Ultrathin carbon is a strong electrical and thermal conductor, making it ideal for enhancing semiconductor chips in electrical devices.
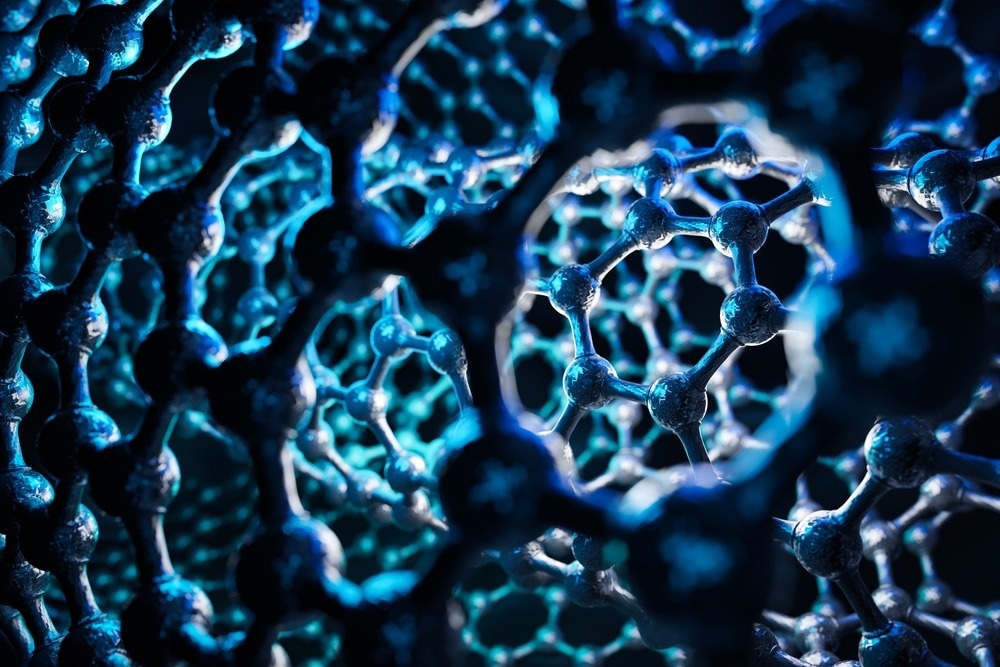
Image Credit: Forance/Shutterstock.com
What are Flexible Electronics?
The history of flexible electronics is extensive. Over half a century ago, single crystalline silicon solar cells were thinned to increase their power/weight ratio to make them suitable for extra-terrestrial satellites. These cells were able to be flexible and coiled. Flexible electronics typically include a substrate, active layer, and interface layer.
Many features can be considered flexible, including bendability, conformal formation, elasticity, light weight, non-breakability, and being roll-to-roll manufacturable.
Flexible Electronics Applications
This field continues to expand with further developments and vast applications. Today's industrial community often associates flexible electronics with X-ray sensor arrays and flexible screens. According to researchers, it refers to ergonomically designed displays, sensors, electronic clothing, and skin.
Wearable electronics utilize the extreme flexibility and conformability of flexible electronics and are anticipated to play a significant role in personalized treatment as they closely and continually track a person's physical activity and health status.
Lightweight and flexible hybrid electronics (FHE) are favorable for applications such as automotive sensors, wearable sensors, flexible displays, and smart packaging radio-frequency identification. These applications typically involve heterogeneous integration of a large number of chips with different functionalities and require fan-out wafer/panel technology.
Limitations of Materials used in Flexible Electronics
Indium Tin Oxide (ITO)
ITO has long been a crucial component in optoelectronic devices such as liquid crystal displays (LCDs), touch screens, OLEDs, and OSCs due to its high electrical conductivity and high T for visible light. ITO production involves high-temperature annealing (> 300 °C) since metal ion substitution into ITO demands a lot of energy. However, low-thermal resistant plastic substrates are unsuitable for high-temperature annealing.
Copper (Cu)
Cu electrochemical deposition is used for wiring on High-Density Redistribution Layers (RDLs). However, as the density of Cu wires on the RDL rises, electromigration of Cu due to high current densities becomes a severe concern. Therefore, a solution to reinforce the Cu wires on the RDL while keeping good conductivity is also needed.
Why Graphene?
Flexible nanoelectronics' rapid technological development has increased the demand for high-performance materials with sophisticated structural designs and excellent characteristics. As a result, two-dimensional (2D) materials with atomic-scale thicknesses are gaining popularity in this field.
Outstanding thermal conductivity, charge mobility, and mechanical strength are all characteristics of graphene. In addition, graphene's unique features make it suitable for surface passivation, antennas, sensors, and transparent conductive films.
Furthermore, when placed on Cu wires, graphene improves reliability and conductivity. Therefore, the graphene coating of Cu wires on the RDL will solve the Cu-electromigration concerns. It also improves the surface appearance of the electroplated Cu.
Graphene Synthesis
Several graphene synthesis techniques have been developed, each with pros and cons.
Mechanical Exfoliation
The mechanical exfoliation method is straightforward and can produce SLG without defects. However, it only makes a modest quantity of tiny graphene flakes. Therefore, this technology cannot be used to manufacture graphene films for flexible electronics in a realistic manner.
Chemical synthesis
Large-area graphene can be produced in bulk by chemical synthesis. In this process, graphite is first oxidized, and the resulting graphene oxide (GO) is subsequently reduced to make graphene sheets.
Chemical Vapour deposition (CVD)
Large-area high-quality graphene films can be created using CVD. Catalytic transition metals, including Ni, Cu, and Pt, are used in CVD. Graphene CVD growth can be divided into two mechanisms: Surface expansion by carbon solubility in metal catalysts, carbon segregation, and precipitation.
Recent Studies
In a recent study published in the journal ACS Applied Materials & Interfaces, researchers used the direct low-temperature Plasma-Enhanced Chemical Vapor Deposition (PECVD) technique for graphene deposition on electroplated copper.
The substrate consisted of layers of polyimide, silicon nitride, sputtered Ti adhesion layer sputtered Cu seed layer, and an electroplated Cu layer. A PECVD graphene growth chamber, filled with hydrogen (H2) and methane (CH4), was used where a solid-state microwave generator generated plasma. The sample was cleaned thoroughly before putting it into the plasma chamber.
Raman spectroscopy results indicated successful deposition of graphene onto electroplated Cu regardless of H2 and CH4 flow rates. However, the H2/CH4 ratio does affect the grain size and quality of graphene. A higher ratio leads to larger grain size and better durability.
The results showed that graphene-covered samples could maintain electrical conduction (as indicated by measurable resistance values) up to 100,000 folding cycles, while the uncoated reference sample broke down after 60,000 cycles.
In a recent study, researchers created a flexible and transparent conductive electrode (FTCE) by spray coating Ag nanowires (AGNWs) and graphene oxide (GO) nanosheets. The GO nanosheets acted as a connecting bridge between AgNWs, improved the electrode's surface morphology and roughness, and improved electrode conductivity with minimal optical and mechanical degradation.
Flexible thin film heater (TFH) and electroluminescent (EL) devices on AgNWs/GO hybrid FTCEs performed better due to lower sheet resistance and uniform conductivity than AgNWs alone. In addition, the hybrid also presented anti-bacterial properties.
In another study published in the Journal of Collide and Interface Science, researchers created a high-concentration screen printing conductive ink using carbon black and graphene powders produced by jet cavitation together as conductive fillers.
This ink's preparation and application processes are straightforward, effective, and affordable because it does not require a solvent exchange, high temperatures, long-term lower temperatures, or photonic annealing, making it suitable for various substrates and applicable on roll-to-roll manufacturing.
The conductivity of printed patterns increased initially before decreasing, peaking at 15 % when the black carbon content of the conductive ink rose from 0 to 20 % of the total conductive infill. The elasticity of conductive ink also increased.
More from AZoM: How are Graphene Batteries Made?
References and Further Reading
Lu, Chen-Hsuan, C.M. Leu, and N. C. Yeh. Polymer-Compatible Low-Temperature Plasma-Enhanced Chemical Vapor Deposition of Graphene on Electroplated Cu for Flexible Hybrid Electronics. ACS Applied Materials & Interfaces 2021 13 (34), 41323-41329. http://doi.org/10.1021/acsami.1c11510
Hyeong-Min Sim & Han-Ki Kim (2021). Highly flexible Ag nanowire network covered by a graphene oxide nanosheet for high-performance flexible electronics and anti-bacterial applications. Journal of Science and Technology of Advanced Materials, 22:1, 794-807. http://doi.org/10.1080/14686996.2021.1963640
Lixin Liu, Z. Shen, X. Zhang, H. Ma (2021). Highly conductive graphene/carbon black screen printing inks for flexible electronics. Journal of Colloid and Interface Science, 582, 12-21. https://doi.org/10.1016/j.jcis.2020.07.106
Disclaimer: The views expressed here are those of the author expressed in their private capacity and do not necessarily represent the views of AZoM.com Limited T/A AZoNetwork the owner and operator of this website. This disclaimer forms part of the Terms and conditions of use of this website.