Automotive manufacturers are aware that the views of consumers are quickly shifting towards an acceptance of greener transportation. This is driving newer or improved processes in the manufacturing of electric vehicles (EVs).
As there is an increasing interest in producing efficient EVs, the internal combustion (IC) engines decline seems inevitable.
As phasing out of the IC engine begins, the number of drive train components necessary will decrease significantly. Therefore, parts that do remain continue to become crucial to the vehicle’s operation and efficiency, including the transmission components in which the high torque from electric motors is converted into RPMs at the wheel.
In order to make EVs viable, improving long-distance driving without stopping, relative to IC engines, is a key factor. EV gears have a central role to play in increasing such ranges. To achieve this, surface textures must be reduced, ensuring surface friction is ultimately reduced while maintaining a good level of lubricity.
Additionally, unlike louder IC engines that conceal the drive train’s noise, EVs are quiet. As a result, it is essential to produce the necessary gear surface texture and waviness specifications to enhance the interactions of the gear’s teeth while limiting any contingent noise.
Role of Precision Metrology
Precision metrology has the capacity to ensure that the production process of gear manufacture is optimized. The high value of processed gears suggests a preference for non-contact measuring technologies.
Due to the geometries and smoother surfaces of EV gears, tactile technologies may present more of a challenge when in use. They do not have the ability to reach the key inspection areas or may result in surface scoring. Therefore, key automotive OEMs are increasingly dependent on 3D non-contact optical profiler solutions.
Within the domain of non-contact metrology, an increasing number of EV parts are being measured using coherence scanning interferometry (CSI). This technology is dependent on specialized optical microscope objectives that offer appropriate imaging and magnifying of a surface while measuring its 3D topography.
CSI-based systems, including ZYGO’s Nexview, are defined by their ability to provide extremely stable measurements, easy access to the measurement area, as well as the assortment of objectives that must be adhered to in order to meet the demanding requirements for on-the-floor production metrology.
Field stitching capability presents further advantages where EV gear metrology is concerned. The instrument user can generate a matrix of overlapping measurements, which may be stitched together to produce a measurement larger than can be achieved using a single objective.
For EV gears, this means the capacity to measure the texture of the surface across a gear flank — from edge-to-edge — or from the root to the tip of the gear. ZYGO’s proprietary stitching algorithms have the ability to conduct these stitched measurements over non-planar surfaces, such as teeth on hypoid gears, meaning the user can re-measure with high-precision consistency.
Looking Ahead
As the EV market inevitably expands, manufacturers are presented with significant challenges as they come to terms with the necessity for technological advancements.
The requirement for advanced finishing and grinding technologies is at the top of the list in order to fabricate precise, complex surface features in gear-teeth to improve efficiency and reduce noise, thereby leading to an improvement in customer satisfaction.
Optical metrology is a dynamic inspection method that plays a key role in validating gear quality and achieving design intent. Consequently, it has become the current go-to metrology solution, benefiting from the fact that it is a rapid, non-destructive, non-contact, highly sensitive method with extraordinary accuracy and resolution.
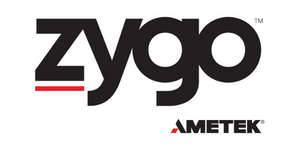
This information has been sourced, reviewed and adapted from materials provided by Zygo Corporation.
For more information on this source, please visit Zygo Corporation.