Can we use the pyrolysis method as a sustainable waste upcycling process for the treatment of decommissioned wind turbine blades (WTBs)?
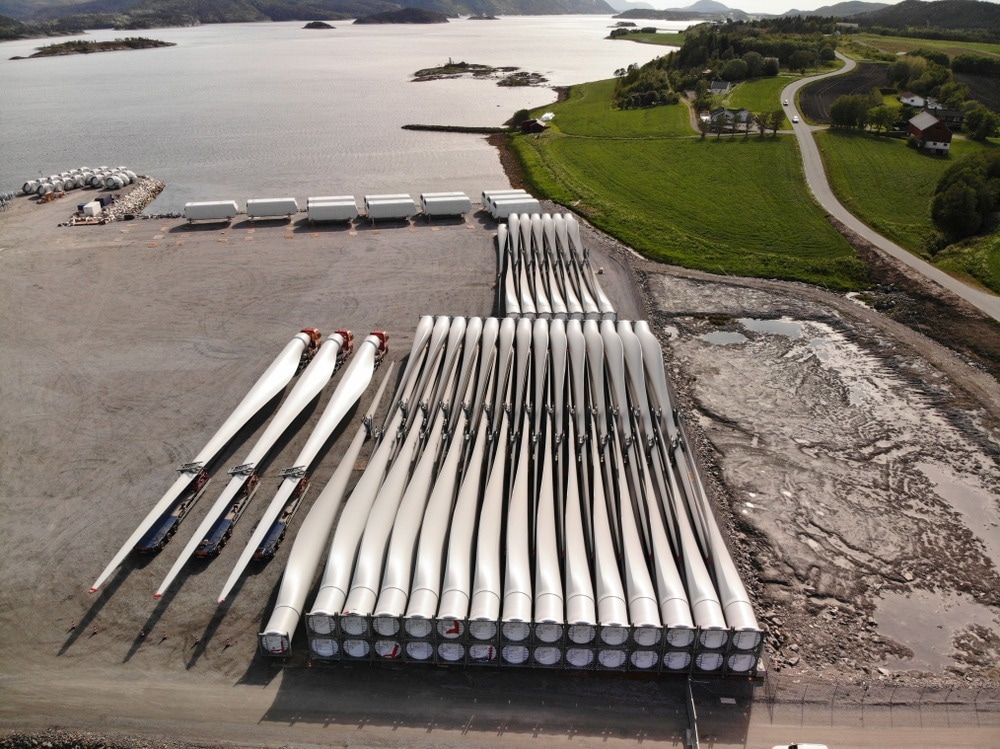
Image Credit: Feher Istvan/Shutterstock.com
Importance of Proper Treatment of Waste/Decommissioned Waste WTBs
The growing emphasis on reducing the carbon dioxide emissions from fossil fuel-based power plants has increased the importance of harnessing clean and renewable sources such as wind to generate energy. In recent years, wind power has accounted for a considerable share of the overall electricity generated globally.
The installed wind power capacity will rise significantly in the upcoming years as several governments focus on increasing renewable energy generation to meet the rising energy demand.
However, the rising number of wind farms will substantially increase the generation of WTB waste due to decommissioning of damaged/aging WTBs and their replacement with newer, more efficient, and larger blades.
WTBs are decommissioned after the end of their 20-to-25-year service lives. An increasing amount of WTB waste can create major environmental issues. Thus, the proper treatment of these waste WTBs using sustainable practices has become a crucial necessity.
Although the other parts of wind turbines, such as the gearbox, generator, foundations, and tower, can be recycled easily, the recycling of the enormous WTBs is extremely challenging due to the complicated nature and inhomogeneity of these blades.
Specifically, the blades composed of thermosetting fiber-reinforced polymer composites were designed to be durable and withstand extreme weather for more than 20 years, making their recycling highly difficult and almost impractical.
Common Waste WTB Treatment Methods and their Drawbacks
Decommissioned/damaged WTBs are commonly disposed of in landfills. However, the high taxes introduced for landfilling composite materials such as WTBs is a major disadvantage of this method. Additionally, the disposal of large WTBs leads to the wastage of valuable landfill space.
Other waste WTB treatment methods such as mechanical recycling, chemical treatment, and incineration also have several drawbacks. For instance, the product obtained after the mechanical recycling of WTBs has a low market value, while the use of chemicals and heat during chemical treatment to separate the polymer composite matrix from fibers can endanger the health and safety of workers.
Although incineration of decommissioned WTBs in combined heat and power (CHP) plants can generate electricity and heat, the process can lead to emissions of hazardous flue gases due to the inorganics present in the composite materials used to manufacture these blades. Thus, these methods are ineffective for sustainably treating waste WTBs and inconsistent with the sustainability goals of wind energy.
Pyrolysis of Waste WTBs
Pyrolysis is a suitable method to produce useful materials/high-value products and energy by recycling inhomogeneous complicated waste substances such as waste WTBs. Pyrolysis involves the thermal decomposition of the polymer matrix in WTBs at 300-500 oC temperatures under an inert atmosphere to avoid combustion.
In this process, the organic part of the composite is degraded into lower molecular weight components, which can be recovered and reutilized in specific cases. Fibers, filler particles, liquid fuels, and organic components can be recovered through the pyrolytic recycling of waste/decommissioned WTBs.
Studies have demonstrated that glass fibers with a high yield can be successfully recovered from waste WTBs through pyrolysis. Pyrolysis also requires lower energy compared to other recovery techniques to degrade the polymer matrix in glass fiber composites. Moreover, no additional pretreatments, such as complex shredding and disassembly operations, are required in pyrolysis.
The processing temperature required for the pyrolysis of WTBs can be lowered using specific catalysts. Extremely high pyrolysis temperatures can thermally accelerate the diffusion of surface flaws over the fibers, leading to a substantial reduction in the tensile strength of recovered fibers, which limits their secondary utilization. Different pyrolyzers, such as fluidized bed reactors, screw pyrolyzers, rotary kilns, and fixed bed reactors, can be used for pyrolysis.
Recent Developments
In a study recently published in the Journal of Analytical and Applied Pyrolysis, researchers investigated the thermal degradation behaviors of epoxy resin mixed with carbon fiber, which are used in base components of WTBs, using tube furnace, thermogravimetric-Fourier transform infrared spectroscopy, and thermogravimetric analysis.
Specifically, the effects of various mixing ratios and heating rates were studied, the pyrolysis reaction kinetics were calculated, and the volatile pyrolysis fraction was investigated. The results demonstrated that a high heating rate strengthened and delayed the thermal degradation of materials.
However, the heating rate displayed a lesser impact on the activation energy compared to the mixing ratio. The difference in pyrolysis behavior was higher under different mixing ratios. Carbon–oxygen compounds, alkanes, methane, carboxylic acids, aromatic compounds, and olefins were the main gaseous products.
The sample proportion closest to the actual component possessed the best recovery value and calorific value. Moreover, the co-pyrolysis of epoxy resin and carbon was more stable than pure pyrolysis/pyrolysis of only epoxy resin.
Carbon Rivers, a company based in Tennessee, has used the pyrolysis method to recover fiberglass from shredded WTBs. The company heated waste fiberglass-resin composite above 300 °C under an inert temperature to obtain a higher-molecular-weight hydrocarbon liquid, glass fibers, and a low-molecular-weight hydrocarbon gas. The gas generated in the pyrolytic chamber is used as fuel to sustain the pyrolysis reaction, while the liquid fuel can be utilized in other industrial processes.
To summarize, pyrolysis has become one of the most promising methods for sustainable waste WTB treatment as it can effectively recover high-value products, such as glass fibers, and generate gaseous and liquid products that can be used as heating sources for pyrolysis procedures, which prevent the wastage of landfill space, reduce hazardous emissions, and requires substantially less energy compared to other end-of-life treatment methods.
More from AZoM: The Intersection Between AI and 3D Printing
References and Further Reading
Ge, L., Li, X., Feng, H., Xu, C., Lu, Y., Chen, B., Li, D., Xu, C. (2023). Analysis of the pyrolysis process, kinetics and products of the base components of waste wind turbine blades (epoxy resin and carbon fiber). Journal of Analytical and Applied Pyrolysis, 170, 105919. https://doi.org/10.1016/j.jaap.2023.105919
Jacoby, M. (2022) How can companies recycle wind turbine blades? [Online] Available at https://cen.acs.org/environment/recycling/companies-recycle-wind-turbine-blades/100/i27 (Accessed on 20 February 2023)
Yang, W., Kim, K., Lee, J. (2022). Upcycling of decommissioned wind turbine blades through pyrolysis. Journal of Cleaner Production, 376, 134292. https://doi.org/10.1016/j.jclepro.2022.134292
Dorigato, A. (2021). Recycling of thermosetting composites for wind blade application. Advanced Industrial and Engineering Polymer Research, 4(2), 116-132. https://doi.org/10.1016/j.aiepr.2021.02.002
Disclaimer: The views expressed here are those of the author expressed in their private capacity and do not necessarily represent the views of AZoM.com Limited T/A AZoNetwork the owner and operator of this website. This disclaimer forms part of the Terms and conditions of use of this website.