This article will provide an overview of waste sulfur and explore the concept of producing polymers from this by-product for a more environmental solution.
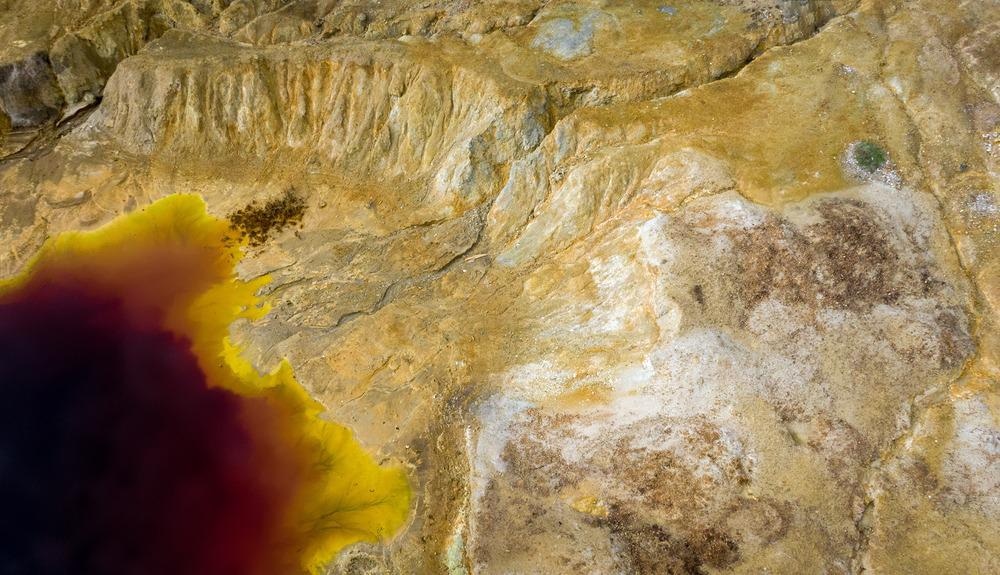
Image Credit: Anna Kucherova/Shutterstock.com
Waste sulfuric acid is created as a by-product from common industrial processes such as through the extraction of minerals and metal smelting processing.
Petroleum refining can also produce millions of metric tons of excess sulfur every year.
The production of waste sulfur has become a concern for the environment and the general state of the Earth, with many industrial processes producing sulfur oxide emissions that contribute to acid rain.
Currently, this waste product can be treated through neutralization or regeneration with the removal of concentrated contaminants and re-refining, however research has also consisted of the novel production of polymers from sulfur waste materials.
Waste Sulfur Products
Approximately 85% of sulfur that is used for industrial processes is converted to sulfuric acid, with this acid used predominantly as a chemical reagent in leaching or catalytic processes such as the mining of minerals including phosphate, copper, and titanium. When translating this to industries within the United States, this chemical reagent can encompass 90%.
The waste sulphuric acid in the final stage of the industrial cycle includes the disposal of this waste through neutralization via the formation of its salts. A large amount of industrial sulfur is released into the environment in the form of sulfite, through atmospheric emissions, and sulfate. Additionally, the ambient oxygen near the Earth's surface oxidizes sulfites to sulfates over time, which results in the sulfates dominating waste compounds.
Converting Sulfur into Polymers
With sulfur being the most undesired waste product in the petrochemicals industry and the high level of this waste, research into converting sulfur into polymers may have great potential.
Polymerization consists of small monomers that join to form a larger polymer molecule. While plastics and polymers are known for their lack of recyclability and difficulties with biodegradation, polymers that are composed of a high volume of sulfur carry many bonds that are easily broken and reformed. This useful notion enables further refinement from sulfur waste products, with ease in creating objects out of sulfur polymers that can later be recycled and reformed to create a different piece.
However, a limitation with this environmentally friendly concept includes sulfur polymer objects having poor mechanical properties. This can be improved through an innovative two-step synthesis process, as found by a group of international researchers from the University of Liverpool, UK, and Northwest Normal University, China, who have collaborated on improving the mechanical strength of sulfur polymers. The research was published in the Angewandte Chemie International Edition journal.
The team introduced a two-step synthesis process that uses urethane bonds as crosslinkers; this included preparing a chemically stable linear pre-polymer from the waste material that is sulfur as well as span 80, which is a trifunctional monomer.
This cross-linking process ultimately resulted in the formation of urethane bonds and significantly increased the mechanical strength of sulfur polymers.
Reducing The Environmental Burden
The novel development and advancement in sulfur polymerization allow for recycling, which is significant for reducing the level of sulfur waste product that is produced from industrial processes. This process may be able to address the high percentage of sulfur by-product that is produced worldwide and work to reduce its effect on the Earth, such as the precipitation of acid rain.
Additionally, the process also resulted in a ‘shape-memory’ effect – this consists of the material being set into a certain shape, allowing temporary deformation for the fabrication of a second shape until being heated, causing the first shape to be re-established.
The potential applications for this innovative approach to reducing sulfur waste material through utilizing polymers and the creation of objects with high mechanical strength is promising for several fields. The utility of this technique can span industries from soft robotics to medicine.
However, whilst the potential for this technology may be high, the reality of combining high mechanical strength as well as high flexibility is still an obstacle and highly challenging. With further research into crosslinking agents and tuning of sulfur polymer properties, the collaborative researchers are sure their principles can be used to address a range of applications.
This cross-linking process may also be a stepping-stone for material science research into reducing other environmentally hazardous greenhouse gases. This would ultimately aid in the global goal of reducing emissions that was outlined in the Intergovernmental Panel on Climate Change.
References and Further Reading
Yan, P., Zhao, W., Zhang, B., Jiang, L., Petcher, S., Smith, J., Parker, D., Cooper, A., Lei, J. and Hasell, T., 2020. Inverse Vulcanized Polymers with Shape Memory, Enhanced Mechanical Properties, and Vitrimer Behavior. Angewandte Chemie International Edition, 59(32), pp.13371-13378. Available at: https://onlinelibrary.wiley.com/doi/10.1002/anie.202004311
Chemistryviews.org. 2022. Turning Waste Sulfur into Polymers :: ChemViews Magazine :: ChemistryViews. [online] Available at: https://www.chemistryviews.org/
Rappold, T. and Lackner, K., 2010. Large scale disposal of waste sulfur: From sulfide fuels to sulfate sequestration. Energy, 35(3), pp.1368-1380. Available at: https://www.sciencedirect.com/science/article/pii/S0360544209005118?via%3Dihub
American, S., 2022. How are polymers made?. [online] Scientific American. Available at: https://www.scientificamerican.com/article/how-are-polymers-made/#
Disclaimer: The views expressed here are those of the author expressed in their private capacity and do not necessarily represent the views of AZoM.com Limited T/A AZoNetwork the owner and operator of this website. This disclaimer forms part of the Terms and conditions of use of this website.