Sialon is a reacted mixture of SiN, Al2O3, SiO2, and AlN.
Sialon is a generic term for the technical ceramic made of aluminum, silicon, nitrogen, and oxygen blended in ratios designed to highlight a few properties. As a material category, producers or sellers of Sialon are free to provide a particular composition that might differ from that provided by another.
As INSACO does not produce materials, the company is free to source materials in the fired or hard state from the most appropriate commercial producer.
The company has years of experience collaborating with producers of all technical ceramics and comprehends the capabilities of the majority of the producers for their available shapes, sizes, and compositions. Normally, Sialons are produced by blending silicon nitride, aluminum nitride, alumina, and silica with a small amount of mixing aid, such as yttrium oxide.
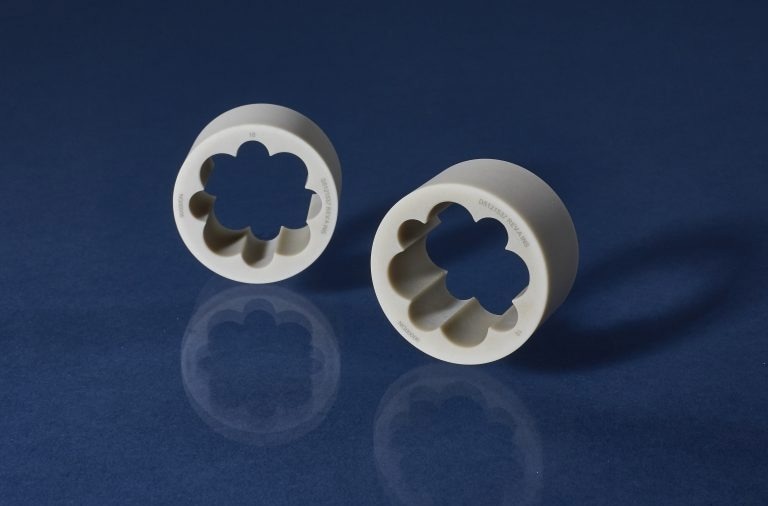
Image Credit: INSACO Inc.-Machining of Hard Materials
This powder mix is pressed and pre-fired, and then, as needed, green machined to obtain the preferred basic form before final firing.
The silicon nitride component adds up to the strength, hardness, fracture toughness, and thermal shock resistance, whereas alumina contributes properties of corrosion and electrical insulation and oxidation resistance
Sialons have been formulated to stress toughness and hardness and also lower density. This benefits body armor application where weight is significant to the soldier.
Generally, such applications use the material in the as-fired state, perhaps only having been green-machined. Normally, body armor does not need overly tight dimensional tolerances so algorithms anticipating dimension following firing-induced shrinkage are sufficient.
One more common application for Sialons is in low-pressure die casting of non-ferrous metals. In this context, good thermal shock resistance, high strength at temperature, and extraordinary resistance to wetting by metals provide significant benefits over other refractory materials.
Sialons may be the best choice over other technical ceramics, where corrosion, toughness, wear resistance at high temperatures, and thermal shock resistance are crucial in the application.
This may be for severe valves and duty pumps or rolls for tube production or dies for wire drawing. In such cases, designs frequently call for high precision of complicated features. As with most of the technical ceramics specified for high-tolerance parts, this is made possible only by machining following final firing when parts are already extremely hard.
Machining has been executed by a diamond grinding process. Being a specialty machine shop for over seven decades machining all technical ceramics, INSACO has developed methods and expertise and equipment to achieve tight control of dimensions on several complicated shapes by diamond grinding, lapping, and polishing.
Source: INSACO Inc.-Machining of Hard Materials
Property |
Value |
General |
Chemical Formula |
SiN-SiO2-Al2O3-AlN |
Mechanical |
Density |
3.1 - 3.7 gm/cc |
Hardness |
1600-1800 Knoop |
Tensile Strength |
28 kpsi |
Modulus Of Elasticity |
46 x 106 psi |
Flexural Strength |
110 kpsi |
Compressive Strength |
300 - 510 kpsi |
Poissons Ratio |
0.21 |
Fracture Toughness |
4 - 5 MPa m½ |
Electrical |
Dielectric Strength |
212 ac V/mil |
Dielectric Constant |
9.3 (@ 1 MHz) |
Volume Resistivity |
> 1014 ohm-cm |
Thermal |
Coefficient Of Thermal Expansion |
2.7 - 6.8 x 10-6/°C |
Thermal Conductivity |
18 - 25 W/mK |
Specific Heat |
0.21 cal/g °C |
Shock Resistance |
300 °C Diff. |
Maximum Working Temperature |
1700 °C |
All properties are at room temperature unless otherwise noted.
Engineering data are representative, and are not intended as absolute nor warrantable. Manufacturer’s Data shown is blended from multiple sources and therefore illustrates the marketplace.
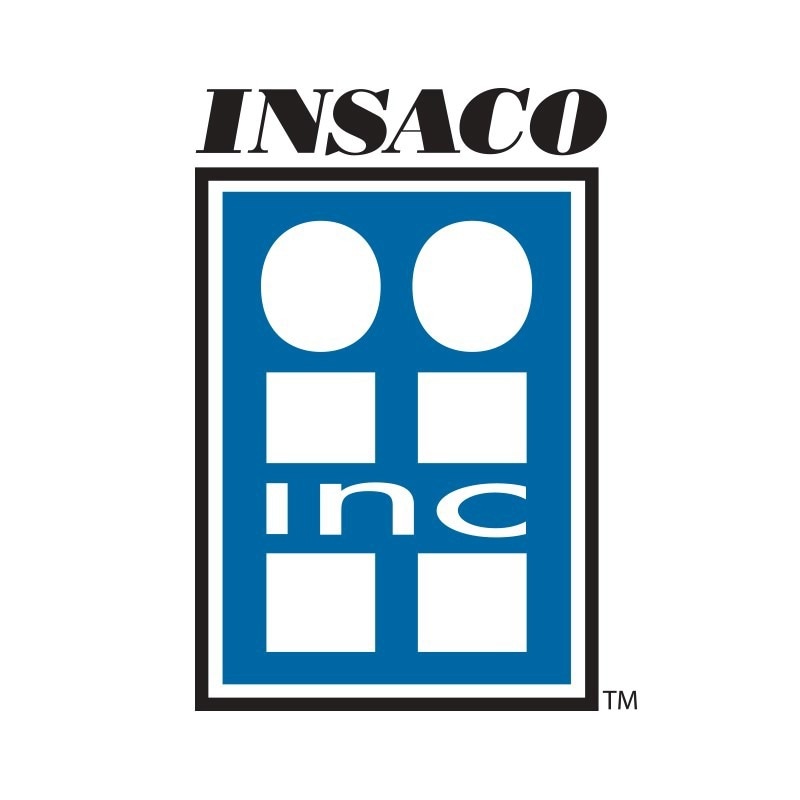
This information has been sourced, reviewed and adapted from materials provided by INSACO Inc. - Machining of Hard Materials.
For more information on this source, please visit INSACO Inc. - Machining of Hard Materials.