Alumina is used in several traditional and advanced industrial applications owing to its low fabrication and material costs, high strength and temperature stability, and good thermal conductivity. This article discusses the feasibility of using the spark plasma sintering (SPS) method to join alumina ceramics with titanium/zirconium interlayers.
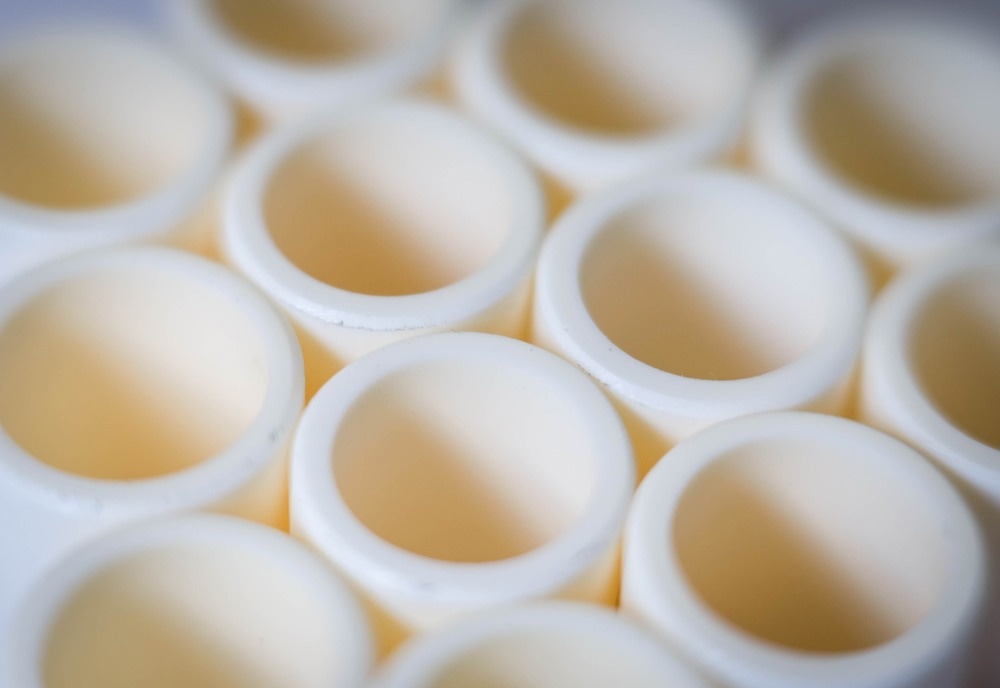
Image Credit: WildSnap/Shutterstock.com
High-Performance Production of Alumina Ceramic Components
Innovations in alumina ceramic production techniques can increase the utilization of alumina ceramics in industrial applications. For instance, simple alumina components, such as alumina discs, can be joined to manufacture objects with more complicated shapes in a cost-efficient manner.
However, several ceramic-based applications such as sensors and solid oxide fuel cells with composite materials and complex shapes require high-performance joining with properties such as good joint integrity, chemical durability, stability of the joint at high operating temperatures, and high vacuum tightness.
Glass sealing, transient liquid phase bonding, active brazing, and solid-state diffusion bonding are commonly used for high-performance joining with such properties. These methods introduce additional interlayers between alumina ceramic components.
Materials used as interlayers during high-performance joining also influence the strength of the joints. Thus, the proper selection of interlayer materials is crucial to prevent the failure of the overall ceramic component.
The selection of interlayer materials in ceramic joints depends on several parameters, including thermal properties, mechanical properties, operating temperature, and joining temperature.
Feasibility of Using SPS to Join Alumina Ceramics
SPS/pulsed electric current sintering (PECS)/ field-assisted sintering technique (FAST) is increasingly gaining attention for the treatment of ceramic materials as fully dense ceramic-based composites, and ceramics can be obtained using this method at lower temperatures compared to conventional methods.
Spark plasma sintering (SPS) uses a direct electrical current (DEC) to perform rapid consolidation of powders in a short duration using high sintering pressures. During SPS, the gap between powder particles is charged with electrical energy, and a spark plasma with high temperature is applied momentarily, which allows sintering at lower temperatures compared to alternative methods while achieving full densification.
Electrical field diffusion effect, Joule heating, spark impact pressure, and spark plasma are generated by this large current pulse energizing technique. High thermo-efficiency, spontaneous heating, better self-purification of the particle surface, and rapid sintering under low temperatures are the key advantages of the SPS process.
The heating power is distributed homogenously during SPS over the entire sample volume at macroscopic and microscopic scales. The heating power also dissipates precisely at the points of contact of powder particles within the sample.
An extremely high heating/cooling rate of 500 K/min can be realized in SPS, which leads to rapid heating of the powder compact to the final sintering temperature without any loss of grain boundaries. The high grain boundary area facilitates rapid densification of the powder compact through grain-boundary diffusion.
Thus, a fully dense ultrafine microstructure can be obtained within a few minutes compared to the several hours required in other techniques, such as hot-pressing sintering, to realize the same sintered density. The method also limits grain growth due to high heating rates.
Although SPS has been utilized to join ceramic-based composites with different interlayers, the method is not used extensively to join pure alumina ceramics.
Recent Studies
In a study recently published in the journal Materials and Design, researchers investigated the feasibility of using SPS to join alumina ceramics/alumina discs with titanium/zirconium interlayers.
Zirconium was selected as the interlayer as it possesses a good wettability and a coefficient of thermal expansion (CTE) of 5.9×10-6 K-1, which is close to the CTE value of 7 × 10-6 K-1 of alumina.
Additionally, titanium was selected as it possesses excellent wettability properties and can react with alumina to form titanium aluminide, a stable intermetallic compound. Moreover, the difference between the CTE value of titanium and alumina is extremely small, which can reduce thermal stresses and eventually decrease the crack formation during cooling after thermal treatment of aluminum oxide-titanium-aluminum oxide bonded systems.
The effect of pressure and temperature on the alumina-interlayer bonding properties was measured for both zirconium and titanium interlayers. The quality of the bonded ceramics was investigated using a scanning electron microscope, while energy-dispersive X-ray spectroscopy was employed to understand the bonding mechanism.
Zirconium-alumina bonding was achieved at 800 and 900 oC with 4.2 kN applied force and at 900 oC with 3 kN applied force. Titanium was bonded to alumina at 900, 800, and 700 oC with 3 kN applied force. However, titanium-alumina systems bonded at 800 oC showed the highest stability and integrity compared to systems bonded at 700 and 900 oC.
In this study, researchers successfully demonstrated titanium-alumina bonding using the SPS method for the first time. The titanium-alumina systems demonstrated a better quality of bonding compared to the zirconium-alumina systems.
Moreover, the formation of zirconium dioxide can reduce the stability of the joined system. Oxygen diffusion through the formation of oxygen vacancies/defects and reaction products such as zirconium dioxide and titanium dioxide supported the bonding mechanisms.
Taken together, SPS can be used to effectively join simple alumina components to manufacture large objects with more complicated shapes suitable for industrial applications.
More from AZoM: What are Ceramic Laser Materials and How Have they Developed?
References and Further Reading
Stosz, M., Narayanasamy, S., Bell, J., Graule, T., Kata, D., Blugan, G. (2023). Joining of alumina ceramics with Ti and Zr interlayers by spark plasma sintering. Materials & Design, 227, 111724. https://doi.org/10.1016/j.matdes.2023.111724
Sharma, N., Syed, N.A., Ray, B.C. (2019). Fundamentals of Spark Plasma Sintering (SPS): An Ideal Processing Technique for Fabrication of Metal Matrix Nanocomposites: Advances in Processing and Applications. Spark Plasma Sintering of Materials, 21-59. https://www.researchgate.net/publication/331183543_Fundamentals_of_Spark_Plasma_Sintering_SPS_An_Ideal_Processing_Technique_for_Fabrication_of_Metal_Matrix_Nanocomposites_Advances_in_Processing_and_Applications
Disclaimer: The views expressed here are those of the author expressed in their private capacity and do not necessarily represent the views of AZoM.com Limited T/A AZoNetwork the owner and operator of this website. This disclaimer forms part of the Terms and conditions of use of this website.