AZoM speaks to Dr. Ralf Dupont, president of Levicron about the potential of the new (U)ASD-H20A motor spindle for semicon industries.
Image Credit: Levicron
Levicron specializes in the production of high-speed ultra-precision motor spindle solutions for CNC machining. Where its main focus has been on the manufacturing of optical and precision components, Levicron is now close to finishing the development work for a new fully automated high-speed precision spindle to give Semicon industries a tool for the future.
Where up until now the consumer dictated production volumes, in Semicon industries, automation has now become the driving force, and a year-over-year production increase of 100% for Semicon products has been forecasted.
Looking at other industries and global trends of fully automated and controlled production makes it clear that sensors, data storage and data processing have become a very important goal. Besides the global trend of Industry 4.0, the IoT (Internet of Things) also covers both industrial and domestic applications. Hundreds of sensor signals, processed through a situation-based control system, are necessary for an autonomous car. But simple things like lights, heating or refrigerators are already at a high level of automation.
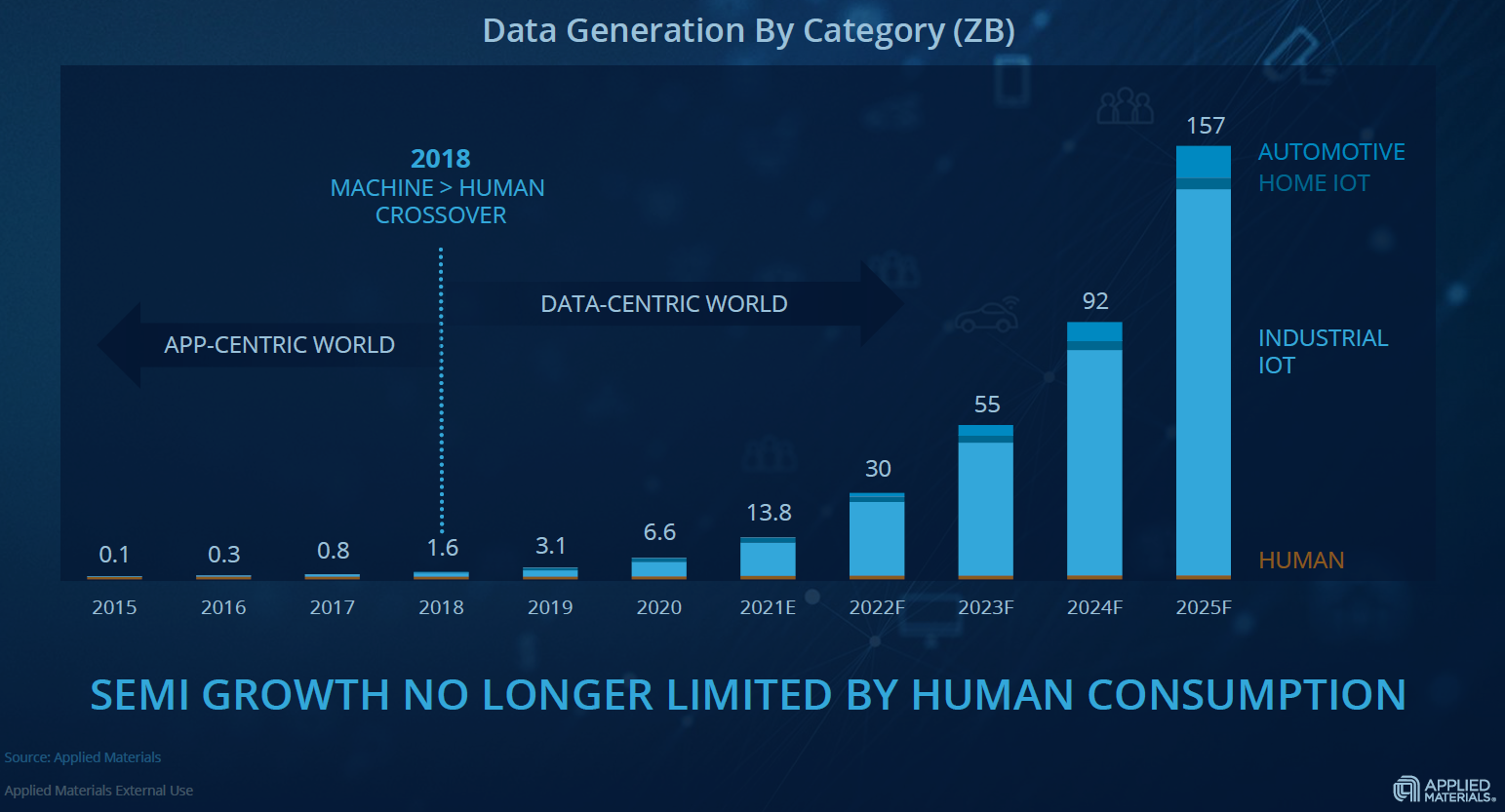
Figure 1. Forecasted semicon growth derived by data generation
Image Credit: Applied Materials
With electronic and optoelectronic components becoming smaller and smaller, more integrated and grouped electronics (“electronic packaging”) are becoming essential, which fundamentally changes the requirements of machine tools. With fiber optics replacing copper solutions, optoelectronic components now highly rely on precision and surface finish. Thus, automated machining solutions, higher spindle speeds for smaller tools, thermal invariance and improved dynamics have to be accompanied by reduced machining tolerances and better surface finish.
Why is the current situation in Semicon industries classed as critical?
Semicon products, such as mobile phones, computers or electronic gadgets, like intelligent lighting, have thus far been consumer-driven. Not only has the production side of things seen an enormous grade of automation, but also the domestic side like roller-shutters, lights, refrigerators and cars. Combining more and more electronic components into an integral component (packaging) requires multi-stage production processes with improved accuracies.
All of the above-mentioned aspects have been driven by automation rather than the consumer and have thus led to a forecasted increase in Semicon production of 100% year over year until 2026.
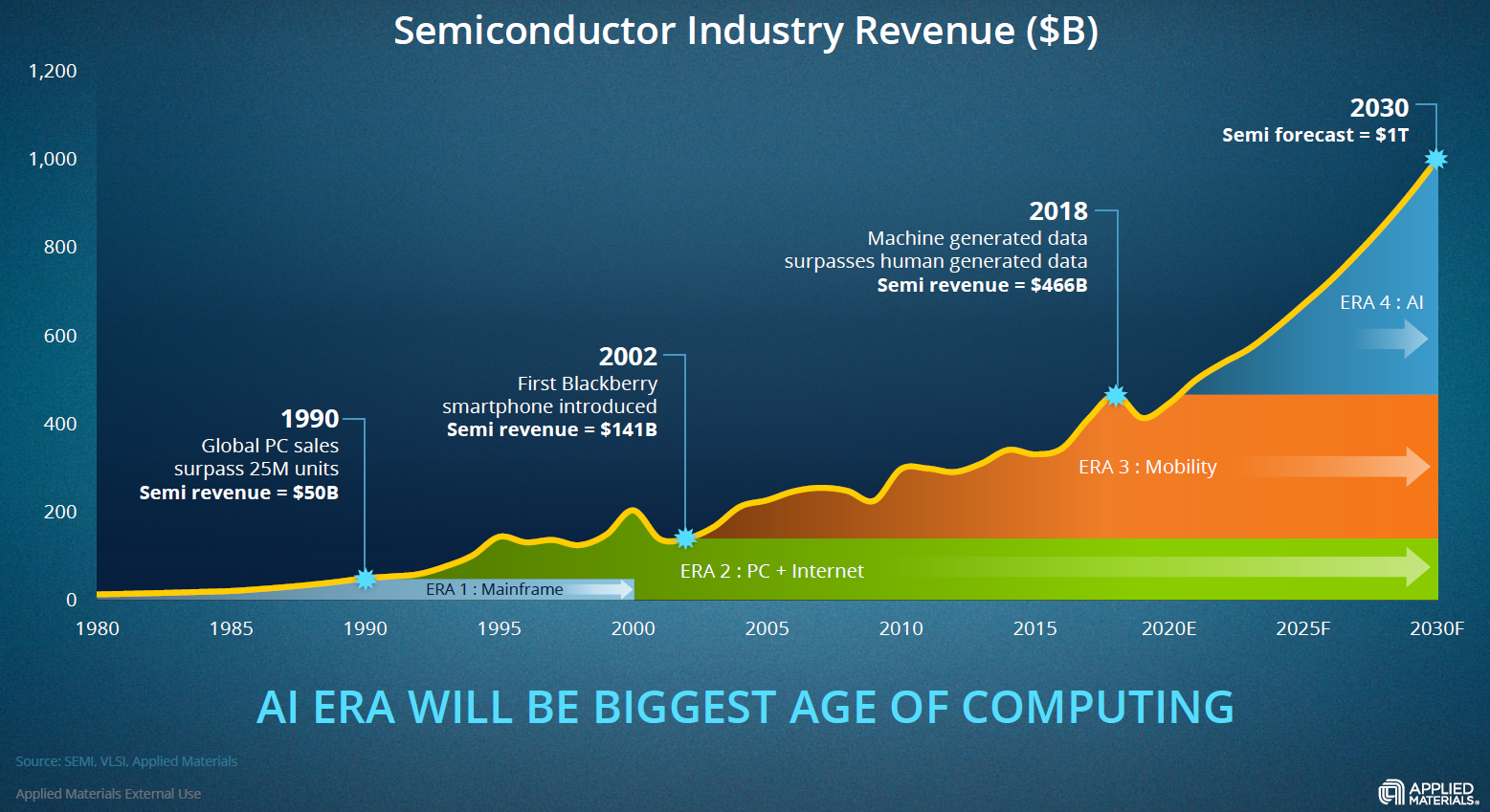
Figure 2. Predicted revenue shares by industrial sector
Image Credit: Applied Materials
Electronic parts are also becoming smaller and smaller, with even smaller tolerances. These machines not only feature comprehensive automation systems but require higher spindle speeds for smaller tools, better dynamics - including spindle dynamics - and a more sophisticated thermal stability to stay within the machining tolerances. Current mobile phones are a good example of how huge this industry is. Major mobile phone manufacturers estimate approximately 20 mio. phones of a single model are made. For production they require about 15.000 CNC, machine tools, plus an installation area, tools, a sufficient power supply and other accessories.
The type of CNC machine tool that is currently being used is not only way beyond its productivity and accuracy limits but has also pretty much reached the end of its life cycle. A machine type change thus seems imminent.
Could you please describe the starting point of the development and why technologies from Levicron and the new spindle solution will make a difference?
Precision, speed and CNC functionality, like automatic tool clamping, are the main features of all our spindle products. Our patented aerostatic bearing system not only allows higher speeds like other air bearing spindles, but it also gives ultra-low errors in motion and thus enables the machining of optical molds and components. We always go beyond the limits that everyone believes are set in stone.
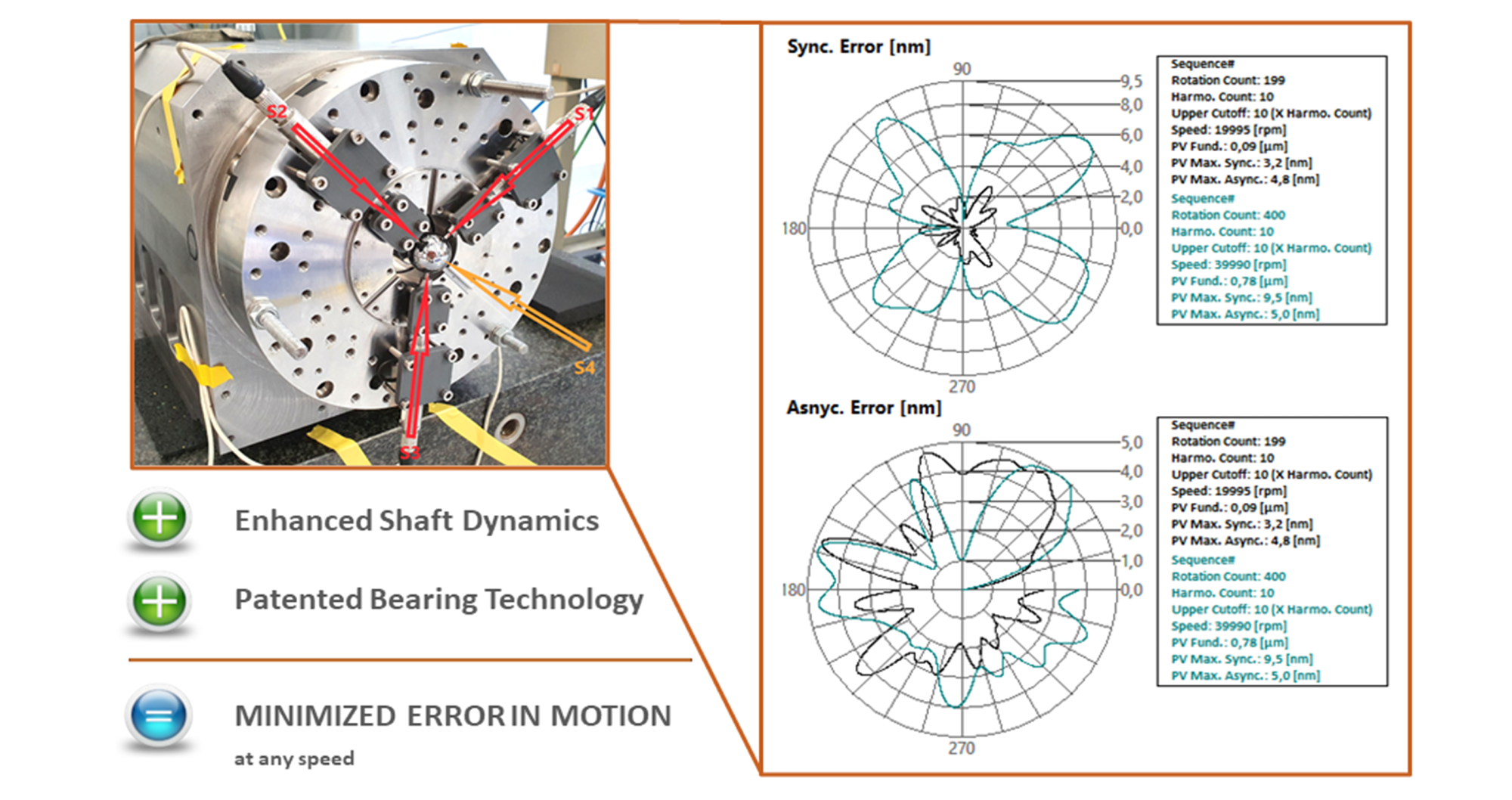
Figure 3. Combining Ultra-Precision with Speed
Image Credit: Levicron
With our technologies in place, it was only a small step to identify the solution to help Semicon industries with productivity, accuracy and thermal/dynamic stability.
With our spring-less HSK clamping system SLH-x in size HSK-E20 and a faster spindle that is capable of speeds of up to 120.000 rpm and 150.000 rpm, we cover both automation and productivity. The non-contact bearing system not only provides high speed and unlimited S1 times, but it also enables 100% wear-free operation even at the highest speeds.
By transferring the symmetrical spindle design and the thin-film liquid cooling from other very successful spindle models, like our ASD-H25/A e.g., we also add dynamic and thermal stability to this equation. All things I see as mandatory for the next generation of CNC machining centers.
What spindle model is this, and what are its main features?
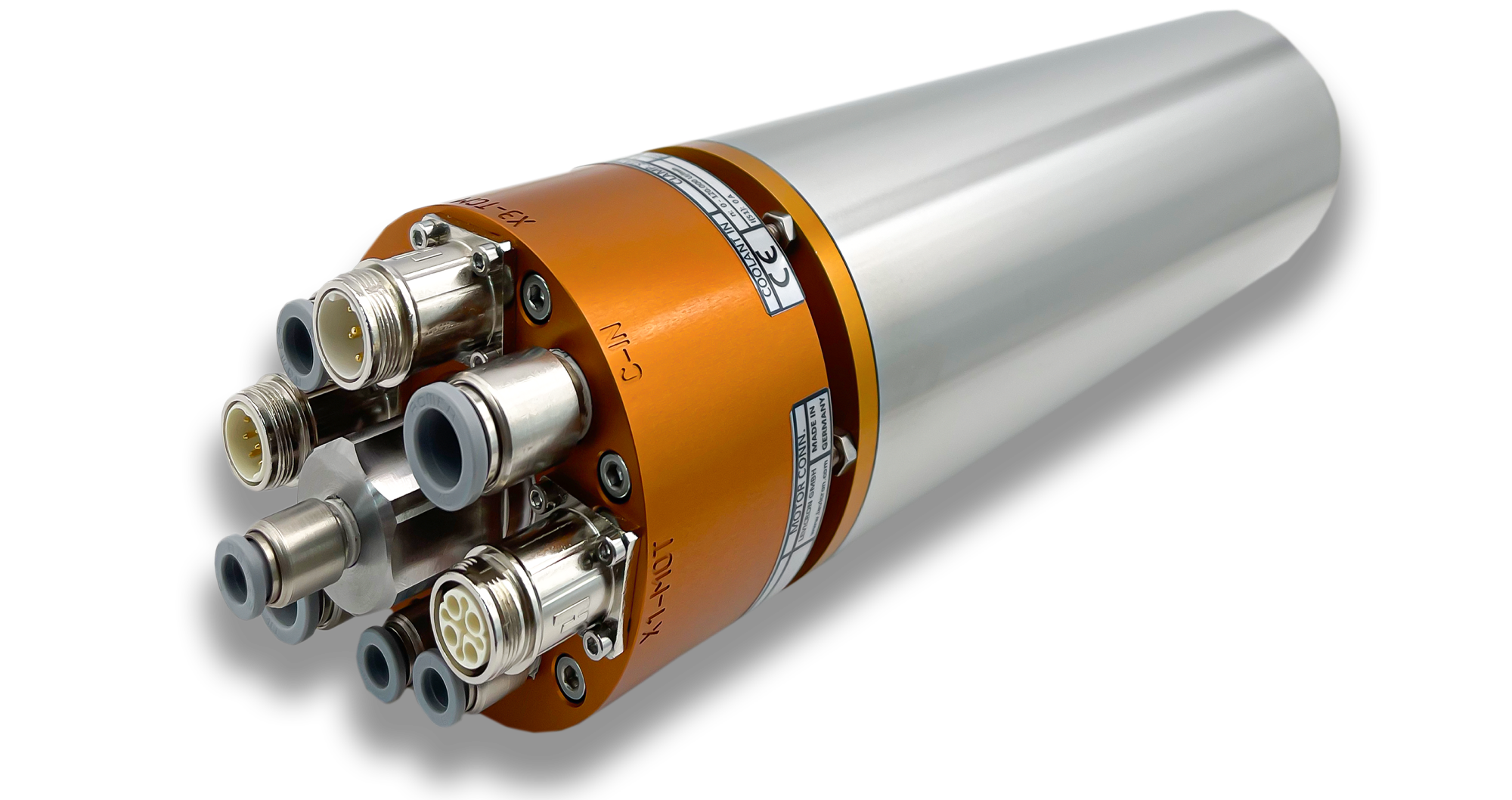
Figure 4. ASD-H20A - High-Speed Semicon Routing with up to 150.000 rpm and HSK-E20
Image Credit: Levicron
(U)ASD120H20A and (U)ASD150H20A, where “ASD” stands for “Air-Static-DC”, “120” or “150” for the nominal speed in 1.000 rpm, and “H20” for automatic tool clamping with HSK-20 interface. “(U)” means that this spindle model also can come with our high-pressure aerostatic bearing system that gives approximately three times higher load capacities than the standard model.
From its name, you can derive its main features, but there is more. Speeds up to 150.000 rpm with HSK-E20 tools is new and outperforms the fastest spindle speed available with this tooling system by 66%. The aerostatic bearing system not only enables these speeds but also provides a wear-free operation and an unlimited S1-time where the customer can use the spindle at top speed for an unlimited time. Roller-bearing spindles on the other hand have to stop at some point for the bearings to cool down and be re-greased. That being said, this also means that the thermal behavior is not only better, but constant, and so is thus the machine temperature stability. The bottom line is, that the machine becomes more productive and stable with reduced downtime at the same time.
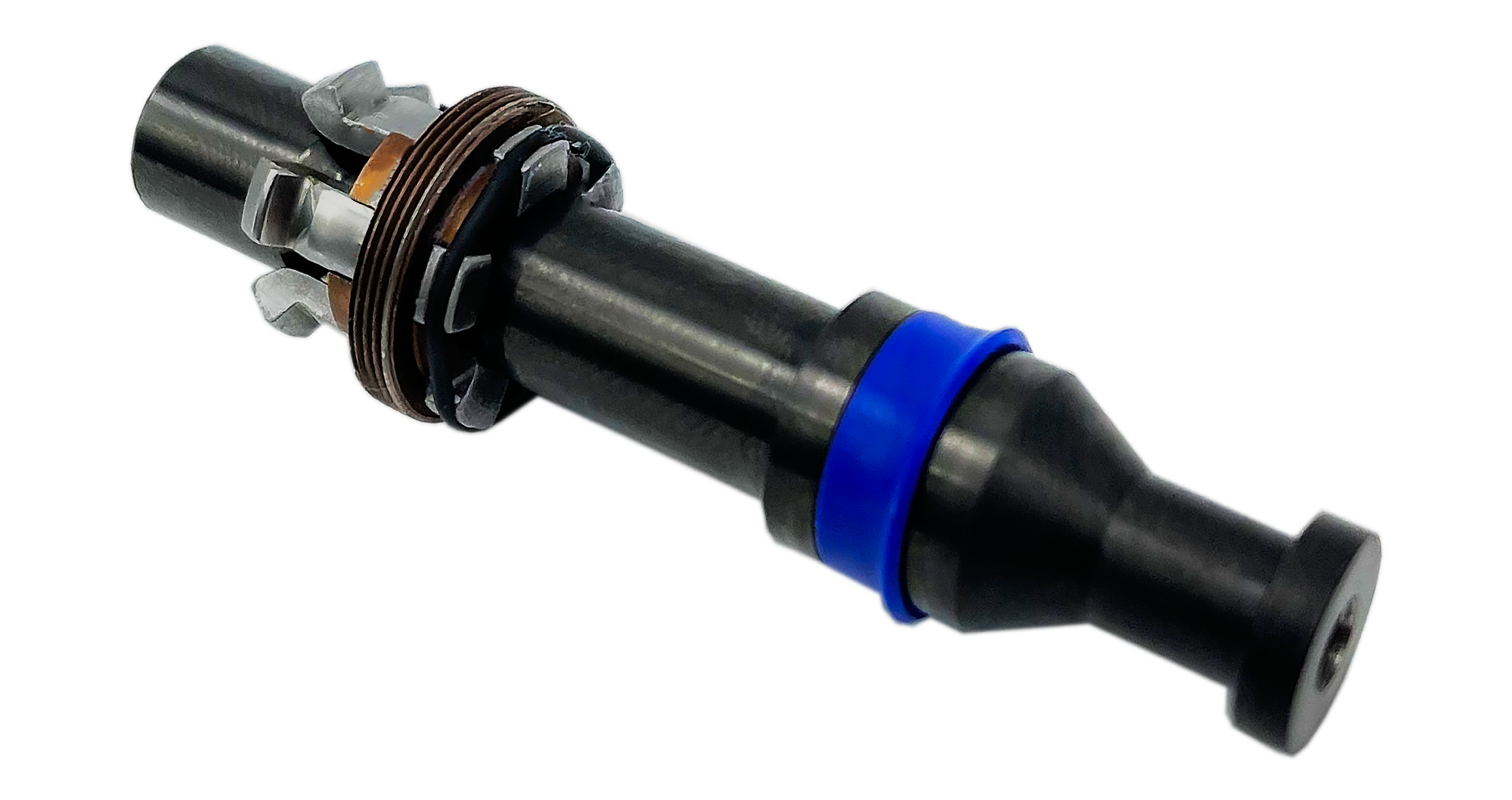
Figure 5. SLH-x, ultra-compact HSK Clamping Shaft Units - Big things have small beginnings
Image Credit: Levicron
Not only is the bearing system essential in this context, but most spindle-integrated tool clamping systems with interface HSK-E20 are also limited to 90.000 rpm. Back in 2017, we developed our very successful HSK clamping units “SLH-x” which do not use springs to retract and clamp a tool and are thus much lighter, shorter, more service-friendly and give higher speeds and significantly better shaft dynamics.
We have specifically developed our SLH-x in size HSK-E20 to be used in our (U)ASD-H20 models and features tool clamp monitoring for a closed-loop automatic and fast tool change using a pneumatic piston pack inside the spindle.
As with all of our spindle models, this also includes an asymmetrical design to compensate for temperature changes as well as our well-proven thin-film liquid cooling. This not only gives superb temperature control, but it also isolates the rest of the machine from the heat sources inside the spindle.
In combination with self-compensating design, where the axial tool displacement caused by the centrifugal load is elimanted by the axial tool displacement caused by the temperature increase, the axial shaft growth from cold conditions and standstill to max. speed and warmed through stay below 1 micron. The spindle soak time from which there isn´t any axial shaft growth anymore is less than 3 minutes. Other air bearing spindles require up to 45 minutes to stabilize, and users of roller bearing spindle have to fight inconsistent axial shaft growths of more than 40 microns.
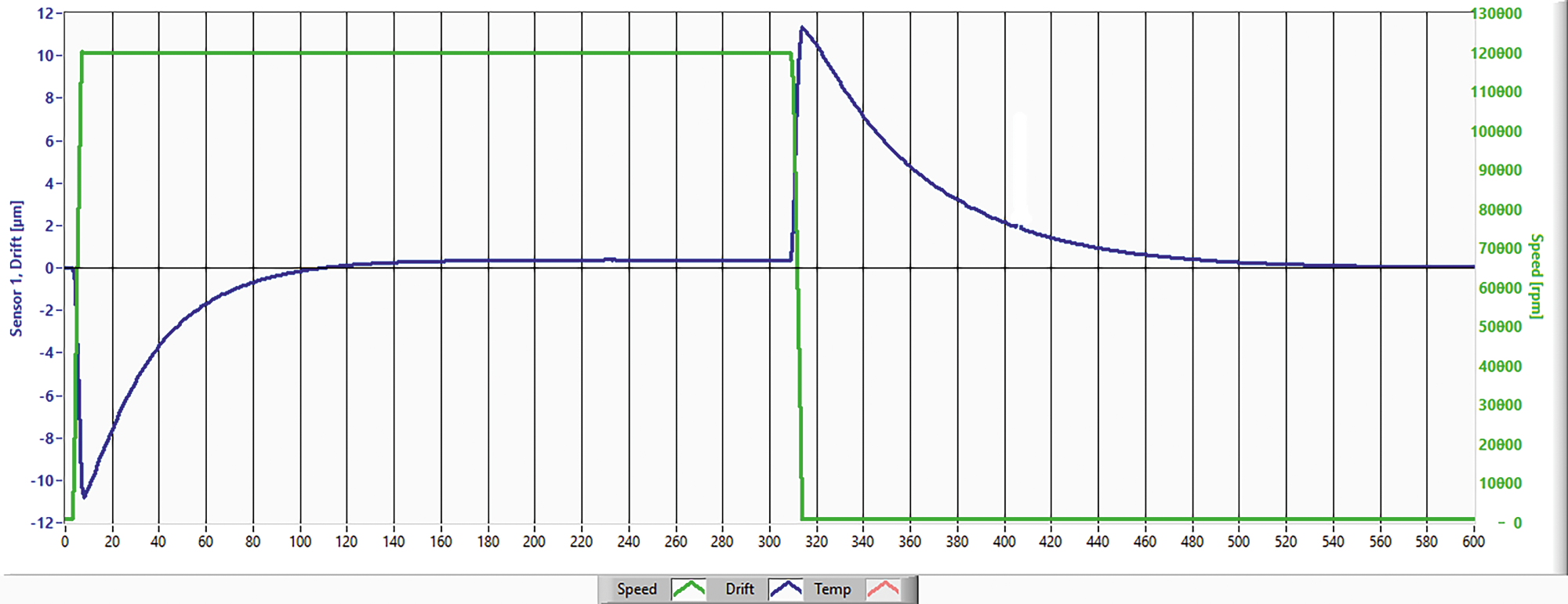
Figure 6. Axial shaft growth, from cold/ standstill to 120.000 rpm/ heated through
Image Credit: Levicron
Not only thermal stability and quick response the customer can expect. Our patented bearing technology gives way higher stiffness values than other gas bearing designs. In combination with a strict optimization for best shaft dynamics the customer can expect dynamic tool run-outs of under 1 micron and very low vibration levels. With no bearing or shaft critical frequencies within the speed ranger our UASD-H20A is even the perfect spindle for tool diameters less than 50 micron which like to just break when running through a resonance.
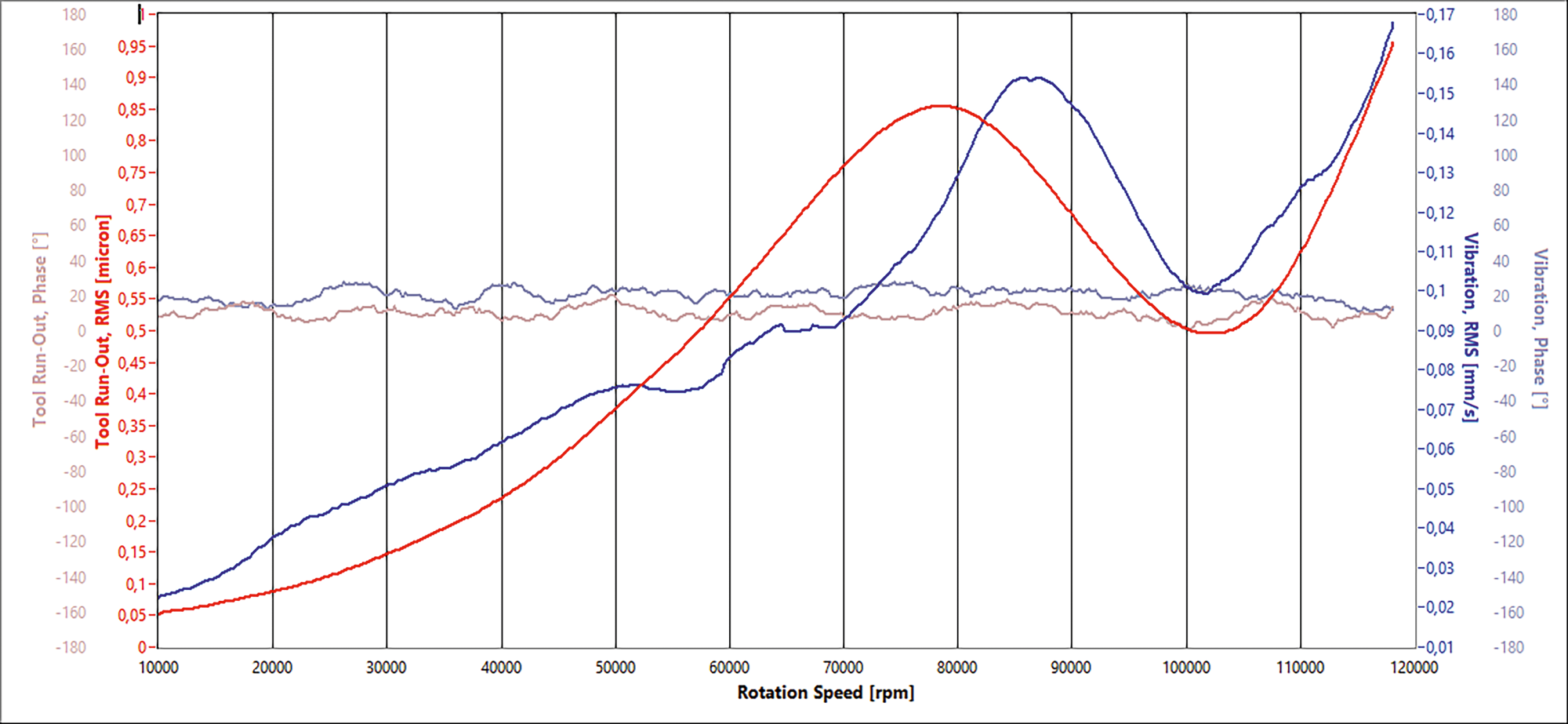
Figure 7. Dynamic tool run-out < 1 micron and spindle vibrations
Image Credit: Levicron
How far down the road are you with the development and when is the first spindle scheduled for test cuts in a customer machine?
With the dynamics tests being carried out, we are testing the SLH-20 clamping system in parallel. The biggest problem at the moment is the supply of components like connectors, connector pins or cables that are needed for the sensor and motor side.
We are close to bringing the spindle and the clamping side together for the final tests. Besides dynamics, endurance and performance testing, we have scheduled long-run tool change cycle tests as well as motor stress tests. As there are already machining trials scheduled, we have to finish the work for the pilot batch by August 2022.

Figure 8. ASD-H20A (front view) - ready for future semicon industries
Image Credit: Levicron
What other industries would benefit from this spindle?
There are quite a few industries that will benefit from this spindle. The closest to Semicon industries is the optoelectronics sector. With optical data transmission now replacing copper-based solutions, the requirements for shape control and surface finish have become very demanding. This includes, for example, connectors or optical couplers.
The Swiss watch industry on the other side is more interested in a smaller Levicron solution and has been inquiring about such a spindle for years. Now we may have an answer to what they are asking.
Other industries and parts to be machined that will benefit from a faster precision spindle with an automated HSK-E20 interface include:
- Precision Molds
- Optical Molds
- Micro Fluidics
- Dies for coinage
- Watch industries
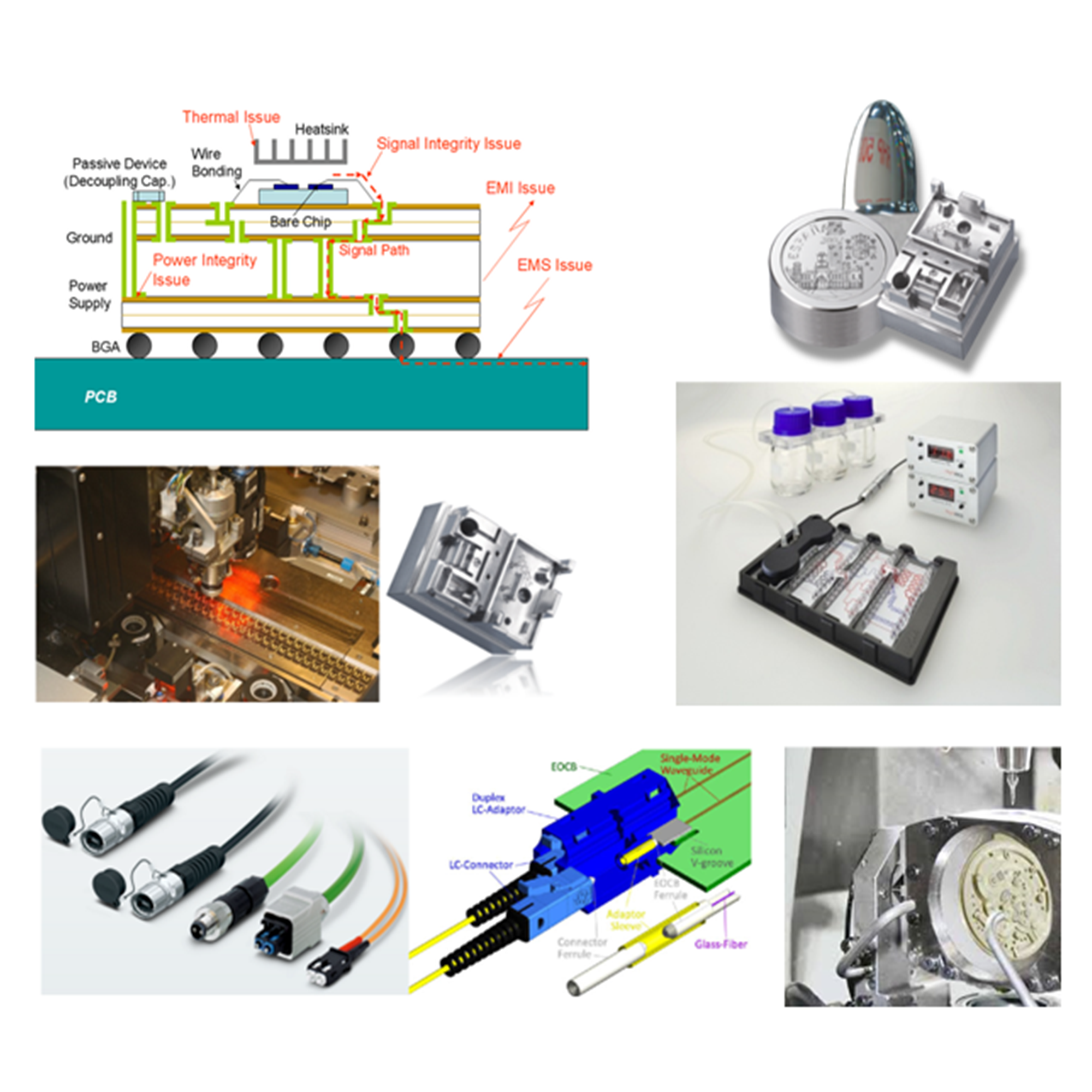
Figure 9. Industries profiting from the new spindle solution
Image Credit: Levicron
What other solutions are being developed at Levciron?
Levicron is working on quite a few new developments. For example, we are developing a precision high-speed spindle with an ultrasonic vibration system. To machine brittle materials like ceramics or tungsten carbide, ultra-sonic vibrations at the tooltip often provide a significantly extended tool life compared to conventional machining.
Solutions already on the market can be used in combination with ultra-sonic oscillators in the tool holder. This not only makes the tool holder very heavy and impacts spindle dynamics, but it also requires significant investments for these tool holders. However, Levicron has found a solution where we can bring the ultra-sonic transducer inside the spindle shaft which not only allows higher speeds at better spindle dynamics, but it also enables the user to use standard HSK (HSK-E32) tool holders rather than heavy cost-intensive ones with an integrated transducer system. We hope to get this product on the market by Q3/2023.
Our successful work-holding spindle ASD-Px is being used more and more for grinding. Although it is already available with a manual HSK-C63 tool interface. We have decided to create a heavy-duty version of it that includes our high-pressure aerostatic bearing technology, a stronger motor and an automatic HSK63 tool clamping system for which we have developed our SLH-x in size HSK-E63. Grinding will not be the only application. It could also be implemented for ultra-precision drum turning. Where very expensive and heavy oil-hydrostatic motor spindles are currently used, our ASD-H63 will be a cost-effective alternative for smaller drum-roll lathes.
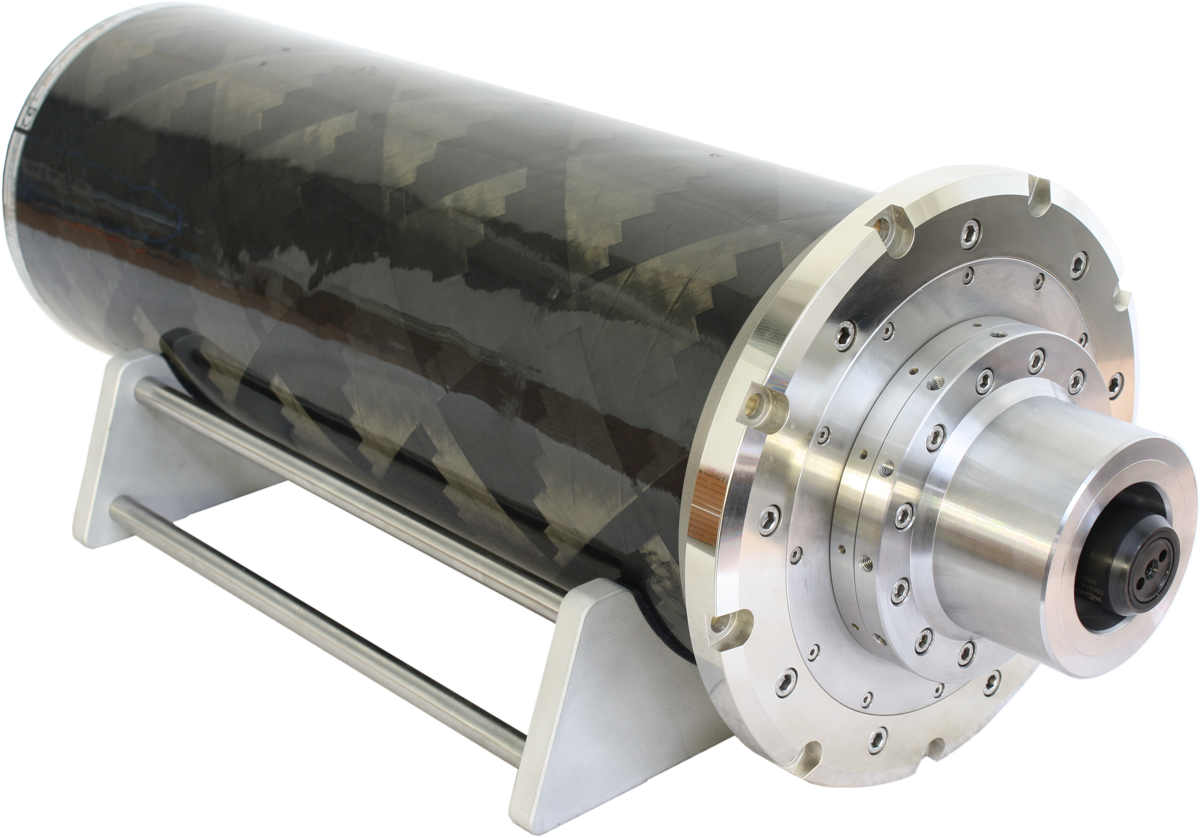
Figure 10. In development - UASD-H63, Ultra-Precision heavy grinding spindle
Image Credit: Levicron
As mentioned, our integral and spring-less HSK clamping system SLH-x is widely used not only for our spindle products. Although currently available for HSK sizes 25, 32 and 40, we are close to finishing our work for sizes 20 and 63 and we are going to have size 50 soon.
Internally we have also made enormous progress with our ShakesBear Analyzers. What began as a collection of our internal spindle test software pieces has now grown into a full spindle and machine dynamics analyzing suite, covering spindle error analysis, dynamic run-out, and resonance maps or FFT tools. We have managed to fully automate our spindle testing where the software also controls the spindle drive and is able to obtain values like phase current, voltage, power losses, or temperatures to generate fully automated reports. The raw data can then be stored in a database. Combined with the right hardware we offer these systems to other spindle manufacturers and machine builders with all the experiences we made being a spindle manufacturer ourselves.
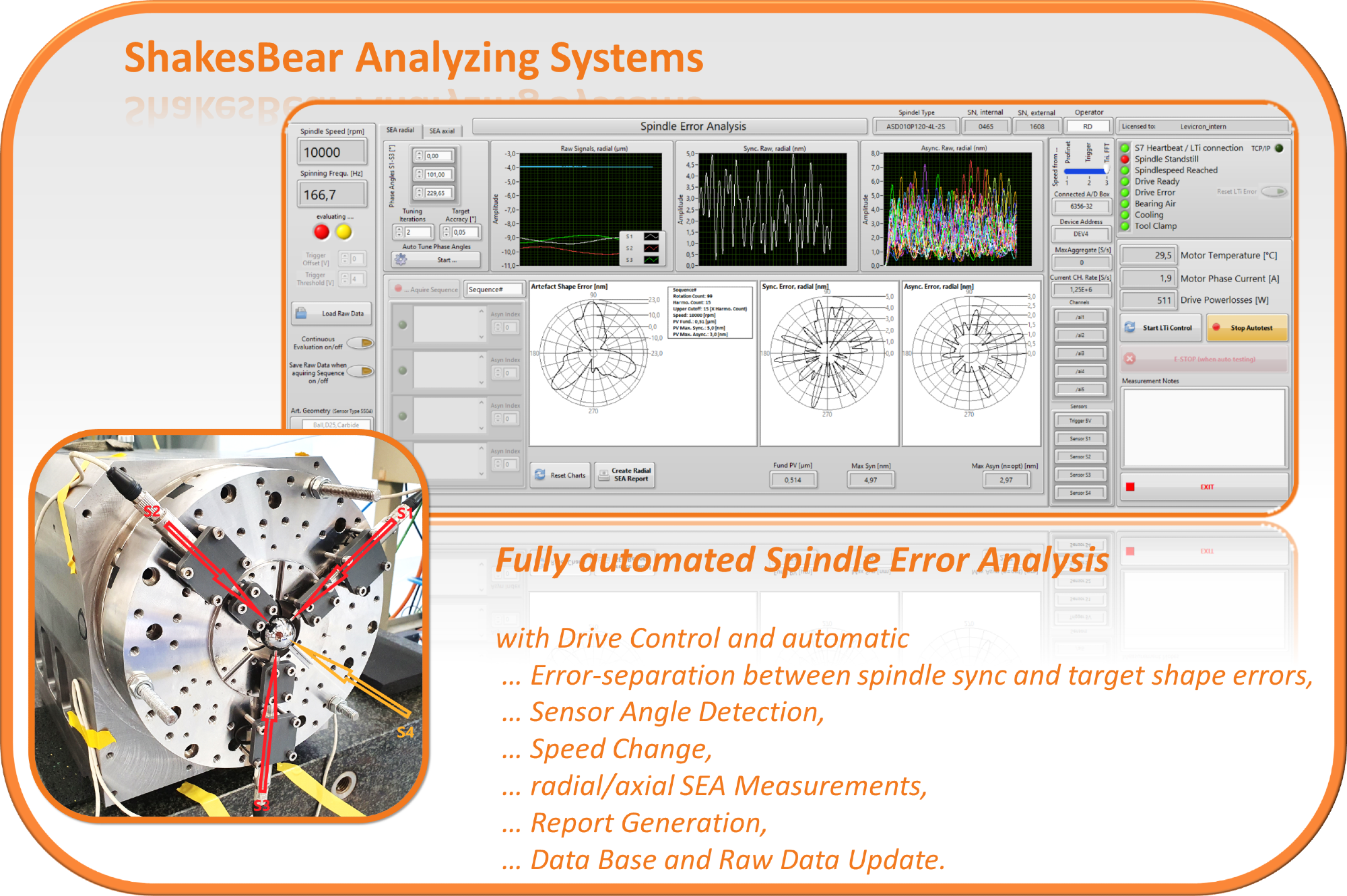
Figure 11. ShakesBear System - fully automated spindle error and dynamics analysis
Image Credit: Levicron
About Dr. Ralf Dupont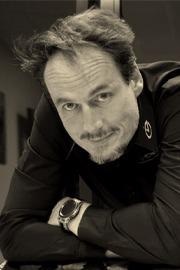
For more than two decades, Ralf has been driven by non-contact bearing systems like air bearings as well as precision engineering and machining. Coming from a high-speed drilling spindles and centrifugal compressors background, he founded Levicron back in 2010 and yielded to his temptation of precision machining and high-speed spindle systems. Ralf holds a degree in industrial engineering from TU Kaiserslautern. He previously worked for Air Bearings Ltd, MAN Turbo AG, Fischer-Precise AG and the University of Kaiserslautern.

This information has been sourced, reviewed and adapted from materials provided by Levicron GmbH.
For more information on this source, please visit Levicron GmbH.
Disclaimer: The views expressed here are those of the interviewee and do not necessarily represent the views of AZoM.com Limited (T/A) AZoNetwork, the owner and operator of this website. This disclaimer forms part of the Terms and Conditions of use of this website.