With the advent of highly automated semiconductor wafer production facilities, there is a pressing trend to broaden the scope of standard automation to incorporate improved decision capabilities with Combinatorial Optimization, Machine Intelligence, and Systems Analysis. This article discusses automation trends in semiconductor manufacturing, relevant challenges and prospects, as well as the latest research taking place in this particular field.
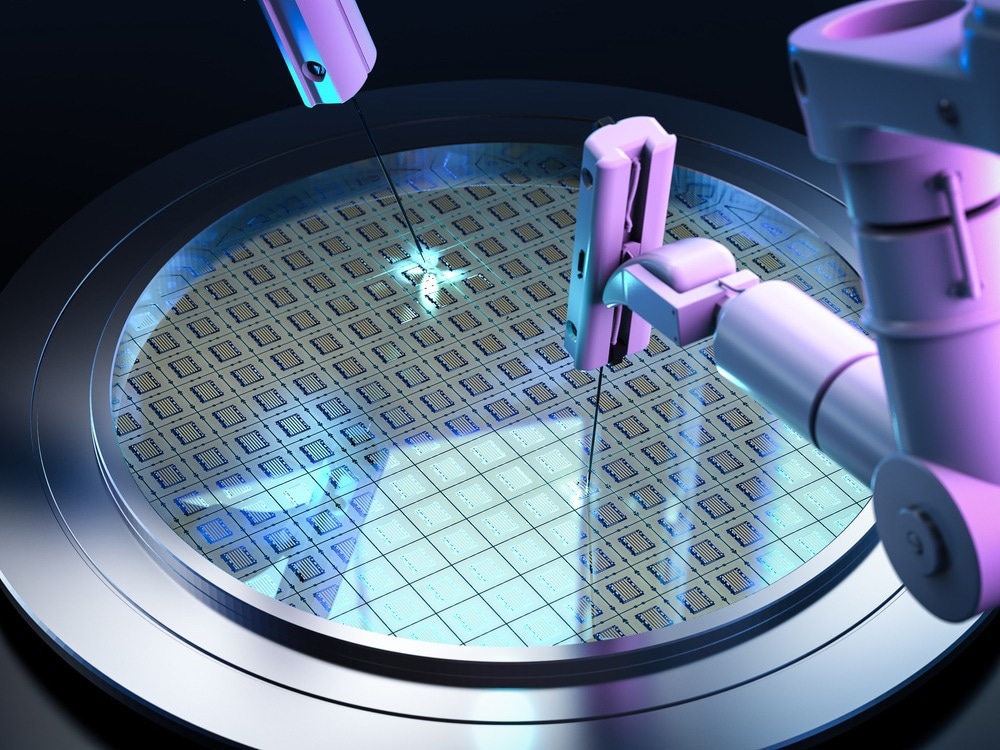
Image Credit: Phonlamai Photo/Shutterstock.com
"Industry 4.0" signifies the fourth industrial revolution, which will be propelled by industrial automation with minimal human interaction. To implement digitalization techniques of Industry 4.0, semiconductor production equipment uses advanced instruments and capabilities such as the Internet of Things, Data Science, AI, augmented reality (AR), etc.
3D Printing and Semiconductor Manufacturing
Designers are constrained while employing traditional semiconductor fabrication techniques, especially in terms of connection layout, polarizability, and substrate form. In contrast, 3D printed circuit boards are saving semiconductor industries a considerable amount of effort, time, and cost while also allowing designers more autonomy to develop semiconductor chips with refined layouts and tailored design concepts as required.
Time Sensitive Networking (TSN) in Semiconductor Manufacturing
To assist firms in delivering products and growth, providers of semiconductor industrial automation equipment should provide cutting-edge innovation that leverages Time-Sensitive Networking (TSN). As the key enabler for a sector that necessitates assured data dependability, consistency, and superior efficiency, TSN is essential for assisting semiconductor firms in futureproofing their workflows, performance goals, profitability, efficiency, and reliability.
Fabs, semiconductor manufacturing plants, as well as other sector-specific assembly plants, have a proven record of attempting to push the performance boundaries of automation and intelligent fabrication. They are coming closer and closer to developing highly customizable, independent, and adaptive networks with each technological advancement.
Impactful track and trace frameworks are required to manage the resource movement and commodities throughout production lines as well as the complete supply chain. To achieve this, it is critical to establish a network that can support higher enterprise-level systems for strong traceability throughout the full assembly line and even beyond, in addition to predictable performance and features. This is where TSN proves to be essential for the future of semiconductor manufacturing.
Automated Visual Fault Inspection in Semiconductor Manufacturing
As per the latest research in the Journal of Intelligent Manufacturing, by utilizing the capabilities of computers and AI vision systems, automated visual inspection attempts to enhance the identification and recognition of semiconductor production faults, allowing producers to profit from greater yields and lower costs of production. The establishment and incorporation of technologies for recording and analyzing production outcomes are required for automated visual defect inspection procedures.
The team presented a unique hybrid multiple-stage approach of layered deep neural networks that enabled the localization of the smallest components within a pixel size using a traditional computer vision workflow and deeper neural networks for categorization. The suggested system shifted the emphasis away from its architecture and onto more task-relevant areas of interest.
According to the findings of the developed testing environment, the multiple-stage approach outperformed current ways of learning-based computerized visual examination. The approach achieved a performance (F1-score) of up to 99.5 percent, which corresponds to an 8.6-fold boost in the system's fault detections.
The Use of AI in Backend Semiconductor Manufacturing
Researchers presented a paper at the 2022 IEEE International Conference on Distributed Computing and Electrical Circuits and Electronics (ICDCECE) suggesting an AI solution involving the use of merged chronological data input from the ERP, MES, and Testscape frameworks to form an integrated data acquisition, planning, and advanced analytic system. This would employ the knowledge to train a model of machine learning such as Deep Learning Neural Networks to forecast processing times, resource utilization, and performance objectives.
Another goal of the suggested approach was to employ AI to overcome product quality issues caused by gaps in existing test and physical condition monitoring abilities and procedures.
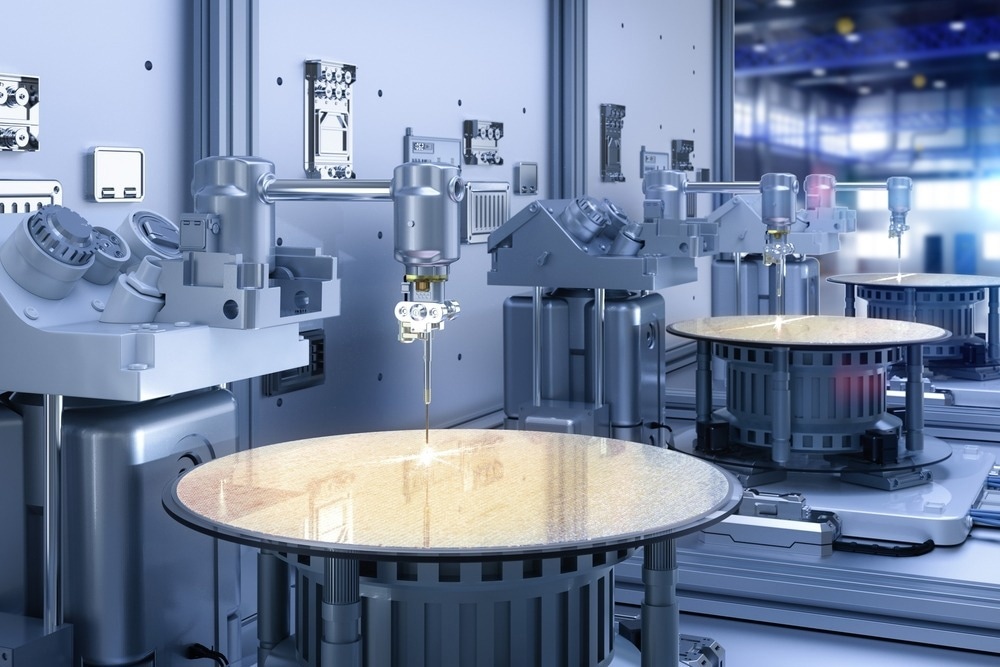
Image Credit: Phonlamai Photo/Shutterstock.com
With this remedy, operators no longer have to decide whether to substitute a device replacement product or keep using it based on their judgment, but can instead delegate this hard choice to an AI system that learns from previous historical information and can make a reliable judgment based on actual data rather than suppositions.
Challenges in Semiconductor Automation
The semiconductor sector is well-known for employing cutting-edge fabrication methods. The worldwide semiconductor chip shortage in 2021 demonstrated how the industry's anticipated skills fell short of realizing the full promise of digitalization and efficient automation.
One of the most significant issues that semiconductor facilities confront is their reliance on traditional manual processes, such as antiquated and usually undocumented MES Programs. These are known as MULEs, which stand for Mature Undocumented Legacy Execution systems. When it comes to the capacity to interact with corporate and IoT applications, MULEs are particularly tricky. They are also infamous for requiring many hours of programming to make minor changes to operations such as workflow. Such applications are thus untenable in the long run.
The traditional mindset of considering automation as a shop or operational floor-level strategy is a major hurdle in semiconductor digitalization. A highly automated process must be initiated with a thorough analysis of the fabrication process far beyond the initial step of materials processing, incorporating all variables of semiconductor manufacturing including the processes being executed, people involved, and products being manufactured.
Prospects of Semiconductor Automated Manufacturing
The future of nanoelectronics production control is all about conquering obstacles. As 300-millimeter technologies have matured, the latest software platforms and characteristics have arisen. These technologies will improve the gathering, preservation, transmission, and transport of data. Recent issues have included increasing system noise as opposed to a shift in the mean.
In model-based furnace regulation, smart thermostats ramping up and down reduces cycle time, and focusing on start-up and shutdown characteristics may benefit equipment. In the future, model-predictive controllers will supersede real-time control algorithms such as PID and use more sensor outputs.
In summary, to fulfill industrial needs, automation and convergence in semiconductor production must continue to grow.
More from AZoM: The Trends Shaping Semiconductor Wafer Manufacturing
References and Further Reading
Ultra Librarian, 2022. Driving Factors For Semiconductor Industry Growth in 2022. [Online]
Available at: https://www.ultralibrarian.com/2022/05/18/driving-factors-for-semiconductor-industry-growth-in-2022-ulc
Cheng, F. T. et. al. (2022). Special Issue on Automation Analytics Beyond Industry 4.0: From Hybrid Strategy to Zero-Defect Manufacturing. IEEE Transactions on Automation Science and Engineering, 19(3), 1472-1476.
Jonathan Karmaou, 2021. What does full automation mean for Semiconductor Manufacturing? [Online]
Available at: https://www.criticalmanufacturing.com/blog/what-does-full-automation-mean-for-semiconductor-manufacturing/
Taj, Md Nasim Afroj. (2022). "Prospects of Automation in Semiconductor Fabrication Process."
Schlosser, Tobias, et al. (2022). "Improving automated visual fault inspection for semiconductor manufacturing using a hybrid multistage system of deep neural networks." Journal of Intelligent Manufacturing. 33(4). 1099-1123.
Pheng, M. S. K., & David, L. G. (2022, April). Artificial Intelligence in Back-End Semiconductor Manufacturing: A Case Study. In 2022 IEEE International Conference on Distributed Computing and Electrical Circuits and Electronics (ICDCECE) (pp. 1-4). IEEE.
Disclaimer: The views expressed here are those of the author expressed in their private capacity and do not necessarily represent the views of AZoM.com Limited T/A AZoNetwork the owner and operator of this website. This disclaimer forms part of the Terms and conditions of use of this website.