In this interview, AZoM speaks with Marco Enger, Senior Tribologist at GGB to discuss how nano fillers affect transfer films within tribological systems.
Could you introduce GGB and the company’s products and services?
GGB is a tribological company that provides technology to reduce friction. We do so by offering a wide variety of materials. Metal-polymers are what GGB is best known for, but we also make engineered plastics, fiber-reinforced composites, metals and bimetals.
More recently, we have added the ability to coat our polymers directly onto customers’ parts. GGB is unique in this regard, as we offer both the polymer itself and the coating operation.
What is the theoretical basis of transfer and sliding films, and how does this inform GGB’s work?
A typical tribological system includes four components; two contacting surfaces, the environment and the lubrication - the medium between the two surfaces in contact. This constellation is known as the system structure.
The tribological system also comprises the collective stress (load, speed and temperature) that acts on the system structure. Interactions among the system structure elements cause friction and wear.
A tribological system can be very complex. The relative speed can range from 0.001 to several meters per second – that is, three to four orders of magnitude. The motion type can also change – it could be continuous rotation, oscillation or linear reciprocation. A similar variety can be observed for the loads. The temperature can range from well below freezing to very high.
There is a huge variety of materials that are used for each surface.
In dry sliding conditions, polymer-based sliding materials can form a thin, protective film on the metallic counter surface known as a transfer film. The composite surface is also modified during the sliding process – this modified layer is known as the sliding film.
The sliding film is a change of the top surface areas of the polymer. This could be a change in surface or volume chemistry, a change in the microstructure, a change in mechanical properties or any combination of these.
The transfer film is the direct transfer of material from surface to the other surface.
The transfer film is very thin, but it is extremely important in a dry sliding scenario because it is a protective layer that masks the counter surface, reducing surface interactions and controlling wear and friction. A good transfer film should be thin and consistent.
These principles have informed the development of a range of GGB’s materials, including match polymers, metal polymers, fiber-reinforced composites and coated surfaces. Our goal is to be able to control the formation of the transfer film to our advantage in a wide variety of situations to better prevent wear and friction.
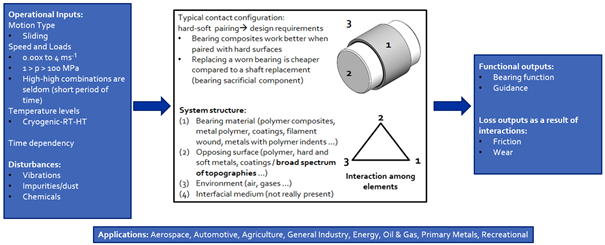
Tribological system.
Image Credit: GGB
What factors influence the quality of a transfer film?
Self-lubricating composites are able to form transfer films on the attacking counter face throughout the relative motion. The unavoidable wear of these materials when sliding against the harder counter face generates wear debris. This debris can escape from the contact zone or may – ideally – deposit onto the counter surface.
The entirety of the permanently adhering debris constitutes the transfer film, which potentially protects the contact from further wear damage. A higher protection rate can be achieved when the film has high quality.
A transfer film’s quality is often linked to its specific microstructural features. The film formation needs to be consistent and uniform, and the transfer film needs to have a sufficient coverage rate.
The other essential property of the film is its robustness. Robustness is linked to the ability of the film to withstand ongoing tribological stress actions. We also believe that the quality of the transfer film is affected by diverse factors dictated by the related tribological system.
The transfer film can also be understood as a response to a specific tribological system and is thus impacted by the induced collective stress, the specific property profile of the opposing surface, the composition of the self-lubricating material, and most likely the conditions of the surrounding atmosphere.
How are transfer films designed and developed?
Actually, we don’t develop transfer films.
We design materials with the right combination of features to enhance their capabilities to form robust transfer films, even under very demanding operating conditions.
As a material designer, changing a well-known material is always a good starting point for imparting new features into a material.
The potential approaches for enhanced transfer film forming are very broad, such as changing the structural architecture or changing the material’s composition by using different volume fractions in the composite.
The use of additional fillers is a promising modification method for enhancing the capability of active materials to form better and more robust transfer films. It is also possible to use a combination of different fillers to create a synergy effect and improve the overall composition.
A typical slide-active polymer compound is the subject of this investigation. The compound consists of a thermoplastic polymer matrix slide-modified with PTFE particles. Nanoparticles are added to enhance the transfer film-forming capabilities of the compound.
The first nanofillers used in this study are of oxide ceramic nature with a mean diameter of 50 nanometers. The second particle was a carbon allotrope with a mean diameter of around 25 micrometers. The thickness of these particles is 5-8 nanometers.
How do you characterize such materials tribologically?
When we create new compounds or composites, these will be tested using tribological testing methods with various boundary conditions. This also includes monitoring the performance and transfer film changes. The key goal is to understand how the different puzzle parts fit together.
The testing methods encompass simple model testing but also advanced component testing. In both cases we apply a defined collective stress (p and v) and measure the resulting friction forces, temperatures and wear of the material pair over time.
The transferability of tribological data from laboratory experiment to real applications is one of the most difficult challenges within tribological research. Comparisons between experimentally measured values are only feasible when based on a very similar tribological system.
Furthermore, model and simulation testing of materials only allows for an estimate of the tribological behavior in specific real-life applications, when the specific operating conditions of the application and test environment are the same.
The basic research is conducted using a simple and abstract model tester. However, to simulate real applications, tests can be performed using a typical journal bearing rig.
What factors impact the wear performance of a metal-polymer-contact?
Many dry operating bearing composite steel pairs generally undergo two characteristic friction and wear phases in their lifetime. They often start with a higher friction, which declines with progress in the covered sliding distance until a steady-state phase (low operation friction) is achieved.
The wear characteristic of such pairs can also be divided into two stages. The first phase is characterized by a high wear slope, and the wear rate decreases until the operational performance window is reached. During this phase, a linear wear characteristic is often observed.
Increasing the PV combination normally results in higher wear. High speeds are critical, especially when reaching the glass transition temperature of the polymer matrix. This leads to a change in the polymer state, which results in a reduction in mechanical properties often accompanied by lower resistance to wear actions. We also see that this tends to lead to premature failure.
The counter surface roughness can be a dominating factor when experiencing high polymer wear. This is accompanied by a change in the dominating wear mechanisms.
For example, for rough surfaces, abrasive wear actions dominate, while for smooth surfaces, adhesive interactions are more common. Meanwhile, moderate rough counter surfaces often lead to low wear because they promote the establishment of a stable transfer film. Another plausible explanation is an equilibrium between adhesive and abrasive interactions.
These two examples demonstrate that friction and wear are not intrinsic material properties; they are system responses.
The incorporation of nanofillers has a huge impact on wear performance.
System behavior completely changed when using nano compounds, with an early failing system transforming into a well-performing system. This could be due to higher, more robust protection against wear actions, or it could be due to an early formation of a robust and protective transfer film; or a synergetic mix of both.
Both the initial and operational wear rates can be reduced when incorporating nanofillers into the polymer composite. Our tests show three to four times lower wear rates when we added in nanofillers in synergy with a clear reduction of initial material consumption, this ensures a longer wear life.
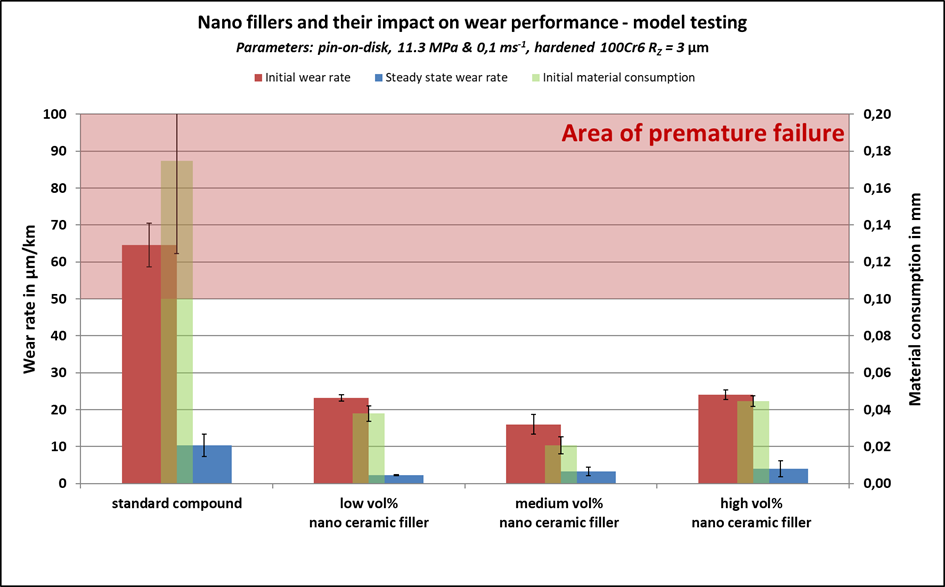
Wear performance comparison.
Image Credit: GGB
What sort of tools are used to characterize the quality and properties of transfer films?
There are a number of different methods we can use to characterize transfer films. A digital microscope is an easy-to-use and rapid tool, but it has some limitations.
A typical image shows limited contrast between the transfer film and the surrounding areas, making transfer film detection challenging. These problems disqualify this method as a basis for the quantitative assessment of transfer film quality using additional image processing tools.
SEM imaging is relatively slow, but it offers high quality and high contrast images of the transfer film.
We use backscattered electron detection because it provides an additional advantage compared to the standard secondary electron detection. This mode emphasizes the material contrast while suppressing topography details. These high-contrast images are highly suitable for further quantitative analysis using image processing software.
Complementary micro and nano-structural investigations can be used to gain additional information regarding the structural depth profile of the transfer films. A typical approach is the generation of nano-sections using a Focused Ion beam. Nano-structural features are assessed by applying scanning electron or transmission electron microscopy to these sections.
The chemical nature of the transfer films can be determined using typical analytical tools like Energy Dispersive X-Ray Spectroscopy, X-Ray photoelectron spectroscopy and Fourier Transform Infrared Spectroscopy.
The transfer film generated by the standard compound showed a very weak coverage rate. Polymer deposition was mainly found in the negative roughness features of the counter surface. Such insufficient masking of the counter face does not reduce surface interactions.
The enhanced transfer film quality was observed with the nano compounds. Transfer film coverage was high. We also observed that the transfer film covered plateau-like topography structures.
Negative roughness features are still filled with polymer. This alteration in the transfer film morphology indicates a change in the bonding mechanisms between transfer film and counter surface. Bonding changed from pure mechanical anchoring to chemical-mechanical bonding.
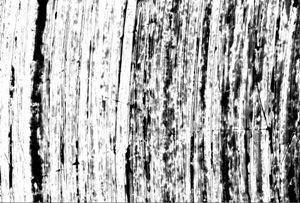
Figure 1. Transfer film morphology: transfer film formed by a nano compound.
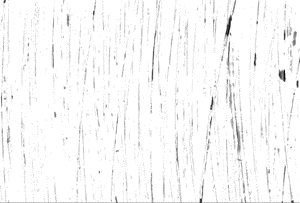
Figure 2. Transfer film morphology: transfer film formed by a standard compound.
Image Credit: GGB
How can transfer films be quantitively analyzed to determine their quality?
It can be very time-consuming to analyze a large number of SEM images. The way we analyze these images can change from day to day, and an objective tool is what has been missing.
Another problem is that qualitative features like thinness, adherence and coverage rate cannot easily be linked to tribological data. To overcome these drawbacks, we developed a MatLab algorithm in collaboration with the University of Mannheim that can be used to quantitatively characterize the quality of a transfer film.
The algorithm determines the free space lengths between polymer patches. In other words, it determines the geometrical density of polymer patches.
It also determines the coverage rate of the transfer film and can distinguish between thick and thin areas of the film.
To do so, the algorithm scans the SEM image from left to right from top to bottom for white areas. The algorithm ignores dark areas, and when a white area is detected, a square expands in the X and Y direction until the square borders reach a dark area. The dimensions of the square are then recorded.
Before we can use the SEM images, we need to clean them using an image pre-processing step. These steps may include cropping regions which could be erroneously identified as transfer films and normalizing the grayscales in the image from 255 grayscales down to three.
In the normalized image, white areas represent local voids in the transfer film where no film is present, light gray areas represent thin films and black areas represent thick films or thick polymer patches.
A noise filter may also be applied to the whole image to remove single pixels with no direct neighbors. Median filtering can also be applied to reduce the pixel noise further.
This process is completed for three different areas of the counter surface disc. We tend to run this algorithm at different magnifications to ensure sufficiently reliable statistics regarding the transfer film quality.
A good correlation between the wear performance and the free space lengths among transfer film patches was found. In many instances, the coverage rate also correlates with the tribological performance, suggesting that a minimum coverage rate is required to promote optimal wear performance.
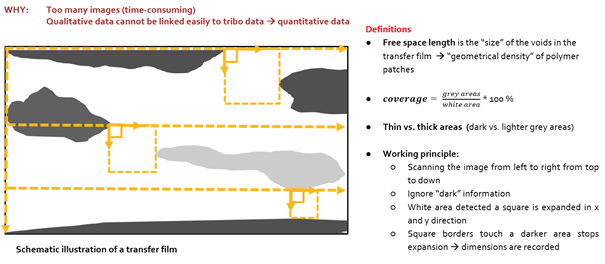
Algorithm to assess the transfer film key characteristics.
Image Credit: GGB
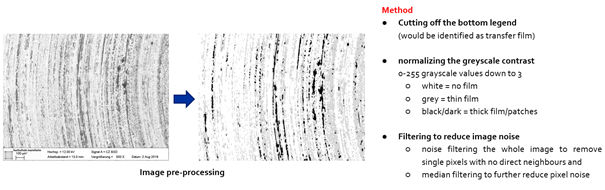
Working steps image pre-processing.
Image Credit: GGB
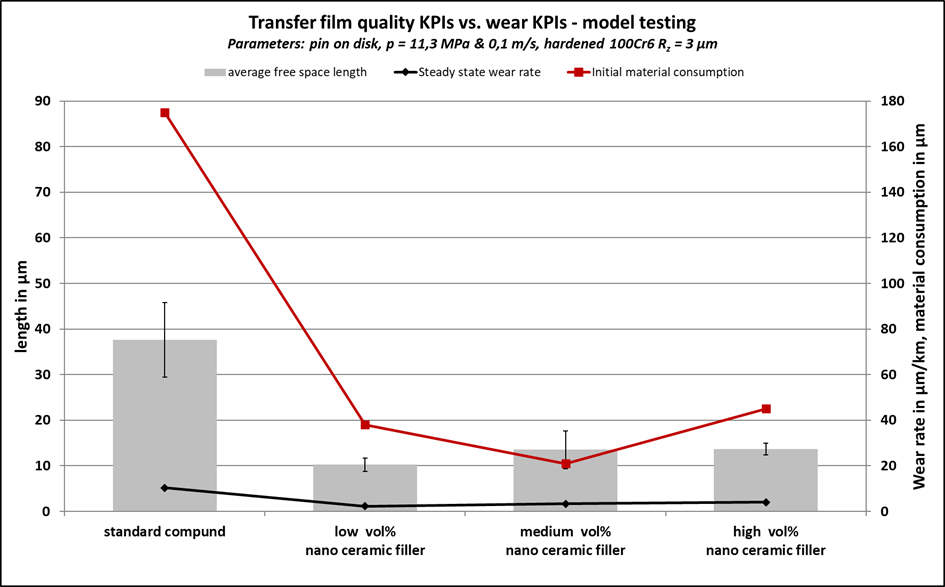
Transfer film key characteristics vs. wear performance.
Image Credit: GGB
About Marco Enger 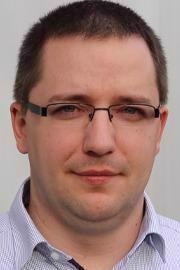
Enger holds a Ph.D. in mechanical engineering with more than 10 years of experience in tribology, tribometry and all related subtopics. In 2014, he became the senior tribologist at GGB and is responsible for all fundamental research works related to tribology. Before he joined GGB, he was working for the Competence Center of Tribology at Mannheim University.
About Andreas Keller 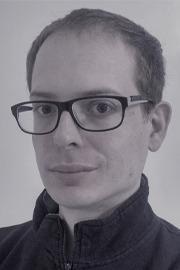
Andreas Keller is working as a researcher at the Competence Centre Tribology (CCT) which is part of the Mannheim University of Applied Sciences. He has a M. Sc. in mechanical engineering and 8 years of experience in tribology and tribometry. In this time, he has worked on several public funded projects, among other things analyzing the wear-mechanisms of tungsten-carbide-tools for CFRPs, testing novel additive formulations for gear oils and researching PTFE transfer film formation together with GGB.
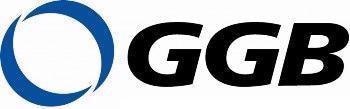
This information has been sourced, reviewed and adapted from materials provided by GGB.
For more information on this source, please visit GGB.
Disclaimer: The views expressed here are those of the interviewee and do not necessarily represent the views of AZoM.com Limited (T/A) AZoNetwork, the owner and operator of this website. This disclaimer forms part of the Terms and Conditions of use of this website.