The world is in the middle of a major global revolution. This transformation will impact people’s lives, societies, and the surrounding environment. However, for the majority of people, nothing will seem to change.
This transition is known as Industry 4.0, and it represents the fourth revolution of its kind in the manufacturing industry. From the first industrial revolution, which used steam power in mechanization, to the second, which used mass assembly and electricity, to the third, which used computers, it is now time to embrace the most recent technical advancements: machine learning, smart systems, and automation.
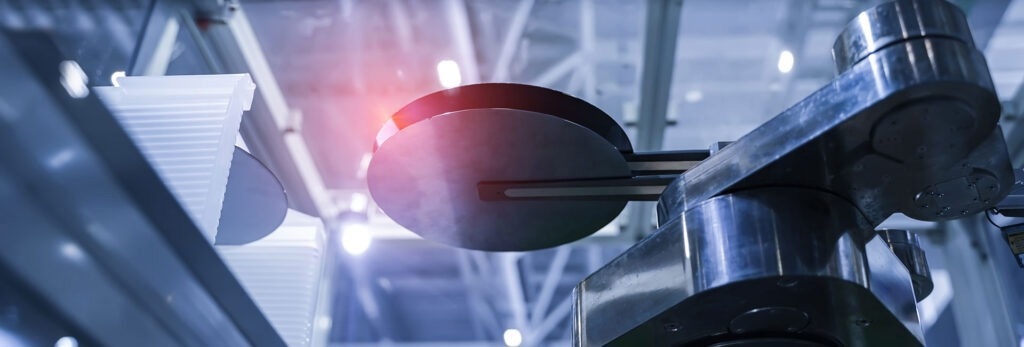
Image Credit: Malvern Panalytical
This revolution has not surprised the semiconductor industry. This is because industry 4.0 is based on innovations that have been building under the surface of semiconductor manufacturing for a significant time.
Many companies in the compound semiconductor sector have already developed into fully matured production companies generating billions in revenue on par with their silicon counterparts.
The innovative nature of the industry means that many smaller companies working on their innovations are still in the process of evolving from research-led operations to start-ups to scale-ups to significant manufacturing firms. Larger companies are adopting SEMI standards at a consistently increasing pace.
The switch from a research-led operation to a production operation might, naturally, appear to be a daunting challenge.
Fabs, for example, have different performance criteria for their equipment than labs. This is mainly due to an increase in the accompanying quality benchmarks that must be met. To avoid limiting the quality and type of semiconductors it produces, it is now essential for any fab to maintain a cleanroom environment following ISO and federal classifications.
Fabs adopting the most recent Semiconductor Equipment and Manufacturing International (SEMI) standards must ensure that their production lines follow ISO cleanroom practices.
Partly as a result of this, automation is becoming more widespread. Automated methods reduce contamination and the need for human involvement, which is a significant advantage for semiconductor production.
With such a vast array of complex and precise processes to perform — particularly in the crucial phase of wafer analysis — it has been essential for research and manufacturing facilities to embrace automation. However, until now, automation has been limited by technical capabilities and the need for human intervention in operating and controlling automated tools.
High-Tech Solutions to Heighten the Analysis
With MRD XL Automation, all that is about to change. With cutting-edge automation functionality, this software allows the X’Pert3 MRD XL instrument to carry out wafer analysis independently, without human input. This makes it a true semiconductor metrology tool since it enables a quicker and more efficient research and production process from wafer selection to analysis all the way to results distribution.
The removal of hands-on human intervention means that wafers are also much less likely to be contaminated than they would be with manual intervention techniques. This automation functionality is beneficial in ensuring a cleaner research or production environment because humans are the primary source of contamination in wafer analysis.
The MRD XL Automation framework’s design enables Malvern's experts to adapt the software configuration to meet each customer's individual needs. This means that customers can modify the software solution to meet their current demands, change the recipes, and adapt their procedures whenever needed.
This extra feature in an already modular instrument makes MRD XL the ideal package for companies that need their tools to grow alongside their operation; or even solutions that can help them to make the essential scale-up from lab to fab.
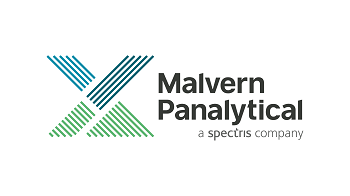
This information has been sourced, reviewed and adapted from materials provided by Malvern Panalytical.
For more information on this source, please visit Malvern Panalytical.