Additive manufacturing (AM) or 3D printing is frequently used for manufacturing products layer by layer with fewer emissions. However, all materials are not suitable for additive manufacturing. Adaptive3D has successfully developed a range of unique elastomeric resins specialized for 3D printing. Their novel elastomer range promotes cutting-edge and innovative additive manufacturing technologies following Industry 4.0 standards.
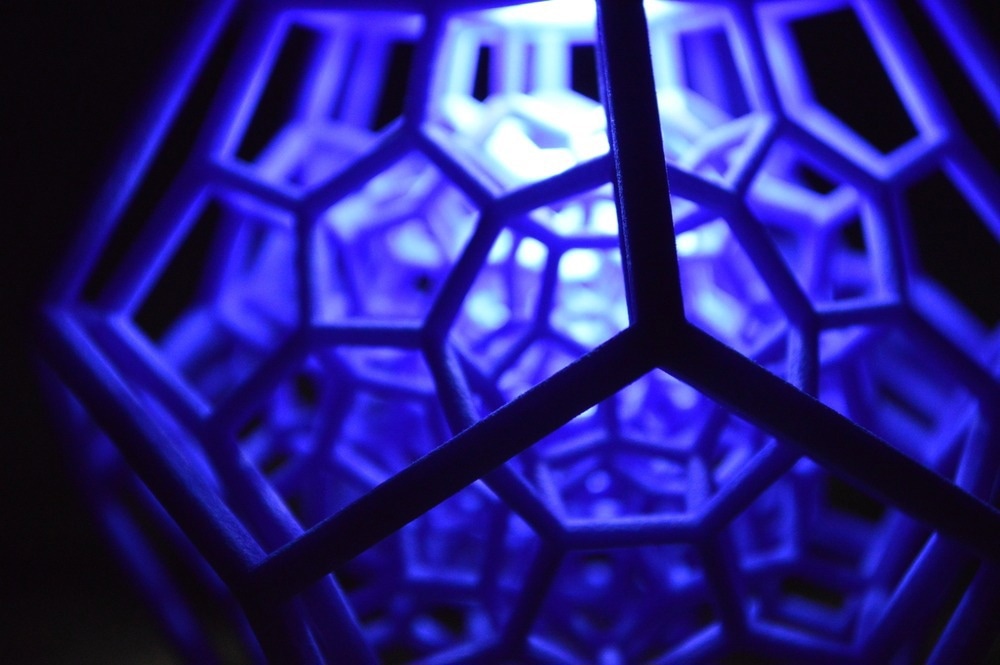
Image Credit: Elizabeth123456789/Shutterstock.com
Problems with Additive Manufacturing
Additive Manufacturing originates from a tradition rooted in fast prototyping, in which material qualities were considered secondary to shape and fit. Material qualities became the key contributor and regulating element as 3D printing evolved into industrial fabrication. Material qualities fall short of the 3D manufacturing industry standards, significantly limiting the industrial utilization and markets in which this new platform can be used.
The poor material qualities of additively manufactured parts are exclusively due to the high curing stresses which lead to layer imperfections and cause interlayer fragility. Additionally, these factors were also the root cause of the extremely slow manufacturing and processing rate of components. Furthermore, injection molding and other polymeric manufacturing techniques hampered the ability to make complex shapes.
Major Challenges in Elastomeric 3D Printing
The manufacturing process has a large impact on the difficulties associated with elastomer fabrication utilizing several AM methods. Numerous issues remain unique to the printer or the mix of the elastomer and the printer. One important issue with photo-polymerization is the fluidity of the photopolymer. Treating elastomers with excessive viscosity frequently leads to delayed production durations at best along with residual stresses and warpage of the printed items at worst.
Additionally, other sets of challenges exist when using elastomers for additive manufacturing including object-manufacturing bed adhesion and extrusion failure mechanisms such as filament failure due to buckling, unsuitable printing filament dimensions, and annular backflow.
How Adaptive3D Elastomers are the Solution
The 3D printing elastomer resins from Adaptive3D have been specially designed for optimum operational cost and manufacturing. These novel resins are ideal for real additive manufacturing of adaptable elastomeric components due to their exceptionally high tear strength, elasticity, and market-leading durability. Additionally, these unique elastomers allow the freedom to manufacture complex geometrical components which were not possible in the past.
Advantages of Using Adaptive3D Elastomers
Adaptive3D employs innovative chemical technology to contribute towards the elongation and hardness of photo-polymeric resins, allowing them to resist end usage in demanding applications such as transportation, petroleum and gas, and industrial facilities. The high-end properties allow not only fast sustainable printing and rapid prototyping but also ensure the full potential of functional parts.
Elastomeric resin 3D printing is much less expensive than other polymers, such as silicone manufacturing, and is optimized for macroscopic commercial processes. Adaptive3D resins ensure exceptional impact resistance, less processing time, and improved service life at a much more affordable price.
Use of Elastomers in Additive Printing
The industrial sector constantly utilizes thermoplastic elastomers (TPEs) for additive manufacturing processes in applications necessitating rubber-like characteristics. TPEs have recently been employed in 3D printing as a supplement to traditional printing substrates (like PLA and ABS).
Elastomers can be utilized to create consumer items, sporting goods, and especially electronic gadgets, along with profound uses in the construction industry and manufacturing of automobile parts.
What Unique Properties Do Adaptive3D Elastomers Possess?
Damping ToughRubberTM, the world's top-notch highest-straining premium photopolymer, has been successfully designed by Adaptive3D to overcome problems with polymer processing. This photo-polymeric resin is the toughest DLP 3D-printable elastomer with the highest performance levels, exhibiting the most superior tensile attributes that enable incredibly robust functioning components and products. The elastomer possesses the highest strain in the world, reaching about 405% with an exceptional yield strength and toughness of 17.3 MPa and 19.29 MJ/m3, respectively. These properties ensure performance and design as per the user’s satisfaction.
Another series of products titled Elastic ToughRubberTM consist of flexible elastomers with superior elongation to failure properties, allowing them to return to the original shape every time after suffering a deformation. These elastomers possess an elongation-to-break value of about 400%, giving the feel and performance of high-quality rubber. Such attributes make it perfect for footwear midsoles, sealings, door boots, foam-like complex geometries, and collision pieces. The advanced class of ToughRubberTM elastomers has been designed by world-class professionals ensuring excellent tear strength, tensile strength, and superior resilience.
Adaptive3D Elastomer 3D Printing Materials on the Xtreme 8K DLP 3D Printer
Video Credit: Proto3000/Shutterstock.com
Soft ToughRubberTM elastomers by Adaptive3D enable users to manufacture tougher, and highly customizable sustainable parts with outstanding precision, isotropic characteristics, and excellent processability. Soft ToughRubberTM (STR) provides the silicone sensation and biomechanical qualities while also delivering a superb surface finish.
DuraChain Photopolymer – A Unique 3D Printable Elastomeric Resin
DuraChain polymers, a crown jewel by Adaptive3D is a unique and novel class of 3D printable resins providing two-part photo-polymeric characteristics and durability in a single pot system. DuraChain 2-in-1 photopolymer phase segregates at the nanoscale level during DLP manufacturing to generate a substance that hardens into a robust, durable, and high-performance network.
This unique photo-polymeric resin family delivers revolutionary material capabilities through a materials science technique known as Photo Polymerization-induced Phase Separation or Photo PIPS. DLP printing heavily relied on standard acrylate resins which have a major drawback of low toughness and being easily susceptible to fracture. To provide more resilient and elastic qualities, the 3D manufacturing industry has been striving to gradually improve the elastomers.
By utilizing the Photo PIPs method to create durable and tough end-use parts without the use of a two-part resin, DuraChain photopolymers ensure a long service life and are environmentally friendly, owing to less waste from unused material.
Future Perspectives
The future for the range of novel elastomers produced by Adaptive3D looks bright. Already, several sectors such as the medical sector, transportation sector, energy sector, industrial manufacturing, and electrical sectors are interested in Adaptive3D’s unique elastomers.
Wetherby Inc. has a visionary policy to deliver products of the highest quality made with the lightest but most durable material. They also turned to Adaptive3D elastomers, as design freedom and flawless manufacturing were their core priorities. Elastic Tough Rubber was selected by them to optimally manufacture recoil pads via 3D printing.
Report Oceans, an American research company, lately released a report in which it assessed the development of elastomers in the 3D printing market. According to the organization, the industry for elastomers will expand by 22.5% each year between 2022 and 2030 to reach 1.389 billion dollars. Adaptive3D’s unique high-performance elastomers are surely going to play a pivotal role in this rapid commercialization.
More from AZoM: Advanced Battery Material Recycling Technology
References and Further Reading
3d Natives, 2022. 3D Printing Elastomers Market Expected to Reach $1.389 Billion by 2030. [Online]
Available at: https://www.3dnatives.com/en/3d-printing-elastomers-market-expected-to-reach-1-389-billion-by-2030/
Adaptive 3D, 2022. Additive Manufacturing. [Online]
Available at: https://adaptive3d.desktopmetal.com/additive-manufacturing/
Adaptive 3D, 2022. Case Study: In Partnership with Weatherby. [Online]
Available at: https://adaptive3d.desktopmetal.com/case-study-in-partnership-with-weatherby/
Adaptive 3D, 2022. Products: Adaptive3D’s Flexible Materials Used for Additive Manufacturing. [Online]
Available at: https://adaptive3d.desktopmetal.com/additive-manufacturing/materials-used-for-additive-manufacturing/
Adaptive 3D, 2022. Soft ToughRubber (TM). [Online]
Available at: https://adaptive3d.desktopmetal.com/additive-manufacturing/materials-used-for-additive-manufacturing/soft-toughrubber-2/
BusinessWire, 2022. Desktop Metal Launches DuraChain™ Photopolymers. [Online]
Available at: https://www.businesswire.com/news/home/20220512005585/en/
Herzberger, J. et. al. (2019). Polymer design for 3D printing elastomers: Recent advances in structure, properties, and printing. Progress in Polymer Science. 97. 101144. Available at: https://doi.org/10.1016/j.progpolymsci.2019.101144
Disclaimer: The views expressed here are those of the author expressed in their private capacity and do not necessarily represent the views of AZoM.com Limited T/A AZoNetwork the owner and operator of this website. This disclaimer forms part of the Terms and conditions of use of this website.