Sponsored by QATMReviewed by Emily MageeJul 28 2022
For decades, cold mounting has been a vital part of the preparation of solid samples. When preparing small sample pieces or assemblies, mounting of the sample material is required. Chemically crosslinking polymer systems are used, particularly for pressure- and temperature-sensitive samples.
KEM 50 UV and the associated Qmount light-curing device are used as the basis for an innovative and throughput-oriented method of cold mounting.

Image Credit: QATM
High temperatures or pressures during mounting can cause systematic artifact formation, particularly in the investigation of minerals, functional ceramics or polymer materials, and in the field of metallic heat treatment.
For some applications, specimens are not encapsulated using a hot mounting press. Frequently, multicomponent mounting materials based on polymerizing acrylates are used to mount standard specimens. A precise mixing ratio of the components must be maintained to ensure consistent specimen quality.
During the polymerization process, reaction diluents and other organic mounting components are emitted. This renders it absolutely necessary to use laboratory fume hoods. 10-20 minutes is the approximate curing time for transparent curing acrylic systems, which are also suitable for target preparation.
A time-saving and user-friendly alternative is offered by UV-initiated acrylic systems. As one of the first companies to offer a complete solution in the field of light-curing mounting materials, QATM has designed the Qmount UV mounting device with its high-quality, long-life components for laboratory applications.
Thanks to LEDs with a narrow-tolerance emission spectrum (max. =365 nm), and the connection of an exhaust system with an activated carbon filter the Qmount is suitable for manufacturing environments.
Figure 1 shows that the heat input due to the power dissipation of the light sources has also been minimized. Curing times of 60 seconds are guaranteed by the optimized LEDs when using the KEM 50 UV mounting medium.
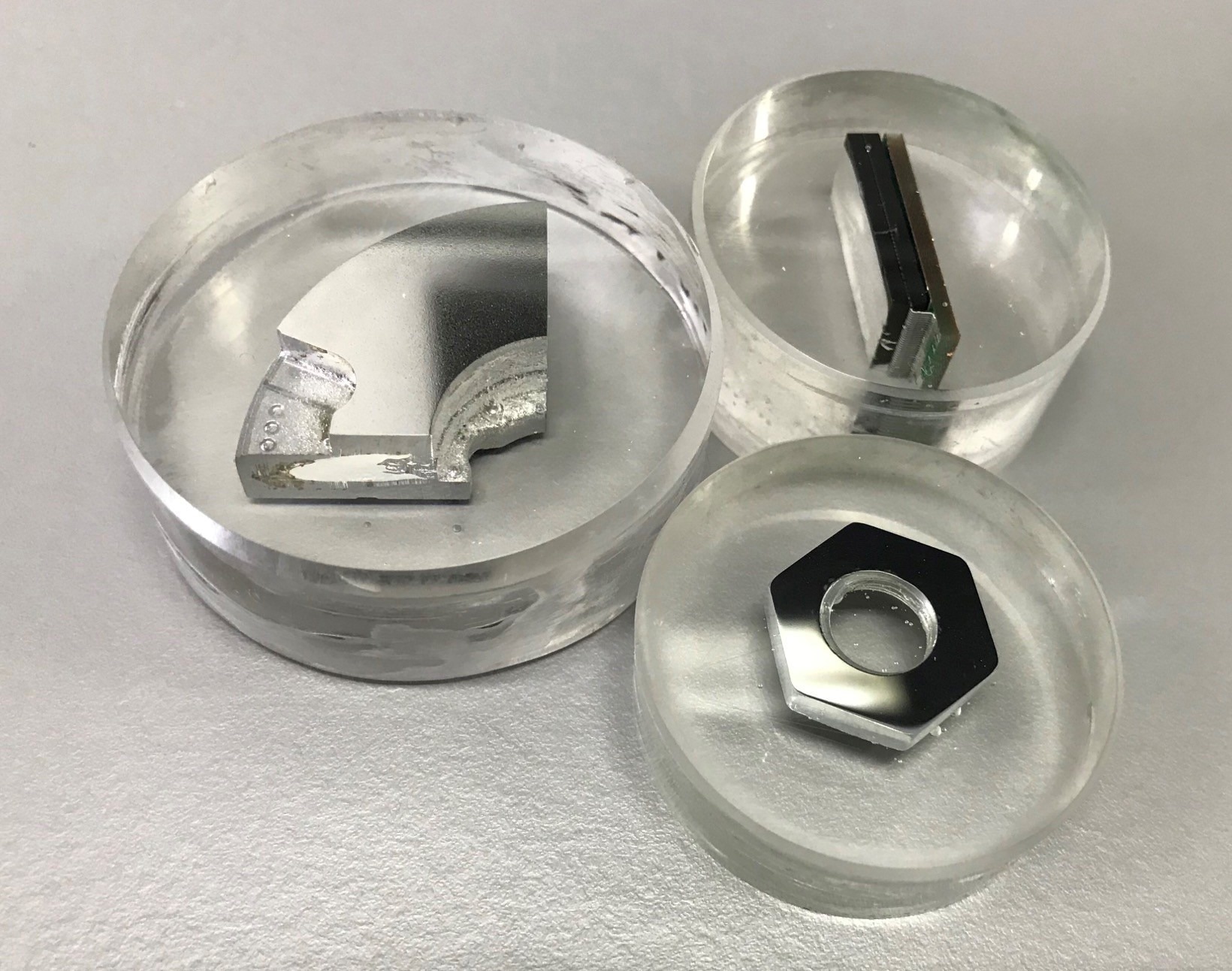
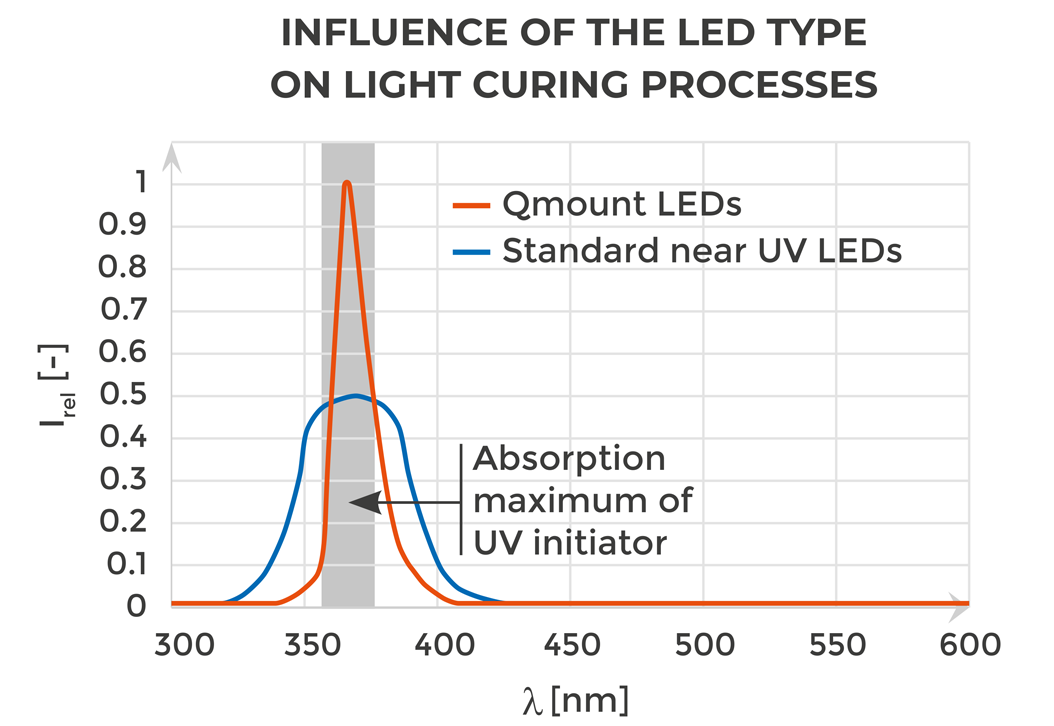
Figure 1. Samples mounted with Qmount (Top) and schematic of emission spectra of UV LEDs (Bottom). Image Credit: QATM
During the curing process of the agent, KEM 50 UV has a peak temperature of 70-90 °C – a temperature of approximately 40 °C lower than classic acrylate systems. In order to carry out the mounting process, the use of UV permeable PP or PE molds is essential.
When compared to classical cold mounting agents, another advantage of the 1-component mounting agent is that it achieves a bubble-free, transparent mount without requiring a pressure pot. The use of KEM 50 UV is recommended for soft to medium-hard materials (hardness < 500 HV), as well as for the examination of core microstructures.
Light-curing mounting materials are not suitable for vacuum infiltration and are intended to be used in the area of shadow-free geometries. The preparation of screws, printed circuit boards and sintered materials for porosity determination are all possible.
Gap formation is limited to approximately 2-10 µm, despite the short curing time. The material obtains mechanical properties which are comparable to common standard cold mounting materials. The drastic reduction of the required mounting time compared to other mounting methods is arguably the biggest advantage of the system.
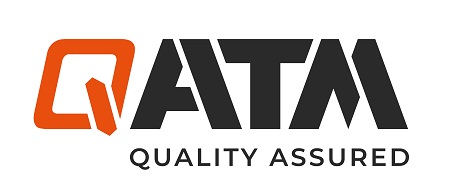
This information has been sourced, reviewed and adapted from materials provided by QATM GmbH.
For more information on this source, please visit QATM GmbH.