The fuel economy of an aircraft is an assessment of the aircraft's transportation energy efficacy. Enhanced fuel efficiency is achieved through improved aerodynamics, weight reduction, and the integration of more efficient engines. The aviation industry has achieved significant advances to improve the fuel efficiency of modern aircraft in this era of sustainable engineering and fluctuating petroleum prices. Adopting cutting-edge technologies and implementing novel engineering innovations has enabled aircraft manufacturers and managers to decrease fuel consumption, reduce carbon dioxide emissions, and mitigate their negative ecological footprint.
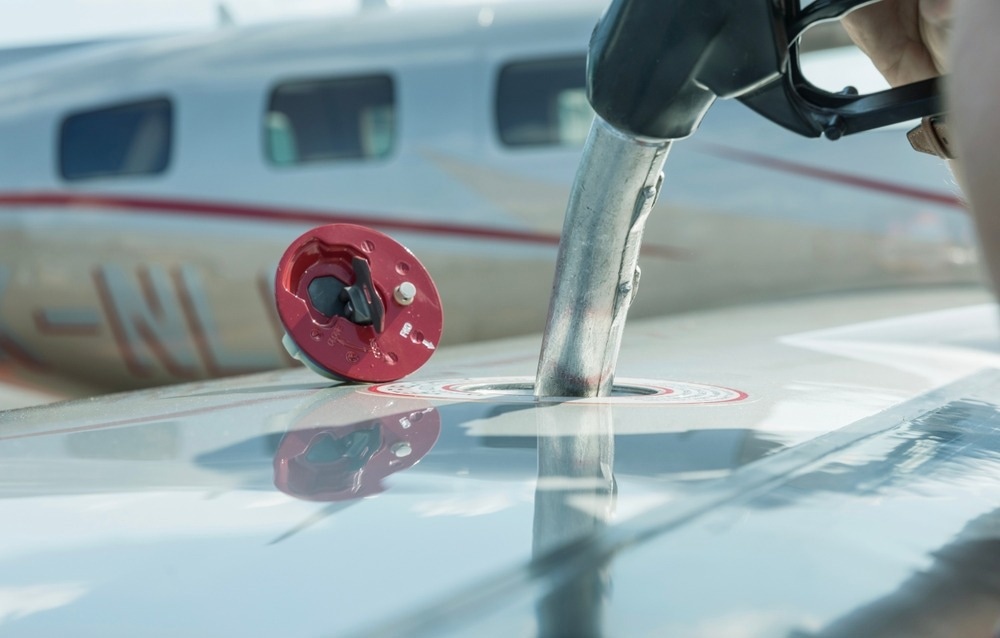
Image Credit: Nadezda Murmakova/Shutterstock.com
Fuel Efficiency Improvement by Airbus
Airbus has developed several fuel efficiency improvement solutions. A major one of these solutions is the Descent Profile Optimization (DPO) upgrade, which takes less than 4 hours to integrate on an A320. It is a software enhancement for A320 and A330ceo aircraft that reduces fuel consumption.
DPO operates by upgrading the Flight Management System (FMS) and decreasing allowances in descent and approach, allowing for a shorter braking distance in level-off. The DPO upgrade enables saving around 75kg of fuel per descent on an A320 and 140 kg while operating an A330. These calculations forecast a massive 140 tons of fuel savings and a decrease in CO2 emissions by around 440 tons.
The DPO has been complemented by the IDLE Factor Optimizer (IFO), which is a web application. IFO perpetually modifies the Flight Management System's downward route forecast. When paired with DPO, each aircraft's descent is entirely optimized, leading to reduced fuel consumption and greenhouse gas emissions.
The application calculates the aircraft’s specific optimized idle factor. This reduces the brake applications during descent and enables fuel savings of 59 tons and a reduction in emissions estimated to be around 184 tons.
Required Navigation Performance Authorization Required (RNP AR) is a procedure allowing for flexible and more direct flight paths, which reduce fuel consumption (and flight duration). Acoustics impact monitoring and enhanced airspace potential are two additional advantages of RNP AR.
Air Management Function (AMF) is another technology that modifies the proportions of developed fresh air from the combustion chamber or APU leak and recirculated air filtered by High-Efficiency Particle Arrestors (HEPA) filtration unit. The cooling system is developed to accommodate high-density configurations in the absence of AMF. It permits annual savings of up to 115 tons of petroleum per aircraft.
Does Twin Fuselage Configuration Improve the Fuel Efficiency of Passenger Aircraft?
In Flightpath 2050, the European Commission (EC) advocates for a 75 percent decrease in CO2 emissions and a 90% reduction in NOx emissions. Twin-fuselage (TF) aircraft design is one of the most intriguing possibilities allowing for an improvement in wing aspect ratio. The design of a wing with a high aspect ratio can boost aerodynamic efficiency, reduce fuel consumption, and lead to decreased emissions.
The latest article published in Aerospace Science and Technology focuses on the boost in fuel efficiency obtained by utilizing TF configuration. The fuselage length is decreased when a TF configuration is adopted instead of a single fuselage configuration. The total airframe volume of TF aircraft is equal to that of the single-fuselage layout divided by √2, so the overall cargo compartment volume of the two fuselages decreases in comparison to the single-fuselage layout.
The researchers presented an assessment of a medium-range TF transport aircraft to illustrate the improved fuel efficiency of the TF airplane layout and evaluation methodology.
With the same flight scenario and top-level specifications, the TF aircraft utilized 29.33% less fuel than the A320neo and was 37.13 percent lighter than the standard configuration. n. A comparative investigation revealed that medium-range TF aircraft was 9.37% more fuel-efficient.
A surrogate-based MDO infrastructure was devised and utilized for the TF aircraft's optimization. Up to a 20.34 % decrease in fuel weight, a 7.1% decline in maximum take-off weight, and a 4.78 % decrease in Overall empty weight indicated a massive boost in fuel efficiency.
Camber Morphing Winglets for Fuel Efficiency
Aeronautical researchers from Brazil have published research in Aerospace Science and Technology focusing on the advantageous fuel-efficient characteristics of camber morphing winglets.
Drag reduction is essential for enhancing aircraft fuel economy. By transferring the wingtip vortex beyond the wing while decreasing its magnitude and strength, wingtip structures diminish lift-induced drag.
By shifting both the leading and trailing edges, the suggested morphing concept permits camber variations in the airfoil segment. It was applied to a commercial jet of moderate capacity. On a typical mission, an aerodynamic adjustment was executed using a genetic algorithm in conjunction with the full potential aerodynamic model of the (Boundary Layer Wing Fuselage) BLWF code. BLWF has been developed by Boeing. Assessment of efficiency revealed a theoretical 6% decrease in maximum range assignment block fuel.
The suggested design may allow for a higher capacity of 8 passengers over a maximum distance flight or a 700 Nautical Mile (NM) boost on aircraft range with a 4-passenger capacity while maintaining the same fuel consumption as the fixed geometry configuration on a 3125 Nautical Mile (NM) mission.
The camber morphing winglet study revealed that this concept has the potential to enhance efficiency and reduce block fuel consumption.
Project AIMS: A Collaboration between Boeing and NASA
NASA will commence flight testing of two novel technologies in 2023. The X-57 Maxwell is a compact, lightweight experimental aircraft powered by fourteen electric motors. It will reduce the average operating cost per hour of a conventional aircraft from $440 to $275. It uses a distinctive form and technology that limits sonic eruptions to a soft thud when perceived on the ground.
NASA and Boeing are developing, constructing, and operating a brand-new, large-scale prototype plane dubbed the Sustainable Flight Demonstrator, with the concept being a single-aisle Transonic Truss-Braced Wing (TTBW) aircraft. The TTBW structure is a compact, ultra-thin wing spanning 170 feet, affixed at the apex of the fuselage and anchored underneath by an arching brace, which is anticipated to increase fuel savings by up to 30 percent.
Future Direction for Improving Fuel Efficiency
NASA and other famous educational institutes, such as MIT, are working on several technologies to enhance the fuel efficiency of modern aircraft. The Massachusetts Institute of Technology is the team leader for the N+3 initiative, which produced the D-series "Double Bubble" and the H-series Hybrid Wing Body carrier concepts.
Not only does the aircraft minimize fuel consumption, but it also reduces pollution and NOx emissions and possesses the capacity to use shortened runways. This design features long, slender wings and a diminutive tail.
It travels 10% slower than the Boeing 737, and the engines are located at the back of the airframe rather than on the wing to utilize the Boundary Layer Ingestion technique. With this approach, slower-moving air from the fuselage's wake enters the combustion chambers, resulting in lower consumption of fuel for the same propulsion. The long-range theory, the Hybrid Wing Body, utilizes many of the same technologies as the Double Bubble but enables larger payloads and better range.
What is the Sugar Volt Concept?
NASA is contributing to safer, more environmentally friendly, and more efficient travel for all individuals through green aviation. In the next 20 to 30 years, electric engines will be a revolutionary idea for aircraft and will surely transform aeronautics. NASA, Boeing subsonic team, General Electric, and Georgia Tech are working on a hybrid aircraft propulsive technology titled SUGAR Volt.
Due to the incorporation of battery energy, the SUGAR Volt concept (which adds an electric battery gas turbine mixed power technology) can reduce petroleum consumption by more than 70% and total energy consumption by 55%. Additionally, blended electric propulsion can minimize disturbance and abbreviate takeoff distances. The SUGAR team additionally recognized hybrid electric engine technology as a "high-risk, high-reward technology."
GE9X – Most Fuel-Efficient Engine
GE Aviation is the foremost global supplier of business and military airliner engines, its components, as well as avionics and electrical aircraft elements. It is currently engaged in GE9X development.
The GE9X is expected to be the most fuel-efficient power plant ever produced by GE, with a 10% improvement in aircraft fuel usage compared to the GE90-115B-powered 777-300ER and a 5% improvement in specific fuel consumption compared to any twin-aisle engine.
In short, various structural and technological innovations are being researched and implemented to ensure a boost in the fuel efficiency of modern aircraft.
More from AZoM: Particle Analysis of Different Types of Automotive Fuels
References and Further Reading
Airbus Aircraft, 2023. Fuel Efficiency Solutions. [Online]
Available at: https://aircraft.airbus.com/en/services/enhance/systems-and-airframe-upgrades/fuel-efficiency-solutions
Airbus, 2023. Descent Profile Optimisation (DPO). [Online]
Available at: https://aircraft.airbus.com/en/services/enhance/systems-and-airframe-upgrades/efficiency-sustainability-systems-upgrades/descent-profile-optimisation-dpo
Wilcox, K., 2023. Project Aims to Improve Aviation Fuel Efficiency. [Online]
Available at: https://appel.nasa.gov/2023/02/27/project-aims-to-improve-aviation-fuel-efficiency/
Eguea, P. et. al. (2020). Fuel efficiency improvement on a business jet using a camber morphing winglet concept. Aerospace Science and Technology, 96, 105542. Available at: https://doi.org/10.1016/j.ast.2019.105542
Ma, Y., & Elham, A. (2021). Twin-fuselage configuration for improving fuel efficiency of passenger aircraft. Aerospace Science and Technology, 118, 107000. Available at: https://doi.org/10.1016/j.ast.2021.107000
Mrazova, M. (2013). Future directions of fuel efficiency in aviation industry. INCAS Bulletin, 5(4), 71. Available at: https://doi.org/10.13111/2066-8201.2013.5.4.8
Disclaimer: The views expressed here are those of the author expressed in their private capacity and do not necessarily represent the views of AZoM.com Limited T/A AZoNetwork the owner and operator of this website. This disclaimer forms part of the Terms and conditions of use of this website.