AZoM speaks to Dr. Ralf Dupont, president of Levicron, about HSK clamping as the new industry standard for automated tool clamping CNC machines.
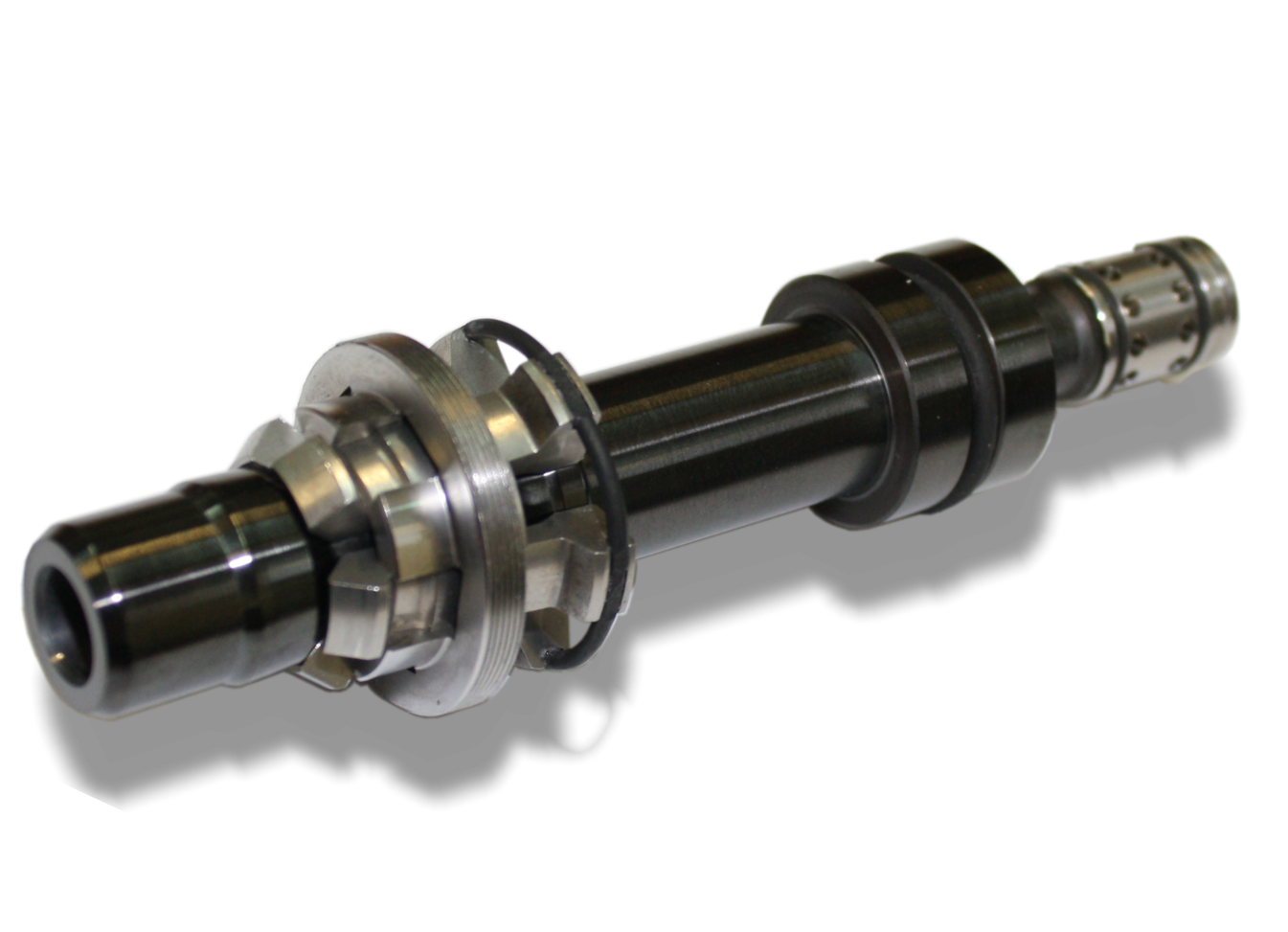
Could you please describe Levicron as a company and their spindle solutions for CNC and Ultra-Precision Machining?
Levicron specializes in developing and offering CNC machining spindle solutions with ultra-precision properties. This not only allows CNC machining to create parts and molds with optical qualities fully automated, but also enables Ultra-Precision machining solutions to add automation to their machine features. To achieve this, many unique solutions have been developed leading to the formation of independent products. This also applies to our spring-less HSK tool clamping units SLH-x.
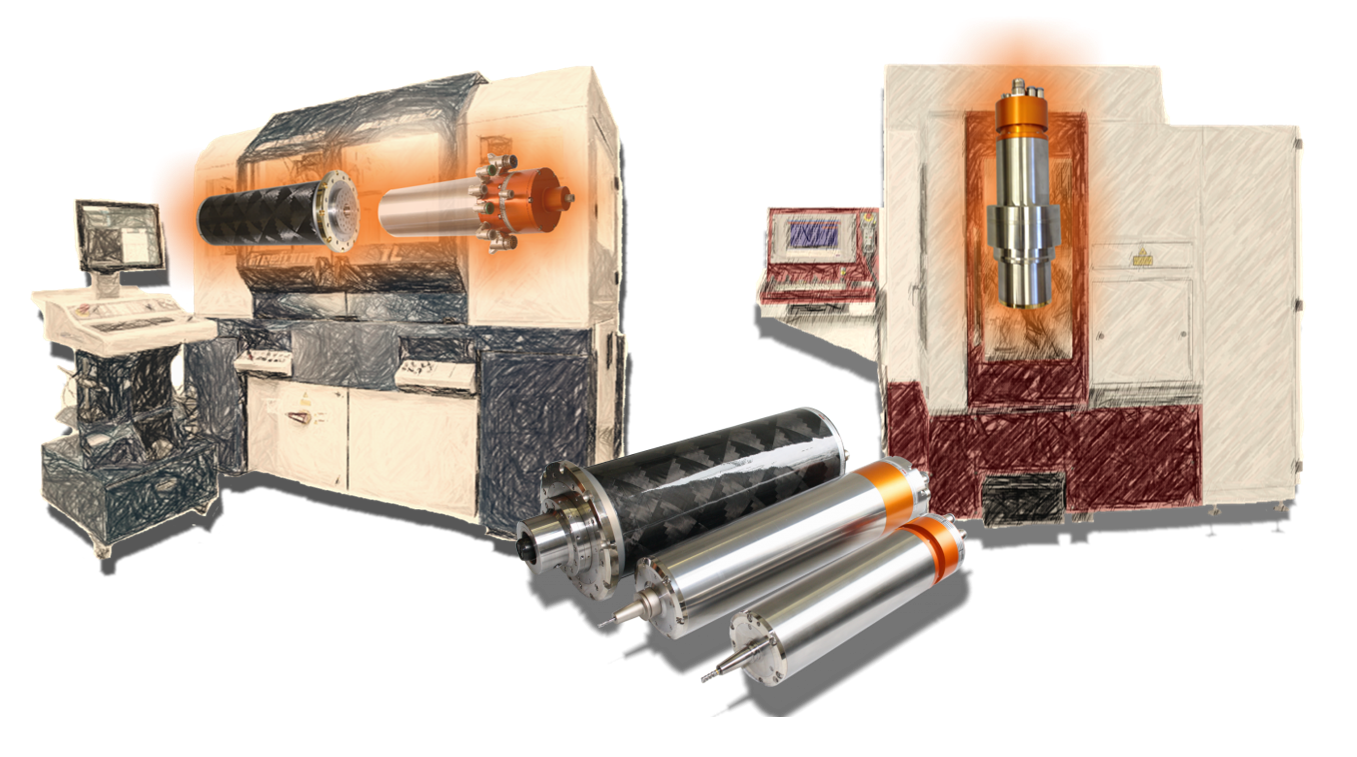
Figure 1: Levicron - Ultra-Precision meets CNC Performance
Could you please explain what HSK (Hollow Shaft Taper) is and why it has become an international standard tool interface for CNC machining?
The HSK clamping, according to DIN 69893, is the successor of the SK clamping system which had been an international industry standard for automated tool clamping in CNC machines. The tool itself is clamped into a tool holder that gets automatically loaded into the spindle during the machining process. It is pre-set and installed into a chain or disc loader in the machine, which allows the machine to provide hundreds of tools for machining by just recalling the tool in the G-code programming.
Compared to the SK system, the HSK system is significantly lighter, and, because of the additional axial face connection, even stiffer. The actual innovation is a different one, though. Although the form of the inner taper of the spindle and the outer taper of the tool holder need to be machined very accurately, form-wise the actual diameter is of less importance. The outer taper of the tool holders is slightly larger in diameter and, as such, is deformed whilst it is pulled into the spindle taper. This allows for manageable tolerances and economical production of such tool holders. While the SK system is pulled into the spindle taper using a simple draw pin at the top of the tool holder, the HSK system requires a split collet that is operated by an internal draw pin. The internal draw pin drives the split collet outside or inside and clamps or releases the tool holder through its internal recess profile.
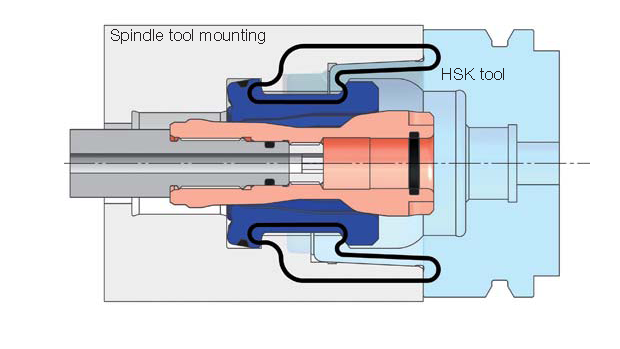
Figure 2: HSK clamping, DIN 69893; Source: https://roehm.biz
Why is it that the clamping repeatability is superior to, let’s say, collet systems?
As explained, the tool holder taper is slightly larger than the spindle taper and deforms in the range of a few microns when pulled into the spindle shaft. Like a press-fit, this gives an excellent radial alignment. As the HSK interface also features an axial face connection between the spindle shaft and the tool holder also the axial position is perfectly controlled and repeatable. Spindles from Levicron that feature an HSK interface offer a tool change repeatability of under 0.2 microns in both radial and axial directions. Precision collet systems work with split collets that grip the tool directly. The controlled manufacture of precise split collets is very difficult, and once split the collet can’t be inspected anymore. Here burrs and releasing material stresses during the split process is a total unknown. As collet systems don’t feature an axial face connection like the HSK interface the axial repeatability is not given and each tool needs to be set after being loaded into the spindle.
How do current HSK clamping units manage the clamping inside the spindle?
As clever as the HSK system might be, delivering the force and travel to the interface still is its weakest point and affects the spindle performance, accuracy and serviceability. For current solutions, the pull-in force is delivered permanently using spring systems. While a moderate pull-in load is required, the movement necessary to eject and clamp a tool is long and requires very long spring systems. Roehrs springs or hundreds of disc springs are necessary, and while these springs need to sit tight inside the spindle shaft they still need some clearance to the shaft bore to work. Each tool change causes the springs to displace slightly and together with the spring system length this leads to the heavy shaft as well as worse and changing rotor dynamics. Disc spring failures, changing clamping travels and very complex assembly procedures are resulting downsides. On top of this, to unclamp a tool the ejecting force needs to overcome the preload of the disc springs first before the drawbar starts to move. This makes a retaining system necessary to protect the bearing system to be damaged.
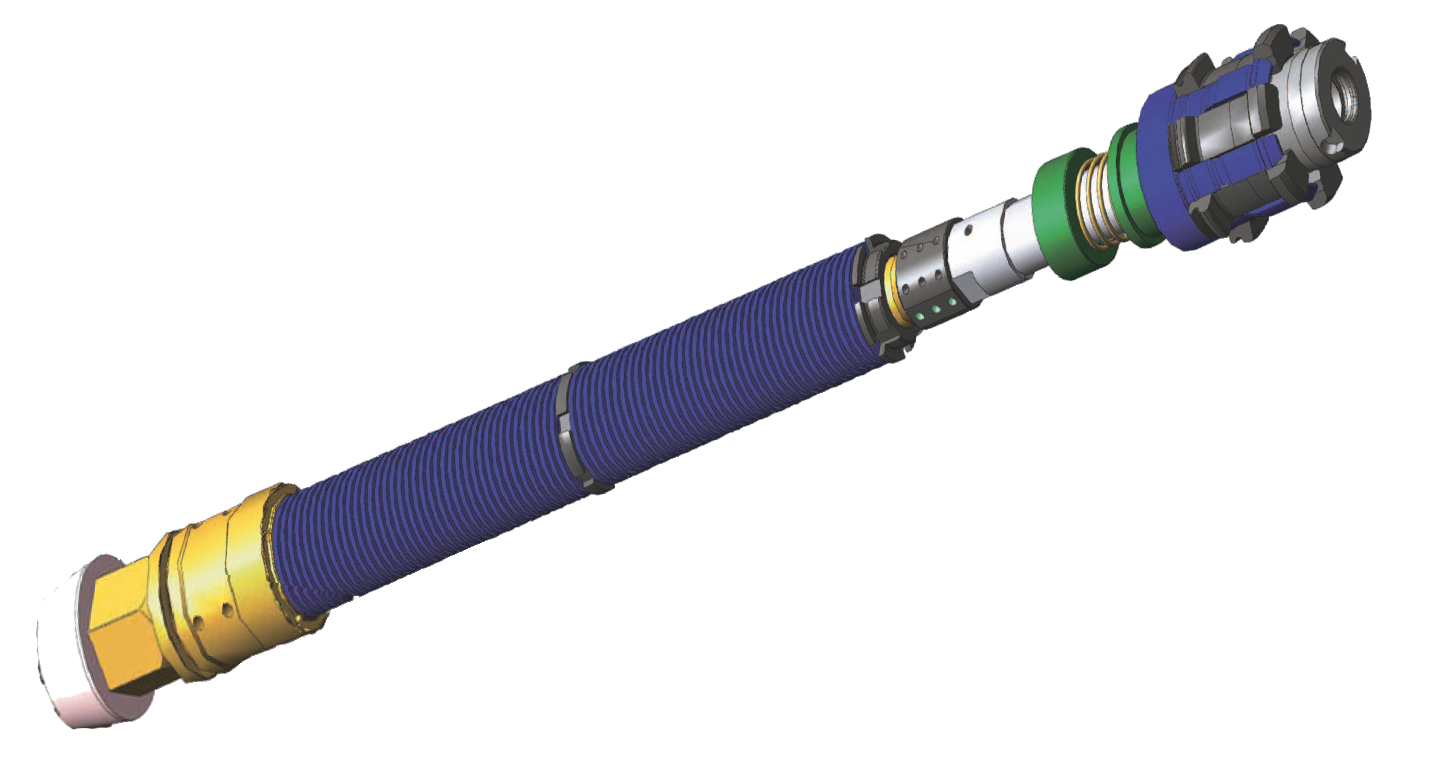
Figure 3: Current state of the art spring-based HSK clamping units; source: https://roehm.biz
Why is it that Levicron had to come up with their SLH clamping units and a new solution?
Facing the necessity of a long and inconsistent spring system inside the shaft to accommodate current HSK clamping systems in their spindle solutions made it clear in the first place that a different solution for both high-speed and ultra-precision spindle solutions has to be developed.
How did you overcome the issues with current solutions and what are the benefits for the OEM and end customer?
Self-locking is the key. There have been attempts to replace the spring system after the actual HSK interface with a self-locking unit. On top of the taper connections inside the HSK interface, these systems added further taper connections with very small angles. Because of so many taper connections with very shallow angles they were very hard to adjust and not consistent with respect to clamping travel and force. Back in 2017, and throughout the course of a new spindle development, Levicron had the idea to make the HSK interface itself self-locking while maintaining the DIN 69893 standard. Instead of two serial systems – the interface plus a spring or locking unit – the self-locking HSK interface leads to only 30% weight and length compared to conventional spring-based systems. The drawbar doesn’t have to rotate with the shaft, and because there is no axial spring load the ejecting force is reduced by 60% so that no retaining system is necessary to protect the bearings from getting overloaded.
Figure 4: non-rotating drawbar and clamp/unclamp forces (HSK40)
Three months after this idea, our first SLH-x system went into a cycle test with 2 million tool changes. The results were spectacular. On top of a significant improvement of the shaft dynamics, consistency, serviceability, and reliability over the spindle life cycle were improved by a great deal. Ever since Levicron has not only replaced the HSK clamping units in all of their spindle solutions with HSK clamping but has changed all HSK clamping in their production with their SLH-x.
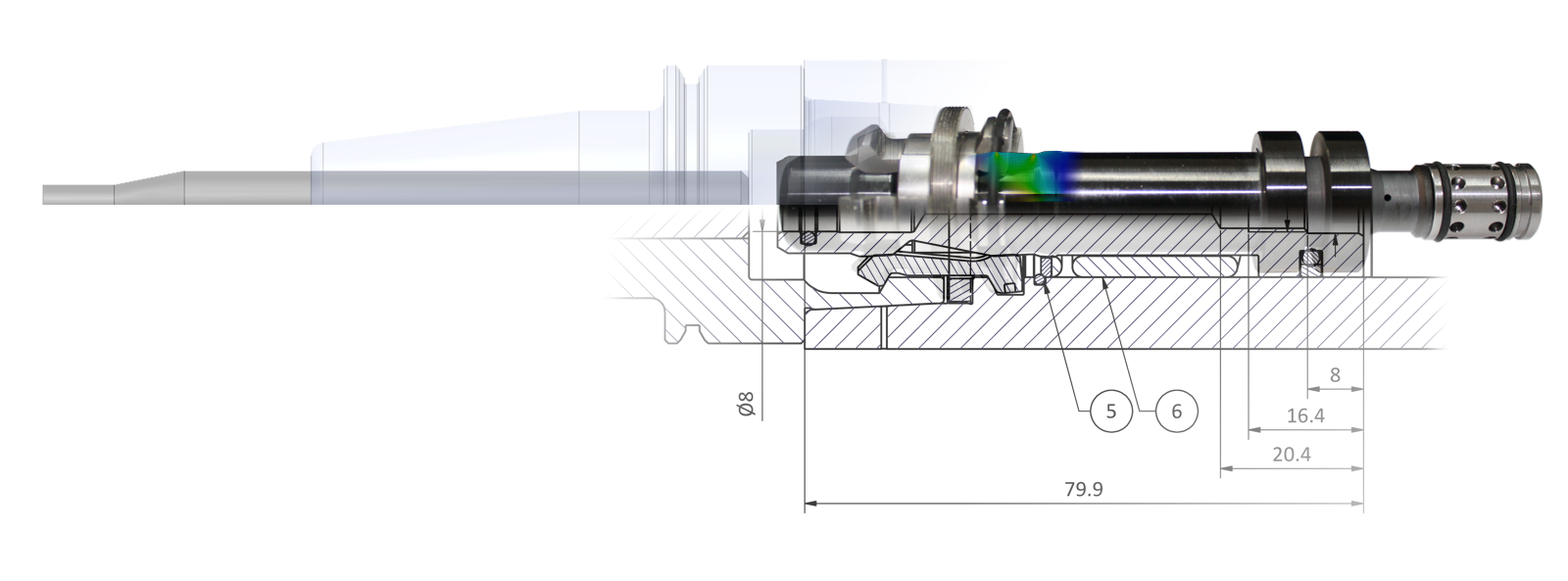
Figure 5: Levicron’s SLH-x – self-locking HSK interface shaft and axis units
The benefits for the OEM are straightforward. It gets a consistent, repeatable, and robust HSK clamping as well as superior shaft dynamics, and much better serviceability. By using hard material sliding coatings our SLH-x is maintenance-free over its lifetime.
The end-customer on the other side benefits from a more consistent part quality and because of the better shaft dynamics even from a better surface finish and longer tool life.
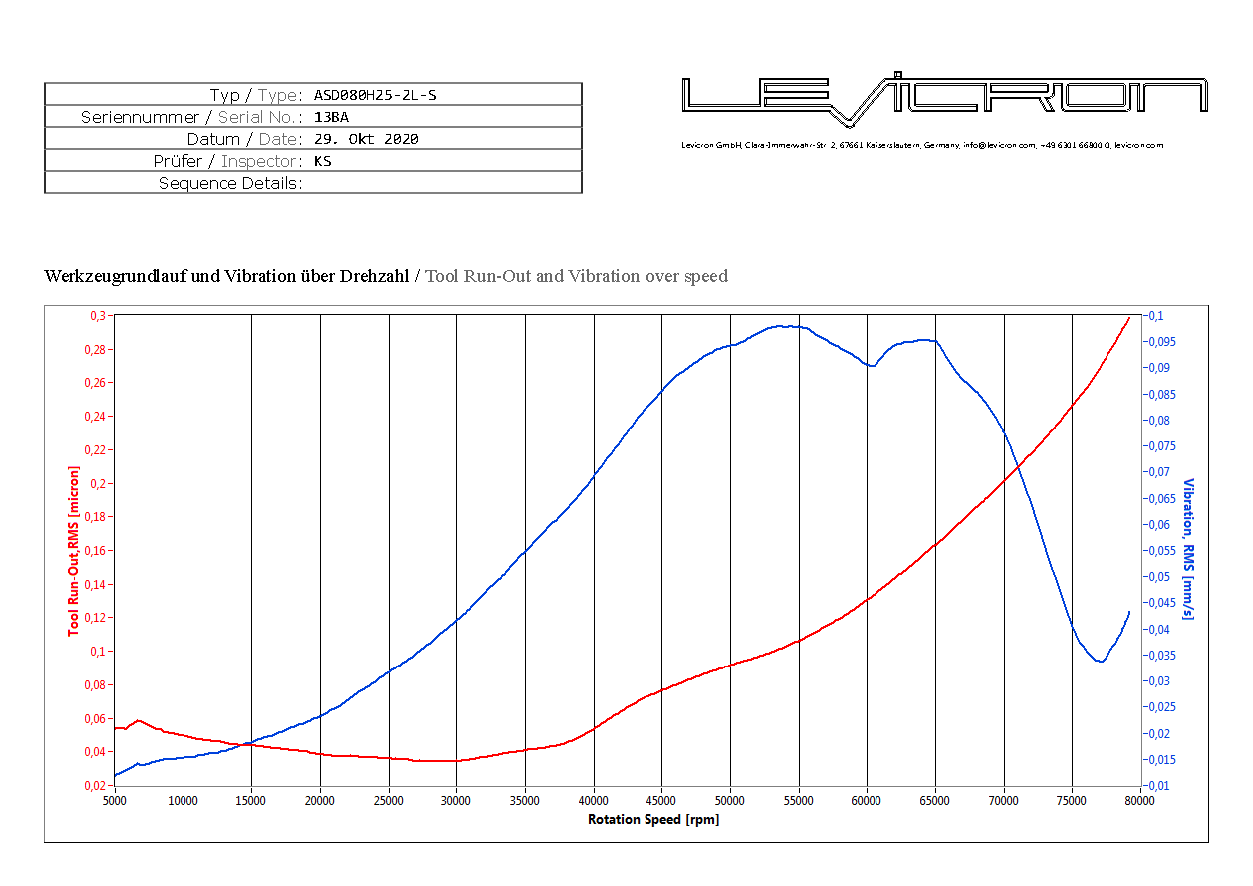
Figure 6: Dynamic tool run-out and vibrations with speed for Levicron’s ASD-H25/A with SLH25.
If the self-locking solution is that obvious and simple, how have you protected your idea, and what is the opinion of the market so far?
After realizing how simple, reliable, and consistent an HSK clamping system inside a shaft or axis can be using the self-locking HSK interface idea I applied for national and international patents. The European patent is granted, the international side for China, USA, Japan a.o. are pending.
On the market, I could see an incorrect belief that at higher speeds the split collet is pushed into the holder’s recess and thus increases the pull-in force on the tool holder, but also decreases the preload of the self-locking. In fact, the opposite is the case because the split collet bends in the middle and thus even increases the pre-load of the self-locking slightly. This has been verified in simulations and many forms of dynamic testing.
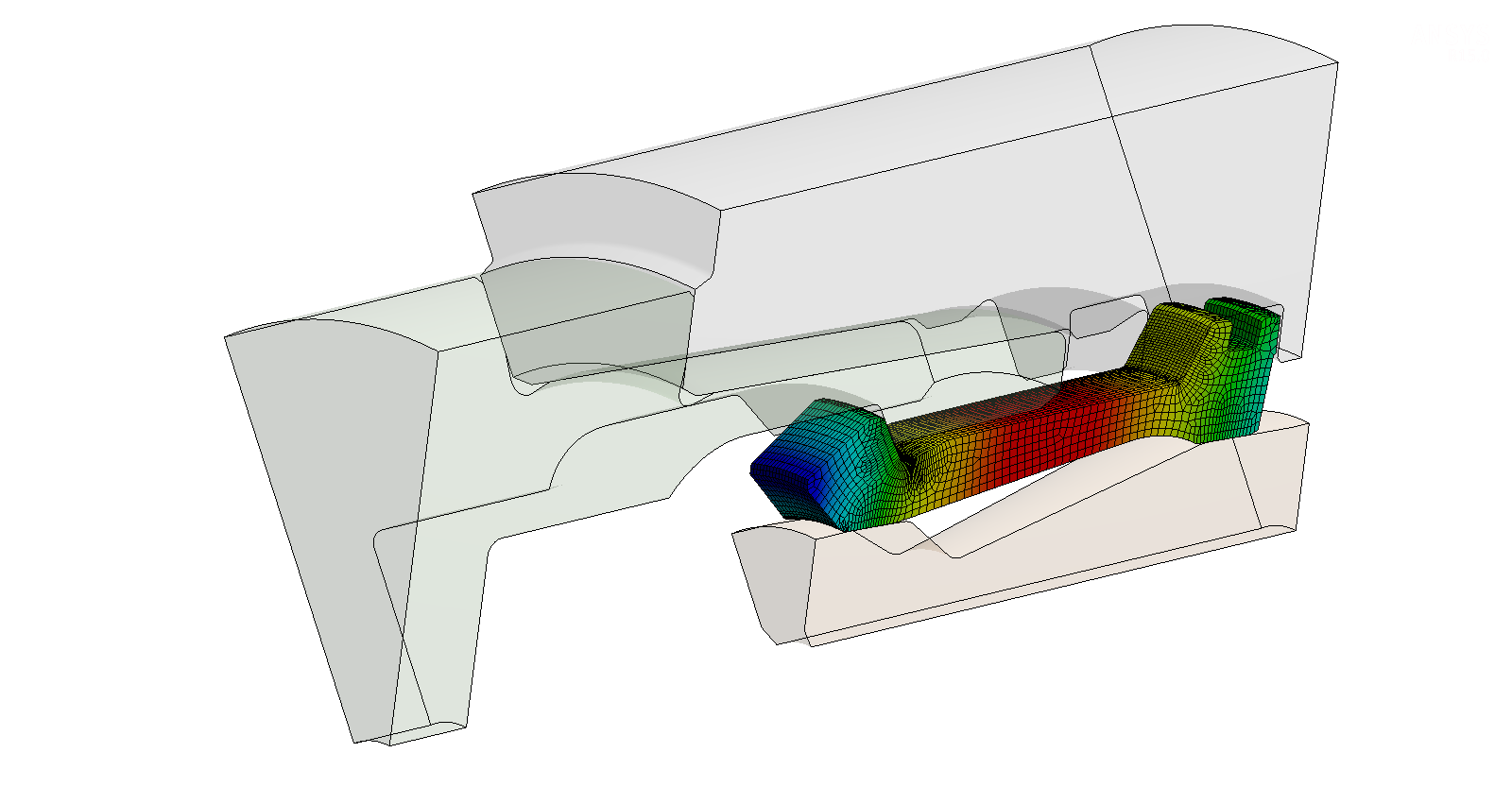
Figure 7: Simulation results to prove the pre-load at higher spindle speeds and side loads
Well, as well as the spindle side there is also the tool holder side. Did you address this matter to offer ultra-precision spindle solutions for CNC Machining?
This even came before the SLH-x clamping units. Driven by customers on the ultra-precision machining side, we had to address tool run-out, tool clamp repeatability, and balance the quality of HSK tool holders in combination with our ultra-precision motor spindles. While with standard tool holders the real and averaged balance quality was up to four times higher than the stated tool run-out of 3 microns. Anything higher was not acceptable for ultra-precision machining. Using our expertise in manufacturing spindle shafts, we were able to create our UTS-x HSK holder series that not only offers a twenty times better balance quality than the stated industry-standard in DIN 69893, but also a three times smaller tool run-out. In combination with our UTS-x HSK tool holder series, we guarantee a tool run-out of under 0.8 microns, a tool clamp repeatability of fewer than 0.2 microns, and thus true ultra-precision spindle solutions with HSK tool clamping.
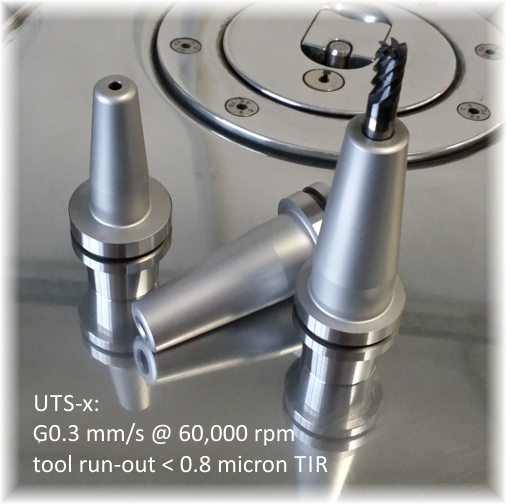
Figure 8: UTS-x – ultra-precision HSK tool holders
How could the current and future Ultra-Precision Machining solutions benefit from HSK clamping?
For me, the next and, in my opinion, necessary step for ultra-precision machining solutions is clear. The world that is heading towards fully automated machining can’t just leave out this industry. Automated tool and work-piece change using tool loaders and robotics as well as fully automated on-machine measurement and machine corrections are likely to be the steps necessary to justify their future existence.
Will Levicron now become a supplier for clamping devices?
Yes and no. Our core competencies are developing, manufacturing, and selling ultra-precision spindle solutions for CNC machining. However, to achieve our goals, we had to come up with many new solutions because such had not been commercially available. Although this means hard work, it also allowed us to produce new products from these solutions. This also applies to our HSK clamping units SLH-x and ultra-precision tool holder series UTS-x. In fact, our HSK tool clamping units SLH-x work that well that I see a very broad use of them in the future and I have decided to make them available to the market. Here future customers can rely on the fact that is in the developers' and manufacturers' best interest for the SLH-x system to work flawlessly. However, to concentrate on our core business, we are looking for a strong partner in the business of tools and tool clamping we can cooperate with. Until then we sell directly to customers.
What HSK sizes are and will be covered in the future?
With our SLH-x HSK clamping units, we now cover HSK25, HSK32, and HSK40. Sizes HSK20 and HSK63 are being developed.
Our UTS-x tool holder series also covers HSK25, HSK32 and HSK40. Please ask us for the right tool shank size and holder length.
How can other companies contact you to switch to your SLH clamping units?
Just get in touch through our official e-mail address. If you could please give us an outline of your application we can also come up with recommendations for the best solution for you. Any other information you can find on our website. Should you be more of a phone person, like me, just contact me on our company phone number.
About Dr. Ralf Dupont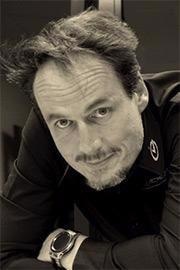
For more than two decades, Ralf has been driven by non-contact bearing systems like air bearings as well as precision engineering and machining.
Coming from a high-speed drilling spindles and centrifugal compressors background, Ralf founded Levicron back in 2010 and yielded to his temptation of precision machining and high-speed spindle systems. Ralf holds a degree in industrial engineering from TU Kaiserslautern. Ralf previously worked for Air Bearings Ltd, MAN Turbo AG, Fischer-Precise AG and the University of Kaiserslautern.
Disclaimer: The views expressed here are those of the interviewee and do not necessarily represent the views of AZoM.com Limited (T/A) AZoNetwork, the owner and operator of this website. This disclaimer forms part of the Terms and Conditions of use of this website.