Coatings are required to remove or diminish the electrical charges that promptly accumulate in a nonconducting material when examined by a high-energy electron beam. Material samples investigated at ideal conditions without a coating layer inevitably display charging effects, resulting in picture aberration as well as thermo-radiative degradation, which can result in considerable material removal from the specimen.
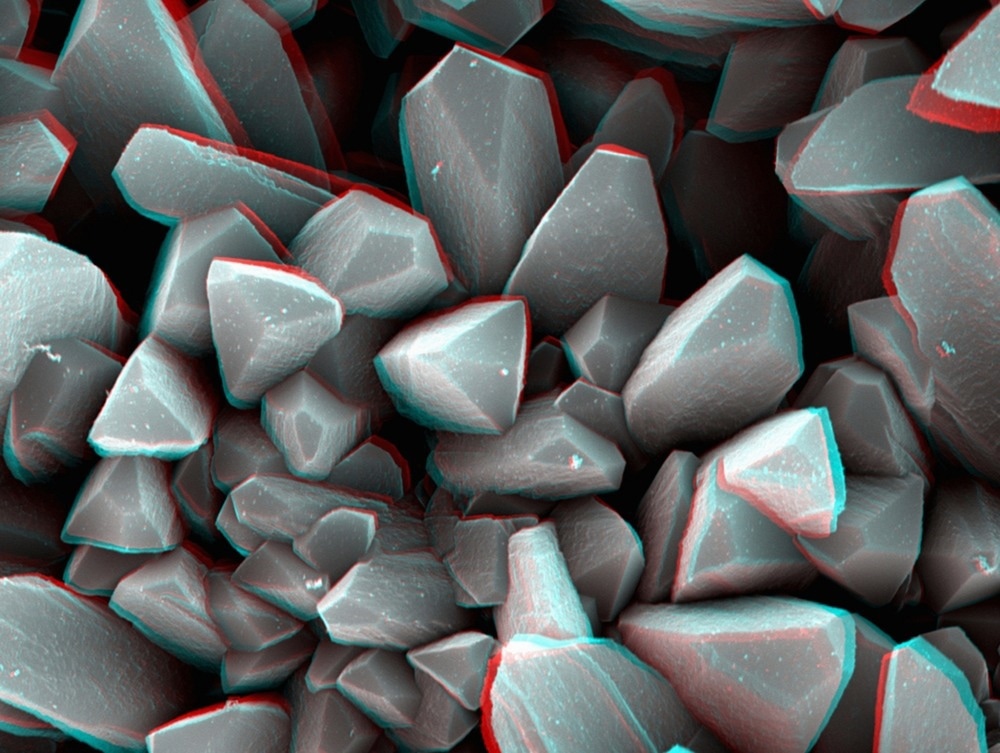
Image Credit: Image Source Trading Ltd/Shutterstock.com
The development of the scanning electron microscope (SEM) in the late 1930s substantially increased the capacity to observe surface morphologies, causing a revolution in the fields of biological studies and materials sciences. Almost all non-conductive materials studied under the scanning electron microscope require a thin coating of conductive materials to be deposited.
The Importance of Carbon Coating
Carbon films and coatings are widely recognized for their application in electron microscopy due to their minimal imaging interference and reasonably strong electrical properties. Thin films, usually 5 nm or 50 Angstroms, are used in TEM, but SEM may utilize thicker films of about 50 nm for activities such as X-ray microanalysis. Carbon coatings have numerous benefits.
Carbon coatings for scanning electron microscopic processes are amorphous and extremely beneficial in preventing charging mechanisms that cause material surface deterioration. They also aid in the highly efficient imaging of biological material. This suggests that carbon coatings are especially useful for preparing non-conductive specimens for energy-dispersive x-ray spectroscopy (EDS).
Thermal Evaporation Methods for Carbon Coating
Thermal evaporation of carbon is a common way to prepare samples for electron microscopy. When carbon is heated in a vacuum using a suitable technique, the vapour pressure exceeds 1.3 Pa, and it evaporates quickly into a monoatomic state. These coatings can be achieved using two comparable methodologies: carbon fibre or a carbon rod technique.
Two carbon rods with a pointed contact area are utilized during the rod coating procedure. This is often referred to as the Brandley approach. The procedure involves the flow of current between the two rods, causing substantial current densities at the sharpened point of contact, resulting in extremely high degrees of heat generation. This causes carbon to evaporate off of the surface. This may be accomplished with either a ramping or a pulsating current. When the pressure of roughly 10 mPa is attained, the reinforcement wiring and, if necessary, the carbon rods can be warmed to a dark red colour.
This first outgassing is especially crucial for carbon rods because it eliminates any chemical binders employed in their production. When the outgassing is finished, the current is reduced and the pumping is resumed. The samples are spun and inclined to ensure equal treatment on all sides. Following carbon deposition, the vacuum pressure is reduced to between 1.0 mPa and 100 µPa. It's better to continually raise the power till the ends of the carbon rods start to glow, then the applied current is lowered.
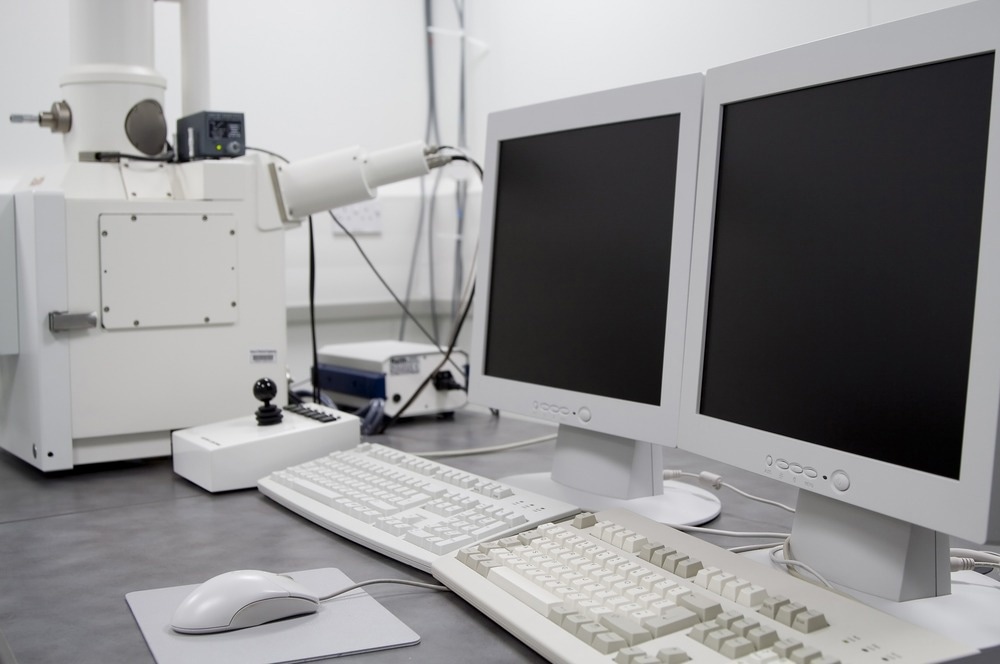
Image Credit: WH CHOW/Shutterstock.com
In the case of the fibre method, carbon fibre is clamped between two clips and a periodic voltage is transmitted. As a result, the carbon on the fibre's exterior evaporates. Both procedures have distinct quality discrepancies. By adjusting the amount of pulsating frequencies and the pulse duration, the carbon fibre technology allows for more control over coating thickness. As a result, it is suitable for TEM grid applications as well as analytical SEM techniques such as EDS and electron backscatter diffraction (EBSD). Carbon rod finishes are "cleaner" and more durable. Carbon rod coatings produced under vacuum conditions with ramping voltage provide the finest quality coverings.
Coating thickness gauges indicate the thickness that has been attained. These have, however, been challenging to utilize with carbon to continuously and precisely regulate layer thickness, particularly with a constant evaporation voltage.
Low Vacuum Evaporation Coating Method
This process involves the evaporation of carbon in an argon environment at a pressure of around 1 Pa. Carbon atoms collide many times and spread in all dimensions. This approach is excellent for making robust carbon coatings and covering extensively sculptured materials before analyzing them with x-rays and backscattered electrons. However, its broad applicability for SEM specimens is dubious, especially given the limited output of secondaries from carbon. There is no doubt that the carbon's simultaneous dispersion and substrate transmission allow it to coat difficult samples more successfully, and as such, it would be a good approach to utilize.
Can Carbon be Sputter Coated onto a Specimen?
Sputtering occurs when an energetic ion or neutral atom impacts the exterior of a substrate and transmits velocity to the atoms over a few nanometers. Some of the atoms are ejected as a consequence of the interaction because they get sufficient power to break their connections with their neighbours. They are transported away from the surface if the velocity given to them is significant. The electrons accelerate toward the positive anode due to the presence of an applied voltage. The positively charged ions are subsequently propelled toward the negatively biased target, causing sputtering. Carbon may be sputtered-coated; however, the resultant films have high hydrogen proportions, making carbon sputtering undesirable for SEM operations. Gold sputtering has been extensively utilized for specimen preparation.
Thin Film Method for Carbon Coating
Glow discharge methods can be used to create carbon films. At reduced pressure and in an anaerobic atmosphere, an expelled container is filled up with hydrocarbon vapour such as acetylene or benzene. A glow discharge is produced, which enables the hydrocarbon vapour to polymerize and form a darkish carbon coating. However, this approach is far too erratic to be useful in SEM.
Comparison of Carbon Coating with its Counterparts
Etheresia Pretorius published an article in the journal Microscopy Research and Technique comparing the results of images obtained by gold, ruthenium vapour, and carbon coating techniques for biological material. RuO4, gold sputter coating, and carbon coating were all executed at 1 kV. Carbon coating took 2 minutes in an EMITECH K950X carbon coater. This resulted in a coat of around 20–30 nM on the substrate.
The main fibres appeared finer in photos acquired from carbon-coated specimens than in samples acquired from RuO4 or gold-coated specimens. In both the carbon and RuO4 samples, the minor fibres looked to be highly comparable. The principal fibres in the carbon-coated specimen seemed smoother, but the major fibres in the gold-coated specimen seemed lumpy. The study concluded that RuO4 and carbon coating are superior coating solutions since the substrate seemed flawless and the nanofibre topology was not affected.
To summarize, carbon coating is usually essential for SEM analysis, although novel techniques such as liquid ion deposition have started to offer an alternative.
More from AZoM - Carbon Coatings: What Are Their Applications and How Are They Characterized?
References and Further Reading
Clutton, L., 2021. Carbon Coatings: What Are Their Applications and How Are They Characterized?. [Online]
Available at: https://www.quorumtech.com/2021/10/05/carbon-coatings-what-are-their-applications-and-how-are-they-characterized/
Electron Microscopy Sciences, n.d. SEM/TEM Carbon Coaters Techniques and Applications. [Online]
Available at: https://www.emsdiasum.com/
Heu, Rod, et al. 2019. Target material selection for sputter coating of SEM samples. Microscopy Today 27(4). 32-36. Available at: https://doi.org/10.1017/S1551929519000610
Pretorius, Etheresia. 2011. Traditional coating techniques in scanning electron microscopy compared to uncoated charge compensator technology: Looking at human blood fibrin networks with the ZEISS ULTRA Plus FEG‐SEM." Microscopy research and technique 74(4). 343-346. Available at: https://doi.org/10.1002/jemt.20914
Goldstein, Joseph I., et al. 1992. Coating and conductivity techniques for SEM and microanalysis. Scanning Electron Microscopy and X-Ray Microanalysis. Springer, Boston, MA. 671-740. Available at: https://doi.org/10.1007/978-1-4613-0491-3_1
Disclaimer: The views expressed here are those of the author expressed in their private capacity and do not necessarily represent the views of AZoM.com Limited T/A AZoNetwork the owner and operator of this website. This disclaimer forms part of the Terms and conditions of use of this website.