There is a high chance that specific shapes and mechanical properties are required when sourcing an alloy product for an industrial, medical, or consumer application. This is where cold working processes come in.
Cold work involves any metalworking process where the alloy is plastically deformed below its recrystallization temperature. Each alloy has a distinct recrystallization temperature, but for the purposes of this article, it is usually found at the halfway mark of the metal’s melting point.
From coining and roll forming to stamping, a successful cold working project results in a material with a high degree of dimensional and mechanical precision, as well as exceptional reproducibility and interchangeability.
When subject to deformation, several metals become harder due to activity at the atomic level. Work hardening occurs when metal is subjected to certain levels of stress and the atoms in its grains dislodge and “lock”. When this happens repeatedly, the metal becomes more resistant to further deformation as many of its atoms have locked into place. Therefore, the introduction of work, or energy, strengthens the material.
Occasionally, work hardening is accidental and undesired. However, it is typically the result of intentional activity, as strong materials are ideal in many scenarios. Consequently, cold working processes are frequently used throughout aerospace and automobile manufacturing and several other industries.
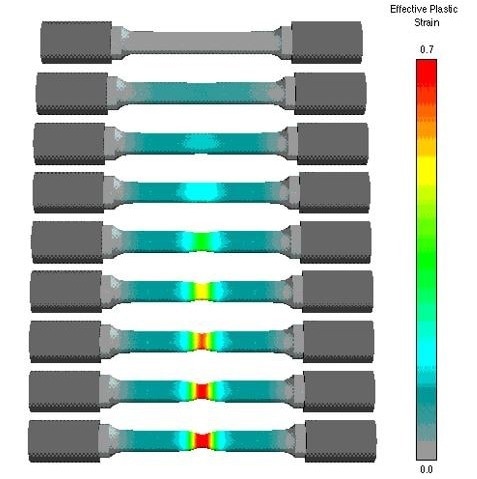
Image Credit: Ulbrich Stainless Steels & Special Metals, Inc.
Hot Work Versus Cold Work
The major difference between hot and cold work is the temperature. However, there are various other essential ways these two metal-forming processes are distinguished.
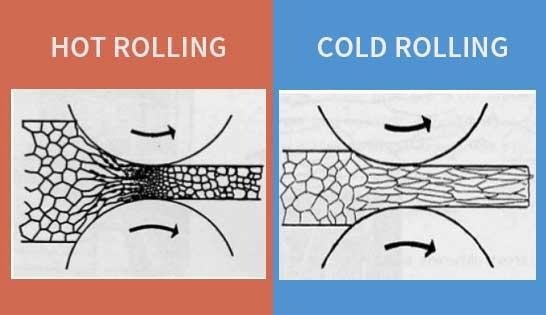
Image Credit: Ulbrich Stainless Steels & Special Metals, Inc.
Recrystallization and the Metal Forming Process
Recrystallization is a critical phenomenon in metallurgy. It takes place when metal atoms are stimulated to a point at which new crystals begin to form. Similar to the way water changes phases to steam and ice, metal also has its own phase changes. Every metal has a distinct recrystallization point.
The technical definitions of both hot and cold work point to the metal’s recrystallization temperature. Hot working is when metal is deformed above its recrystallization temperature. Conversely, cold working is when metal is deformed below the recrystallization temperature. Warm forming, a third metal forming process, sits between the two.
When to Use Hot Versus Cold Work
Hot work has various requirements and results compared to cold work. These differences are crucial to consider when choosing a metal-forming process. Stainless steel that has been subjected to hot working, for example, will have high ductility and show no strain hardening or residual stress. However, hot working demands significant amounts of heat energy, which usually means a short lifespan for metallurgical tools and equipment. This indirectly raises costs.
While heating is not required for a cold working process, it also comes at its own cost. To cold work stainless steel, higher forces are needed to deform the metal. This compromise results in smoother metal surfaces and more control over mechanical properties.
Types of Cold Working Processes
As with heat treating, each of the cold working processes has a set of specific pros and cons. Manufacturers choose between the various options by evaluating the metal’s future use.
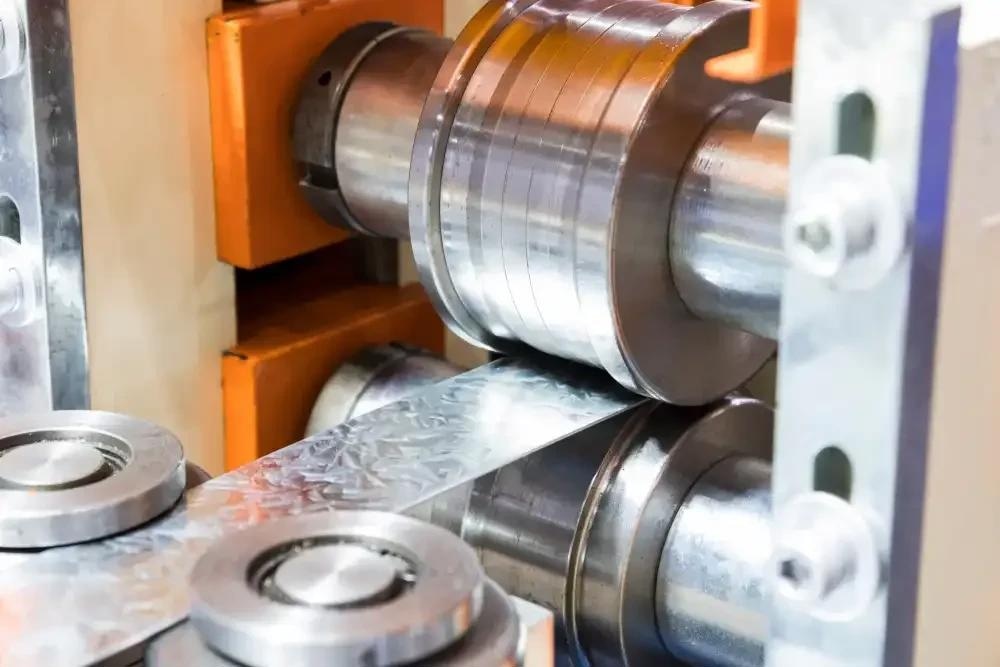
Image Credit: Ulbrich Stainless Steels & Special Metals, Inc.
Methods and Examples of Cold Working Metal
The different processes are indicative of the variety of use cases for metal. Each cold working method yields metals with specific characteristics.
The four main types of cold working processes are:
- Squeezing
- Bending
- Shearing
- Drawing
Precision stamping is a complex process that brings together several of these coldworking methods.
Squeezing
Rolling, cold forging, coining, and extrusions are all considered coldworking methods that are thought of as squeezing.
Cold rolling, one of Ulbrich’s main capabilities, is the most common cold working method. Sheet, strip, and more can be cold rolled to produce products with smooth surfaces and distinct material properties.
Cold-rolled steel is subjected to severe stress. Its resulting strength is due to strain hardening, rendering the metal up to 20 percent harder than it was prior to the applied stresses.
In cold forging, metal is positioned between two dies, which are then struck repeatedly. The metal then takes on the shape of the dies.
In extrusion, the metal is forcibly passed through a die, which works it into a given cross-section.
Bending
Bending methods are generally applied to shape alloy products.
During the roll forming process, a long strip of metal (usually coiled steel) is bent after being passed through sets of rolls, each contributing to an incremental part of the bend. The product is bent until the desired cross-section profile is reached.
Tube, roll, and angle bending are other frequently used methods.
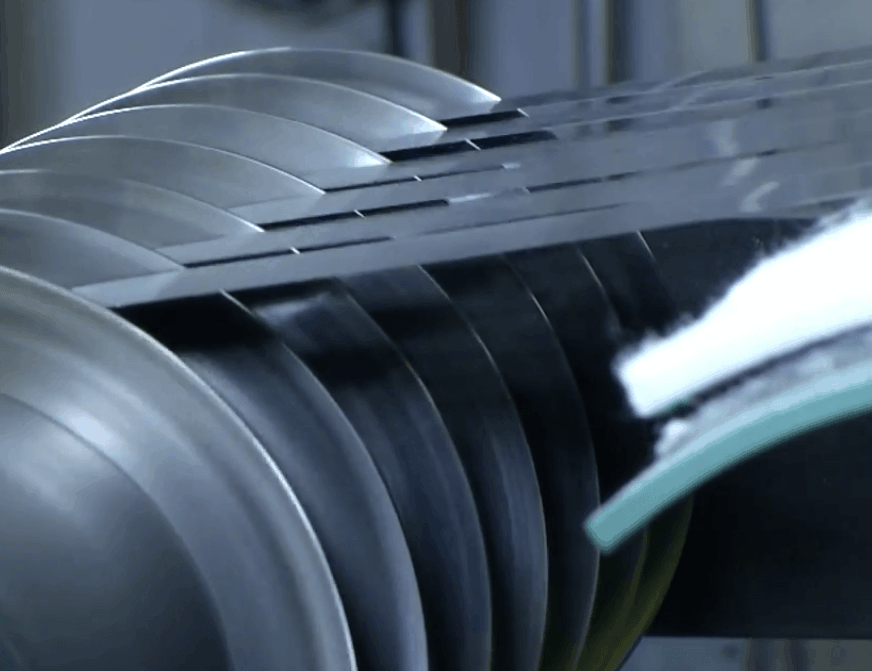
Image Credit: Ulbrich Stainless Steels & Special Metals, Inc.
Shearing
Slitting sheet into strips is considered the most frequently applied shearing method of cold working.
Steel slitting cuts a wide master coil of metal into narrower strands that feature more consistent measurements. Manufacturers simply feed the large stainless steel through a slitter machine, then recoil the resulting strands into a finished coil. However, the machine’s knives leave a burr on the slit edge.
Drawing
Metalworkers use cold drawing to draw, or pull, metal to extend the material without cracking it.
A rolled coil is punched through a hole or die when deep drawing metal, and the punch helps achieve the desired shape.
The die cavity matches the punch but is slightly wider, enabling passage and clearance. The compression force pushes the raw material into the die. Each draw operation is a separate step. There is a reduction in diameter during each step, increasing the height or depth of the part. This ensures that re-crystallization occurs as the metal changes shape. Products developed via deep drawing include battery enclosures, implantable medical devices, aerospace solutions, and aircraft defense components.
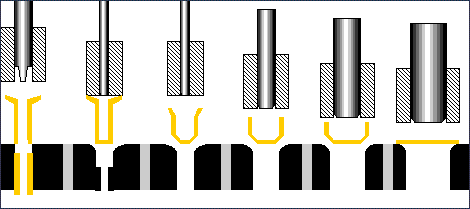
Image Credit: Ulbrich Stainless Steels & Special Metals, Inc.
Precision Stamping
Metal stamping is an ideal manufacturing process for developing metal products where tight tolerances are needed.
A flat metal strip coil is converted into various shapes in metal stamping. This complex process involves several metal forming techniques, such as punching, coining, piercing, blanking, and bending, among others.
Applications and Benefits of Cold Working
Cold work provides many benefits that ensure that demand for cold working processes remains high, even though they require a great deal of force.
Applications of Cold Working
Cold work has many applications, including:
- Vehicles such as automobiles, aircraft, and ships have many cold-worked components
- Medical devices and applications, including pacemaker stamping and hypodermic needle manufacturing.
- Blind rivets, gaskets, and shielding.
- Many other complex shapes can be produced via cold working
Benefits of Cold Working
Cold working is an effective way to strengthen metals.
Hot-rolled steel is cold-rolled to ensure it has the required mechanical properties, including increased tensile strength. Hot rolling and cold rolling are the most used metallurgical processes.
As well as improving the strength of metal, cold rolling also produces a smoother surface. Cold-rolled steel can be ten times smoother than hot-rolled in terms of the roughness height (a measure of surface irregularities). This makes cold working an optimal choice for fabricating the metal surfaces found in consumer goods.
Cold working is an economically efficient option as it does not generate metal waste (scrap metal). On the other hand, hot working requires soaking pits and furnaces, which are not needed in cold working.
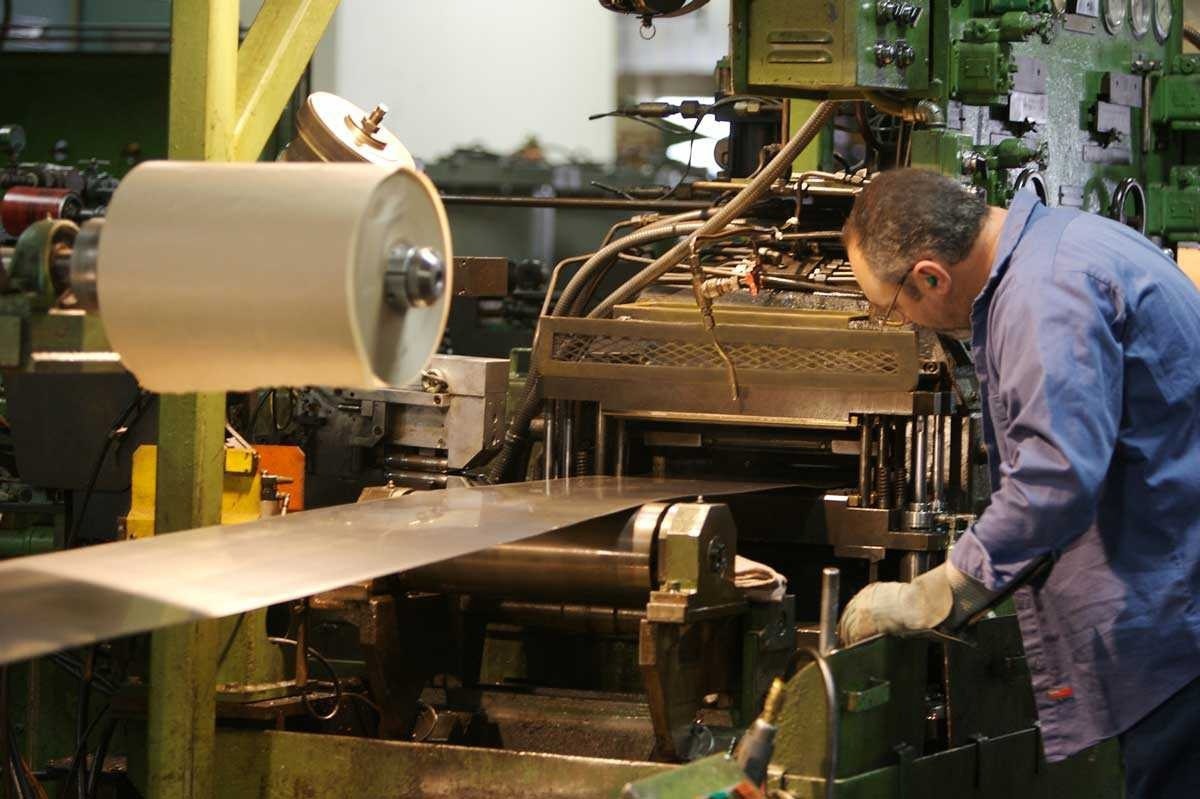
Image Credit: Ulbrich Stainless Steels & Special Metals, Inc.
Materials That Can and Cannot Be Cold Worked
As with several other industrial processes, cold working is only applicable for a particular range of metals. In addition to being restricted for use on certain types of metals, it is also limited to particular sizes of metal. Those kinds and sizes that fall out of this remit are better suited for hot forging.
Materials That Can Be Cold Worked
Cold work can be performed on a wide range of metals. These include tool steels such as stainless steel, cobalt, copper, and aluminum alloys, nickel-based alloys, and some titanium grades.
Materials That Cannot Be Cold Worked
Cold working is not suitable for larger pieces of metal because the force required to cold work a larger metal would be immense. Generally speaking, cold working cannot be performed on anything with a diameter over 25 millimeters. Larger pieces may require hardening via other methods.
It is simply not possible to cold work some types of metals. These include alloy steels that are not ductile at room temperature, carbon steel, and titanium grade 5. Some metals that can be cold worked, such as copper, may also become brittle after cold working.
Learn More About Cold Working Processes
Due to the various cold working methods available, it is crucial to select the right process for each use case.
The appropriate kind of cold work can lead to the production of a stronger, smoother, and more effective metal. Get in touch today for additional information about the cold work processes offered by Ulbrich.
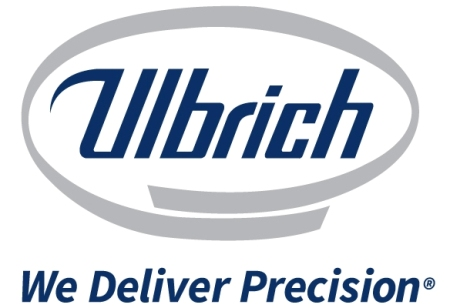
This information has been sourced, reviewed and adapted from materials provided by Ulbrich Stainless Steels & Special Metals, Inc.
For more information on this source, please visit Ulbrich Stainless Steels & Special Metals, Inc.