The void fraction, an important powder packing property, directly impacts many of the powder's physical characteristics and applications. To demonstrate how the variation in powder particle size affects its packing property, this articles illustrates the skeletal density, tapped density, bulk density and void fraction of glass beads at different particle sizes.
Porosity is the primary characteristic of dry powder, and it usually only considers the fraction of voids between the particles. This property is valuable for understanding the electrical, mechanical, flow, and heat transfer properties of the powder in various fields, including ceramic, soil, metallurgy, and pharmaceutical.
The void fractions are associated with particle size, particle shape, and packing mode. To determine the void fraction, bulk density, tapped density, and skeletal density of packed powder are usually characterized. This article aims to examine the relationship between the void fraction and the particle size.
Evaluation Parameters of Void Fraction
The void fraction can be determined by the difference between skeletal density and either bulk density or tapped density.
When the powder packs naturally, the powder’s packing density is equivalent to its bulk density, while its void fraction is equivalent to its bulk-packing void fraction.
When the powder is in the tapped packing state, its packing density is equivalent to its tapped density, and the void fraction is identical to the tapped-packing void fraction.
The following equations provide these values:
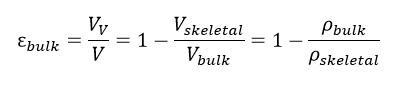 |
(1) |
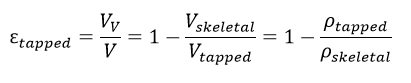 |
(2) |
Where:
εbulk = void fraction of bulk powder
εtapped = void fraction of tapped powder
Vv = volume of void
Vskeletal, ρskeletal = skeletal volume, skeletal density
Vbulk, ρbulk = bulk powder volume, bulk powder density
Vtapped, ρtapped = tapped powder volume, tapped powder density
Effect of Particle Size on Void Fraction
Regarding the actual manufacturing process, particle shape, particle size, moisture content, and wall effect all play a significant part in the performance of the powder-packing property.
In the experiment outlined in this article, glass beads with different particle sizes were studied. Their particle circularity and sizes were initially characterized by the image analyzer BeVision S1. The results are outlined below in Table 1 and Figure 1.
Table 1. Particle size and shape values of the glass bead samples. Source: Bettersize Instruments Ltd.
No. |
D10 (μm) |
D50 (μm) |
D90 (μm) |
Circularity (S50) |
#1 |
25.9 |
40.1 |
53.2 |
0.996 |
#2 |
54.8 |
60.1 |
65.8 |
0.996 |
#3 |
60.9 |
65.7 |
71.4 |
0.998 |
#4 |
169.7 |
200.3 |
232.5 |
0.995 |
#5 |
400.2 |
433.5 |
474.2 |
0.994 |
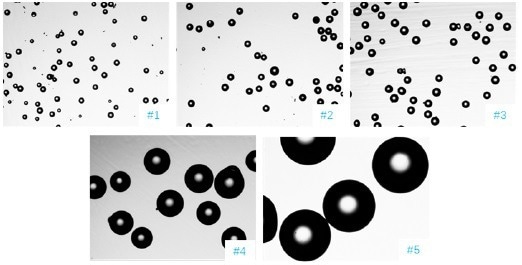
Figure 1. Microscopic images of glass bead samples (40x, Photoed by BeVison D1). Image Credit: Bettersize Instruments Ltd.
There was minimal variation in the circularity of the samples, with them all being well-rounded. The tapped density and bulk density were measured using the Tapped Density Tester BeDensi T2 Pro.
The wall effect could be omitted due to the employed cylinders having a diameter of 24 mm and the ratio of the diameter value to the D90 of the sample being more than 50.
When the ratio of the container diameter to particle size exceeds 50, it has been proven that the wall effect caused by the container size may be ignored.
Before the test, the samples were also dried at a high temperature to remove the effect of water content on the test results. As a result, particle size is the principal factor impacting the void fraction in this experiment, and the effect of particle size on the void fraction may be further explored.
The BetterPyc 380 was employed to test the skeletal density of the samples, while the BeDensi T2 Pro was employed for bulk density and tapped density.
The bulk-packing void fraction and the tapped-packing void fraction of the samples were determined by equations (1) and (2), respectively, with Table 2 detailing the results.
Table 2. Packing properties of glass bead samples. Source: Bettersize Instruments Ltd.
Sample |
ρskeletal (g/cm3) |
ρbulk (g/cm3) |
ρtapped (g/cm3) |
εbulk |
εtapped |
#1 |
2.4839 |
1.31 |
1.49 |
0.474 |
0.402 |
#2 |
2.4869 |
1.39 |
1.51 |
0.441 |
0.393 |
#3 |
2.4860 |
1.41 |
1.53 |
0.438 |
0.386 |
#4 |
2.4842 |
1.45 |
1.55 |
0.418 |
0.378 |
#5 |
2.4851 |
1.47 |
1.58 |
0.408 |
0.364 |
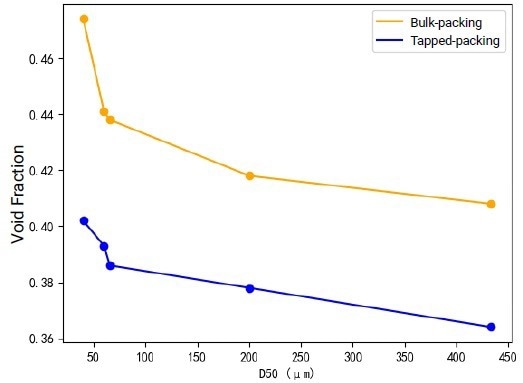
Figure 2. Particle size effects on sample void fraction. Image Credit: Bettersize Instruments Ltd.
The results demonstrate that the skeletal density almost remained constant, but as the particle size reduced, the tapped density and bulk density also reduced while the void fraction increased, as displayed in Figure 2.
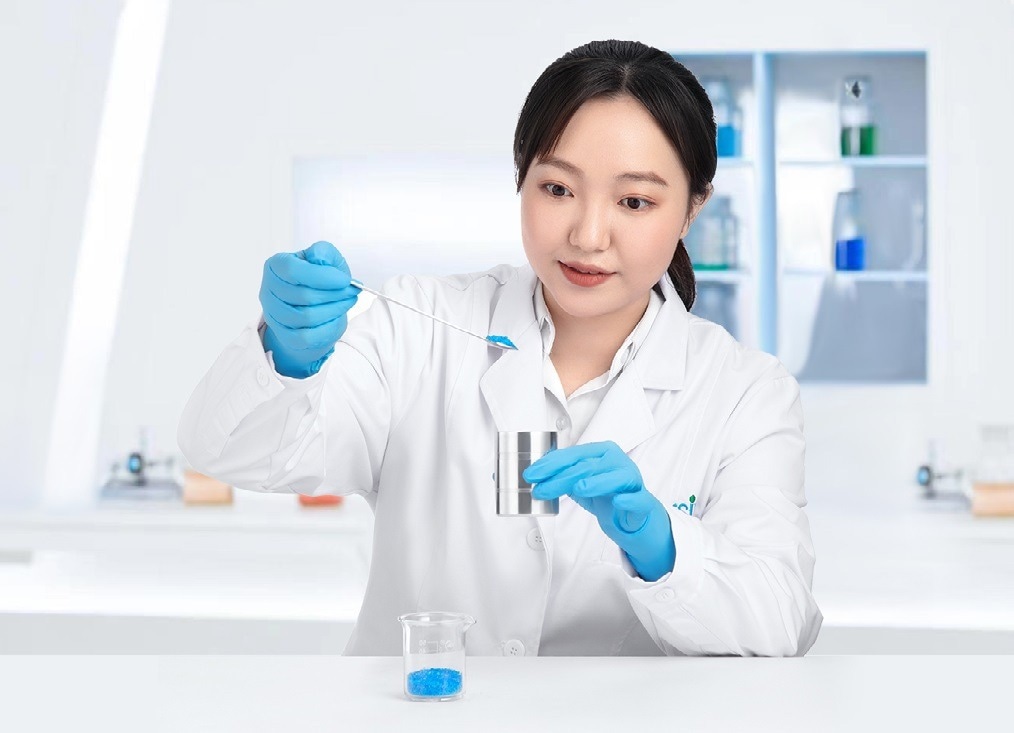
Image Credit: Bettersize Instruments Ltd.
The reduction in particle size substantially increases the void fraction, especially when comparing glass beads #1 and #2, as when particle size is lesser, the void fraction is greater.
Conclusion
Characterization of a powder’s packing property with different particle sizes, such as true density, bulk density, and tapped density, reveals the importance of particle size in the packing property of powders.
During the development or production of powder products, the particle size can be modified to optimize the powder packing property.
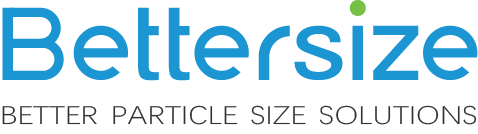
This information has been sourced, reviewed and adapted from materials provided by Bettersize Instruments Ltd.
For more information on this source, please visit Bettersize Instruments Ltd.
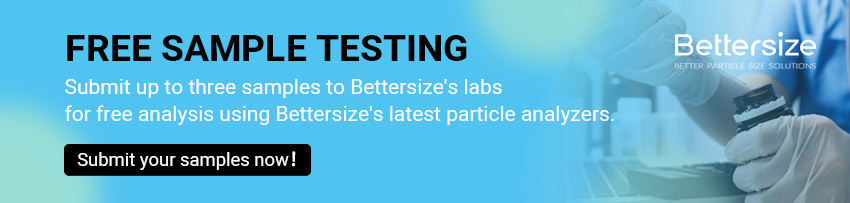