AZoM speaks with Joseph Toombs, a Ph.D. student at the University of California, Berkeley, about his research that has developed a new 3D printing process for the manufacture of small glass objects.
Please can you introduce yourself, your background, and how you began researching 3d printing manufacturing processes?
I joined the Design for Emerging and Nanoscale Manufacturing lab in 2018 after graduating from the University of Illinois, Urbana-Champaign. Advised by Professor Hayden Taylor in the Mechanical Engineering department at the University of California, Berkeley, I began researching volumetric additive manufacturing after learning about the new technique of computed axial lithography, which had just been developed in the lab the year before I joined.
Why is it necessary to 3D print glass objects? What kinds of applications are these objects used for?
The pressure to shrink devices in the consumer electronics industry and the emergence of remote optical fiber sensing technologies places demanding size constraints on integrated optical systems. New microscale additive manufacturing technologies like two-photon polymerization and micro-CAL have demonstrated capabilities to directly manufacture these systems without requiring assembly.
Additionally, glass has excellent chemical and heat resistance which makes it an attractive material for microfluidic applications. 3D printing of glass microfluidic chips can make possible new flow-through chemical synthesis and encapsulation techniques with harsh solvents and acids.
Your research has expanded on a process called Computed Axial Lithography (CAL). Please could you describe this system?
Computed axial lithography is a 3D printing process that forms objects all at once by tomographic superposition of light projections. This tomographic volumetric additive manufacturing (VAM) technique, which draws inspiration from x-ray computed tomography, works by projecting a series of digital light patterns from different angles that photopolymerizes photosensitive resin. This differs from other light-based AM methods which solidify objects layer-by-layer.
How does your new system, ‘Micro-CAL’, differ?
The micro-CAL system differs from the larger-scale systems in two main ways - first, the light source, a laser, and second, the digital light pattern created by the DMD is demagnified or scaled down in size rather than scaled up in size as in the larger tomographic VAM systems. The combination of these two differences enabled us to achieve greater optical resolution over a long depth of focus (albeit within a smaller field of view than the larger systems).
What role do light and lasers play in the 3D printing of glass objects using this method?
The computed tomographic light patterns are sequentially projected through the rotating container of nanocomposite and the accumulation of the absorbed light dose photopolymerizes an arbitrary 3D geometry all at once.
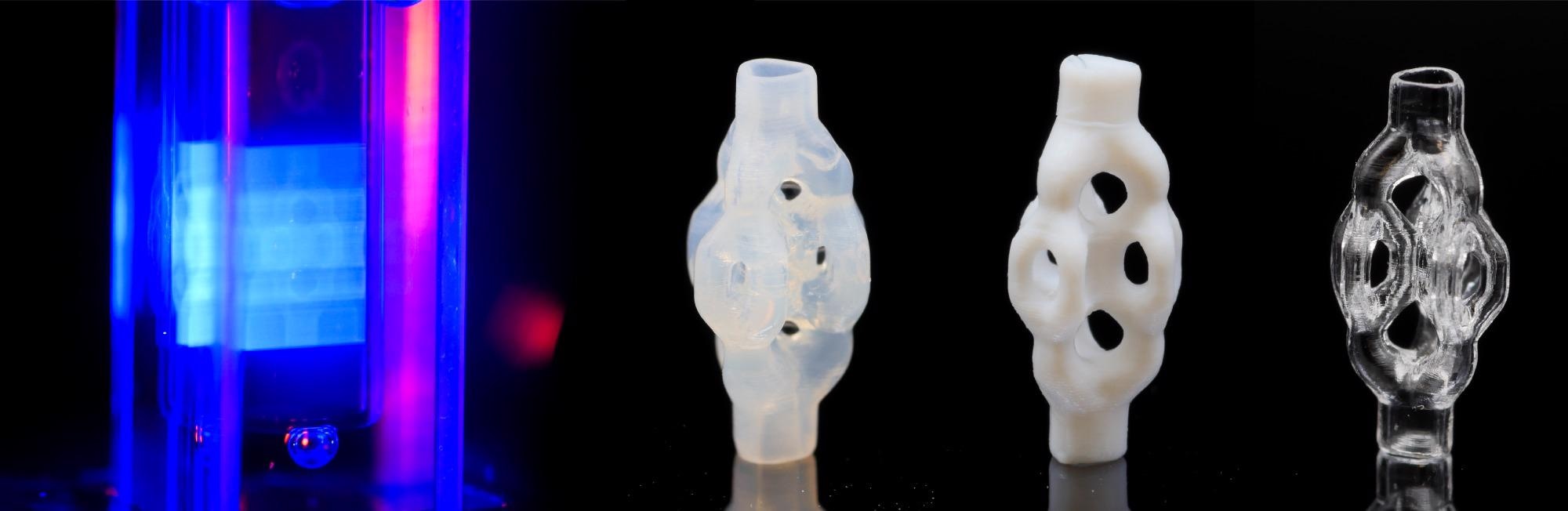
What are the advantages of using the CAL process over other 3D printing technologies?
Because the object is printed simultaneously, the roughness typically observed in layer-by-layer 3D printing processes is largely avoided. This advantage gives objects reduced roughness which improves optical quality and yield strength consistency as we describe in the article.
You have collaborated with other researchers to produce a new Glassomer material used in the 3D printing process. Could you describe the properties of this material and why it is used?
The Glassomer material is an organic-inorganic nanocomposite–a colloid of silica glass nanoparticles dispersed in a liquid monomer precursor. The liquid monomer component of the nanocomposite material can be photopolymerized and the resultant polymer network serves to bind together the silica nanoparticles. After the 3D printing process, the nanocomposite material can be thermally treated to produce a fully dense silica construct with optical properties nearly identical to commercially available silica.
How scalable is this process? Can we use this on an industrial scale to manufacture glass objects?
At present, the micro-CAL system has a somewhat small build volume and may limit the technique’s appeal to industry users. However, the Glassomer nanocomposite approach to glass manufacturing is very scalable, in fact, Glassomer has recently introduced a new formulation compatible with injection molding.
Are there any limitations in regard to the process or properties of this material that you are working to overcome?
The maximum cross-sectional thickness of a 3D printed component with this material is limited due to the thermal treatment and debinding process. The burnout of the binder material necessitates a pathway through which the gaseous phase may pass. Currently, the maximum cross-sectional thickness is a little less than 1 mm, although other Glassomer formulations have been tuned to relax this constraint.
What effect do you foresee this technology having on manufacturing industries in the future?
Micro-CAL printing of Glassomer provides a new way to produce rapidly challenging glass geometries or geometries with a high degree of customization. The technology expands the possibilities of glass, one of the most widely used materials in history.
What is personally the most exciting aspect of this new research for you?
The advancements we made in scaling down the minimum printable feature size with CAL bring new applications in the fields of microfluidics, filtration and membrane science, and mechanical metamaterials into reach.
What are the next steps for your research? Do you hope to conduct further research on 3D printing manufacturing processes?
In our lab, we are developing new VAM techniques and optimization algorithms for generating digital light patterns for VAM. Specifically, we are researching how we can enlarge the extent to which we can print microscale features. We want to answer the question: how can we print geometries with the same microscale features that we demonstrated in the article but within a much larger envelope or build volume? If we can design a system with this capability, it will be more appealing for industrial applications like next-generation filtration and membranes.
About Joseph Toombs
Joseph Toombs is a 4th year Ph.D. student. His research spans microscale additive manufacturing technologies and design optical and mechanical systems. He also researches and characterizes new photopolymer chemistries and develops optical metrology techniques for VAM
Highlights:
Disclaimer: The views expressed here are those of the interviewee and do not necessarily represent the views of AZoM.com Limited (T/A) AZoNetwork, the owner and operator of this website. This disclaimer forms part of the Terms and Conditions of use of this website.