AZoM speaks with Dr. Rajashekar Badam from the Japan Advanced Institute of Science and Technology (JAIST) about his recently formulated method for anode fabrication that could pave the way to the very fast charging of lithium-ion batteries.
With current climate change concerns, why is it so important to shift from gas cars to electric vehicles (EVs)?
The whole world, by large, is in the phase of transition from its dependency on fossil fuel-based energy sources to more renewable ones. It is now more important than ever before that we make drastic resolutions regarding climate change. Vehicular pollution is a major contributor to overall pollution. Thus, the automobile industry is inching towards EVs to reduce both pollution levels and reliance on fossil fuels.
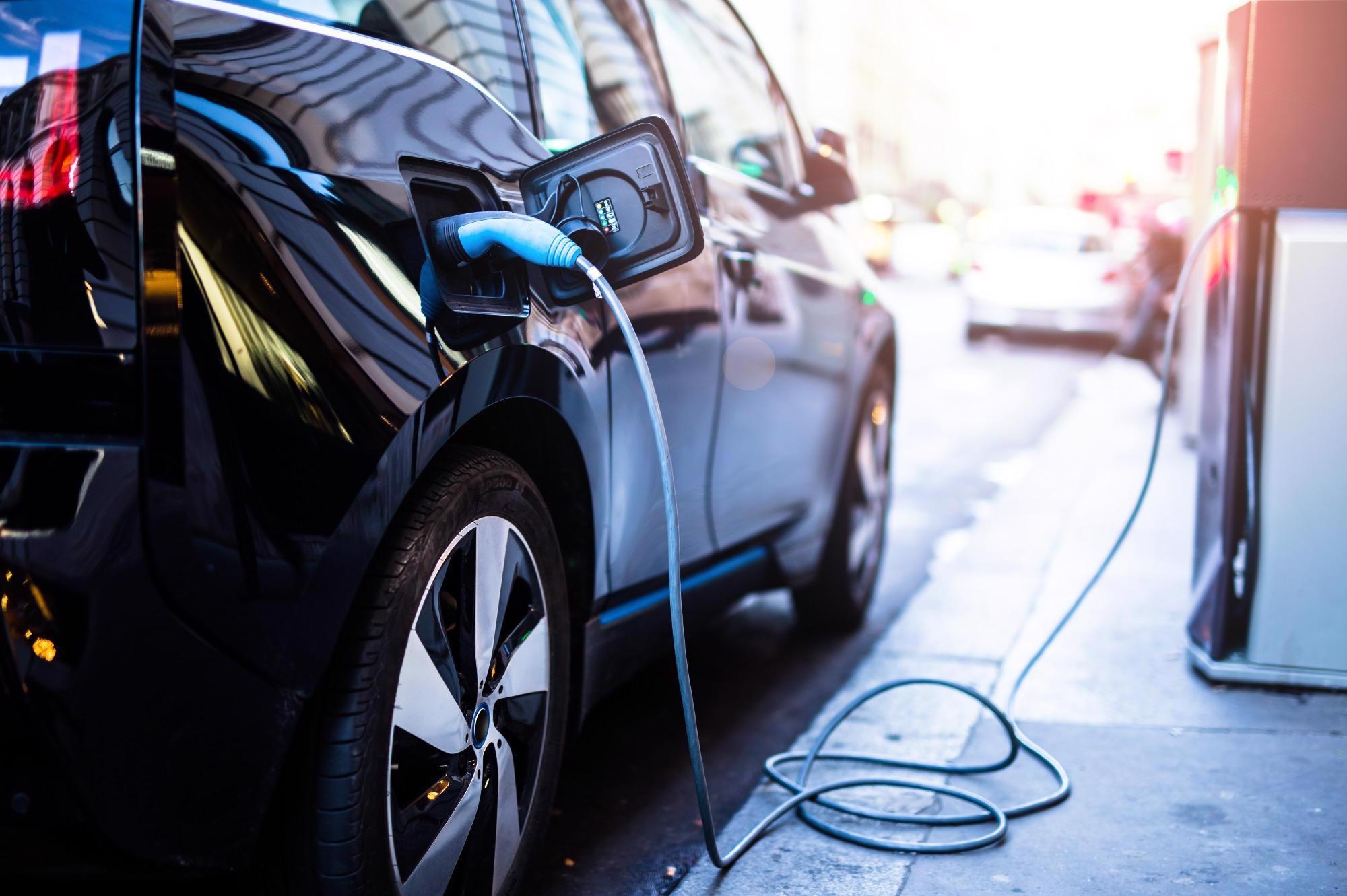
Image Credit: Shutterstock.com/guteksk7
Why is it important to enhance EVs to make them more appealing than conventional gas-powered cars?
Lithium-ion batteries are a key component of EVs. However, they are currently expensive due to the disparity in the distribution of Li and Co metals in several countries, and some of them are politically unstable.
Alongside safety, the durability of the battery used in EVs and the fate of the used battery stand as the key questions for the customers. These are some of the bottlenecks that hinder the mass market expansion of EVs.
Aside from autonomy, safety and durability, what is the main thing that people want from Evs?
Besides the aforementioned aspects, the most important enhancement that most people want is the reduction of charging time. Most of the current flagship EVs take at least 40 to 90 minutes to charge up completely. On the contrary, it takes just a few minutes to fill the tank of conventional gas-powered cars.
The current outlook of battery researchers and industry is to optimize the battery and its materials to enable super-fast charging.
What inspired your research into the enhancement of EV batteries?
Among the several types of anode materials, graphite is the only candidate that saw the face of commercialization. Unlike Li and Co, graphite is comparably less of a challenge to the industry when it comes to supply. However, most of the current EV industry prefers synthetic graphite over natural graphite for better performance.
Synthetic graphite is expensive and has severe impacts on the environment. Furthermore, graphite does not have the capability to reach the fast-charging demand of the EV industry due to its inherent disability of slow Li-ion diffusion kinetics.
Graphene (and other 2D materials) could possibly help to solve these issues, but the commercialization is still far-fetched due to its cost.
We saw a huge scope in exploring this lacuna with the unique skill that our team has at JAIST, combining materials science, polymer chemistry and electrochemistry.
At present, it takes around 40 minutes to recharge EVs, while traditional gas cars can be ‘recharged’ in just a matter of minutes.
What charging time needs to be achieved to make EVs an attractive and viable alternative to gas cars?
In order to make EVs a viable alternative to conventional gas cars, the charging time of the battery needs to be reduced to at least 15-30 minutes. This will poise a level of customer satisfaction. But the current idea is to achieve 10-minute charging to reach 80% of its State of Charge (SoC), and this type of charging is termed extreme fast charging (XFC).
Can you provide an overview of how your team achieved extremely fast-charging lithium-ion batteries (LIBs)?
Improvement of Li-ion diffusion within the anode and the available active sites for lithiation are the key aspects that determine the fast charging capability and high specific capacity (total amount of charge that can be stored per gram of active material) of the anode material.
As a design strategy, both these material properties can be modified by increasing the interlayer spacing of the carbon layers or introducing electrochemically active hetero atom doping such as nitrogen. Though there have been numerous reports over the past decade based on the nitrogen-doped graphene/carbon using graphene oxide or sucrose as the source of carbon and urea/melamine as the source of nitrogen, the maximum doping that could be achieved was up to <15% with a char yield of <40%.
These low char yield processes generate high amounts of greenhouse gases like CO2 during the preparation. Hence our strategy was to develop a facile method with both a single precursor as a source of carbon and nitrogen with high char yield and increased interlayer spacing.
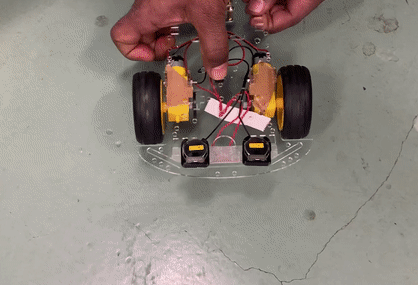
Toy car demonstration with two CR 2025 coin cells using PY-PBI-800 anodes and LiCoO2 cathodes.
With this background, our research group (Prof. Noriyoshi Matsumi, Prof. Tatsuo Kaneko, Sr. Lecturer Rajashekar Badam, Technical Specialist Koichi Higashimine, Research Fellow Yueying Peng, and student Kottisa Sumala Patnaik) used heat-resistant polybenzimidazole, a bio-based polymer with nearly 22% of nitrogen atoms, as a single source to prepare the carbon material.
Using a simple pyrolysis method at 800 ℃, a nitrogen-doped carbon was prepared with an improved interlayer spacing of 3.5 Å compared to that of graphite with 3.3 Å, and nearly 17 wt% of nitrogen was retained in the material.
In general, the wider interlayer space improves the free diffusion of Li-ions that promotes the fast charging process. The char yield was found to be ~95% in our methodology, which means that we have reduced nearly 55% of greenhouse gas emissions during the material preparation itself.
In addition, it was observed using XPS that graphitic, pyridinic and pyrrolic types of nitrogens were introduced into the carbon matrix.
When galvanostatic charge-discharge was conducted using anodic half-cells, the novel nitrogen-doped carbon material, PY-PBI-800, outperformed graphite at a high rate (current rate equivalent to 10 C for graphite) with at least twice the capacity for up to 3000 cycles.
Furthermore, the cells were cycled at an extremely fast charging rate of 7.5, 11 and 18.6 Ag-1, which takes 25, 15 and 3.5 seconds to charge. The battery showed stable performance for up to 3000 cycles with more than 80% capacity retention.
What techniques did you use to verify the successful synthesis of the precursor material?
In this study, we verified the successful synthesis of the precursor material using FT-IR spectroscopy.
Did you compare the performance of this material with any other commonly used materials, and if so, what were the results of such a test?
The novel carbon material, PY-PBI-800, has been compared to the most commonly used battery-grade graphite. At current rates of 0.04, 0.07, and 0.20 A g−1, PY-PBI-800 delivered discharge capacities of 388, 326, and 254 mA h g−1, respectively, whereas graphite delivered discharge capacities of 258, 244, and 145 mA h g−1.
In summary, PY-PBI-800 showed nearly twice the capacity of graphite at all the charging rates with exceptional stability.
What are the advantages of this proposed anode material?
The novel carbon material, PY-PBI-800, is derived from a bio-based polymer as a precursor. Approximately 95% char yield reduced greenhouse gas emissions during the pyrolysis method. The cost of PY-PBI-800, in terms of lab-scale preparation, was found to be nearly 45 times lower than that of commercial N-doped graphene.
The PY-PBI-800 anode material has many interesting advantages, such as high initial coulombic efficiency, higher specific capacity, cyclability and extremely fast charging for several thousands of cycles, etc. with respect to electrochemical behavior.
Most importantly, various structural modifications can be made to the polymer precursor to tune the interlayer spacing, nitrogen doping content, surface area, pore size, etc., of the carbon material. Hence, there is a large possibility to tune the structure and, thereby, the anode material’s activity, which is impossible using conventional precursors like sucrose/graphite and urea/melamine.
When will this fast-charging capacity be implemented into commercially-available EVs?
The department of energy, USA., has set a target to achieve XFC within 10 minutes by 2028. Thus, the commercial realization of XFC could be within the next 5-10 years.
What are the next steps for your research?
Various structural modifications can be done to the existing polymer precursor to optimize certain characteristics, such as surface area, interlayer spacing, porosity, content and type of nitrogen doped into the carbon matrix.
Modification of pyrolysis conditions will also have implications on the structural aspects and, thereby, electrochemical properties of the carbon.
In the future, we aim for societal implementation through joint research with industries. We hope that the development of fast charging technology will lead to the development of technologies that contribute to the realization of a low-carbon society.
About Dr. Rajashekar Badam
Dr. Rajashekar Badam has been working as Senior Lecturer at the Graduate School of Advanced Science and Technology, Japan Advanced Institute of Science and Technology (JAIST), Japan, since 2019. He obtained his M.Sc in Chemistry from Sri Sathya Sai Institute of Higher Learning, India, in 2011. He obtained his Ph.D. in Materials Science from JAIST with an “outstanding graduate award for the year 2016”. Furthermore, he worked at Toyota Technological Institute, Japan, as a Post-doctoral fellow. In April 2018, he joined the Matsumi lab, JAIST, as Asst. Professor before being promoted to Senior Lecturer in the same group. His key research interests are energy materials, electrochemistry and electrocatalysis. In 2021, he was a recipient of the young researcher award by Tanaka Kikinzoku Memorial Foundation.
Disclaimer: The views expressed here are those of the interviewee and do not necessarily represent the views of AZoM.com Limited (T/A) AZoNetwork, the owner and operator of this website. This disclaimer forms part of the Terms and Conditions of use of this website.