Unmanned aerial vehicles, commonly referred to as drones, are aircraft that operate without the presence of a human pilot on board. They play a key role in an intricate unmanned aircraft system (UAS) comprising a ground-based controller and a communication mechanism that enables interaction between the controller and the UAV.

Image Credit: Superior Sensor Technology
During operation, the UAV can be controlled remotely by a human operator or can operate independently through internal electronics. However, in both scenarios, sensors play a crucial role in ensuring the proper execution of the UAV’s intended actions.
Unmanned Aerial Vehicles offer unique advantages to the aviation industry. This includes the ability to complete remote sensing and surveillance without a human pilot. UAVs rely on a variety of sensors that measure and adjust the system to environmental conditions. These sensors are vital to the safe and efficient operation of the UAV.
The following sensors are vital to the operation of UAVs:
- Gyroscopes are responsible for detecting and measuring angular velocity, rate of rotation, and degree of tilt.
- Accelerometers detect linear movement along any axis of the UAV.
- Barometers maintain a stable altitude by measuring air pressure.
- Pitot tubes measure the airspeed and angle of attack (AOA) to determine the aerodynamic forces of winged UAVs.
- Magnetometers determine the heading of the UAV by measuring the magnetic field strength and direction.
- GPS’ are used to establish the position of the UAV.
- Obstacle avoidance sensors are required to prevent UAVs from colliding with objects.
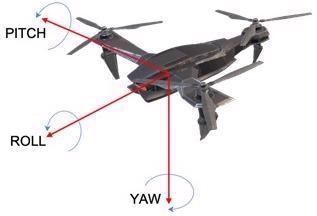
Figure 1. UAV Roll, Pitch, and Yaw. Image Credit: Superior Sensor Technology
This article will examine the first four sensors, which rely heavily on highly accurate pressure sensors. Gyroscopes, accelerometers, and barometers are sometimes combined to create an Inertial Measurement Unit (IMU) to measure crucial parameters such as pitch, roll, and yaw of the UAV. At the same time, the pitot tube determines airspeed.
A combination of these sensors ensures the reliable and precise navigation and control capabilities of the UAV, ensuring it can operate safely and efficiently, regardless of the environment.
Differential Pressure Sensors in IMUs
The IMU system heavily depends on the functionality of differential pressure sensors to detect and signal necessary adjustments to the UAV. These sensors play essential roles in three specific areas within the system. Their rapid response to pressure fluctuations allows the UAV to execute the corrections needed for optimal performance promptly.
Barometer
Utilizing a barometric pressure sensor is crucial for precise altitude monitoring, particularly due to the significant influence of altitude on air pressure. As altitude increases, air pressure decreases accordingly. Thus, a barometer facilitates swift and accurate measurement of atmospheric pressure to maintain optimal flight elevation.
Accelerometer
Accelerometers measure the velocity’s rate of change over time. They are responsible for establishing the UAV’s movements and orientation. When combined with accelerometers, differential pressure sensors can monitor air pressure variations in the UAV’s nose. This enables a stabilized rate of movement for the UAV regardless of wind conditions or other environmental conditions.
Gyroscope
Gyroscopes play a vital role in measuring angular movement and can be enhanced by integrating differential pressure sensors. These sensors help detect variations in air pressure caused by changes in angles, and they are applicable to movements along any axis, whether roll, pitch, or yaw.
Differential Pressure Sensors in Pitot Tubes
Pitot tubes are installed on the outside of a UAV, utilizing a differential pressure sensor to establish the airspeed of the UAV in reference to its environment. These tubes gauge the disparities in static pressure (the pressure of stagnant air) and ram pressure (the pressure of air in motion) experienced during the UAV’s forward motion. With increasing UAV velocity, the disparity between the pressure readings widens.
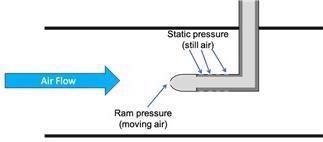
Figure 2. Pitot Tube Diagram. Image Credit: Superior Sensor Technology
Superior Sensor’s Technology Advantage
NimbleSenseTM architecture was developed by Superior Sensor as an integrated platform. This pioneering system has incorporated innovative pressure sensing technology and customizable building blocks to provide unrivaled reliability and precision while reducing system costs.
Superior Sensor is revolutionizing UAV performance with its cutting-edge ND Series of pressure sensors. The ND015A barometric pressure sensor provides unparalleled accuracy in measuring atmospheric pressure, ensuring stable drone altitude maintenance.
Additionally, the Multi-Range differential pressure sensors, such as the ND005D, offer highly accurate airflow measurements, allowing UAVs to travel at precise speeds. Together, these sensors establish a new benchmark for UAV performance by offering:
Lowest Noise Floor
Superior’s pressure sensors have advanced digital filtering technology that restricts noise from impacting system performance. This guarantees that error signals resulting from noise are removed before they distort the accuracy of air pressure readings.
Highest Levels of Accuracy
The key to reducing the potential impact on a UAV’s trajectory is to use a differential pressure sensor with exceptional levels of precision. The ND Series provides precise measurements with an effective resolution of 19 bits, resulting in measurement accuracy within 0.05 % of the designated range and a total error band (TEB) of only 0.10 % of FSS.
Fastest Response Times
The speed at which a pressure sensor updates its measurement data is as critical for a UAV’s optimal function as accuracy. Receiving the updated pressure measurements quickly allows the drone to efficiently maintain precise positioning. The ND Series can provide options to configure update rates supporting speeds as fast as 2.25 milliseconds.
Sensor Customization and Flexibility
A major advantage of a single, adaptable sensor integrated into the design of UAVs is the variety of customizations available for numerous applications on the drone. This feature enhances the efficiency of design and reduces product costs.
The ND Series sensors are pin-compatible. The same sensor can be utilized for all UAV pressure sensing needs. Depending on the specific requirements, each sensor can be optimized and offers customization of features like pressure range, bandwidth filter, and output data rate.
Conclusion
For successful operation, UAVs must receive a dependable stream of flight information. Pressure sensors are a vital component in providing this data. The sensors need to meet these demands by filtering environmental interference quickly, maintaining pinpoint precision despite variable conditions, and meeting the ever-changing demands of the UAV market.
Superior Sensor Technology’s ND Series offers an innovative solution with unparalleled design flexibility and exceptional performance. For additional information, please visit the product page for the ND Series of sensors.
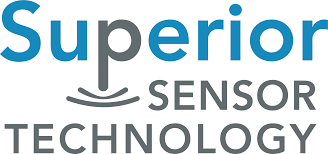
This information has been sourced, reviewed and adapted from materials provided by Superior Sensor Technology.
For more information on this source, please visit Superior Sensor Technology.