The petrochemical and petroleum refining sectors together are worth untold billions of dollars and are vital to the global economy. This industry provides fuels as well as a wide range of consumables, fertilizers, and polymers.
Hydrocarbon processing is a high-hazard business because of the nature of the petrochemicals being processed and handled, even though refineries and petrochemical facilities are among the most treasured industrial assets in the world.
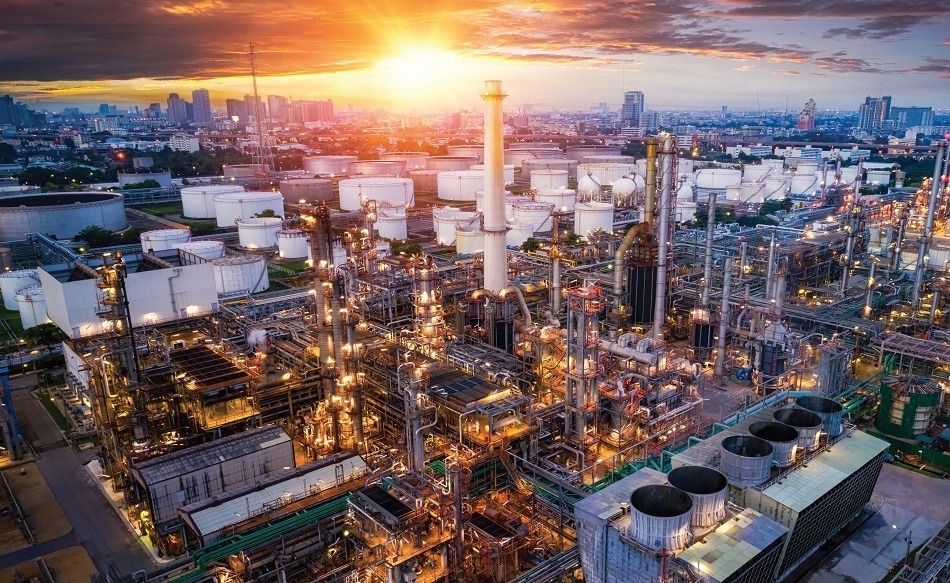
Image Credit: Thermo Fisher Scientific – Handheld Elemental & Radiation Detection
The industry’s top concern is still worker health and safety, with an emphasis on asset integrity and Process Safety Management (PSM). A lot of focus is put on preventing releases (spills, etc.) of poisonous and extremely hazardous compounds that might cause significant accidents. Unintentional releases may have negative effects such as outages, leaks, property damage, deadly accidents, and other risks.
At refineries, chemical plants, pipeline networks, and gas processing facilities, equipment failure is the main reason for losses. Such failure is often the result of an unintentional or incorrect replacement of building materials, which might have disastrous results.
Continuously precise and accurate material analysis is necessary to verify the Mechanical Integrity (MI) of systems, pipes, etc.
Utilizing Thermo ScientificTM NitonTM XL5 Plus portable XRF and NitonTM ApolloTM handheld LIBS analyzers, retroactive Positive Material Identification (PMI) assures that crucial refinery system components are what they should be by spotting issues or improper materials before they fail.
Mechanical Integrity (MI) continues to be a major consideration. Specific requirements aimed at reducing and preventing catastrophic releases are identified in enforcement rules like 29 CFR 1910.119 “Process Safety Management of Highly Hazardous Chemicals” provided by the United States Occupational Health and Safety Administration (OSHA).
Specific regulations were implemented by OSHA’s National Emphasis Program (NEP) to defend against possible disasters:
- June 07th, 2007: Enforcement Directive Number CPL 03-00-004;
- November 29th, 2011: Petroleum Refinery Process Safety Management National Emphasis Program and Directive Number CPL 03-00-014;
According to application industry statistics, there is a chance that 3% of rogue material makes its way into the field. This undesirable material often ends up in the final fabricated assembly, piping system, pressure vessel, or essential process machinery. Several circumstances at the point of entrance might result in the substance being accidentally utilized, including:
- Integrity of the original mill test report (MTR) is compromised during the procurement and supply cycle as ownerships exchanges and data is transposed or even manipulated
- Maintenance occurring outside normal operating hours is not subjected to typical QA/QC inspection practice
- Warehouse stocks inventory in the wrong location and error is carried forward
- Welder or pipefitter selects the wrong component during the fabrication process
- Welder uses incorrect filler metal due to selecting from the wrong rod box, improper labeling or stocking of inventory, or borrowing weld rods from a fellow welder
- Improper tagging or marking of materials during maintenance removal and lack of verification prior to re-installation.
- Component manufacturer applies the incorrect material stamp to a finished part
- Fabricator uses unmarked, unknown material during the fabrication process (i.e., loose stock, drops, cutouts)
- Multiple pieces are made from a single stock and material traceability is not maintained during fabrication (i.e., gussets, lift lugs, stiffener rings, support clips, pipe pups, gasket rings)
The US Chemical Safety and Hazardous Investigation Board (CSB) report No. 2005-04-B presents a lesson learned as a result of an investigation into an incident involving a significant fire at one of the largest refining complexes in the country, which resulted in reported property damage of $30 million and minor injuries.
Positive Material Verification Programs
A reliable, affordable, and quick Positive Material Identification (PMI) test technique is in-situ alloy material verification utilizing X-Ray fluorescence (XRF), laser-induced breakdown spectrometry (LIBS), or another non-destructive material testing. To optimize safety, facility owners, operators, and maintenance providers should make sure that verification processes demand PMI testing.
The American Petroleum Institute Recommended Practice (API RP) 5781 or other appropriate methods to verify all key service alloy steel pipe components removed and reinstalled during maintenance are appropriate verification programs.2
According to research on corrosion-related incidents at petroleum refineries in the European Union (EU) and Organization for Economic Cooperation and Development (OECD) nations, 9 out of 99 important refinery accidents included inadequate material composition. History shows that unintentional material substitutions continue to be a significant issue in the petrochemical and refining industries.
However, employing Recognized and Generally Accepted Good Engineering Practices (RAGAGEP) when implementing an efficient material verification program is supported by applying the principles and recommendations provided in API RP 578, “Material Verification Program for New and Existing Alloy Piping Systems” (MVP).
Owner-users can significantly lower the likelihood of material mix-up and avoid the consequences of failure while reducing corporate risk by implementing a thorough PMI training for pressure-containing components, welding process for in-service devices, new construction materials, or during maintenance activities.
Sulfidation corrosion, a key contributor to leaks in the refining sector, and its effects on steel pipelines and equipment are another area of concern. Carbon steels with low silicon content (sulfidation corrosion impacts steel piping and equipment) are a significant contributor to leaks in the refining industry due to the carbon steels’ (<0.10%) accelerated corrosion rate when exposed to hydrocarbon-containing sulfur compounds at high temperatures.
Sulfidation causes the pressure boundary wall to thin, allowing very dangerous compounds to escape into the atmosphere. Retrospective PMI is recognized as a material verification program (per API RP 578) inspection technique to identify and monitor sulfidation corrosion in API RP 939C, “Guidelines for Avoiding Sulfidation (Sulfidic) Corrosion Failures in Oil Refineries.”3
Additionally, HF alkylation is a crucial step in the refining process that creates petrochemical compounds. Since carbon steels, such as MonelTM 400, copper–nickel, and other nickel-based alloys like HastelloyTM C-276 and B-2, are common building materials, it is essential to choose, use, and position alloys within the process piping envelope properly to prevent unpredicted corrosion and degradation of pressure equipment components.
When residual element (RE) content is regulated during the HF alkylation process, carbon steel has shown acceptable corrosion resistance against HF corrosion. Case studies have shown that carbon steel’s REs, particularly Cr, Ni, and Cu components, could accelerate HF corrosion.
The ideal base metal parameters are C > 0.18% wt % and Cu + Ni + Cr, 0.15% wt %. As the type and concentrations observed will have an immediate impact on the necessary analytical procedure operations, these variables are crucial.4
A quick and precise nondestructive testing technique called handheld X-Ray fluorescence (HHXRF) may positively identify a material’s grade in accordance with standards while also confirming the alloy composition.
The use of HHXRF verifies the accuracy of materials that have been purchased, ensures quality assurance and control (QA/QC) during fabrication, satisfies end-user material requirements for products that are shipped, and ensures that welds and installed components correspond to the engineering design and application for which they were created.
The Handheld Laser-Induced Breakdown Spectroscopy (HHLIBS) technique for PMI analysis is also suggested by the API 578 third edition. HHLIBS is a rapid, precise, and almost non-destructive method for measuring alloy composition and determining alloy grades. The primary distinction between HHLIBS and HHXRF in the field is the capacity of HHLIBS to measure carbon.
When the measurement of carbon is crucial to the weldability or corrosion resistance of steel and stainless-steel assets, HHLIBS is chosen over HHXRF, despite the latter being simpler to use for studying a wider range of metals and alloys. Based on carbon content, HHLIBS can distinguish between steel and stainless-steel grades and determine the carbon equivalent from the observed composition.
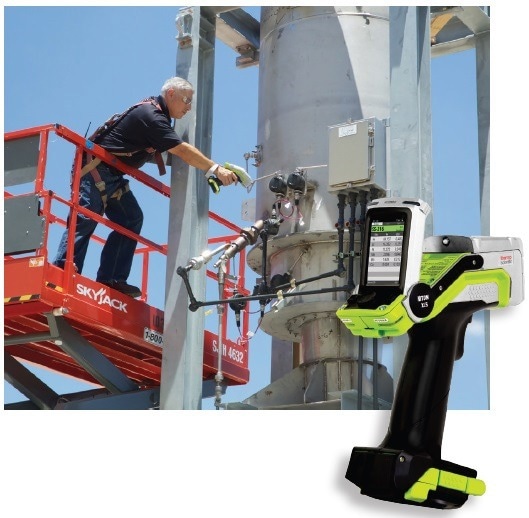
Image Credit: Thermo Fisher Scientific – Handheld Elemental & Radiation Detection
Niton XL5 Plus Handheld XRF Analyzer
The smallest and lightest high-performance HHXRF analyzer on the market is the Niton XL5 Plus portable XRF analyzer. In addition to reducing operator fatigue, the Niton XL5 Plus portable XRF analyzer allows testing in areas that are generally inaccessible to bigger HHXRF, HHLIBS, and mobile Optical spectrometry (OES) equipment.
In challenging refinery conditions, the Niton XL5 Plus portable XRF analyzer enables quick, precise elemental analysis spanning from Mg to Bi and offers the following major advantages to the refining industry:
- Highest overall accuracy, sensitivity, and quickest light element (Mg, Al, Si, P, and S) detection, thanks to a patented 5 W X-Ray tube and cutting-edge big silicon drift detector with a graphene window
- 2.8 lbs (1.3 kg) of lightweight design with optimized user comfort that allows for operator fatigue-free rope access PMI examination
- Enhanced productivity, thanks to mobility, which makes testing possible in confined locations
- Equipped with a snap-in Hot Work Standoff and an optional KaptonTM window to make measurements at high temperatures under typical process working conditions between 200 °F and 900 °F.
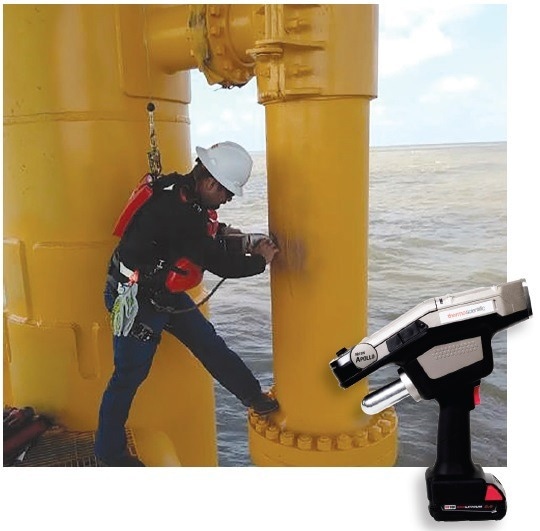
Image Credit: Thermo Fisher Scientific – Handheld Elemental & Radiation Detection
Niton Apollo Handheld LIBS Analyzer
When knowledge of carbon content is needed, the Niton Apollo handheld LIBS analyzer is a trustworthy instrument for material analysis and critical asset inspection. The Niton Apollo handheld LIBS analyzer, weighing just 6.4 lbs. (2.9 kg.), eliminates the need for bulky OES carts.
The Niton Apollo portable LIBS analyzer, which has a strong, accurate laser and high purity argon flush, offers PMI inspectors a number of advantages:
- Stainless steel L&H grades may be correctly identified by carbon measurement down to 0.01%
- Superior signal stability, precise chemical composition measurement, and identification of steel and stainless-steel classes based on principal alloy components and carbon concentrations are all guaranteed by sealed argon purge
- The computation of carbon equivalency and real-time display decide if steel is weldable
Modern devices with a smaller footprint and lighter load than existing HHXRF and mobile OES analyzers include the Niton XL5 Plus handheld XRF analyzer and Niton Apollo portable LIBS analyzer. Other characteristics include:
- Integrated 1.2 million micro and 5 million macro cameras, tiny spot analysis, picture capturing, and better reference and data integrity
- A flexible interface that enables simple optimization and tailored process solutions for certain applications, including carbon equivalency, residual and trace element analysis, and low silicon measurement
- A brilliant touch screen display with tilting capabilities that may be utilized while wearing gloves
- For difficult settings, the rugged housing is splash and dustproof
- Hot-swappable battery and battery life indication display for extended field usage
- Unmatched chemical and grade identification precision for consistently accurate findings
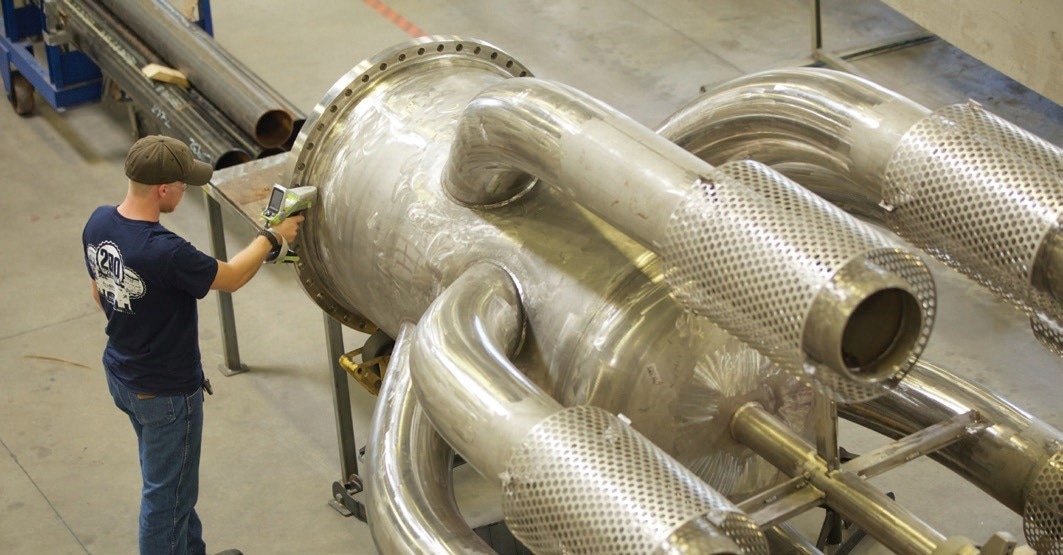
Image Credit: Thermo Fisher Scientific – Handheld Elemental & Radiation Detection
Instrument Selection for Material Verification Programs
Table 1 lists the instrument model that is ideal for the user’s PMI program. Both HHXRF and HHLIBS technologies may and ought to be employed in certain circumstances.
Table 1. Recommended Instrument(s) for Material Verification. Source: Thermo Fisher Scientific – Handheld Elemental & Radiation Detection
Program |
Application |
Recommended Instrument(s) |
API 578 |
General metal and alloya PMI |
Niton XL5 Plus |
P + S and main elementsb in low alloy steel |
Niton XL5 Plus |
C and main elementsb in carbon and low alloy steel |
Niton Apollo |
C and main elementsb in stainless steel for L/H grade |
Niton Apollo |
API RP 939 C |
Sulfidic corrosion: measuring Low Si (<0.1%) |
Niton XL5 Plus (needed on hot pipes)
Niton Apollo |
API RP 571 |
Residual elements: measuring low Cr+Cu+Ni (<0.15%) |
Niton XL5 Plus
Niton Apollo if C<0.18% needed |
a All elements from Mg to Bi including and all types of alloys including low alloy steel, chromium steel, stainless steel, nickel, cobalt, copper, aluminum, titanium, tin, lead, magnesium, zirconium, tungsten alloys, etc.
b Main elements are steel and stainless steel, including Al, Si, Ti, V, Cr, Mn, Fe, Co, Ni, Cu, Nb, Mo, and W.
Conclusion
Testing in-situ or in retrospect to determine if existing assets are still functional in an aging infrastructure is often fraught with difficulties. The Niton XL5 Plus and the Niton Apollo LIBS are specifically designed to fulfill the needs of process facility inspectors working in all industrial sectors, from petrochemical and refining to power generation, gas processing, offshore transportation, and pipeline transportation.
The Niton XL5 Plus is the perfect PMI instrument because it combines portability, exceptional ergonomics, and best-in-class analytical performance. When determining carbon content is essential, the Niton Apollo LIBS complements the Niton XL5 Plus as a maneuverable, indispensable and simple instrument.
References
- API RP 578 – Material Verification Program for New and Existing Alloy Piping Systems
- “Safety Bulletin,” U.S. Chemical and Safety Hazard Investigation Board, CSB report No. 2005-04-B, October 12, 2006, page 7.
- API RP 939C – Guidelines for Avoiding Sulfidation (Sulfidic) Corrosion Failures in Oil Refineries
- API RP 751 – Safe Operation of Hydrofluoric Acid Alkylation Units
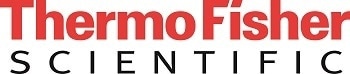
This information has been sourced, reviewed and adapted from materials provided by Thermo Fisher Scientific – Handheld Elemental & Radiation Detection.
For more information on this source, please visit Thermo Fisher Scientific – Handheld Elemental & Radiation Detection.