Sponsored by PerkinElmerReviewed by Olivia FrostAug 30 2022
Epoxy resin is a versatile product in numerous industries thanks to its well-known strong adhesive properties. Due to its resistance to heat, moisture, and chemical exposure, it is the perfect material for encasing OLEDs (organic light emitting diodes).
Epoxy resins are frequently utilized for adhesive applications in addition to moisture barrier uses. Epoxy can be used for engineering and structural purposes due to its strength. The aerospace and automotive sectors use some of their most intriguing applications to create lightweight components with intricate composite architectures.
Epoxy adhesives are crucial to the electronics, building, painting, and coatings industries as well; therefore, it is important to look into and comprehend the characteristics of epoxy resins.
The cure kinetics of a thermosetting resin, like epoxy, is a crucial component of the substance. Kinetics is the modeling of how temperature and time affect how well thermosetting glue cures.
A researcher or process control engineer might use the knowledge gained from the establishment of cure kinetics to estimate the shelf life of thermosetting resins or composites or to improve processing settings.
Three methods can be used with DSC to ascertain the cure kinetics of a thermosetting resin:
- Investigations of isothermal cure at three or more distinct temperatures
- Multiple dynamic heating experiments (three or more different heating rates)
- Single dynamic heating experiment
The cure kinetics of a thermosetting material, like epoxy, is most accurately predicted using the isothermal method.
This is because maintaining isothermal conditions prevents potential issues like the occurrence of temperature gradients from occurring. Both standard (nth order) and autocatalyzed resins can be used with the isothermal technique.
When used in autocatalyzed systems, the dynamic DSC technique can produce kinetics data that is wildly inaccurate. Additionally, isothermal studies typically model and match the actual processing conditions needed to produce the ultimate thermoset product, the finest for processing optimization.
A DSC system with a very quick response time is required to carry out proper isothermal cure experiments. This makes sure that as soon as the isothermal goal temperature is reached, the sample and instrument can equilibrate promptly. The whole curing exothermic peak will be acquired without losing important data, thanks to a highly reliable DSC.
Power Compensation DSC
The Power Compensation DSC from PerkinElmer Instruments is the best DSC for carrying out isothermal cure tests of thermosetting materials. Low thermal inertia and the quickest response time of any DSC equipment on the market are provided by very low mass furnaces.
This enables the ballistic heating of an uncured resin at a rate of 400 or 500 °C/minute from ambient temperature to the required temperature (around 150 °C).
The Power Compensation DSC may immediately “lock in” on the isothermal target temperature and “equilibrate” due to the short response time. This offers the highest-quality isothermal cure peak and reduces the possibility of cure data loss, especially during the very essential early stages of the isothermal study.
As many epoxy resins exhibit their maximal rate of cure at the beginning of the experiment (time = 0), this phenomenon is known as nth order kinetics. A very responsive DSC, like the Power Compensation DSC, is necessary to achieve the full cure exothermic peak. In addition, heat flux DSC devices have a slower response time due to their larger furnace.
Due to this, it is unable to conduct isothermal cure investigations since the heat flux DSC cannot heat and equilibrate as rapidly as the Power Compensation DSC. Sophisticated DSC kinetics software (N5370610) from PerkinElmer is available for the most thorough investigations of the kinetics related to thermoset cure and thermoplastic crystallization.
Experimental
A powdered epoxy resin’s cure kinetics were evaluated under the following circumstances.
Source: PerkinElmer
Experimental Conditions |
Instrument |
Power Compensation DSC |
Cooling Device |
Intracooler II |
Sample Mass |
12 mg |
Sample Pan |
Open aluminum pan |
Purge Gas |
Nitrogen |
Isothermal Cure Temperatures |
160, 155, 150 , 145 and 140 °C |
Temperature Program |
Heat from 25 to isothermal temperature at a rate of 400 °C/minute and hold for 60 minutes |
Cure Kinetics Using DSC
The PerkinElmer PyrisTM kinetics program (N5370610), a complete package, makes it simple to evaluate the cure kinetics of a thermosetting resin. The isothermal technique was used in this study’s kinetics examination of the epoxy resin.
For both nth order and autocatalyzed resins, this method extracts kinetics data to the best, most accurate, and most dependable degree. The rate of reaction, dx/dt, is considered to be the sum of two functions, k(T) and f(x), for the analysis of the epoxy cure kinetics.1,2,3
The temperature reliant function or rate constant, k(T), is:
k(T) = Ze-Ea/RT
where R is the gas constant (8.314 J/mol deg), Z is the pre-exponential factor, T is the absolute temperature (°K), and Ea is the activation energy. This equation implies that the reaction rate is greater at extremely high temperatures.
The second function, f(x), shows how the reaction rate depends on how much of a response there is. Consequently, the rate drops when the reactants are depleted. This function is written as follows:
f(x) = xm(1-x)n
where x is the proportion of the reaction and m and n are the reaction orders. This process is autocatalyzed, and when m = 0, the resin exhibits the more typical nth order kinetics as follows:
f(x) = (1-x)n
The Pyris kinetics program analyzes the degree of response (or the partial areas of cure) automatically before performing an ideal factor to the aforementioned equations to derive the kinetic parameters. This information is used to calculate the activation energy of cure, Ea, preexponential component, Z, and reaction order, n.
DSC Results for Epoxy Resin
The DSC data obtained on the epoxy resin using heating at a rate of 10 °C/minute are shown in Figure 1. The main transitions may be seen, such as the Tg at 74 °C, the peak of enthalpic relaxation at Tg, and the exothermic peak of the cure between 125 and 220 °C, with the peak maxima at 165 °C.
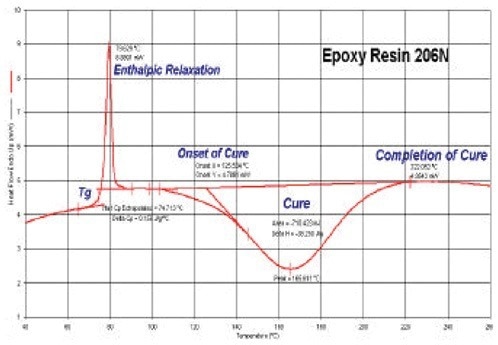
Figure 1. DSC results for uncured epoxy resin. Image Credit: PerkinElmer
The DSC isothermal cure curves for epoxy resin at various isothermal temperatures are shown in Figure 2. These results show the necessity of a DSC with a quick response time as the peak maxima (highest rate of cure) occur at the beginning of the isothermal waiting period.
This is what one would anticipate from a resin that follows nth order dynamics. The first part of the cure exotherm would be destroyed with a heat flux DSC as the device tries to restore the equilibrium state. Incorrect isothermal readings and issues with the next kinetics analyses will result from the reaction’s lost heat.
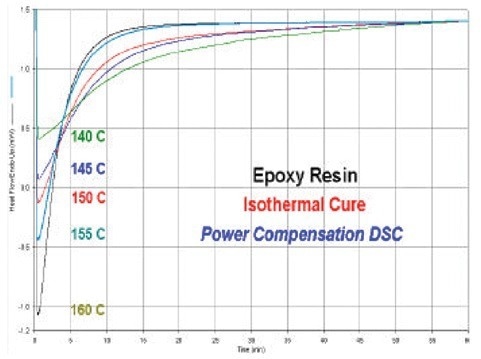
Figure 2. DSC isothermal cure curves for epoxy resin. Image Credit: PerkinElmer
Utilizing PerkinElmer kinetics software, the isothermal DSC values at 160, 155, and 150 °C were evaluated. The so-called log–log plot, which is shown in Figure 3, illustrates the degree of fit of the isothermal DSC values. These log–log charts can be used to calculate the kinetics parameters.
First order kinetics is supported by the discovery that the Arrhenius activation energy, Ea, is 81.4 kJ/mole and that the average reaction order is n = 1.2. The value of lnZ, the pre-exponential function, was found to be 17.2.
The cure kinetics of the epoxy resin can be modeled thanks to the calculation of these kinetic parameters by the PerkinElmer kinetics software system. The generation of cure prediction curves, which are very helpful for process optimization and for estimating the resin shelf life, is thus possible.

Figure 3. Log-log kinetics plots generated from kinetics software at temperatures of 160, 155, and 150 °C. Image Credit: PerkinElmer
The predicted curves for isothermal conversion produced by the kinetics software are shown in Figure 4. At various isothermal cure temperatures, these curves display the estimated level of cure (% reacted) as a function of time.
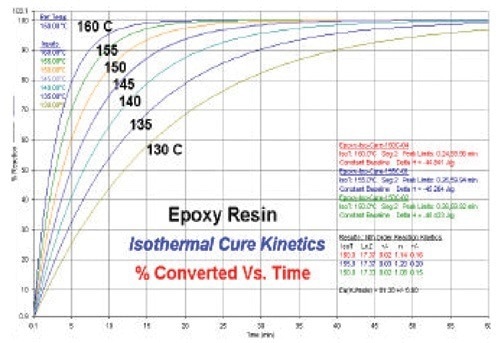
Figure 4. Isothermal conversion predictive curves for epoxy. Image Credit: PerkinElmer
The estimation of thermosetting resin cure times can be done using this predictive data. The isochronal conversion curves are displayed in Figure 5 and indicate the projected level of cure as a response to the temperature at various time intervals.
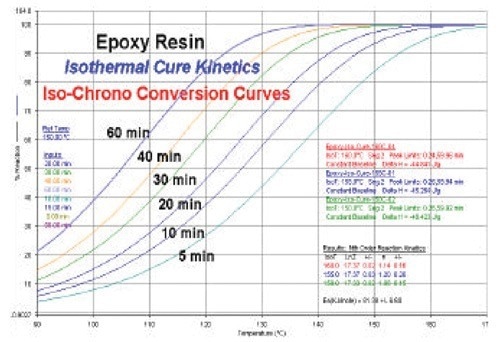
Figure 5. Isochrono conversion predictive curves for epoxy. Image Credit: PerkinElmer
The crucial connection between conversion (% cure), temperature, and time is established by the cure kinetics. Figure 6 shows the predicted curves for the epoxy resin’s iso-conversion curve. These curves demonstrate the relationship between temperature and the amount of time needed to reach the specified goal level of cure.
A thermosetting resin’s shelf life can be predicted using these curves. The process engineer can choose the best temperature–time conditions for producing a component made of a thermosetting resin with the aid of these prediction curves.
The kinetics information can be used to balance energy use and cure completion for thermosetting products.
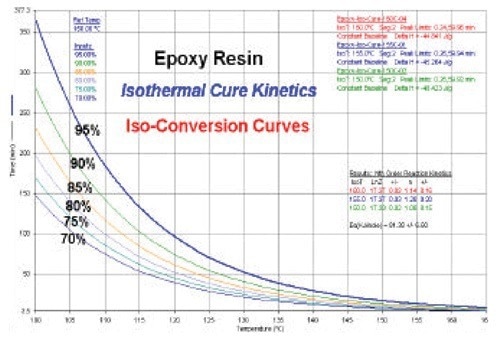
Figure 6. Isothermal conversion predictive curves for epoxy. Image Credit: PerkinElmer
Summary
When used with the excellent performance PerkinElmer Power Compensation DSC, the PerkinElmer Pyris Kinetics software offers a potent tool for examining cure and crosslinking reactions related to thermosetting substances. This software offers a way to judge the kinetics data’s level of quality and offers flexible input options to enhance the analysis.
The kinetics analysis offers valuable information on the cure characteristics of a thermosetting resin. The kinetics software can be utilized to address the consistency and quality of thermosetting resins.
The isothermal technique is the best, most precise, and most trustworthy way to measure cure kinetics by DSC. Since the isothermal technique closely resembles the real processing parameters used with the majority of thermosetting resins, it offers practical information.
A DSC instrument with a very quick response time is necessary for the establishment of isothermal cure kinetics. Considering its extremely quick reaction, the Power Compensation DSC from PerkinElmer is the finest DSC for this crucial application.
References
- Sichina, W.J., Proceedings of the 16th NATAS® Conference, Washington DC, (1987), 147.
- Flynn, J.H., J. Thermal Analysis, (1988) 34:367.
- Flynn, J.H., J. Thermal Analysis, (1991) 37:293.
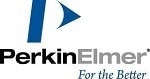
This information has been sourced, reviewed and adapted from materials provided by PerkinElmer.
For more information on this source, please visit PerkinElmer.