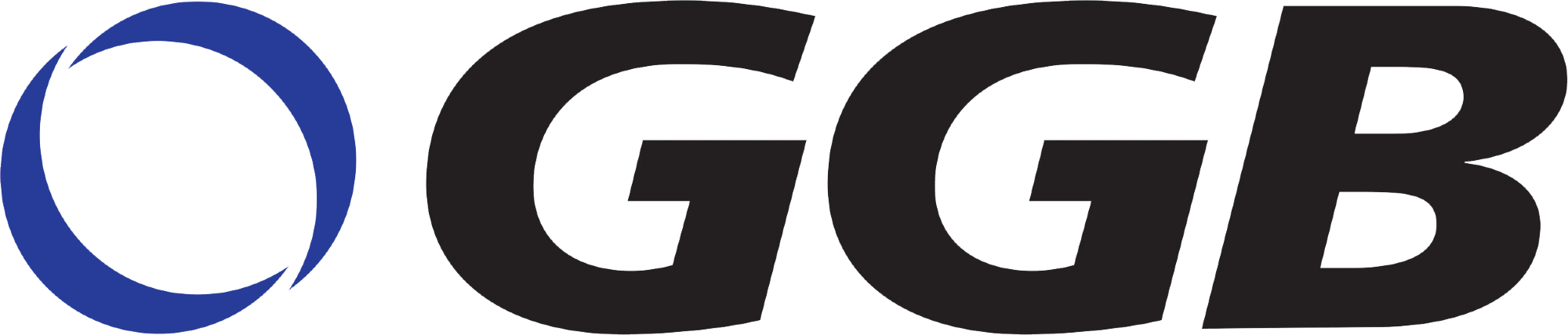
This information has been sourced, reviewed and adapted from materials provided by GGB.
For more information on this source, please visit GGB.