AZoM speaks with Dr. Nicola Ferralis from MIT about his research that has developed a low-cost process of creating carbon fibers from hydrocarbon pitch. This research could lead to the large-scale use of carbon fiber composites in industries that have thus far been limited.
Please could you introduce yourself and your professional background?
My name is Nicola Ferralis and I am currently a Research Scientist in the Department of Materials Science and Engineering at MIT, and the Program Manager for the MIT Energy Initiative Low Energy Carbon Center on Energy Storage. A native of Italy, I hold a Bachelor’s and Master’s degree in Physics from the University of Padua and a Ph.D. in Experimental Condensed Matter Physics with distinction from Penn State University, where I was a National Science Foundation Fellow in Graduate Research and Education.
While a post-doctoral fellow at the Center for Integrated Nanomechanical Systems at UC Berkeley, I developed novel techniques to identify function-property relationships in complex carbon-based nanomaterials. I currently lead several research programs on carbon materials design and development in the areas of energy harvesting systems (from photovoltaics to geothermal systems), water filtration and chemical separation, electronic and sensing systems based on natural carbonaceous materials, and continuous additive manufacturing of natural-carbon based products, from fibers to thin films and membranes.
What are carbon fibers and why are their properties so desirable?
Carbon Fibers (CF) are fibers of 5-10 micrometers in diameters mostly made of aromatic carbon domains. CFs have several advantages such as high stiffness, high tensile strength, high strength to weight ratio, high chemical resistance to corrosion, high-temperature resistance and tolerance, and low thermal expansion. All these properties make CFs not only competitive but often superior to metals, since such properties can be achieved at a much lower weight.
It is important to note that fibers alone cannot be used, as they would look like a strand of unbundled hair. Therefore, they are woven into fabrics and impregnated with epoxy to make a composite, which after curing, will result in the final part. The woven process is required not only to give the required structure to the part needed but also to optimize the load distribution.
Furthermore, while fibers have a very high tensile strength and elastic modulus, their compressive counterparts are not as good. This is true both at the composite level as well as the CF level. For simplicity, this is since carbonaceous molecules within the CF are stacked as graphitic sheets (similarly to graphite), so their high tensile strength derives from the very strong carbon bonds within these sheets. However, under compression, the weak interlayer bonding limits the strength of the CF. This is in essence the result of the very anisotropic nature of a CF molecular structure. In a composite, this is largely mitigated through the specific design of the woven fabric.
However, a fiber that can achieve both high strength and modulus requires a fundamental redesign of the molecular structure, and this was one of the goals we achieved in this work: a new type of isotropic fiber with similar elastic tensile and compressive performance.
What limits the use of carbon fibers in vehicle manufacturing?
The major limit in the deployment of carbon fibers in the automotive industry is cost. CFs (regardless of the feedstock used), can run from $10-15/lb and much higher for aerospace applications (most rockets and several new-generation planes use more than 50% of their part made with carbon fiber composites), depending on their properties. For reference, aluminum currently costs $2/lb, and steel is at $0.50/lb). Ideally, carbon fibers would need to be just as cheap: however, cost per pound is not the only metric. Because of the high strength-to-weight ratio compared to metals, you can use fewer CFs to achieve the same performance for heavier metal parts.
If cost were to be on parity with metals, you could deploy CF everywhere in the car where you need structural strength, from the chassis to structural elements (roof, doors), and exterior panels.
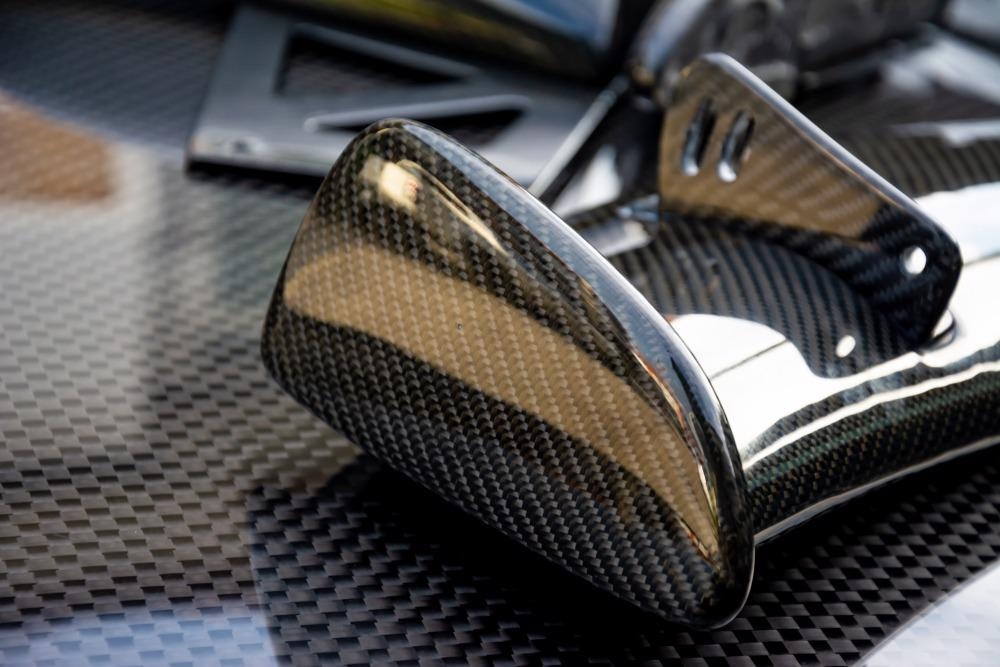
Image Credit: Composite_Carbonman/Shutterstock.com
In principle, you could also make wheel rims, seat frames—anything we use metal parts for now. You could also replace and redesign plastic components to be both structural and serve an aesthetic function. This is not done only for marketing, of course: CF will always be lighter and stronger than metals, with added benefits in terms of high resistance to corrosion, so with less need for specific paints and treatments. The BMW i3, one of the few mass-produced cars with a CF composites frame, has the frame fully exposed and unpainted.
Ultimately, a CF car would be much lighter (some estimates would lead to 30-40%), which could lead to smaller engines, or for EVs smaller and lighter battery packs, leading ultimately to even larger savings. Unfortunately, the cost is still too high (even at $3/lb) for such a massive deployment. However, more extensive use, under this cost bracket, could be foreseen in more significant components than the one we see right now in supercars, such as in parts of the chassis, roof, and heavy system supports (powertrain, suspensions, etc.), where titanium and aluminum are currently used.
Even in this limited deployment, CF can provide significant weight redistribution benefits. For example lightweight components high on the car (roofs) lower the center of gravity, providing better and safer handling.
You have managed to create carbon fibers from cheap feedstock in the form of petroleum refining waste. Could you please describe how you were able to do this?
This work combines sophisticated computational modeling and state-of-the-art carbon fiber fabrication facilities (both at lab-scale and pilot-scale) to develop new and optimized recipes for making carbon fibers from hydrocarbon pitch. The overarching goal of this work is the development of not one, but a framework, of realistic atomistic models and related CF prototypes, which are representative of a broad range of performance properties and structural characteristics of the fibers.
The key in the models is the significant reliance on experimental data not only to validate the models but to allow for a one-to-one relationship between modeling and experimental fibers. Therefore, the choice of molecular compounds in the fiber precursor (pitch) is achieved by selecting molecular size, functionality, and distribution from mass spec data from the actual pitch used in the lab.
At the same time, when the fiber models are tested for elasticity, the obtained values for density and elastic modulus are directly (i.e. with no parametric correction) evaluated against the testing data from the experimental fibers manufactured under the same conditions. With this experimentally driven approach in mind, the models were developed in steps.
Firstly, the pitch precursor molecules are heterogeneous; so, we figured that the shape, size, functional groups, and dispersity of the initial molecules could affect the final properties. Secondly, the manufacturing procedure used results in processing parameters like density, temperatures, oxygen diffusion rate, etc. which can also affect the final properties. These two factors resulted in a large parameter space being available for us to study.
We wanted to design a modeling framework that could predict the fibers accurately enough for experimentalists to use, and so we decided to choose our parameters and design strategy to closely replicate experimental procedures. To account for the heterogeneity of the initial precursor molecules, we used the spectra given to us by our experimental collaborators and designed our initial set of molecules such that they could replicate the spectra. Next, to account for the manufacturing procedure, we did the following:
- To account for the increased alignment resulting from the mesophase conversion and melt-spinning step, we designed two subsystems for each system: one where the molecules (in the box) are placed randomly, thus modeling the isotropic pitch, and the other where the molecules were aligned along a given direction, resulting in modeling the mesophase pitch.
- Since the point of both stabilization and carbonization was establishing crosslinks between neighboring molecules, we simulated that by activating the sites for crosslinking by initially removing a certain fraction of hydrogen atoms in the initial hydrocarbons.
- Finally, just like the experimental graphitization step, we also subjected the (simulated) fibers we obtained after the carbonization step to a high temperature for a given period of time and tabulated the subsequent elastic modulus.
Crucially, several of the proposed CF models were used to produce equally performing fibers in the lab, validating the performance targets as well as compatibility with existing fabrication facilities and methods. Furthermore, it led to the development of a new type of high-density carbon fiber with high tensile AND compressive modulus. This is novel in that most CF have high tensile performance but poor compressive performance, so future adoption will lead to deployment on load-bearing applications.
How do the properties of these new waste-based carbon fibers compare to conventionally produced fibers?
From a purely performance point of view, pitch-based fibers can be made to perform just as well as regular polymer-based fibers (which use polyacrylonitrile-PAN as polymer precursor). However, the main draw for pitch-CF is the potential cost savings. In PAN-based CF, the major cost is from the precursor itself, and the transition to pitch can, according to our estimates, reduce that cost of the feedstock by 2-3 times.
That is the advantage of using a “waste” feedstock, rather than a highly engineered polymer. Pitch-based CFs are currently mainly deployed in the top-end of the market (aerospace), not only for their mechanical properties but for their thermal properties, as they have very high thermal conductivity.
Petroleum pitch as a byproduct is not combustible and is often landfilled. How will utilizing this waste for carbon fiber production help to make multiple industries greener?
The current availability of pitch as a byproduct of coking or pet refining should not be the defining factor for pitch. The production of coke is designed to maximize coke yield, but simply because it is considered more valuable. One could potentially redesign the pitch extraction process (which relies on a sequence of heating steps) to maximize pitch yield, something that can be done, for example, using renewable energy.
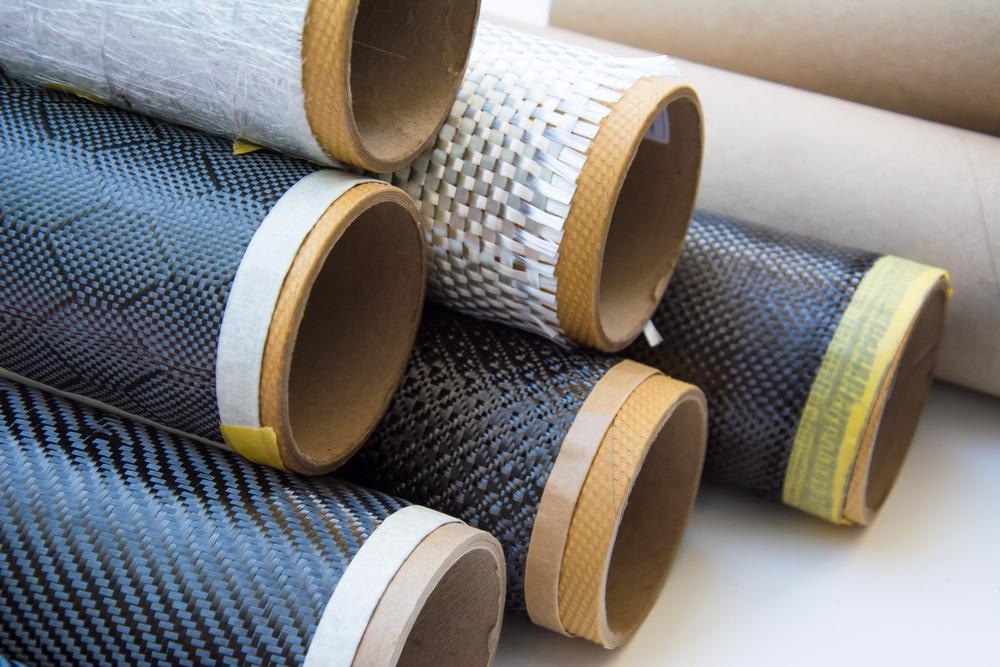
Image Credit: Composite_Carbonman/Shutterstock.com
In essence, the broad availability of pitch shouldn’t be linked to the fact that it is produced from the process used for producing combusting products. It should be considered, as we do for many other mined elements (from lithium to cobalt, for example), as a resource that could be used directly, rather than because of other processes.
Once again, the massive availability and low cost, combined with smart and sustainable mining practices, can allow the full utilization of pitch-based CF in a carbon zero deployment. The benefits could be substantial, not just in the replacement of other materials (like steel, which does require similar high temperature and carbon-intensive processes), but also for lighter, more efficient vehicles.
As an example, the transition from a Boeing 767 or Airbus A330 (made of metal alloys) to a Boeing 787 or an Airbus A350 (where CF composites make up to 50% of the planes), allowed for the latter to be much more efficient, running for much longer with a similar amount of fuel, and with significantly improved rigidity across the different operating conditions. For example, the transition from metal alloys to low thermal expansion carbon composites allows such planes to have a simulated air pressure in the cabin equivalent to ~6000 ft altitude, compared to the usual ~8000 ft, leading to better travel comfort and higher oxygen levels.
Furthermore, these planes feature much larger windows, owing to the fact that the stronger structure compensates for larger openings on the fuselage. These advances are a direct result of the CF intrinsic properties; one could envision similar and novel design advances when applied to cars as well. Of course, aviation is less affected by costs, allowing the plane to be fully commercially competitive even at a high cost of CF. However, it highlights how, if the cost would drop to ~$3/lb, similar gains could be achieved with cars as well.
Usually, carbon fibers used in vehicle manufacturing are very expensive. How can low-cost composite materials like that produced in this study revolutionize the automotive industry?
As stated above, the major cost saving comes from the very much reduced cost of pitch compared to PAN. As we highlighted in our publicly available report for the US Department of Energy (who sponsored this work), which is available here [1], we can facilitate the achievement of industrial production of carbon fibers at less than $5/lb, in fact, below $3/lb with optimization of the process.
With such optimization to achieve consistency in performance and materials properties, fibers can potentially be deployed directly. However, when using the high-density isotropic route we identified in this work as an alternative to the conventional carbonization/graphitization routes, further gains can be achieved in load-bearing applications (or optimized to achieve that by reducing the overall amount needed).
Furthermore, fibers are embedded in a composite using woven fiber arrangements. Isotropic (tensile and compressive) performance allows us, at least to some extent, to translate the intrinsically strong tensile performance of the single fiber into sufficient compressive performance by the way the fibers are arranged and the composite is designed. That said, a fiber that can intrinsically perform well under compression allows for the simplification of the fabrication process.
More Interviews on AZoM: Promoting Sustainability in the Lab
What other applications beyond vehicle manufacturing could these carbon fibers be used for?
One potential application is in structural elements in buildings. Currently, CF cannot be used in, say, rebars, as they do not have sufficient compressive performance. That may change with the isotropic pitch fibers. And of course, the knowledge acquired in this work on pitch processing allows for its use in the fabrication of highly engineered carbon materials, such as films (for electronics [2, 3]) as well as for nano-filtration and nano-separation membranes.
Does the material have any limitations yet to be overcome?
At this stage, the CFs here produced have high promise both in their performance and possible industrial feasibility, but more work is needed to develop the synthetic process from a lab scale into a full-fledged, large-scale fabrication reality. While it may sound trivial, for any material to scale from a few grams to tons may require a complete redesign of the industrial processes needed. Furthermore, a composite is more than just fiber, so more research is needed to maximize the number of CFs in the composite while reducing the amount of epoxy binding them together.
In your opinion, what is the most exciting aspect of this research to you?
As a materials scientist, the ability to directly connect an atomistic model to a very real material made in production is key, as it allows for prediction on how to optimize the fabrication process. Practically, though, what I am most excited about is the prospect, now backed by this work and the analysis we performed for the US Dept. of Energy, that CFs at a highly competitive cost can be made.
So, the ever-recurring hope that CFs would become mainstream may finally become reality in the next few years. Furthermore, this may happen while not relying on highly engineered materials and polymers, but on petroleum and coal byproducts. The sustainability argument in using byproducts (and often waste) in designing highly technological materials is what I would consider the highest goal.
What are the next steps? Will you continue to develop novel green materials, and carbon fibers in particular?
The main goal for us is to further develop our CF design process beyond fibers and into carbon composites. For example, how can the properties and their variability be optimized and upscaled into a woven composite? Another aspect we are working on is the optimization of the chemistry of pitch to enable the mitigation of the most energy-intensive steps of the fabrication, namely high-temperature carbonization.
This, in addition to novel processes to control density, not only may enable the achievement of high-performance CFs at even lower cost and higher sustainability but may further augment the CF space by providing CFs that have comparable tensile and compressive performance. In the longer term, we are applying this modeling framework to characterize not only the mechanical performance of fibers (or pitch-based carbon systems, such as films and membranes) but also their thermal and electrical properties.
The ability to broadly tune how electrons and heat travel across the CFs may enable the CFs to do more than just provide structural support, but also enhance heat transfer (or provide insulation), or act as an electrode or an electrical insulator.
More Interviews on AZoM: How Can Valve Diagnostics Reduce Emissions in the Chemical Industry?
Where can readers find more information?
The research article in Science Advances is publicly available here:
https://www.science.org/doi/epdf/10.1126/sciadv.abn1905
References
[1] Consortium for Production of Affordable Carbon Fibers in the United States (Final Report), https://www.osti.gov/biblio/1829480
[2] Laser engineered heavy hydrocarbons: Old materials with new opportunities: https://www.science.org/doi/10.1126/sciadv.aaz5231
[3] Upgrading carbonaceous materials: coal, tar, pitch and beyond. https://www.cell.com/matter/pdf/S2590-2385(21)00615-9.pdf
About Nicola Ferralis
Nicola Ferralis is currently a Research Scientist in the Department of Materials Science and Engineering at MIT and the Program Manager for the MIT Energy Initiative Low Energy Carbon Center on Energy Storage. A native of Italy, he holds a Bachelor’s and Master’s degree in Physics from the University of Padua and a Ph.D. in Experimental Condensed Matter Physics with distinction from Penn State University, where he was a National Science Foundation Fellow in Graduate Research and Education. While a post-doctoral fellow at the Center for Integrated Nanomechanical Systems at UC Berkeley, he developed novel techniques to identify function-property relationships in complex carbon-based nanomaterials.
As the Chief Scientist for Experimental Research in the industry-sponsored X-Shale MIT-Schlumberger-Shell program, he led the design of novel characterization methods for rapid assessment of hydrocarbon productivity in unconventional reservoirs and oil/gas production. He is currently leading several research programs on materials design and development in the areas of energy harvesting systems (from photovoltaics to geothermal systems), water filtration, electronic and sensing systems based on natural carbonaceous materials; development of machine learning algorithms for ultrafast, edge-based, low-power detection and characterization of use solid carbon species in space exploration and hydrocarbon recovery; continuous additive manufacturing of natural-carbon based products, from fibers to thin films. Most recently he is the leading PI of a Department of Energy-sponsored project aimed at using density functional theory to construct hydrocarbon precursor models to train machine learning algorithms with predictive capabilities of the chemomechanical properties of the precursors needed for the synthesis of pitch-based and PAN-based carbon fibers. Fully integrated atomistic to mesoscale modeling with coarse-graining molecular dynamic simulations and reactive force fields are used in this project to reproduce each phase of the synthesis of carbon fibers, with the aim of predictive structure-functional relationships between processing conditions, materials used, and the final mechanical response.
Disclaimer: The views expressed here are those of the interviewee and do not necessarily represent the views of AZoM.com Limited (T/A) AZoNetwork, the owner and operator of this website. This disclaimer forms part of the Terms and Conditions of use of this website.