A new generation of materials scientists is developing sustainable materials – and methods for making them – in response to warnings of an imminent climate catastrophe. Natural and plant-based composite materials are gaining traction, but can they replace traditional alternatives?
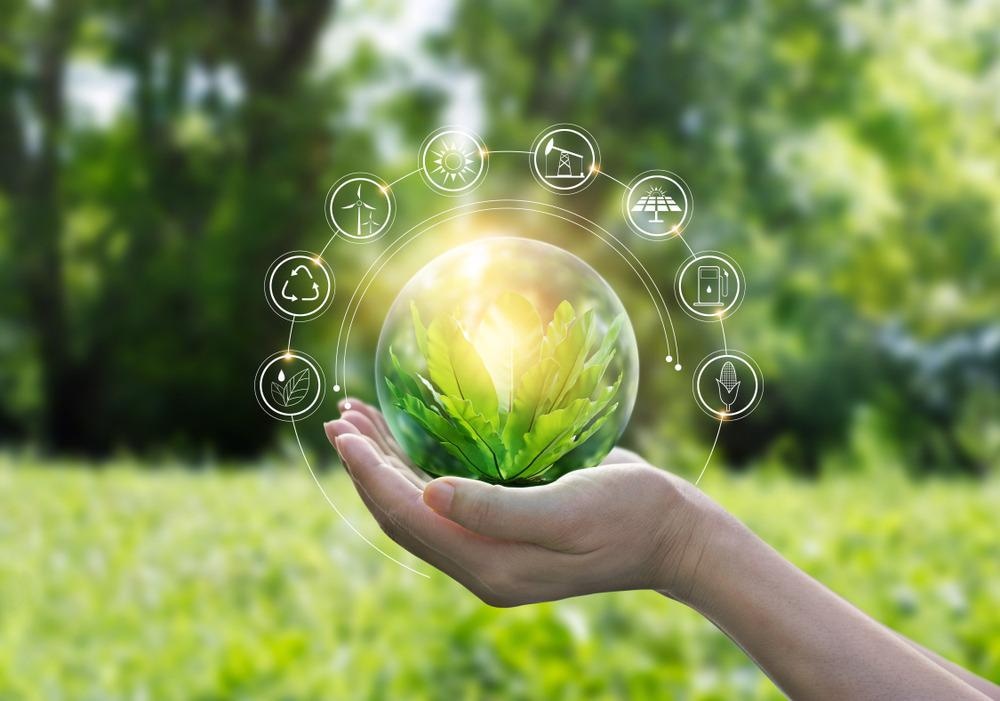
Image Credit: PopTika/Shutterstock.com
Pioneers in both research and industry are working to prove that, in fact, plant-based composites can replace traditional, unsustainable materials. A team from the Massachusetts Institute of Technology (MIT) recently engineered a plant-based composite made with polymer and cellulose nanocrystals (the structures that make trees and other plants so strong.)
Meanwhile, the largest ever natural fiber composite structure – a nacelle for an offshore wind turbine – was installed by Dutch shipbuilders Greenboats in the Harbor of Rotterdam, Netherlands, in summer 2021.
We Need a New Approach to Materials Manufacturing
Plant-based and natural composite materials are being developed in response to increasing demand for environmentally friendly, sustainable, and biodegradable composites.
This demand comes from increasing awareness, regulation, and obligations toward the environment, and the knowledge that manufacturing and building activities that recklessly consume resources will destroy the balanced ecosystems that maintain civilization on Earth.
Natural fibers are already well-established in the composite industry at large. They have demonstrated excellent physicochemical and mechanical properties in numerous studies in the last few decades.
These properties combine with good biodegradability (they decompose without releasing toxins into the environment), biocompatibility (they can be used safely in animal bodies), and renewable sourcing (materials can be grown again in a realistic timeframe, unlike oil for plastic which takes millions of years to form underground.)
Natural fibers could be from mineral or animal sources, but plant-based fibers are by far the most relevant. Unlike animal-based fibers like natural silk (which requires vast amounts of energy and freshwater to extract), plant-based fibers are actually sustainable materials from production through to their end-of-life. Plant-based fibers are more economical than animal-based fibers and are typically biocompatible, unlike untreated animal- or mineral-based fibers.
In many cases, plant-based fibers have already replaced fiber reinforcements made out of glass, carbon, and aramid in many composite applications. Automotive, aerospace, clothing, and pharmaceutical manufacturing sectors have all embraced plant-based fibers to varying degrees.
The Latest Development in Plant-Based Composites: Cellulose Nanocrystals
Cellulose is a naturally occurring – and abundant – polymer. It is the main structural component of all algae and plants. Each cellulose fiber contains reinforcing cellulose nanocrystals, called CNCs, which arrange themselves in a crystal-like nanostructure.
CNCs form the walls of plants’ microscopic cells and provide plants with considerable strength. They are both stronger and stiffer than Kevlar, and researchers believe they can be applied to make strong plastics that are produced sustainably.
In the last few years, scientists developed a method for extracting CNCs using acid hydrolysis. But incorporating the crystals into composite materials at large quantities has remained challenging: the CNCs tend to clump up and only bond weakly with the substrate material.
Plastic Alternatives: Where Are We Now?
New research by MIT scientists describes a composite containing a large proportion of CNCs, combined with a synthetic polymer. The composite is stronger and tougher than bone and harder than standard aluminum alloys. The research, overseen by MIT mechanical engineering professor John Hart, was published in the journal Cellulose in 2022.
The team mixed commercially available powdered CNC with a synthetic polymer in a ratio that would result in a gel solution. The viscosity of the solution was tuned so that the team could feed it through a 3D printer’s extrusion nozzle, or pour it into a cast as in conventional composite layering.
An ultrasonic probe was employed to disperse clumped-up CNCs in the gel, increasing the chances of individual crystals strongly bonding with the molecules of the polymer substrate. The resulting material uses up to 90% CNCs in the composite mix, the highest ratio of CNCs in a composite achieved so far.
The principal investigator, Abhinav Rao, a Ph.D. student working under Hart’s supervision, said:
“We basically deconstructed wood, and reconstructed it. We took the best components of wood, which is cellulose nanocrystals, and reconstructed them to achieve a new composite material.”
Plant-Based Composites in Wind Energy
Renewable wind energy could be a major contributor to a net-zero carbon economy in the future, but its contribution to the world’s sustainability goals is limited by its use of energy-intensive, non-recyclable, non-biodegradable materials in wind turbine manufacture.
The high engineering requirements for wind turbine components like blades – they have to be very large, very lightweight, and very strong – have made this challenging. However, Dutch shipbuilders Greenboats recently took the challenge head-on.
The first-ever natural fiber composite nacelle was installed in a Harbor of Rotterdam wind turbine in the Netherlands in summer 2021. A nacelle is the part of a wind turbine that houses the gearbox, drive train, brake assembly, and generator that work to harness electric energy from the rotation generated by wind.
The 7.3 m Green Nacelle in Rotterdam is installed on the 600 kW wind turbine’s rotor (44 m in diameter) and is satisfying ongoing engineering checks. Not only is it the largest nacelle ever made from plant-based composites, it is also the largest natural fiber composite structure ever made.
Is the Future of Composites Plant-Based?
Currently, examples like MIT’s CNC composite and Greenboats’ plant-based nacelle are at the cutting edge of sustainable materials research and application. However, the field is expanding quickly in both academia and industry, and the need for alternatives is becoming ever more clear.
Industry needs to adopt these new technologies at scale, and soon. Researchers, policymakers, and the consuming public can all accelerate this adoption by feeding more knowledge, guidelines, and demand for a better way to make materials back to industry.
References and Further Reading
Chu, J. (2022). New plant-derived composite is tough as bone and hard as aluminum. MIT. [Online] Available at: https://news.mit.edu/2022/plant-derived-composite-0210
Pilkington, B. (2021). The First-Ever Natural Fiber Composite Nacelle for Offshore Wind Turbines. AZO Cleantech. [Online] Available at: https://www.azocleantech.com/article.aspx?ArticleID=1196
Rao, A., Divoux, T., Owens, C.E., et al. (2022). Printable, castable, nanocrystalline cellulose-epoxy composites exhibiting hierarchical nacre-like toughening. Cellulose. Available at: https://doi.org/10.1007/s10570-021-04384-7
Syduzzaman, M., M., Abdullah Al Faruque, K. Bilisik, and M. Naebe (2020). Plant-Based Natural Fibre Reinforced Composites: A Review on Fabrication, Properties and Applications. Coatings. Available at: https://doi.org/10.3390/coatings10100973
Disclaimer: The views expressed here are those of the author expressed in their private capacity and do not necessarily represent the views of AZoM.com Limited T/A AZoNetwork the owner and operator of this website. This disclaimer forms part of the Terms and conditions of use of this website.