Natural gas pipeline operators manage a range of gas analyzers while ensuring the necessary reliability, system integrity, and performance to meet critical requirements in custody transfer and process control applications.
Today’s analyzers that try to meet these challenges often generate sub-optimal measurement and instrument reliability, false readings (especially during process upsets), and tedious, time-consuming maintenance in remote locations due to the application of legacy technologies (such as lead acetate tape, electrochemical, UV analyzers, traditional tunable diode lasers, and chilled mirror-based analyzers). In this interview, AZoM speaks with ABB Global Product Manager Stefan Parmentier about the new Sensi+™, a laser-based analyzer to monitor multiple contaminants in natural gas streams.
Could you please introduce yourself and your role?
My name is Stefan Parmentier, and I am Global Product Manager at ABB.
ABB helps pipeline companies ensure a safe and reliable natural gas transmission network, which is of critical importance. This is because natural gas contaminants such as H2S, H2O and CO2 constitute a significant hazard to an operator’s business as they represent both a safety (H2S) and pipeline integrity risk due to corrosion. Corrosion left undetected can further cascade into pipeline failures.
Mitigating the risk of natural gas contaminants can often be frustrating, as companies are typically required to manage numerous technologies and devices to analyze the different contaminants independently.
This legacy approach is complex, failure-prone, and expensive, as each contaminant requires its own analyzer, maintenance schedule, and specific skill set to operate and validate. ABB’s highly sophisticated OA-ICOS™ laser technology solves the multitasking problem with the capacity to analyze up to three contaminants accurately and reliably in a single device in any natural gas stream in real-time. In effect, ABB’s Sensi+ replaces the legacy solution implemented to date by the industry.
What does the Sensi+ solution offer ABB’s customers?
The compact Sensi+ natural gas contaminant analyzer can measure up to three gas contaminants, including H2S, H2O, CO2, simultaneously and continuously to reduce capital equipment expenditures (CAPEX) and operational expenses (OPEX).
The system is relatively compact, which leads to significant space savings. Sensi+ can automatically measure in any natural gas stream without field or factory calibration.
The low sample flow rate of the Sensi+ can enable an emission-free measurement of natural gas by installing a catalytic converter that oxidizes the sample vent.
ABB’s highly innovative and proven OA-ICOSTM laser technology ensures unsurpassed measurement precision and accuracy in all process conditions while providing the highest analyzer reliability and uptime and the lowest cost of ownership.
Moreover, ABB Sensi+ and the market-leading natural gas chromatograph NGC8200 series becomes the first complete gas quality solution that combines gas composition, calorific value and contaminant measurements with a comprehensive, compact, and economical measurement system.
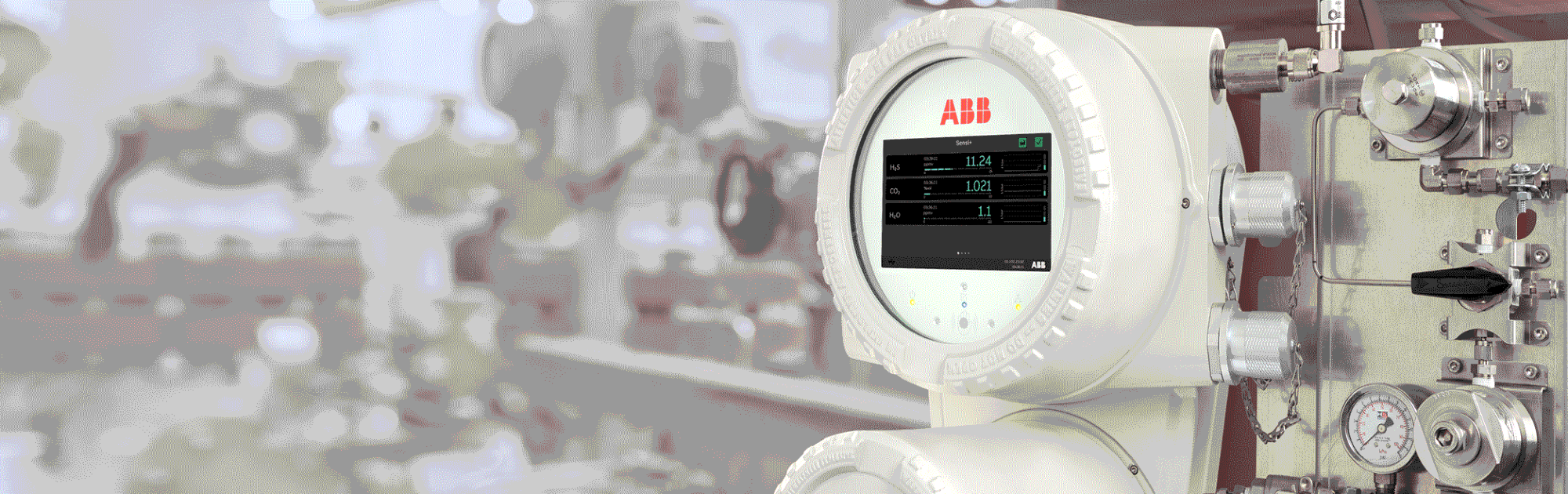
Image Credit: ABB Inc.
How easy is the Sensi+ to operate?
The modular design, modern user interface, and comprehensive system health metrics make it easy to use and troubleshoot remotely to reduce expensive, time-consuming site visits.
This step change in analyzer design, coupled with the built-in hardware redundancy features and remote diagnostics, can significantly reduce unnecessary downtime and costly onsite intervention.
Intuitive HMI supports Wi-Fi connectivity and requires no proprietary software. The Modern user interface design gives users confidence that the system operates reliably and allows fast, easy service while delivering continuous, detailed digital health metrics in real-time.
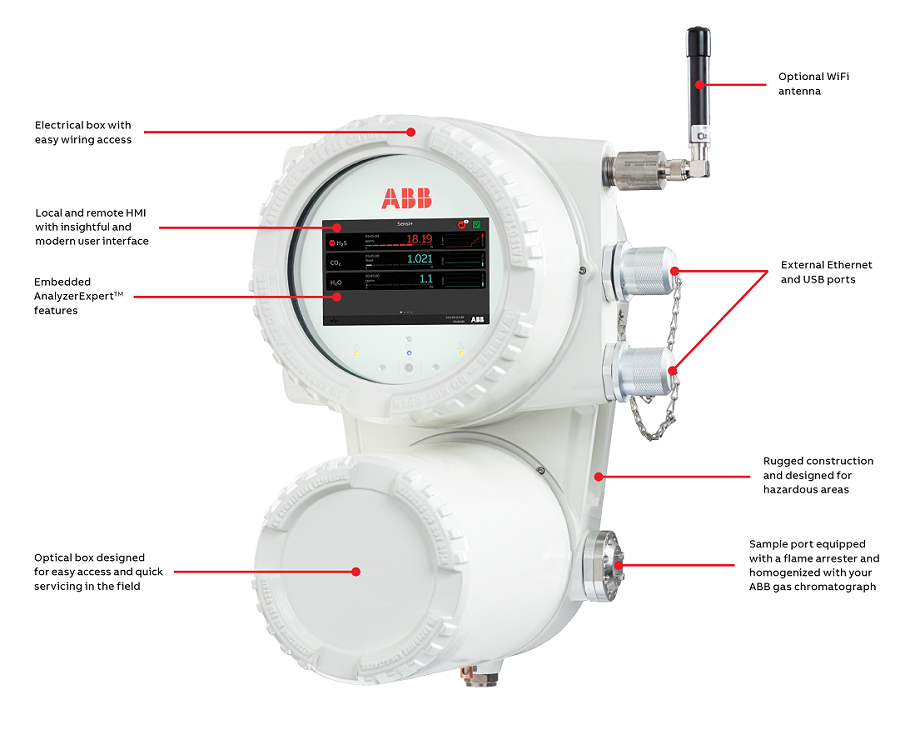
Image Credit: ABB Inc.
Why is it important to measure contaminants in natural gas?
Excessive concentrations of the target gases lead to internal corrosion within the natural gas infrastructure, notably in gas pipelines, storage facilities, and other mission-critical assets.
As a result, requirements in custody transfer mandate measurements of these target gases routinely. Industrial production processes cannot tolerate excessive concentrations, so proper gas quality monitoring and control are required to meet operational objectives and production yield.
H2S, CO2, and H2O naturally occur in oil and gas reservoirs and can react to form corrosive compounds like acids that corrode steel pipelines. Additionally, H2S is dangerous gas that raises safety concerns, excessive CO2 levels reduce the gas heating value, and phase changes in water due to temperature and pressure variations can accelerate internal pipe corrosion.
Therefore, measuring H2S, CO2, and H2O concentration is required at processing plants and natural gas custody transfer points to ensure the levels are low enough to meet quality specifications for pipeline transportation.
What are the advantages of using Sensi+ over conventional gas analyzer systems?
Sensi+ is based on OA-ICOS which is a unique TDLAS method. It is a cavity enhanced technique making it extremely sensitive while also being robust making it reliable, portable, field deployable, and field serviceable. The relatively simple optical configuration makes it possible to combine lasers and the sensitivity enables differentiation of gases so that multiple contaminants can be measured simultaneously. Whereas conventional measurements systems employ a specific gas analyzer for each contaminant gas.
Sensi+ is fast. Not only does it have a fast update time, like all TDL technologies, but OA-ICOS also has a fast time response because the long path length can be achieved in a physically small gas cell with a small volume. While gas chromatographs are ideally suited for gas composition and colorific value, due to long cycle times, they are not able to track the rapid changes necessary for monitoring contaminant gases.
Sensi+ is reliable. The opto-mechanical configuration is simple with minimal components. The off-axis design allows for straightforward alignment routines and lowers the sensitivity of the instrument to vibration and thermal stresses that could lead to misalignment. Therefore, the maintenance requirements are much lower. Conventional analyzers based on lead acetate tape can be useful, but they have high maintenance requirements and can suffer from reliability issues. Sensi+ is accurate. For over 15 years, ABB’s OA-ICOS laser absorption technology has been used around the world for applications requiring the highest overall performance in the most demanding conditions. This proven technology has been updated with customized electronics and recent advances in spectroscopic analysis algorithms to yield accurate measurements over varying conditions. Analyzers that employ broadband UV light sources and narrow bandpass filters are prone to interference from changing background gas concentrations. The lamp lifetimes are relatively short, increasing the effective total annual cost of ownership. Sensi+ is robust and up to the challenge as ABB analyzers employ near-infrared diode lasers that provide many years of reliable continuous operation over all environmental conditions. Conventional tunable diode laser-based methods often rely on chemical scrubbing methods and a priori knowledge of the stream to operate and do not offer comparable speed, sensitivity, selectivity, or accuracy or the variety of measured contaminant gases in a single enclosure when compared to the Sensi+.
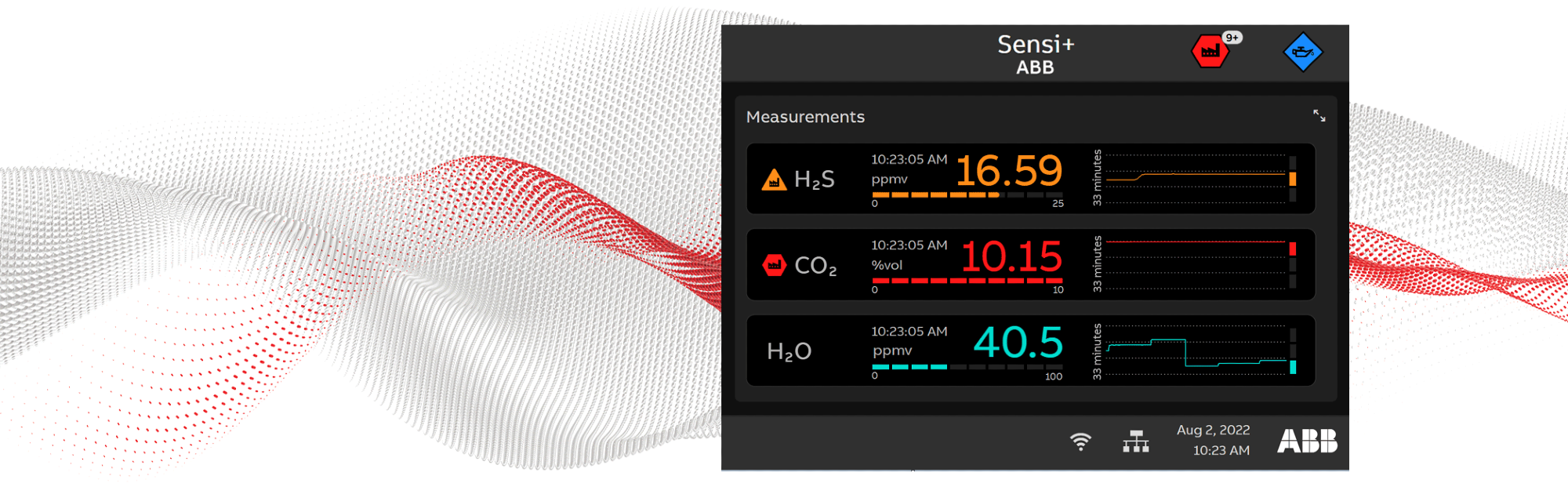
Image Credit: ABB Inc
How does ABB and a product like Sensi+ meet the market’s demands while demonstrating innovation?
For over 15 years, ABB’s OA-ICOS laser absorption technology has been at the core of the world’s most reliable gas analyzers for applications requiring the highest overall performance.
We employ proven laser-based technology combined with recent advances in spectroscopic analyses that provides the highest accuracy, precision, sensitivity, and reliability.
In Sensi+, this technology has now been updated with customized electronics suitable for hazardous area installation and photonics, along with advances in spectroscopic analysis algorithms to yield accurate measurements in complex and time-varying natural gas flows with minimal cross interferences without any requirements for chemical scrubbers.
Rapid flow time response allows operators to react and redirect pipeline gas containing abnormally high contaminants.
The analyzer recovers quickly after exposure to flows with elevated concentrations of contaminants. No other technology offers reliable measurements of contaminants at very low and high concentrations to allow consistent measurements of treated, sweet gas, and raw gas flows.
About Stefan Parmentier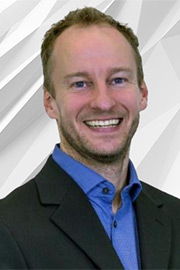
Stefan Parmentier has a Bachelor's degree and a Master's degree in Engineering. He has worked at designing high-tech products in various advanced fields (such as optoelectronics & lasers, implantable biomedical devices, instruments for non-destructive testing (NDT) industry) by prioritizing the fine understanding of customer needs and their alignment with the company's business model.
Over the past 6 years, he has held various management positions, including overseas management experience in a fast growing business environment. He now currently works as the Global Product Manager for Industrial ICOS at ABB Inc.
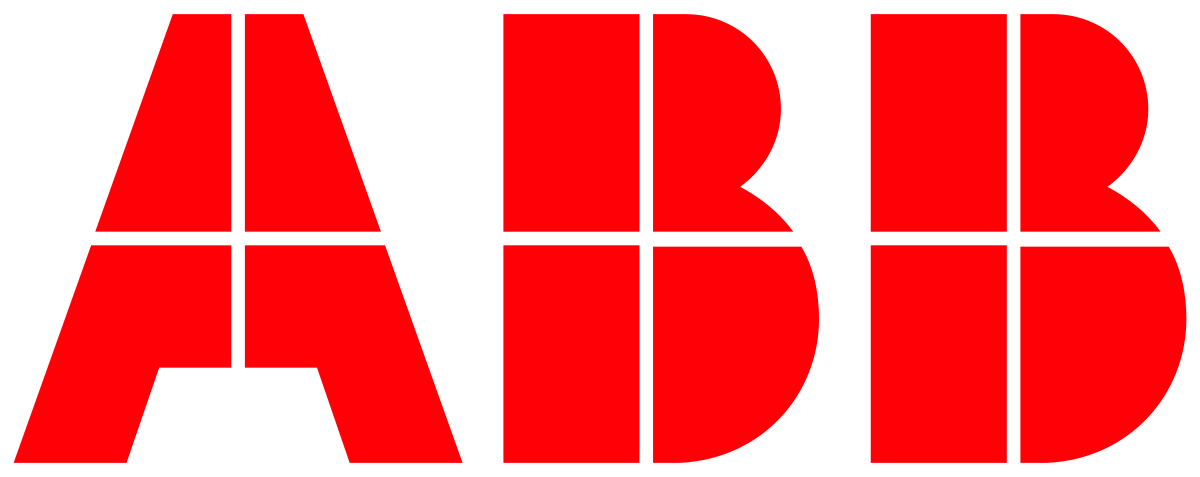
This information has been sourced, reviewed and adapted from materials provided by ABB Measurement & Analytics - Analytical Measurement Products.
For more information on this source, please visit ABB Measurement & Analytics.
Disclaimer: The views expressed here are those of the interviewee and do not necessarily represent the views of AZoM.com Limited (T/A) AZoNetwork, the owner and operator of this website. This disclaimer forms part of the Terms and Conditions of use of this website.