Nuclear submarines are ubiquitous with modern navies. Developments in technology since the mid-20th century has led to the increased efficiency, operational standards, and safety of these underwater weapons platforms. Advanced materials have been one of the cornerstones of nuclear submarine development, and this article will provide an analysis of the subject.
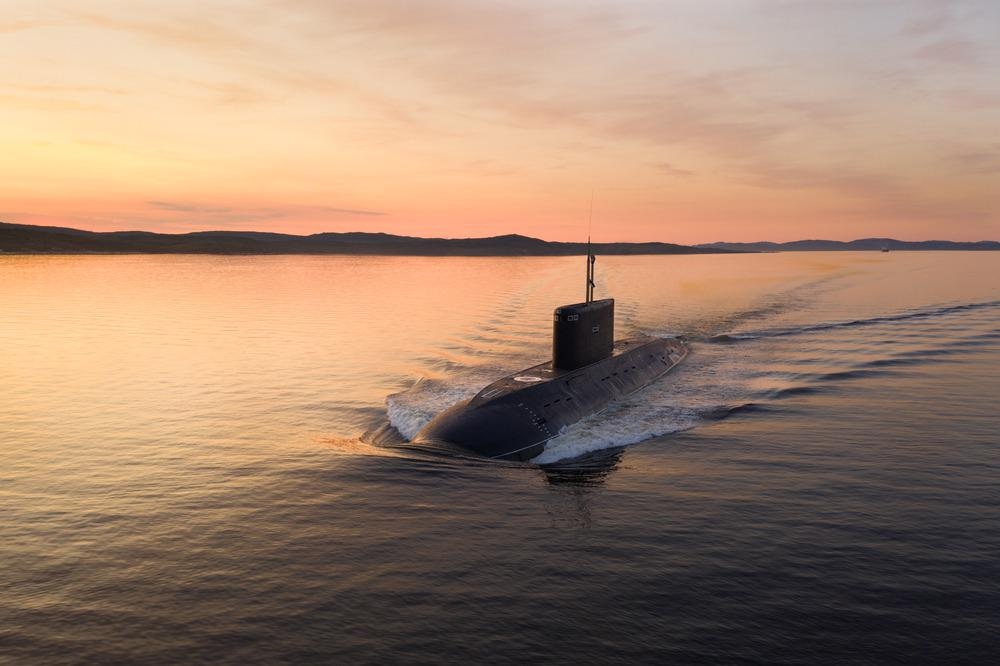
Image Credit: Aleksandr Merkushev/Shutterstock.com
The History of Submarines
The history of submarines is surprisingly long. William Bourne, an English mathematician, was the first to seriously propose a design for a submarine in 1578. Bourne’s design included two hulls constructed from wood and leather but was never built. It would not be until 1620 that the first working submarine, designed by Dutch inventor Cornelis Drebbel, would be built. This primitive submarine was propelled through the River Thames by eight wooden oars.
The 18th century saw the introduction of several smaller designs for submarines, including a design in 1747 that included goatskin bags which would fill with water to lower the submarine, and when the water was released from the bags the submarine would rise. This concept is still used in modern ballast tanks.
The first use of submarines as weapons of war would come in the American Revolution, when the Turtle attempted to blow up a British ship. The Nautilus was designed in 1801, which used copper sheeting over iron ribs, but despite sinking several ships in tests, France and Britain rejected the design. The Nautilus could carry a crew of four.
During the American Civil War, the Confederacy would make limited use of these vessels, most notably in the sinking of the Housatonic, a Union ship, in 1864 (although the vessel was itself destroyed in the explosion.) Over the course of the late 19th and early 20th century, submarine technology developed rapidly, most notably in the methods used to power them, evolving from hand-operated propellers to steam engines, electric power, and gasoline engines.
By the first World War, diesel engines had been developed and were extensively used. Submarines used diesel engines for surface travel and electric batteries when under the water. The era of the submarine as a ubiquitous weapon of naval warfare had arrived.
After World War 2, with the advent of nuclear power, submarine technology was revolutionized. The first nuclear submarine, again called The Nautilus was launched by the US Navy in 1954. By 1959, strategic submarines had been developed, which could carry nuclear missiles. Attack submarines were developed that could sink enemy ships and other submarines.
The submarine rapidly became an integral part of navies worldwide. In 1982, the British sank the Argentine naval light cruiser General Belgrano during the Falklands War, which was the first use of a nuclear submarine in active combat.
Raw Materials used in Nuclear Submarine Construction
Several materials are used in modern nuclear submarine construction. The main raw material used is steel. This material is used to construct the inner and outer hulls, ballast tanks, and other crucial infrastructure elements in the submarine.
Other raw materials used in the construction of various parts include copper, brass, aluminum, glass, and plastic. Electronic components use materials such as silicon and germanium. Nuclear reactors primarily use highly enriched uranium as an energy source. Other materials are used in the construction of the weapons that are kept ready for use if the need arises.
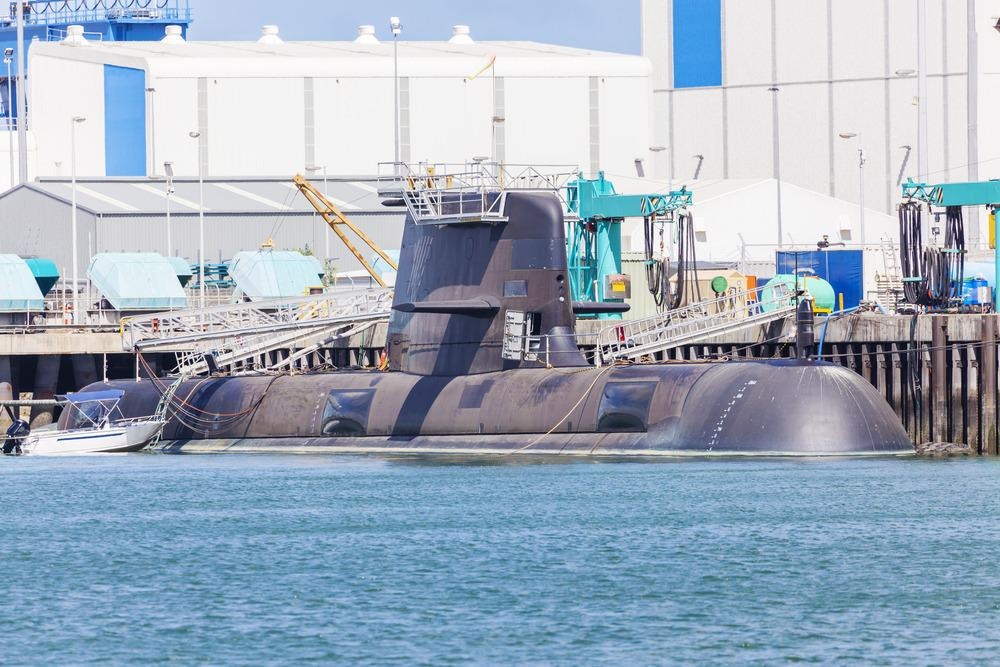
Image Credit: ymgerman/Shutterstock.com
Designing the Nuclear Reactor
The reactor is one of the most vital elements of a nuclear submarine. If it were to fail, not only would the submarine be without power, but there is a possibility of a radiation leak or explosion. All these scenarios have the potential to be fatal for the crew.
Nuclear reactors have specific material and technical requirements that ensure their optimal and safe performance. Nuclear reactors must be properly shielded to avoid contamination with radioactive materials. HMS Astute (S119), a British submarine, uses two-part shielding. The lower section is constructed of a lead water vessel that absorbs gamma rays.
The upper part of the shielding is composed of flexible blocks of polyethylene which have enhanced scattering power and a high absorption cross-section. This upper part must be moveable, as engineers need to remove spent fuel and control rods and insert new ones.
The second outer layer of the reactor is the vessel. Specifically treated materials are used in its construction. In the case of HMS Astute’s reactor, the reactor vessel is made from a low alloy manganese molybdenum steel. Highly weldable to minimize singular points of high stress, this alloy has enhanced physical properties such as strength. The alloy is highly resistant to the extremes of temperature and pressure which are found in nuclear reactors.
Inside the Reactor Core
Inside the reactor core are elements such as fuel rods, control rods, and coolant/temperature moderators. The fuel rods are filled with radioactive pellets, most commonly made from enriched uranium dioxide. In a process known as sintering, heat and pressure are used to form powdered uranium dioxide into the ceramic-like fuel pellets. The fuel rods are covered with a corrosion-resistant alloy which does not absorb neutrons and interfere with the fission process.
Control rods are used to prevent runaway nuclear reactions. They are placed between the fuel rods and are dropped to stop the fission process. The material used to make fuel rods is typically boron. Boron is chosen because of its high melting point and high neutron absorption properties. Water is used to regulate the reactor’s temperature and additionally it acts as a moderator, reducing the collision rate between neutrons which would otherwise cause a runaway nuclear reaction.
Manufacturing a Submarine: From Concept to Launch
The manufacturing process for a submarine involves several complex steps from initial concept to launch and operation. At all steps, quality control and regulations are tightly adhered to.
The first stage of the manufacturing process involves design and funding procurement. As all nuclear submarines have a military purpose, the decision to build one is made by a national government. In the USA, this is handled by the US Navy’s Underwater Warfare Division. Bids from companies to make the components are accepted and funding is approved by the government out of the national defense budget. The most closely guarded design aspect is the nuclear reactor.
Next, the hull is constructed out of 2–3-inch steel plates which are cut to size with acetylene torches and formed on rollers under immense pressure. The plates are rolled until the desired curve is achieved. Using a wooden frame, the hull is constructed from multiple steel plates welded together. T-shaped metal ribs are used to strengthen the structure.
The inner hull is made from several welded sections and the two hulls are connected with steel ribs. To allow the submarine to stay upright, the outer hull extends only as far as the top and bottom of the inner hull. Steel plates are used to form water-tight compartments, and steel bulkheads and decks are welded into place. The welding seams on the exterior hull are polished until smooth, which makes the hull easier to paint and add protective coatings to, while providing a streamlined profile.
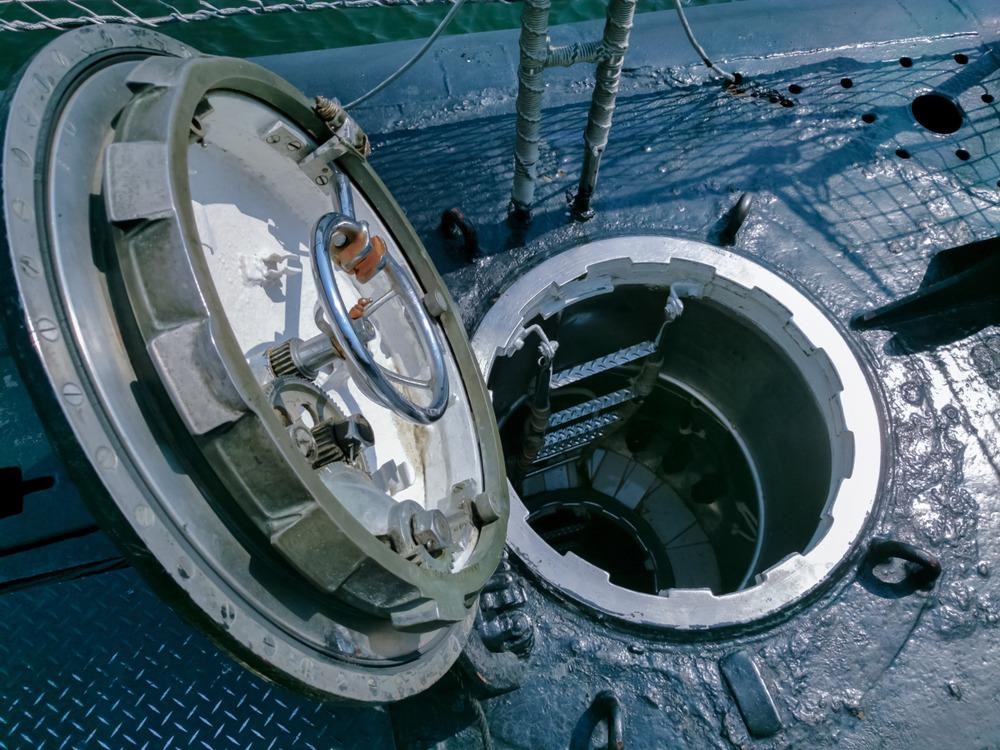
Image Credit: Lord Beard/Shutterstock.com
Vital exterior components such as rudders and propellers are constructed with precise machining methods. One manufacturing method used in fabricating these components is sand casting, where a mold made of a plastic or wooden model of the part and surrounded by tightly packed sand is made. Molten metal is poured into this mold and allowed to cool until the part is formed. The exterior parts are then installed in the submarine.
The last step in the manufacturing process involves finishing the interior parts of the submarine. Larger equipment is placed inside whilst the hull is still being constructed, as otherwise they would not be able to be installed. Smaller parts are installed after the exterior hull is finished. These smaller parts include equipment such as engine parts, wiring, the periscope, snorkels, refrigerators, ovens, air conditioners, furniture, and so forth.
Once the submarine is finished, it is launched and undergoes sea trials. The nuclear reactor begins operating during this time. Once the submarine and crew have been fully tested, the submarine enters active service.
Quality Control
Quality control is more important than any manufactured part to ensure the safe and efficient operation of a nuclear submarine. All parts are inspected before they are installed, from the wiring to the steel plates that make up the hull. The nuclear reactor is subject to especially stringent ad extensive quality testing. As the nuclear submarine plays a vital role in defense and the lives of the crew depend on its safe operation, quality control is crucial.
Pipes are filled with helium to check for leaks. Every piece of equipment is checked to see if it is in good working order. Welding is x-rayed to ensure its quality. Steel plates are examined to ensure their dimensions are accurate to within one-sixteenth of an inch. During sea trials, the speed and maneuverability of the submarine, as well as its ability to stay undetected, are tightly monitored to ensure the vessel meets strict necessary requirements.
Further Reading
How Products are Made (website) Nuclear Submarine [online] madehow.com. Available at:
http://www.madehow.com/Volume-5/Nuclear-Submarine.html
AJ Mitchell (2021) How do nuclear-powered submarines work? A nuclear scientist explains [online] Theconversation.com. Available at:
https://theconversation.com/how-do-nuclear-powered-submarines-work-a-nuclear-scientist-explains-168067
Disclaimer: The views expressed here are those of the author expressed in their private capacity and do not necessarily represent the views of AZoM.com Limited T/A AZoNetwork the owner and operator of this website. This disclaimer forms part of the Terms and conditions of use of this website.