Several 3D printing methods have been developed over the past few decades. These technologies have been rapidly adopted by multiple industries, with SLA and FDM emerging as two major 3D printing methods. This article will discuss and compare these two technologies.
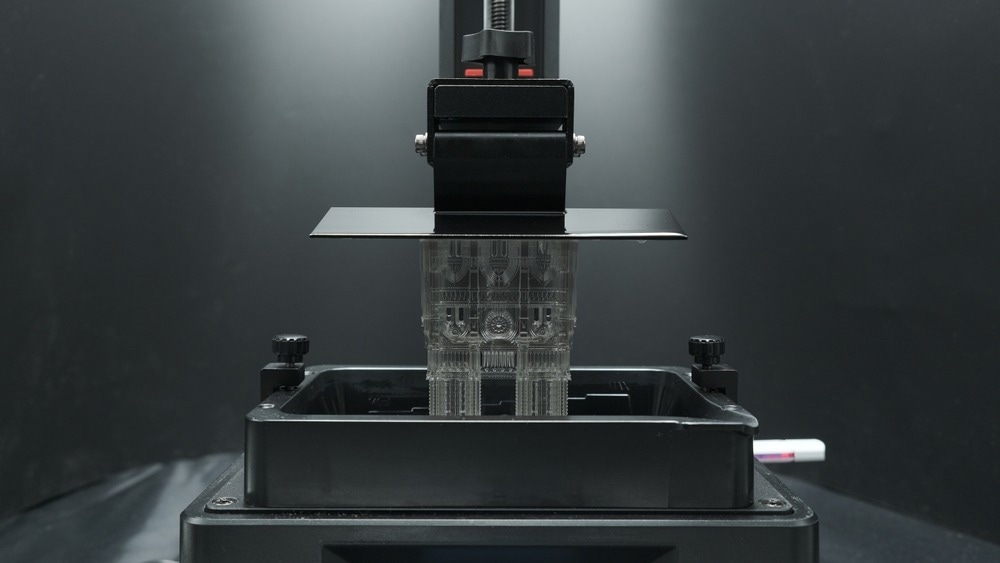
Image Credit: Tanasara/Shutterstock.com
3D Printing: An Overview
3D printing has emerged over the past four decades to become a major cornerstone of the fourth industrial revolution. Today, affordable desktop 3D printers are used by hobbyists worldwide, with 3D printing used to produce a multitude of commercial products.
Also known as additive manufacturing, 3D printing has emerged as a solution to key issues such as the housing crisis, organ shortages, and the democratization of product manufacturing.
3D printing has some key advantages over conventional subtractive manufacturing. It minimizes waste and cost, as products are constructed layer by layer from a slurry, using up all the materials. Additionally, it allows for greater design flexibility, and products and parts can be printed from multiple materials.
Additive manufacturing is a more sustainable and cost-effective approach to manufacturing, with construction and the space industry two major sectors seeing a current growth in the use of 3D printing.
Several techniques have been developed since the invention of 3D printing in the mid-1980s, with Stereolithography (SLA) and Fused Deposition Modeling (FDM) being two of the most widely used methods.
What is SLA?
SLA, or stereolithography, was the first 3D printing process invented, with the patent for the technology granted in 1986. A dominant 3D printing method, it has spawned similar techniques such as Digital Light Processing (DLP.)
SLA is a vat polymerization method that produces 3D parts from a UV-sensitive resin using photo-polymerization. A light source cures this photo-sensitive resin in a vat. The laser-solidified resin is extruded by the printer and deposited layer by layer to produce the final printed product.
Mirrors are utilized in SLA printers to control the laser, aiming it and curing the photo-sensitive resin. As with all types of 3D printing techniques, SLA uses 3D computer-generated sliced models to build the final product layer-by-layer.
Two types of SLA printers are commonly used in additive manufacturing. These are top-down and bottom-up. Top-down methods are the most commonly utilized in SLA 3D printing, but bottom-up methods do have their advantages over top-down techniques.
Top-Down Vs. Bottom-Up SLA: Benefits and Drawbacks
The two types of SLA 3D printing methods have some benefits and drawbacks over the other. Top-down advantages include:
- Faster printing
- No need to separate the printed layers from the build plate before a new layer is printed.
- More reliable (generally.)
- Less chance of print failure due to less force needing to be applied on the 3D part.
- Printing does not need to be performed at an angle. Therefore, less supports are needed.
Top-down method disadvantages include:
- Larger machine
- More resin is required.
- The thickness of resin between the top of the model and the surface must be carefully controlled.
- More expensive to replace resin tanks.
Bottom-up method advantages include:
- Easier control of layer thickness
- Less resin is required.
- Smaller machines.
Bottom-up disadvantages include:
- Increased chance of print failure
- Vats need to be replaced more often to avoid print quality loss.
- Prints must be performed at an angle, requiring the use of supports.
What is FDM?
Fused deposition modeling was developed soon after Stereolithography. The method was patented in 1989. FDM has arguably become the most-well known additive manufacturing method in use today, used to produce a multitude of commercial products by both major companies and hobbyists.
FDM is also known as Fused Filament Fabrication (FFF.) The production process is commonly referred to as FFF, whilst FDM is the trademark. A material extrusion method, thermoplastics are extruded to form parts rather than the photo-curable resin used in SLA.
A heated nozzle is used to heat the thermoplastic filament to around 200oC/392oF. This heated filament is then extruded, forming the three-dimensional part layer-by-layer according to the computer model’s design.
The print head is moved upward by a set distance after each layer is printed. Layers briefly cool and are heated again when the subsequent layer is deposited. This action continues until the entire part is printed.
Common materials used in FDM methods include PLA, ABS, Nylon, PEEK, and polycarbonate. ABS is the most commonly used material in FDM printing, being inexpensive with good strength and chemical resistance. ABS is widely used in household products such as Lego.
FDM Benefits and Drawbacks
Like all other 3D printing methods, FDM has some advantages and drawbacks that inform its choice in additive manufacturing processes. Benefits include:
- An accessible, inexpensive technology. Ideal for beginners and hobbyists. Ideal for rapid prototyping due to its ease of use.
- User-friendly operation. FDM is commonly used as a consumer process rather than an industrial one, making ease of use a key feature.
Disadvantages:
- Reduced print quality.
- Slow operation compared to other methods. This makes FDM unsuitable for high-throughput industrial processes.
- Dimensional issues such as shrinkage and warping can occur.
In Summary
Stereolithography and Fused Deposition Modeling are two common 3D printing methods, both developed in the 1980s.
SLA and FDM have different uses, each having its own benefits and limitations over the other. For instance, SLA produces more detailed, smoother parts whilst FDM produces more durable and stronger parts. SLA is faster than FDM, whereas FDM can print more colors.
These differences inform the use of each method. SLA is more suitable for high-throughput industrial processes, whereas the limited speed but user-friendliness of FDM makes it more suitable for consumer products, beginners, and hobbyists.
As with any manufacturing method, companies and individuals looking to leverage the environmental, cost, and design freedom benefits of 3D printing should weigh up the benefits and drawbacks of each method before investing time and money in their implementation.
More from AZoM: Why is a Cooling System Important for 3D Printing?
References and Further Reading
3DSourced (2023) Stereolithography: Everything You Need To Know About SLA 3D Printing [online] 3dsourced.com. Available at:
https://www.3dsourced.com/3d-printing-technologies/stereolithography-sla/
Xometry (2022) SLA vs. FDM: Differences and Comparison [online] xometry.com. Available at:
https://www.xometry.com/resources/3d-printing/sla-vs-fdm-3d-printing/
3DSourced (2023) Fused Deposition Modeling: Everything You Need To Know About FDM 3D Printing [online] 3dsourced.com. Available at:
https://www.3dsourced.com/3d-printing-technologies/fused-deposition-modeling-fdm/
Disclaimer: The views expressed here are those of the author expressed in their private capacity and do not necessarily represent the views of AZoM.com Limited T/A AZoNetwork the owner and operator of this website. This disclaimer forms part of the Terms and conditions of use of this website.