In this interview, AZoM talks to Anna Walkiewicz, Applications Specialist at Quorum Technologies, about sample coating and how it can help improve SEM imaging.
Could you provide a brief overview of Quorum Technologies and its work?
Quorum Technologies is a UK-based company on the South Coast of England. Our product portfolio comprises sample preparation systems and cryo solutions for electron microscopy. We aim to support our customers to develop streamlined sample preparation workflows suitable for electron imaging of different types of materials.
What are some of the main benefits of coating samples before analysis with electron microscopy?
There are several key benefits to coating samples. We may want to localize a minimal volume of penetration to the very surface of our sample.
We can achieve this by applying a thin metal coating, localizing the response from the sample, and improving the contrast and the yield of secondary electrons. Coating a sample will also reduce localized heating, reducing beam damage.
Coatings reduce the charge of the sample, making it easier to analyze. When the sample is coated, the electrons are removed from the top of the sample, and the sample is grounded, meaning that charge accumulates, forming a potential on top of the sample.
If the sample is not coated, that charge accumulates, potentially resulting in negative charging, positive charging or even traveling charge.
The accumulation of charge is related to microscope operating conditions, and charge effects may vary between microscope models, including edge charging, line by line charging, area charging or residual charging.
Properly preparing a sample can reduce or remove these effects. It may also be prudent to adjust the imaging parameters, for example, by examining the total yield versus beam energy.
Another benefit of applying a thin metal coating to samples is reducing contamination. Contamination can come from the sample (for example, when working with outgassing samples) or from the microscope itself (for example, from samples that had been imaged previously).
Why is it important to distinguish between the effects of charging and contamination?
When organic samples have gas or moisture trapped inside them, this can be released during scanning. In the worst-case scenario, this could damage the sample and the microscope.
To differentiate between charging and contamination, we can scan a small area with higher voltage, zoom out to a lower magnification and scan a larger area with low voltage.
If the effect is still visible, this generally means we are dealing with contamination rather than charging.
A thin metal coating will prevent the microscope from becoming contaminated. As local overheating from the beam is reduced, there is no increase in temperature on the sample’s surface, and any gas trapped in the sample will not escape the sample.
It is important to avoid outgassing because escaping hydrocarbons can accumulate in a microscope’s chamber, negatively affecting further imaging. The resolution will be progressively lower between samples until the microscope is cleaned – an often costly process that results in downtime.
What factors must be considered when selecting a material for coating a sample?
We must first decide what material will be used as a coating. We do this by choosing a target, deciding coating thickness, coating quality and the application method. In particular, we need to use a coating grain size that does not obscure the sample’s features.
We first need to consider the nature of the sample. If the sample is sensitive to vacuum, it is likely to be unsuitable for coating and imaging in the SEM, but it may be possible to use other preparation techniques before coating to prepare the sample to withstand vacuum.
It is also important to consider whether samples need to be stored. If there is a need to revisit samples later, oxidizing metals cannot be used.
We must think about the specific features of interest. Features several microns in size allow us to choose a metal that exhibits slightly larger grains in the coating, but if the features of interest involve nanostructures, a coating metal must have a tiny grain size.
Finally, consideration must be given to the end goal of the imaging, for example, a composition study or further analysis via EDS. Once all these factors have been considered, an appropriate metal can be chosen for the coating.
What role do an element’s properties play in its suitability for coating samples?
An element’s neutral atom size is not particularly important when considering sample coatings, but the size of the ion that the atom forms is vital.
Cations are typically smaller than anions, but there are differences in the size of cations.
Gold is a common choice for metal coatings, but its ion size of 137 picometers is large enough to obscure particularly small features on a sample. Platinum’s ion size is 80 picometers, while iridium’s ion size is 68 picometers – a tiny grain size.
These three metals are typically costly, and their cost is prohibitive for many applications. Alternatives do exist, however.
Chromium is comparable to platinum in terms of ion size, but it is highly oxidizing. Imaging must be performed immediately when coating with chromium, and there is no option to revisit the sample later.
When working with samples that possess features of interest at the nanoscale, tungsten and molybdenum are viable options as these possess extremely small grain sizes.
We must also consider the secondary electron yield, ideally coating samples with a metal that has the highest secondary electron yield.
The coating’s physical properties will impact its analysis, such as its thermal conductivity and fragility. When working with brittle metals, applying pressure to the sample just after coating may create cracks that will hinder the analyst’s ability to determine features of interest.
Chemical stability is also important. We tend to coat samples with normal metals, but we sometimes need to remove the coating after analysis. Silver and copper are good options here because these metals can be easily dissolved.
Finally, coating thickness should be adjusted according to the features of interest to avoid obscuring these with a coating material.
What are some of the most common coating methods when preparing samples for electron microscopy?
Standard coating methods include carbon or metal evaporation, with more sophisticated methods available such as low angle shadowing, with subsequent terminal evaporation of metal or carbon.
While it is possible to use electron beam evaporation and ion beam sputtering to produce very fine coatings, coaters capable of utilizing these methods are expensive.
The most common method is direct current magnetron sputtering – a rapid, inexpensive and widely applicable method ideal for delicate samples because this method involves minimal heat applied to the sample.
Without magnetrons, the head of the coater can become very hot, running the risk of destroying the sample.
Cold magnetrons produce areas of localized electrons, allowing a plain current to create plasma from the sputtering gas. As the cations of the sputtering gas bombard the target, they knock out atoms of sputtered target material that land on the sample, forming a thin film.
What parameters should users consider when optimizing the cold magnetron sputtering process?
The most important parameters in the cold magnetron sputtering process are base vacuum, sputtering current and sputter gas pressure.
The vacuum is created just before coating, and this will determine how much the chamber is evacuated before the sputtering gas is allowed to enter. The level of vacuum required will depend on the sample itself and the necessary level of detail.
We can understand the impact of these parameters using the example of electrospinning fibers – widely used fibers in battery support, medical devices, filters and membranes.
Electrospinning fibers have a very discrete morphology, and successfully doping these fibers involves understanding how this doping is localized and to what degree it will change the structure of the fibers’ surface.
Using the initial vacuum in the chamber before coating will result in issues and unwanted features; for example, big grains will make it difficult to distinguish between the fibers.
In this example, the vacuum should be set at 10-6 operational vacuum to ensure uniform coating that is fine enough to distinguish between fibers and allow analysts to resolve features on the fibers’ surface correctly.
A balance must be struck between speed and quality when selecting a current to use. For electrospinning fibers, a high current of 20 milliamps would result in fast deposition, but coating quality would suffer.
Removing sufficient gas and impurities from the chamber before coating will generally result in a better-quality coating. Reducing the sputtering current of the process improves the quality further, though both these adjustments are more time-consuming.
It is essential to control the quality and grain size of a coating because this ultimately affects imaging, mainly when working with high-resolution SEM. This requires a proper understanding of how different parameters can be set to avoid coating artifacts and ensure the best quality imaging possible.
About Dr. Walkiewicz
Dr. Anna E. Walkiewicz is the Applications Specialist at Quorum Technologies. She holds a PhD from the University of Birmingham, where she researched the recognition of chirality at the nanoscale. During her previous role as Applications Scientist for SEM and AFM products at Keysight Technologies, she acknowledged the extreme importance of proper sample preparation for high-resolution imaging. Her main area of interest lies in discovering the outcome of processes occurring at the uppermost part of surfaces.
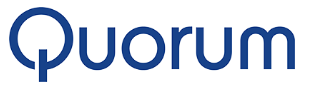
This information has been sourced, reviewed and adapted from materials provided by Quorum Technologies Ltd.
For more information on this source, please visit Quorum Technologies Ltd.
Disclaimer: The views expressed here are those of the interviewee and do not necessarily represent the views of AZoM.com Limited (T/A) AZoNetwork, the owner and operator of this website. This disclaimer forms part of the Terms and Conditions of use of this website.