Sponsored by QATMReviewed by Emily MageeJan 5 2023
Objectives
The aim of this article is to explain the principle of materialographic cutting as well as the consumables and parameters which can influence the cutting result.
Metallographic cutting or sectioning usually marks the first step of the metallographic sample preparation process. In most cases it is necessary because the part or solid body is too large for the following metallographic grinding and polishing steps carried out on a laboratory scale. Depending on part geometries and material hardness as well as employed analytical techniques, different cutting techniques and consumables are used.
Cutting Process
Amongst the mechanical sectioning processes, wet abrasive sectioning is the most frequently used technique for the materialographic analyses, because it has a lowest deformation during the cutting process. It is suitable for the thin sectioning of hard materials and applicable to almost all solids. The exceptions include very soft polymers or rubber materials, but even then, there is still application potential.
In general, in the abrasive sectioning a small plastic deformation zone is observed which is commonly below a depth of 200 µm from the cut surface. This means that the grinding and polishing steps can be drastically reduced because there is less material to remove to reach the true microstructure.
However, curved cuts or complex sample geometries are not possible with this approach; in these cases, a saw, mainly a wire or band saw, can be applied. For the thin cutting there is a technique named microtomy. This technique is standard in polymer industry and biology with limited applicability on hard and brittle materials since a defined blade is used for cutting.
Cutting very soft and ductile materials like very hard and brittle ones can be optimized by choosing the appropriate cutting discs. As a rule, the following principle applies: Soft-bonded wheels are suitable for cutting harder materials, whereas hard-bonded wheels for cutting soft materials.
Workflow of Wet Abrasive Cutting
To start the wet abrasive cutting process, the part is placed and fixed in the clamping device in the cut-off machine. The user must then select the appropriate consumables, set the correct parameters, and place the cut off wheel into position. Consequently, the user must initiate the automated or manual sectioning process. After the sample has been sectioned, it can be removed and cleaned and then it is ready for use.
Requirements of the Cutting Process
The following requirements apply to sampling:
- Cutting by wet abrasive cut-off machine with sufficient cooling and rotating cut-off disc (e. g. no band saw). Otherwise, the deformation in the surface is so high that it cannot be rectified without reworking through tedious grinding.
- Optimum cooling is indispensable for evaluation. An excessively heated surface gives rise to misconceptions – artefacts simulate a false result.
- Corrosion protection agent must be added to the coolant, otherwise there is a risk of surface oxidation at the cutting surface. This is also important to protect the interior of the cutting device.
- The size and design of the cutter depend on the sample size – the criterion here is the so-called cutting capacity.
Types of Cutting
Symbol and Name
|
Description
|

Traverse cut
|
Two versions are possible in this case:
1. The sample table with the workpiece previously fixed on it is moved to the fixed cut-off wheel manually or automatically.
2. The cut-off wheel is moved accordingly.
|

Chop cut
|
The workpiece to be cut is firmly fixed on the cutting table. The cut-off wheel is then manually or automatically guided from top to bottom into the fixed workpiece.
|

Step-cut X
|
The workpiece is not cut in one cutting step, but in layers (stepwise). This type of cut is particularly suitable for cutting the large, thick workpieces of solid material.
|

Step-cut Y
|
The workpiece is not cut in one cutting step, but in layers (stepwise). This type of cut is particularly suitable for cutting the large, thick workpieces of solid material that must be clamped on edge (plates, angles, etc.).
|

Diagonal cut
|
In case of a diagonal cut, the table moves backwards (X axis) and the cut-off wheel moves downwards (Y axis) at the same time. This type of cut is particularly suitable for cutting asymmetrical workpieces, or for compensating the wear of the cut-off wheel to obtain a constant cutting depth.
|

Zigzag cut
|
The workpiece is not cut in one cutting step, but in layers (stepwise). The zig-zag cut is made in the middle of the component.
|

Care cut
|
During manual cutting, the clamping table (X axis) moves back and forth until the cut is completed. It starts with the movement from front to back. This type of cut is particularly suitable for workpieces where a clean cutting edge and material-friendly processing (temperature, deformation) is required due to the smallest possible contact surface.
|

Rotation cut
|
This process is most often used on precision cut-off machines. It can also be used for large workpieces with corresponding rotary sample holders. The sample is turned clockwise or anti-clockwise towards the cut-off wheel. Quarter or half rotations are also possible. For a round workpiece with a diameter of 50 mm, only a cutting distance of 25 mm is required.
|
Cut-off Wheel Selection
Wear (i.e., abrasion resistance), service life and cutting performance are decisive for the quality of the cut-off wheel. Abrasive agents (Aluminum oxide, Silicon carbide, Diamond, Cubic boron nitride (CBN), etc.) and bonding (metal, synthetic resin, or rubber) are characteristics of the wheel composition.
Application Range of Cut-off Wheels
The available QATM abrasive materials are listed below:
- Aluminum oxide cut-off wheels with synthetic resin bond for all steels, depending on hardness
- Silicon carbide cut-off wheels (SiC) for soft and medium-hard non-ferrous metals as well as hard non-metallic materials (glass, stone).
- Diamond cut-off wheels (C) for hard ceramic materials, ceramic composites and geological materials (rocks).
- Cubic Boron Nitride cut-off wheels for tough Co- and Ni-based alloys, hard metals, hard composite materials, and hard to very hard carbon steels.
The grain size of the abrasive in the cut-off wheel is an aspect that must not be neglected when cutting materialographic samples. It should be between 45 and 180 μm. This allows an optimally cut surface, which should facilitate further preparation, provided all parameters are observed. A very fine grain size is recommended when using thin cut-off wheels. A fine grain size is also important if burr-free cutting is required.
The degree of hardness of a wet abrasive cut-off wheel does not say anything about the hardness of the abrasive grains, but rather about the hardness of the bond, i. e. about the resistance of the individual abrasive grain to breaking out of the bond material.
- A softer bond should be used for large-area contact points between the workpiece and the wet cut-off wheel. This also ensures that worn abrasive grains are broken out. This type of cut-off wheel is also well suited for heat-sensitive materials.
- In the case of smaller contact areas, a harder and more stable wet cutoff wheel is however suitable. Those are also used for cutting tubes and profiles. The advantage of this type of cut-off wheel is that it has less contact with the workpiece since the wall thicknesses is usually small.
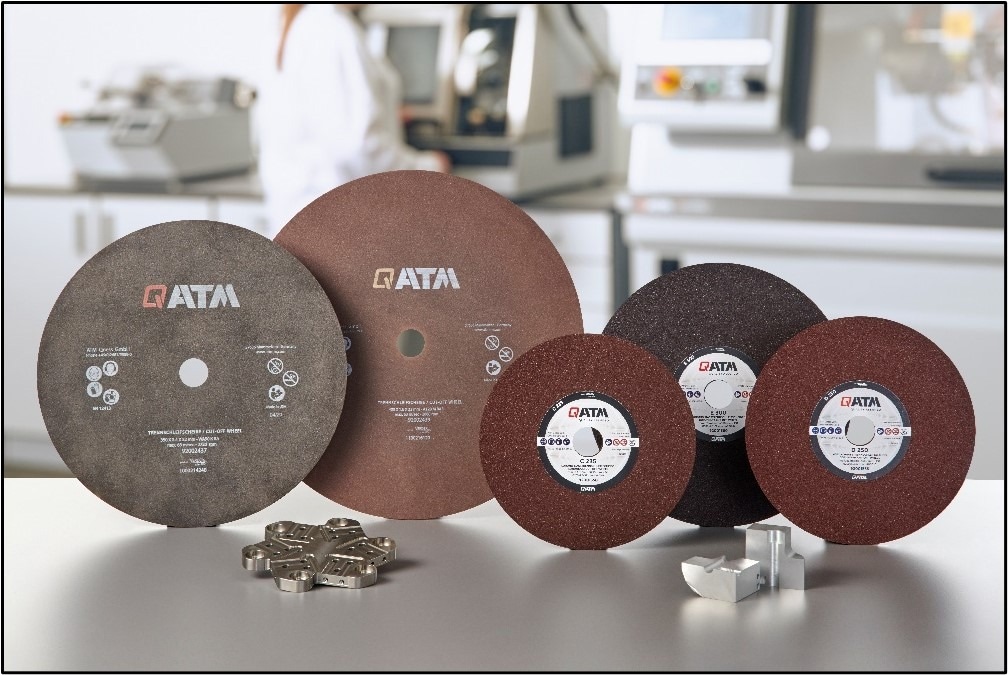
Figure 1. QATM Al2O3 cut-off wheels with rubber (left side) and synthetic resin bond (right side) Image Credit: QATM
Anti-Corrosion Coolants
Optimum cooling is essential during cutting. Excessive heat development during the cutting process damages the specimen as well as the cut-off wheel. The purpose of anti-corrosion coolant is to protect the machine and specimen from corrosion and to improve stock removal by providing suitable lubrication during the cutting process. Commonly the appropriate pH value for this purpose is between 9 and 10. To improve the cooling performance QATM’s coolants have higher boiling points than water.
The most common anti-corrosion coolants are the aqueous solutions which have a medium cooling performance and reasonable capacity to carry the abrasive residuals.
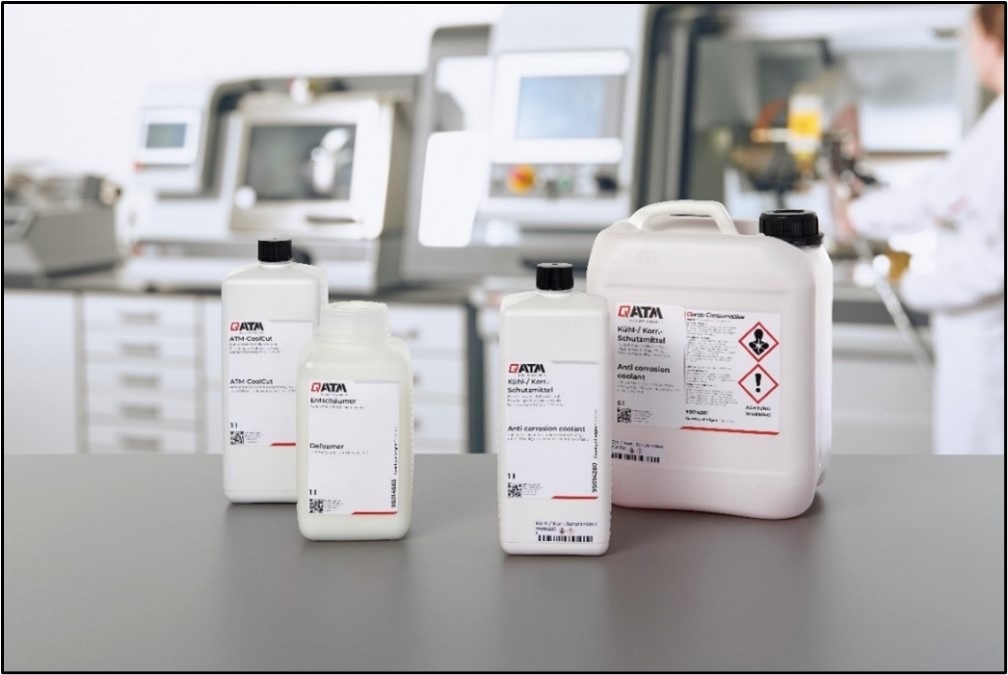
Figure 2. QATM anti-corrosion coolants Image Credit: QATM
Clamping Tools
A vast range of different clamping tools and systems is available for all QATM cut-off machines. With our clamping tools, any sample size and material are safely fixed for accurate cutting procedures. Our clamping tools include:
- A range of easy-clamping bases, available in three sizes
- Different head pieces to match the rotatable plates
- Vacuum sample holder, duo-sample holder, fast lock vices and swiveling prisms
- Vertical vices, fast lock vices, cross vices, angle vices, rotating vices, universal vices, and chain clamping vices.
- power clamping system, clamping jaws, step jaws; different clamping shoes, guide bars, height adaptors and more.
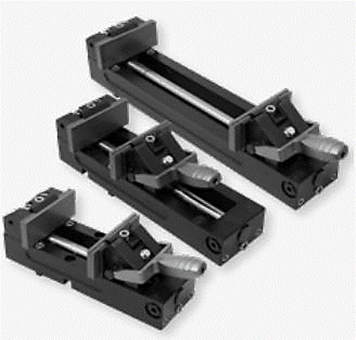
Figure 3. QTool clamping tool which can be fixed directly on the working table. Image Credit: QATM
Artefacts During the Cutting Process
The main error that the user must avoid during wet abrasive cutting is excessive heat generation, due to insufficient cooling. In this case, the generated heat causes the materials microstructure to be unpredictably altered in an impermissible way – it no longer represents the original material structure. This happened with the sample shown in figure 43 on the left side. The intensive tarnish colors are unmistakable, compared to the correctly cut sample in the figure on the right.
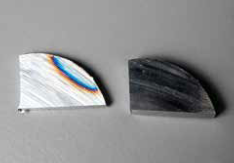
Figure 4. Samples which were cut with inappropriate cutting parameters Image Credit: QATM
Further cutting artefacts can be found in our materialographic sampling guide titled Expert Guide Materialograpy/Metallography. The following link provides a reading sample and information on receiving the Expert Guide.
Summary:
- The wet abrasive cutting is the most suitable cutting method for materialographic sampling due to low deformation. Selecting the appropriate cut-off wheel, sufficient lubricating and suitable cutting parameters can optimize the results.
- QATM cut-off machines allow the costumer to select the suitable parameters for cutting. Different cutting processes such as transverse or chop cutting, as well as a variety of cut-off wheels enable our customers to achieve the best cutting results.
- Select the suitable cut-off wheel can help you to prevent the cutting artifacts and save time. The wide range of QATM cut-off wheels with different abrasive particles and bonds offers our customers a wide choice to optimize their cutting processes.
- The clamping tools are another factor that should be considered for the cutting. QATM clamping devices come in a variety of shapes and sizes. Fast clamping devices and universal ones are versatile tools that every laboratory should have. However, in applications that require precision, customized clamping solutions, a large variety of QATM customized clamping tools are available to ensure each application can be catered.
- QATM anti-corrosion coolants protect cut-off machines as well as sample parts from the corrosion.
This article is an introduction to the principles of materialographic sampling (cutting). For more details, please refer to our guide to materialographic sampling titled Expert Guide, which can help you deepen your information on this topic.
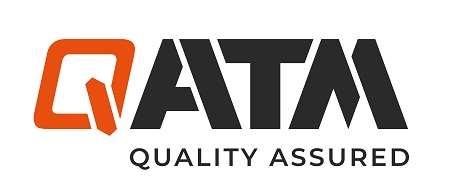
This information has been sourced, reviewed and adapted from materials provided by QATM.
For more information on this source, please visit QATM.