In this interview, AZoM talks to Dave Cist, Roger Roberts, and Rob Sommerfeldt from GSSI about the PaveScan RDM, PaveScan MDM, and their ground penetrating radar (GPR) capabilities. They also discuss how this can aid the asphalt production and compaction.
Could you explain how the compaction of asphalt affects pavement performance?
Rob Sommerfeldt: There are a number of studies dating back to the 1980s that state every 1% of density below the desired threshold resulted in a 10% reduction in the life of the road. That goes hand in hand with the amount of maintenance that has to be provided for the life of the road. So compaction is one of, if not the most important issue when it comes to pavement life.
Dave Cist: For instance, a new road might usually have an expected lifetime of around ten years. However, if it is poorly constructed and placed, this can easily be reduced to five years. On the other hand, if it is done well, the lifetime can be extended to around 15 or 20 years. Good compaction is one of the keys to long road life.
What is air void content, and how does this affect pavement performance?
Roger Roberts: When asphalt is compacted, the air void content decreases, so it is directly proportional to compaction. So you want to compact asphalt and decrease the air void content until it reaches a certain level. You need a little bit of air in the asphalt; otherwise, you will experience other issues.
What are the consequences of these effects, and why is this a problem?
Dave Cist: Essentially, water is the enemy of asphalt. If you have too many air voids, water can seep in, then freeze and crack. Dissolved chemicals in water can also penetrate and really mess things up. Therefore, you want asphalt compacted enough to produce a good water barrier.
However, as previously mentioned, if you compact it too much, you will encounter other problems. There is a sweet spot for asphalt compaction that depends on many factors including mix design, thickness and rolling methods. he main goal is to delay the inevitable fatigue and deterioration (think potholes) for as long as you can.
What are some of the density assessment techniques that are currently in place?
Rob Sommerfeldt: The “accepted” way right now is through the application of a few different methods. For example, one method utilizes a spot-checking type of technology where a contractor or even the department of transportation or the ministry of transportation go out with either a nuclear gauge or a PQI, which is a non-nuclear gauge, and they pick random spots.
When inspecting miles of road or 1,000 or 2,000, 3,000 feet of road, they will pick maybe ten spots, and those ten small spots will determine a few things. Another way to spot check is to locate ten random spots for coring, and literally go out and pull X number of cores, depending on the specifications, and take those cores to the lab, evaluate them, and calculate the density of those cores.
Could you provide a brief introduction to what ground penetrating radar is and how it supports workers in the field?
Rob Sommerfeldt: Simply put, ground penetrating radar facilitates penetration of the surface of the ground, or asphalt, or concrete, allowing you to see what is going on underneath the surface. Depending on the application and the type of equipment used, penetration is possible from instruments that can go 18 inches deep all the way to 30 or 40 feet depending upon the type of material that is being penetrated through.
Roger Roberts: On a more technical note, the ground penetrating radar utilizes electromagnetic waves radiated from an antenna to probe the subsurface and record the energy that is reflected back from discontinuities in electromagnetic properties. Many of the buried objects that we see have a significant contrast in electromagnetic property compared to soil.
We see a lot of buried objects that way, but PaveScan technology is different than typical ground penetrating radar because, with PaveScan, we are only looking at the reflection off of the surface of the asphalt; we are not penetrating the asphalt beyond a very tiny amount.
What recent advances in ground penetrating radar have aided GSSI in this field?
Dave Cist: This is a field that has been improving steadily over 20 to 30 years. Previously, accuracy levels for measuring compaction used to be around 10%, which if you are trying to measure a 1% improvement on asphalt density is kind of useless.
Over the years, we went from 10% to 5% to 2%, and now we have achieved an accuracy level that is below 1%. The technique has improved partly because of improvements in equipment. The hardware has become more stable and more accurate. Progressively, the accuracy and repeatability of the measurement techniques have also improved. Then, there are all kinds of other things like cloud-based capabilities in order to be able to take the data and be able to share and make it immediately available as well as real-time visualization.
Why is it advantageous to do away with field calibration cores?
Dave Cist: First and foremost, most contractors do not necessarily like holes being punched in their perfect, new mat. Since it creates weak points in the mat, it can easily become the first pothole.
Moreover, when you pull a core, it can be miscut, mislabeled, mishandled, or break apart. There are all sorts of things that create an error in the measurement of the cores themselves. Bad core results can fail a job that might be perfect. On the other hand a bad job might pass because of a lucky core location or an erroneous measurement.
Coring is also dangerous; there is a real risk of being hit by a car when taking the sample from the middle of a major highway at night. It is also an expensive process; you have to pay for a crew and maintain the crew, the trucks, the equipment, and the lab measurements in addition to the police detail and the bumper-trucks. There is a slow, steady cost added to the construction job just for doing the coring. I have never met a QC technician without a near-death story to tell.
So the obvious advantage of GPR is that it is a non-destructive test, whereas coring is destructive. But the other advantages of safety, cost and accuracy are just more good reasons to end reliance on field cores.
How does GPR help, and what are the main goals/objectives when using these instruments?
Dave Cist: Starting with the [old] method, you waved an antenna over the ground to display asphalt density at each point. Then with three antennas side by side, three times the data let's you quickly make full-coverage maps of an entire lane or an entire runway.
The goal is to let the experts be the experts. They don't care about geophysics or reflection amplitudes. The expert knows that you always risk low densities along longitudinal joints. The expert knows that when your mix gets cold (and stiff), you are going to need to roll it more to achieve the same density. If you can measure it during the job, you have a chance of fixing problems as they arise.
And after the job, when they see a map of the final product, they can instantly assess the quality of the work -- see where the paver stopped or where the equipment broke down or where the roller pattern went wrong.
Quality Assurance is what road owners wish they had. Quality Control is what contractors wish they had. GPR give process control to both.
Rob Sommerfeldt: The bottom line is that, as a quality control type of tool, it allows the foreman or whoever is the head of the project and is on-site to make very intelligent decisions based on feedback that can be obtained in real-time from PaveScan RDM.
To what extent are project workers able to perform a good quality check throughout the whole process, and how important is time when it comes to addressing potential issues on the road?
Rob Sommerfeldt: At present, the nuclear gauge and its random spot checks do not provide enough information to enable such intelligent decisions to be made on-site in real-time. I have been on sites where PaveScan RDM was used as a demo. During the demo, we were finding issues, and stopping the job to fix them before we continued on. This has proved very successful.
Furthermore, when it comes to coring, this process could take anywhere from a day to a week in some cases. However, when it comes to detecting an issue, a day or a week is too late. This is simply due to the amount of paving that can be carried out in a day, let alone a week. So real-time evaluations are very much essential.
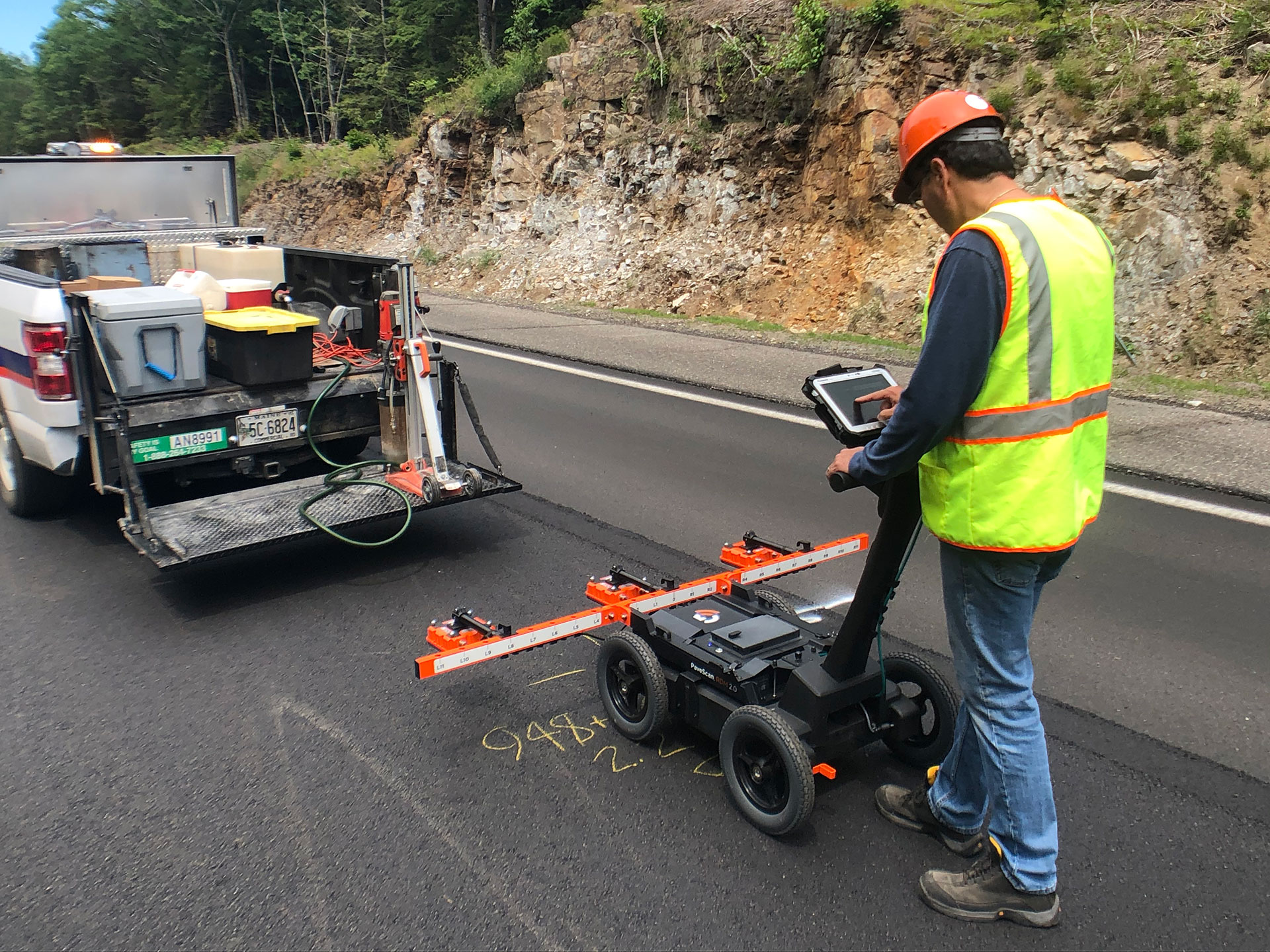
GSSI's PaveScan RDM 2.0 system. Image credit: GSSI
Dave Cist: I have also been on jobs where their real-time PaveScan map shows areas of low compaction. It wasn't too late for the roller operator to hit it again to bring compaction up. Thanks to real-time mapping, compaction problems can be spotted and fixed "in train", which is a huge win.
Of course to do a good job, contractors also need to control the mix coming from the plant. If the mix is wrong, this can affect production for the rest of the day and ruin a job. Some bad mixes simply can never be rolled out properly, which is why maintaining the mix quality at the plant is just as important as placing it.
GPR can help in its calibration process. PaveScan calibration takes a dielectric value, an electrical property that no one cares about, and converts it to percent voids or the compaction level. The accuracy of that calibration is the hidden key to PaveScan's success, and the best way to calibrate is to integrate into the plant's process for making good mixes.
Can you tell our readers more about the newest PaveScan product, the PaveScan MDM?
Dave Cist: PaveScan MDM, the mix design module, is used in the plant's Materials Lab.
Rob Sommerfeld: For the MDM, the one in the lab, we simply get samples from the asphalt plant and take those samples and compact them to a certain compaction level. We are then able to measure that and calibrate the PaveScan RDM system.
How important is the PaveScan MDM in the process, and how does it support the work you do?
Dave Cist: The mix design module measures the mix design, and there are hundreds of mix designs that are made over the course of the winter before the paving season.
If you have a high-traffic road with lots of trucks, a specific mix design is needed; if it is a parking lot just for cars, then a different mix design would be required. Mix designs are adjusted for a plant quarry that is blasting granite rather than blasting limestone or if it rains the night before. These are all important things to consider, and it takes decades of experience for a plant QC Manager to fully master the mix.
What we can do with the PaveScan MDM is take the mix relevant for a particular road or purpose and very accurately measure any changes in the mix from day to day or hour to hour. We can even take a mix design change and help to predict how it will behave when placed. This is essentially a way of troubleshooting the mix in the lab before the asphalt is even created so that it does not have to be disposed of it if something were to go wrong.
Roger Roberts: One of the major values of our method is that we can pre-calibrate our equipment so that when the user uses it in the field, they can get percent compaction numbers. Other equipment is calibrated differently, but conceivably we can have it pre-calibrated, and the calibration can be updated if there are changes in the mix during the day.
No other product really does this, but we can as we are actually in the lab; we can be in the lab right where they are making the asphalt. So this is a lot more accurate.
Dave Cist: There are two benefits to this; one is it helps us make our equipment accurate in the field – i.e. the calibration process. The other is that we can monitor and track any minor changes that might occur, even down to which stones got wet the rain the night before. We are sensitive to that. The calibration part is great for us, but then there is the mix and data we can provide about the mix, which can be a great help to the plant operator.
Rob Sommerfeld:A third benefit would be that the need for coring may eventually be eliminated. This is because the calibration utilizes samples from the plant rather than from coring, for example.
What were your methods of verifying the new testing protocol?
Roger Roberts: Everybody relies on cores to assess whether or not the equipment is working properly. Given that there are some uncertainties in each core measurements, you cannot just use a few cores as ground truth. The equipment accuracy has been verified using numerous cores obtained from multiple paving jobs around the country as part of the SHRP2 R06C government-funded research project.
Can GSSI's GPR measurement method be widely implemented, or are there still some issues to overcome?
Dave Cist: We are always going to push for higher and higher accuracy. One of the things we have not really touched upon is the testing that has been done all over the country and other parts of the world as well, and so the calibrations have proven accurate in Arkansas, in Sweden, in the Granite State of New Hampshire, with Florida limestone and Alaskan quarries.
It works everywhere we've tested, having proven accurate for many different mixes and with diverse stones, and in lots of different asphalt plants. We are always looking for surprises in mixes we haven't yet tested, but generally, we are no longer working on the big problems, just corner cases and minor surprises.
What is next for this research?
Dave Cist: There is a lot of really exciting research in the works. For example, we have been aiming to get it under the roller for years.
However, before this is possible, there are some technical problems to overcome. Rollers put down moisture on the mat, and moisture can throw off the measurement. So we have been figuring out different ways and researching various methods to account for that and help with that process.
We think that we are now at a point where we can make accurate measurements, nearly as accurate as the PaveScan RDM, and plenty accurate enough to be useful for roller operators and QC managers. This is a huge step forward in our research.
One of the really interesting things relates to lab measurements. We can use our MDM, the bench-top device we use to calibrate PaveScan, to measure individual stones.
This opens up a world of opportunity for creating an extensive database at each plant, where we can predict with high accuracy whether a mix change is going to be good. That adds tremendously to the process control of the plant.
We can also measure if the quarry stones have changed or if one particular stone size got wet from rain. We can know that immediately, and isolate which component was bad or which has changed because of the quarry or the way it was sieved. There are all kinds of complicated things that can cause trouble which we can flag more accurately than possible before.
Roger Roberts: Moisture can be a big problem in aggregate. Ideally they burn it off before the asphalt is made, but often they do not do it enough, especially if the aggregate gets really wet from rainfall.
Until now, there was no ideal way to find out if you have excess moisture in your mix. However, as we do pre-calibration, we can predict if there is some moisture in your mix the day you mix it all up. Therefore, there is a lot of potential in that area.
Optimistically, we ought to be able to significantly improve the life of many roads that are placed around the world with such monitoring, resulting in billions of dollars in cost savings.
About Dave Cist
Starting with GSSI in 1996, David was first hired to develop GPR equipment that was progressively more intuitive and easier to use. He has been GSSI's VP of Research & Development since 2017.
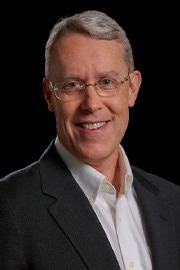
About Roger Roberts
Roger has been at GSSI since 1994. His work has been focused on extracting useful quantitative information from GPR data. Recently, he has been deeply involved in the development of GSSI’s PaveScanRDM, and PaveScanMDM products.
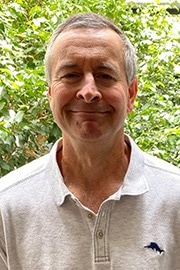
About Rob Sommerfeldt
Rob Sommerfeldt started with GSSI in 2007. He began this career as a trainer and customer support. Starting in 2015, Rob was promoted to sales of products regarding the infrastructure industry. Most recently, Rob has been involved in the development of the PaveScan RDM and MDM systems and providing education on this technology throughout the industry.

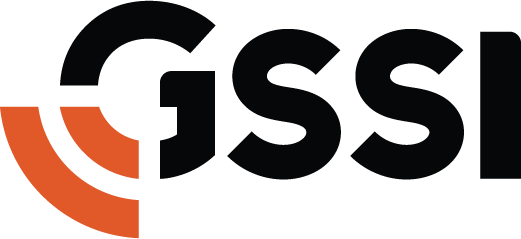
This information has been sourced, reviewed and adapted from materials provided by Geophysical Survey Systems Inc.
For more information on this source, please visit Geophysical Survey Systems Inc.
Disclaimer: The views expressed here are those of the interviewee and do not necessarily represent the views of AZoM.com Limited (T/A) AZoNetwork, the owner and operator of this website. This disclaimer forms part of the Terms and Conditions of use of this website.