Animal feed producer Mars GmbH, located in Verden, Germany, operates its boiler house in accordance with the operating permit authorized by the local certifying body and the harmonized European standards, DIN EN 12952 and 12953. This also conforms to the formerly applied Technical Steam Directives (TRD).
Among others, special measures for 72-hour unsupervised operation are outlined in these requirements.1-5 In the event of potential contamination of fats, oil, and grease (FOG), a dependable system is essential to avoid FOG ingress into the steam generator. This system is enhanced by online monitoring, which can signal automatic drainage of the contaminated condensate.
The specifications of the boiler manufacturer state that the boiler feed water and returned condensate must be free from organic contamination. While the make-up water portion of the boiler feed comes from a regulated process, the condensate is exposed to potential contamination throughout the heat exchange. It should therefore be closely monitored.
Due to immense maintenance and imprecise measurement values, a previous attempt to determine the condensate's organic contamination with the use of a UV-sensor solution was canceled.
Cleaning was required multiple times a day as high levels of particulates affected the measurement and covered the optical windows. Such optical sensors are also not sensitive enough to catch the low-level organics in the condensate.
Challenge
Steam is used in various processes in an animal feed production facility: for sterilizing, heating, and cleaning, or direct steam treatment of a product. The liquefaction of bovine suet through a heat exchanger, for example, is one such steam application in the Mars GmbH facility. Therefore, there is a threat of organics intrusion in the form of FOG into the steam cycle.
Insufficient detection using standard sensors such as conductivity or pH probes is the challenge with fats or oils. Fat and oils barely dissociate in aqueous solutions and thus only slightly impact these two measurement parameters. Therefore, the determination of organic contamination could not have been possible.
On weekends, the boiler house is unmanned. Regulations for boiler operation in an unattended case state, “If there is a possibility of FOG ingress, a two-circuit system must be provided. This can be dispensed with, if it is ensured by suitable equipment that no oil or grease can get into the steam generator, e.g. the use of reliable monitoring devices with automatic drainage of the condensate."3
Another difficulty is the condensate matrix of the Mars GmbH plant. To prevent corrosion, the boiler is treated with nonvolatile amines that retain alkaline pH in the boiler water. The nonvolatile amines do not transition into the steam phase, which keeps the steam clear of any contaminants and at a relatively low pH of 7-8, meaning that it can be used for direct product contact.
However, the reduced pH encourages corrosion and can damage condensate pipes, which results in large quantities of particulates. Within an analyzer employed to monitor condensate, such particulates can cause clogging and disturb analysis.
Solution
Conventional sensors do not adequately sense organic contaminants. Instead, organics monitoring in the form of Total Organic Carbon (TOC) analysis provides an all-inclusive approach to capturing organic substances irrespective of their type. It can be incorporated into the system for quick online analysis.
Sample preparation, however, is critical to an efficient automated system with minimal downtime.
Condensates have increased temperatures. The water is usually contaminated with particles from piping corrosion (Figure 1) and can include conditioning chemicals. The pH value ranges from neutral to alkaline.
The Mars GmbH facility is conscious that its condensate contains several particles that appear to be mostly rust particles. Even though these particles do not contribute to organic pollution, they disturb analysis as they can result in blockages and deposits in analyzers.
Sample preparation is essential for this application and vital for robust and accurate analysis. Therefore, the feed manufacturer agreed to a trial of an online TOC analyzer, the Sievers* M9 that is already established in condensate monitoring, with sample preparation customized to the application.
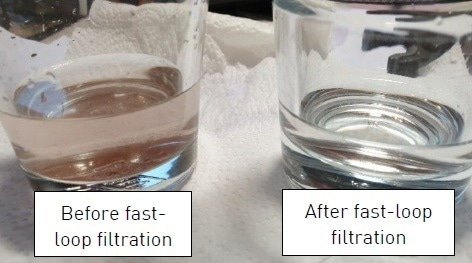
Figure 1. Comparison of condensate before and after pretreatment. Image Credit: Veolia Water Technologies & Solutions
The objective of the trial with the Sievers M9 TOC analyzer was to test filtration for sample preparation that Sievers Analytical Instruments has made in collaboration with an engineering company with the following properties:
- Pressure resistant up to 60 bar
- Temperature resistant up to 150 °C
- Resistant and robust against bases and acids by the exclusive use of stainless-steel elements
- Low maintenance resulting from the self-cleaning properties of a fast-loop filter
- Filter components ranging from 1–200 µm pore size for various applications, a 5-µm filter element was used in this trial (Figure 5)
- Flow monitoring for filtrate
- Compact design (Figure 2)
- Backwashing the filtrate lines and filter and (optional)
- DOC filter or a cooling coil in the filtrate flow (optional)
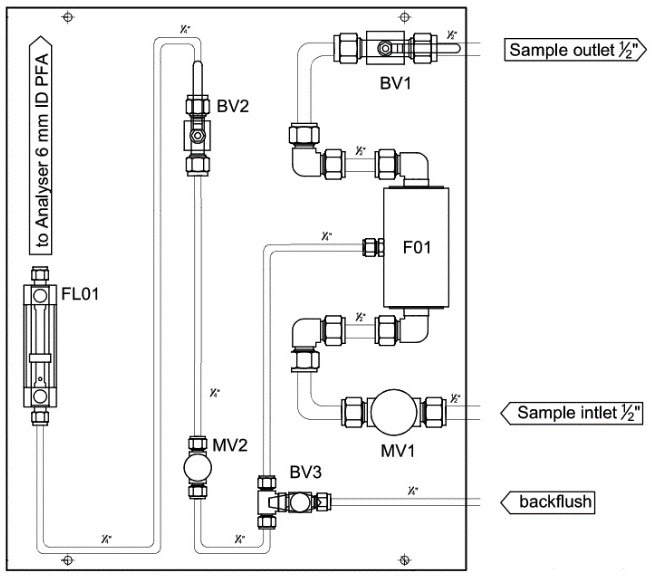
Figure 2. Fast-Loop filtration plate. Image Credit: Veolia Water Technologies & Solutions
The Sievers M9 TOC analyzer uses Sievers exclusive membrane conductometric detection technology to ensure precise measurements.6, 7
This technology employs a gas-permeable membrane that selectively passes only carbon dioxide produced by the organics' oxidation, thereby preventing other byproducts of oxidation from interfering with the measurement and offering accurate results (Figure 4).
The long-term calibration stability, low maintenance, and the capacity to provide accurate results on the lowest levels of organics make the Sievers M9 the best option for condensate monitoring.
Further advantages of the Sievers TOC Analyzers include minimum reagent consumption in uninterrupted operation, no requirements for instrument air, short measurement cycles, and a compact, user-friendly design.
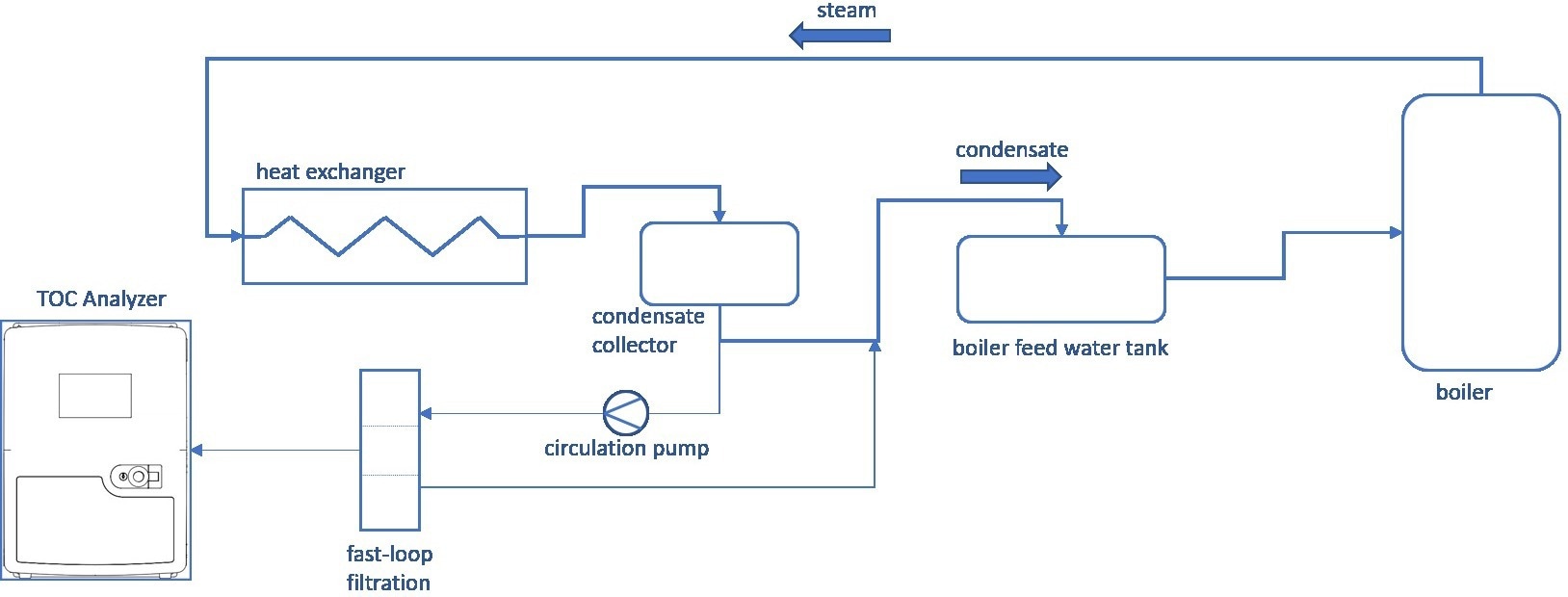
Figure 3. Process demo set up. Image Credit: Veolia Water Technologies & Solutions
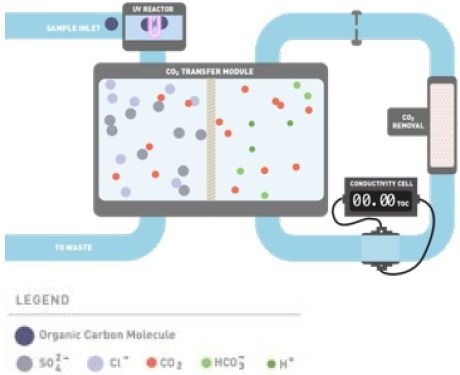
Figure 4. Membrane conductometric technology. Image Credit: Veolia Water Technologies & Solutions
Trial Setup and Results
For the trial installation, the sample was sourced from the condensate return line immediately before the feedwater tank. The condensate was conveyed to the pre-treatment system and returned to the main pipe (Figure 3) by a fast-loop line equipped with a circulation pipe.
To supply 200–300 mL/minute of filtered sample to the TOC analyzer, the flow rate of the circulation pump of around 6 L/minute was sufficient.
At the sampling point, the highest temperature of the condensate was specified at 105 °C. The temperature at the integrated online sample port (iOS) of the analyzer did not reach over 90 °C due to losses across the fast-loop and pre-treatment system.
The Sievers M9 was equipped with a high-temperature iOS, appropriate for up to 95°C sample temperature, so no further sample cooling was required.
After an initial flush-in time during which all the new lines from the sampling point to the analyzer had to have any residual organics cleaned out, the measured results stabilized below 100 ppb TOC (Figure 5). These outcomes established the cleanliness of the returned condensate from organic contamination.
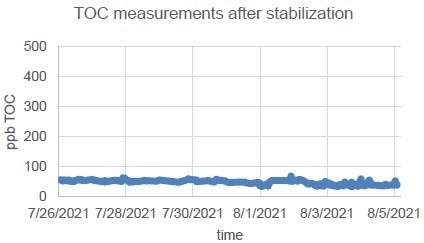
Figure 5. Measuring results. Image Credit: Veolia Water Technologies & Solutions
The trial lasted for seven weeks. In that period, neither the fast-loop filtration nor the Sievers M9 TOC analyzer needed any maintenance. No considerable decrease in the filtrate flux was identified due to the filtration's self-cleaning function, despite the significant quantities of particles in the sample (Figure 1).
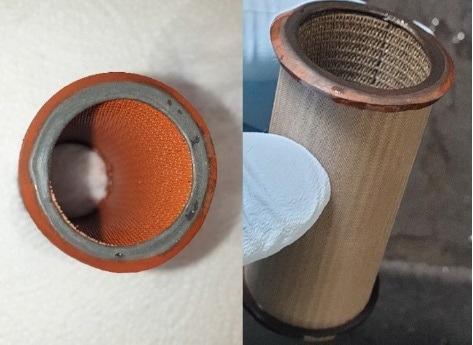
Figure 6. Filter element after 7 weeks trial (left) and after regeneration (right). Image Credit: Veolia Water Technologies & Solutions
The filter element is made of stainless-steel mesh, it is, therefore, possible to restore the filter element after the trial by brushing and treatment with 0.1 M HCl (Fig. 6).
Conclusion
The Sievers M9 Online TOC Analyzer offered precise and consistent data to monitor condensate return on a low level ranging from 30–60 ppb TOC. Contrary to the UV sensor, minimal maintenance, increased sensitivity, and high uptime was enabled by upstream filtration paired with TOC analysis. Proposed maintenance is a rinse of the whole system with 0.1 M HCl at defined intervals (every 1–3 months).
Utilizing a fast-loop filter provided a robust, simple, and low maintenance sample preparation. Despite the significant particle load, the filtrate performance remained significantly over the 50 mL/minutes flow necessitated by the analyzer. This was due to the cleaning effect of the filter specified by the manufacturer.
The 5-µm pore size was found to sufficiently protect the analyzer from clogging. In conclusion, the Sievers M9, in connection with the prototype employed for sample filtration, proved to be a reliable measuring device for monitoring the organic impurities in the condensate return even for the complex sample at the Mars GmbH facility.
The Sievers M9 TOC Analyzer and the filtration ran without issue or maintenance throughout the trial period. They provided the company with more reliable and precise measurements to keep its equipment running smoothly.
References
- Water-tube boilers and auxiliary installations - Part 12: Requirements for boiler feedwater and boiler water quality; German version EN 12952-12:2003.
- Shell boilers - Part 10: Requirements for boiler feedwater and boiler water quality; German version EN 12953-10:2003.
- Abschnitt 2 TRD 604 Blatt 2 – Zusätzliche Anforderungen an die Ausrüstung der Dampfkesselanlage (Außer Kraft am 1. Januar 2013 durch die Bek. vom 17. Oktober 2012 (GMBl S. 902)).
- Water-tube boilers and auxiliary installations - Part 7: Requirements for equipment for the boiler; German version EN 12952-7:2012.
- Shell boilers - Part 6: Requirements for equipment for the boiler; German version EN 12953-6:011.
- "ASTM E2656 - 16 Standard Practice for Real-time Release Testing of Pharmaceutical Water for the Total Organic Carbon Attribute". www.astm.org.
- Standard Methods for the examination of water and wastewater, 23rd edition, 2017, 5310 Total Organic Carbon (TOC).
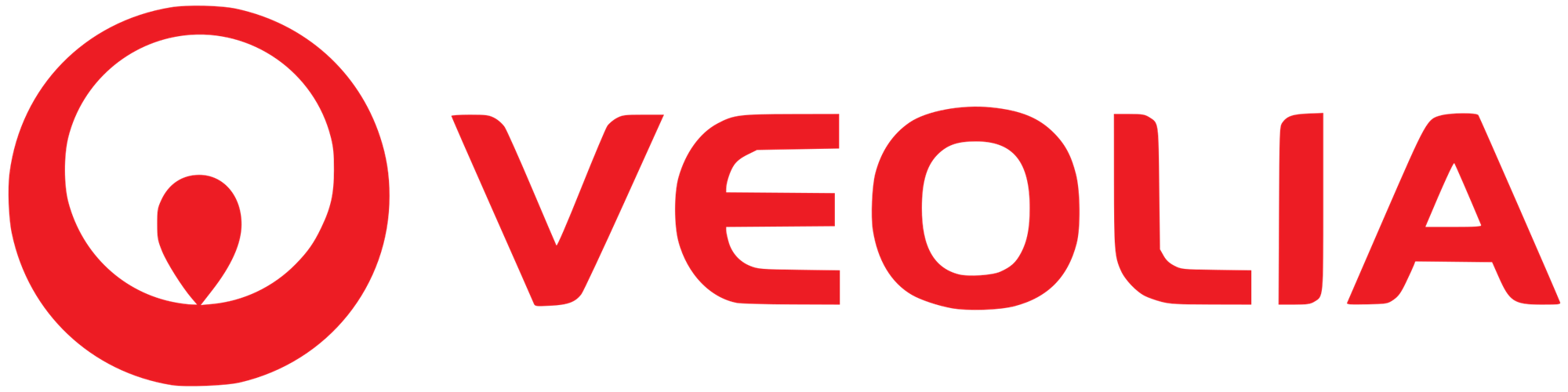
This information has been sourced, reviewed, and adapted from materials provided by Veolia Water Technologies & Solutions.
For more information on this source, please visit Veolia Water Technologies & Solutions, Sievers Instruments.