In this interview, AZoM talks to James Terrell from SciAps, about carbon grading in small parts and the implications this has for industry.
Why is analyzing carbon in small parts important for grading materials and product manufacturing?
Even small parts are an integral part of the asset. The failure of small parts could lead to catastrophic consequences just like larger components.
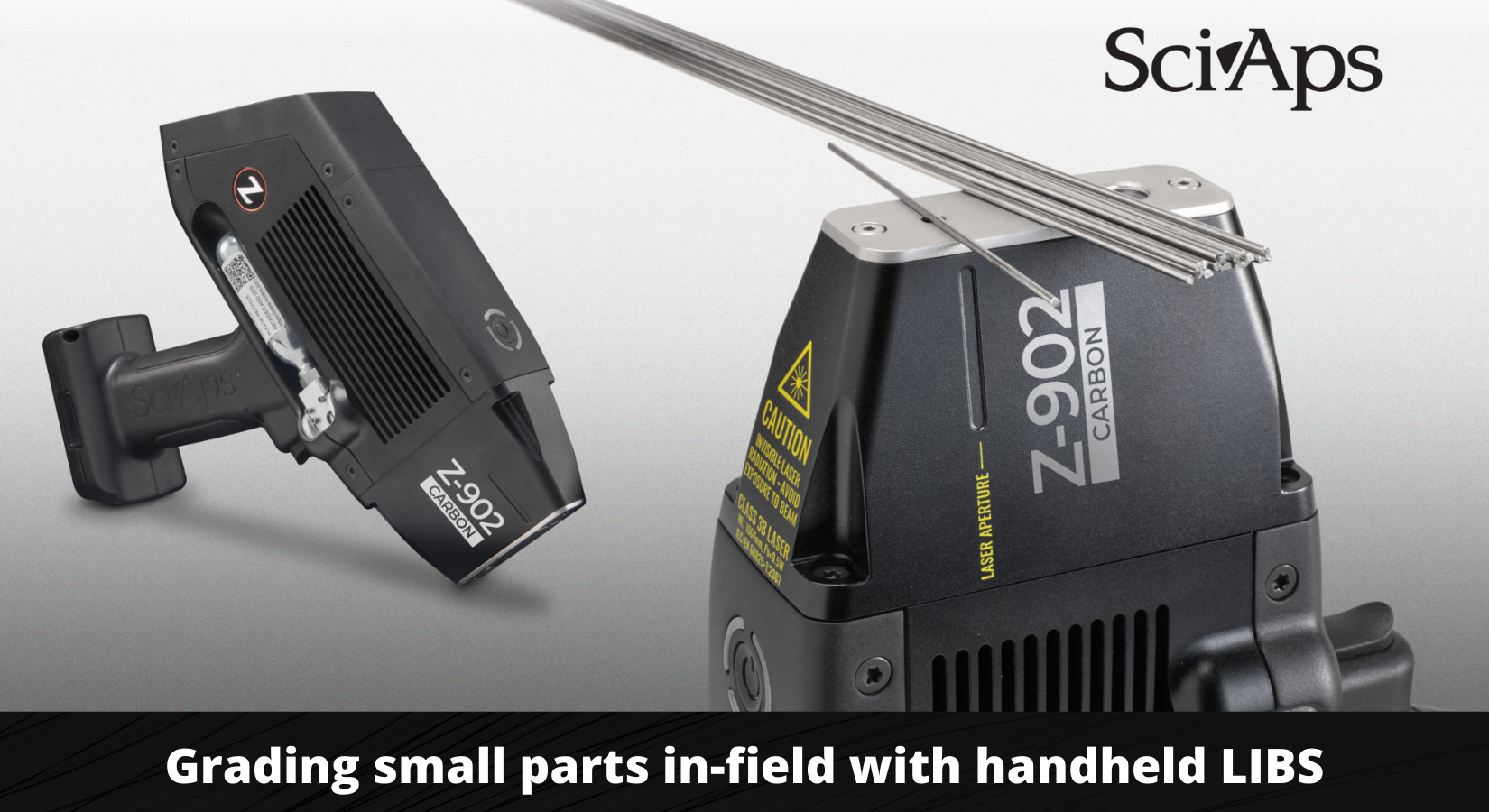
Image credit: SciAps
What are some of the current challenges that manufacturers face when analyzing carbon in small parts?
Size and geometry present the biggest challenges. The ability of the testing equipment dictates the size of material it can accurately analyze.
How did you overcome these challenges from both a laboratory and industry perspective?
The SciAps analyzer uses a patented purging technique for measuring carbon that does not require a sealing surface to create the inert atmosphere needed to measure carbon.
This small aperture still allows for analysis on small parts without the need for various adapters to accommodate the geometry or size of the part. Curved surfaces or surfaces smaller than the aperture are still able to be analyzed without the need for special adapters.
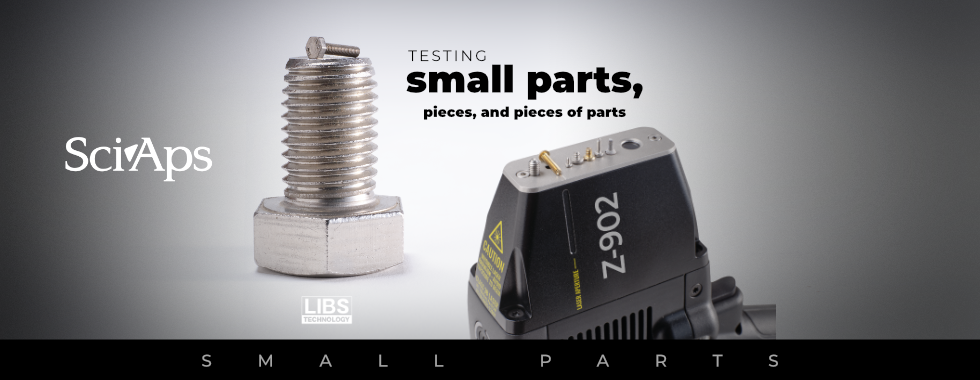
Image credit: SciAps
What are some disadvantages of optical emissions spectroscopy when analyzing carbon content in small parts?
When utilizing conventional OES analyzers, the probe and aperture of the probe are larger and require a sealing surface at the burn chamber. If the part is smaller than the sealed area of the burn chamber, then you would need an appropriately sized adapter to accommodate that part.
The physical size and weight of an OES is also a disadvantage for fieldwork that requires working at elevated work platforms or in a ditch. The OES also requires a large argon bottle and external regulator to perform the analysis. This ultimately adds to the weight and size of the analyzer.
What are the strengths and weaknesses of X-ray fluorescence in small part carbon analysis?
XRF is a reliable technique for measuring and identifying alloys, even on the smallest of parts. The downside of XRF is that it is not capable of measuring Carbon content. Therefore, it cannot grade materials such as L or H stainless steels.
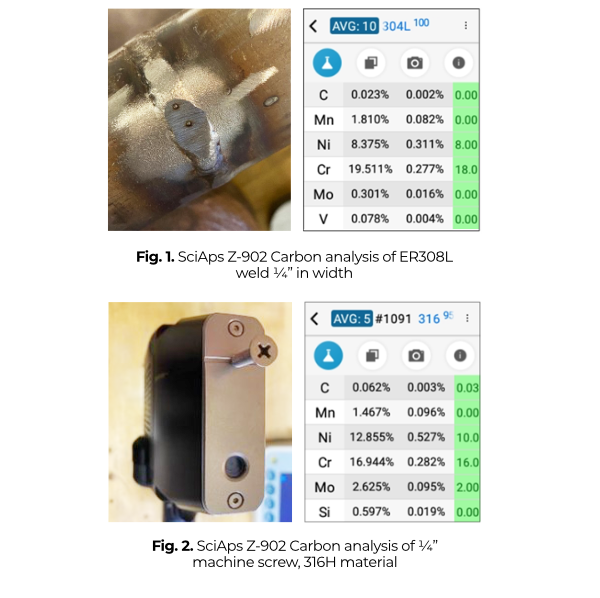
Image credit: SciAps
What is laser induced breakdown spectroscopy (LIBS)?
LIBS is an optical emissions technique that utilizes a pulsed laser to ablate the surface of the material and create a plasma. An on-board spectrometer performs a qualitative measurement of the light from the plasma, separates the individual wavelengths to reveal elemental content, which is then quantified with the on-board calibration.
How can handheld LIBS help streamline manufacturing processes and improve carbon analysis for manufacturers?
These instruments provide an efficient and cost-effective solution in a handheld device.
These handheld devices provide the owner/operator with a compact all in one, lightweight, cost-effective way to analyze incoming material, service/retro PMI material, welds, welding consumables and any critical component in their PMI program without the added labor or cost of buying sacrificial parts or collecting shavings and sending them to a lab and waiting on results.
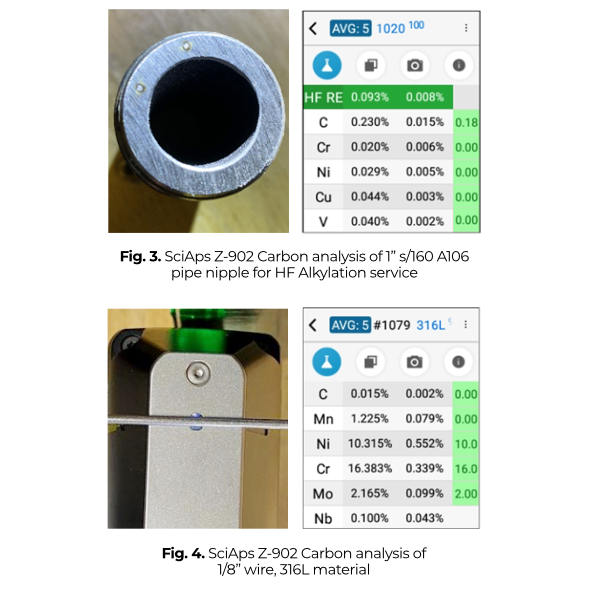
Image credit: SciAps
Why is comprehensive, on-site analysis an improved solution to grading carbon in small parts?
On-site analysis eliminates the long waiting time that is often required to get results from the lab. It allows asset owners to continue to make critical decisions in real-time without having to send parts out to be analyzed. This type of flexibility allows the owners to continue to operate their assets or begin operating sooner, saving valuable time and money.
Can you provide some examples of how SciAps handheld LIBS improves carbon grading in small parts such as weld wire, round bar, small bore pipe and bolting?.
By utilizing the SciAps LIBs analyzers, the user can now analyze parts such as small weld wire without the need to deposit the wire to create a weld button for testing. It can also test small bore piping, bolting and small diameter round bars without the need or cost for additional adapters to accommodate the part that is to be tested.
Sources:
About James Terrell
James joined the SciAps Team as a Subject Matter Expert (SME) for practical field application and solution provider for handheld XRF and LIBS technology in the chemical oil & gas industry. He has 30 years of experience in petrochemical, manufacturing, fabrication, new construction, and maintenance.
James will be focusing on business development for practical field application solutions in these technologies that will help the end user to safely and efficiently confirm, verify, and identify, alloy and carbon steel materials that could be susceptible to industry issues such as rouge material in process units, or identifying damage mechanisms like low silicon content (sulfidic corrosion) in carbon steel pipe.
James began working in the industry in 1987 in construction as a pipefitter and welder and then eventually spent his last 6 years in construction management as a General Foreman and then Construction Superintendent. James began his own PMI business in 1997 utilizing handheld XRF and OES units performing these techniques in multiple segments of chemical oil & gas, power, manufacturing, and fabrication. He has been directly involved in various industry programs including retro-PMI programs, incoming material verification, welding applications, as well as restrictive element application such as HF Alky.
James started working as a PMI SME and Division Manager with Acuren Inspection in Houston Texas in 2009 and helped developed a PMI division that included developing PMI procedures and training technicians to perform the XRF and OES technologies to support the demand for PMI compliance. He also spent 4 years with Acuren as Director of Operations for the SW region.
James also worked as a Vice President of Operations for TUV SUD America Chemical Oil & Gas Division from 2015-2018. He was responsible for the day to day operations and developed a PMI division and program for TUV SUD and was a consumer of XRF and OES technologies.
He joined Thermo Scientific in 2018 to help facilitate the launch of the Niton LIBS analyzer before joining SciAps in 2020
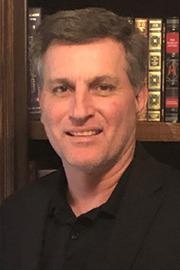
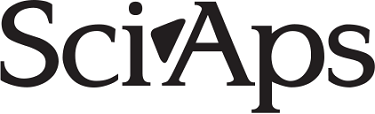
This information has been sourced, reviewed and adapted from materials provided by SciAps, Inc.
For more information on this source, please visit SciAps, Inc.
Disclaimer: The views expressed here are those of the interviewee and do not necessarily represent the views of AZoM.com Limited (T/A) AZoNetwork, the owner and operator of this website. This disclaimer forms part of the Terms and Conditions of use of this website.