3D printing is an additive manufacturing process that turns a digital model file into a physical object. A 3D printed object is created by layering materials sequentially using additive processes until the object is generated.
Each of these layers can be visualized as a thinly sliced cross-section of the object.
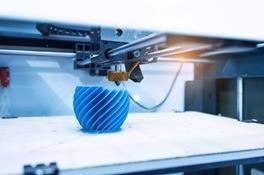
Image Credit: Superior Sensor Technology
3D printing is the total opposite of subtractive manufacturing, which involves cutting out/hollowing out a piece of plastic or metal with machinery such as a milling machine. In comparison to traditional manufacturing methods, 3D printing allows for the production of complex geometries with less material.
Most Common Types of 3D Printers
3D printing is a “catch-all” term that encompasses a variety of additive manufacturing technologies and processes. At least 10 different 3D printing manufacturing methods are currently available.
While all of them can be used for rapid prototyping and manufacturing, technological advancements and lower costs have led to the adoption of some methods by hobbyists for home use and small businesses for light manufacturing.
These specific technologies come in small desktop versions and are used in a variety of applications, including dentistry, jewelry, confections, fashion (for example, sneakers) and toys.
Fused deposition modeling and stereolithography are the two most common types of 3D printers.
Fused Deposition Modeling (FDM)
FDM, also known as fused filament fabrication (FFF), is the most widely used consumer-level 3D printing technology. FDM uses a heated nozzle to extrude thermoplastic filaments into an object, melting the material and applying it layer by layer to build the final product.
Stereolithography (SLA)
In 1986, SLA was created for the first time. This 3D printing method is still very popular today, particularly for professional applications. Photopolymerization is the process by which SLA 3D printers cure liquid resin into hardened plastic. SLA is a better technology than FDM for producing complex parts and those that must be airtight or watertight.
Other 3D printing technologies work with materials other than plastic. This includes ceramics, concrete, metals, paper and even edibles like chocolate.
Typically, these alternative technologies necessitate more specialized and costly 3D printing equipment. Whatever the requirements are, there may be a device that is a better fit than FDM or SLA-based printers.
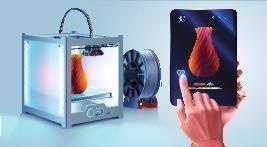
Figure 1. Desktop FDM 3D Printer. Image Credit: Superior Sensor Technology
Potential for Pressure Sensors in 3D Printers
The value that differential pressure sensors could bring to 3D printers is comparatively clear. For beginners, attention should be drawn towards the nozzle where there is a demand for a comfortable and predictable flow of material.
If not, there is a considerable threat of having inconsistent material placement when the object is being made. For instance, it is crucial to see if the nozzle is being hindered by a filament or another object which tends to impact the intended operation. Quantifying the pressure of material flowing via the nozzle will verify if this is the case or not.
Also, it is essential to verify that the “arm” of the printer is applying a sufficient amount of pressure (but not too much) as each layer is “printed” on top of the previous one. This guarantees that the layers are well-bonded; if not, the object may wind up lopsided or warped.
In this case, employing a pressure sensor can help quantify the arm pressure against the object across the layering process.
Also, differential pressure sensors can be employed to alter the structural soundness of the object as it is being fabricated. If values deviate from the pressure parameters, the sensor can instruct the printer to decelerate the process.
By doing so, the present layers will have enough time to “cool down” and stiffen. This will guarantee that the object fulfills the original design parameters.
Ultimately, making sure the object is structurally sound across fabrication will help decrease the need for printing support structures for any parts of the 3D model that expanded beyond the core base.
The pressure control coming from the differential pressure sensor enables the printer to alter its speed until the essential materials are sufficiently cured to the point of being able to aid the overhang of the structure.
This decreases the amount of material required to make the object and normally leads to a faster printing process as the need to “print” the support structures has been removed.
Superior Sensor’s NimbleSenseTM Architecture for 3D Printing
The NimbleSense architecture has a remarkably low noise floor, which is ideal for the accurate, low-pressure measurements that 3D printers demand to improve precision and performance.
But the benefits of NimbleSense expand beyond the low noise floor. Many of its application-specific building blocks provide additional value for 3D printers.
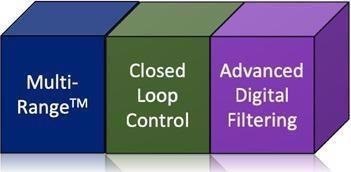
Figure 2. NimbleSense Building Blocks that can Benefit 3D Printers. Image Credit: Superior Sensor Technology
Multi-Range TechnologyTM
Multi-Range technology enables one pressure sensor to function at optimal performance levels over several different pressure ranges. Based on the materials used for the object being “printed,” the level of pressure needed by the nozzle and the proper pressure required for structural soundness will vary.
Multi-Range allows “on the fly” pressure measurement adjustments to fulfill the needs of several projects irrespective of the materials utilized or pressure required.
Closed Loop Control
A combined closed loop control could improve the speed, responsiveness and reliability of the 3D printer’s pressure sensing system.
The potential to do so decreases loop delays significantly and guarantees that readings are precise by directly regulating any motors, valves and actuators that tend to control the function of the arms, nozzle and other parts of the 3D printer.
Advanced Digital Filtering
3D printers are loud and can be impacted by vibrations. Each of these factors can have a significant impact on the accuracy of pressure sensors.
Using Superior Sensor Technology’s integrated advanced digital filtering technology, noise can be removed before impacting the 3D printer. Therefore, the noise is nullified before it becomes an error signal that can lead to inaccurate readings.
Conclusion
The light manufacturing landscape is changing with the development of 3D printing technology.
As 3D printers become more commonly employed in various market applications, the ability to guarantee accurate material disposition and structural integrity will set the best performing products apart from the rest of the field.
Differential pressure sensors, particularly those provided by Superior Sensor, provide a simple and economical solution.
To find out more about the NimbleSense architecture, or talk about a 3D printer project, users can visit Superior Sensor’s technology page or contact the company directly.
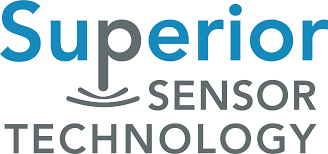
This information has been sourced, reviewed and adapted from materials provided by Superior Sensor Technology.
For more information on this source, please visit Superior Sensor Technology.