SEM-Base® VI is the next generation of STACIS active piezoelectric vibration cancellation technology. Engineered to provide comprehensive support, SEM-Base VI caters to a wide array of commercial Scanning Electron Microscopes (SEMs), as well as various Focused Ion Beam (FIB) and Small Dual Beam instruments.
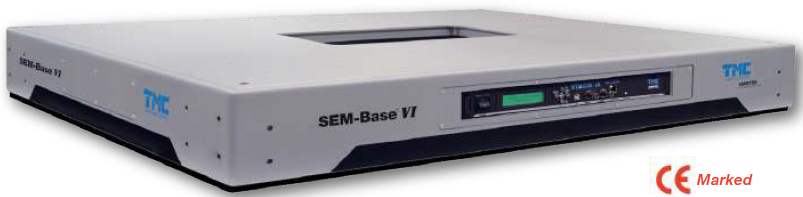
Image Credit: TMC Vibration Control
SEM-Base VI provides enhanced vibration isolation, a faster and more robust controller, and an advanced graphical user interface (GUI). These advancements will allow more laboratories and facilities to attain the level of floor vibration required to satisfy the tool manufacturer’s specifications.
With its distinctive “serial architecture,” SEM-Base VI employs vibration sensors to gauge floor vibration rather than payload vibration. This innovative approach circumvents the inherent limitations posed by payload resonances in conventional designs, ensuring superior vibration isolation and stability.
The vibration sensors are low-frequency inertial velocity sensors that deliver maximum sensitivity in the sub-hertz frequency range. Complemented by the unique piezo-actuator technology, SEM-Base VI achieves an exceptional degree of vibration cancellation, even for environments already characterized by minimal noise levels.
SEM-Base VI provides an average improvement of 6 dB in vibration isolation when compared with previous models. The latest controller from TMC, the DC-2020, boasts a novel dual-core processor, empowering tool users and researchers with an intuitive graphical interface for fast system assessment and operational peace of mind.
When connecting over Ethernet, the DC-2020 creates the SEMBase GUI in the user’s browser without having to install additional software or application programs. Alternatively, the user can interface with the controller via an onboard menu-driven liquid crystal display (LCD).
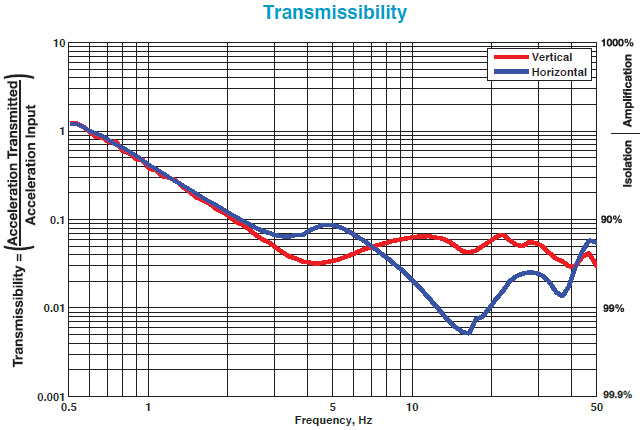
1800 lbs (818 kg) payload tested with simulated vibration at VC-C (500 μin./s, 12.5 μm/s, RMS). Image Credit: TMC Vibration Control
The SEM-Base® VI Advantage
- Hard-Mount Technology: SEM-Base® Vl maintains compatibility with all internal SEM vibration control systems and effectively reduces low-frequency floor vibrations from 0.6 Hz onwards.
- Active Inertial Vibration Cancellation: Employing high-sensitivity, low-frequency inertial velocity sensors, SEM-Base VI achieves significant levels of vibration reduction, even in environments with minimal background noise.
- Serial Design with Piezoelectric Technology: The distinct serial design combined with the exclusive high-force piezoelectric technology yields a broad active bandwidth spanning 0.6 Hz to 150 Hz. This leads to unparalleled inertial active vibration cancellation, with a remarkable 90% reduction starting at 2 Hz.
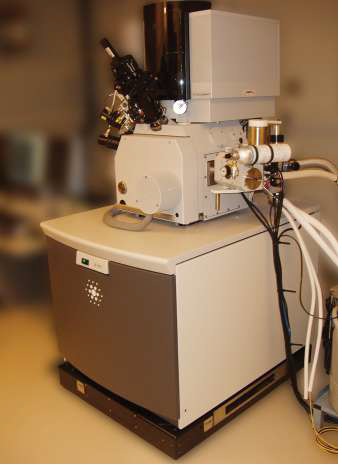
Example application. Image Credit: TMC Vibration Control
Technical Specifications
Source: TMC Vibration Control
Performance |
Active degrees of freedom |
6 |
Active bandwidth |
0.6 Hz - 100 Hz |
Passive natural frequency |
12 Hz nominal |
Effective active resonant frequency |
0.5 Hz |
Isolation at 1 Hz |
40 - 70% |
Isolation at 2 Hz |
90% |
Isolation at ≥3 Hz |
90 - 98% |
Internal noise |
<0.1 nm RMS |
Operating load range |
Standard capacity: 900 - 2,500 lbs | 408 - 1134 kg
High capacity: 2,500 - 3,200 lbs | 1134 - 1452 kg |
Magnetic field emitted at max. 4 in. (102 mm) from platform |
<0.2 µG broadband RMS |
Source: TMC Vibration Control
Design, Dimensions, Environmental and Utility |
Environmental and safety |
CE and RoHS compliant |
Active isolation elements |
Piezoelectric actuators with minimum 3300 lb. (1500 kg) capacity receive signal from a high-voltage amplifier with an output of up to 800 VDC. Vertical actuators support the isolated payload |
Passive isolation element |
Single stiff elastomer (no compressed air supply needed) |
Vibration sensor elements |
Downward facing geophone type inertial sensors that measure floor vibration below the isolator and deliver voltage proportional to the velocity of vibration motion |
Active feedback control |
Floor vibration is measured, processed and attenuated below the spring supporting the isolated surface |
Dimensions (WxD) |
35.25 x 44.25 in. | 895 x 1124 mm |
Height |
6.3 in. | 160 mm nominal
Doesn’t change when SEM-Base is switched off |
Operating temperature |
50° - 90° F | 10° - 32° C |
Storage temperature |
-40° - 130° F | -40° - 55° C |
Humidity (operating) |
<80% @ 68° F (20° C) |
System power requirements |
100 - 240 VAC, 50-60 Hz, <600 W |
Floor displacement |
<800 μin. | 20 μm below 10 Hz |
Source: TMC Vibration Control
Built-in Controller |
Processor |
150/75 MHz dual core |
Sampling rate |
10 kHz |
Analog outputs |
16 channels |
Analog inputs |
16 channels |
Status light |
Single LED |
Front panel ports |
1x serial USB 2.0; 1x serial micro-USB; 1x Ethernet RJ-45; 2x BNC |
User interface |
Front LCD display; character menu on HyperTerminal; Extended GUI for Microsoft Windows; embedded ethernet GUI |
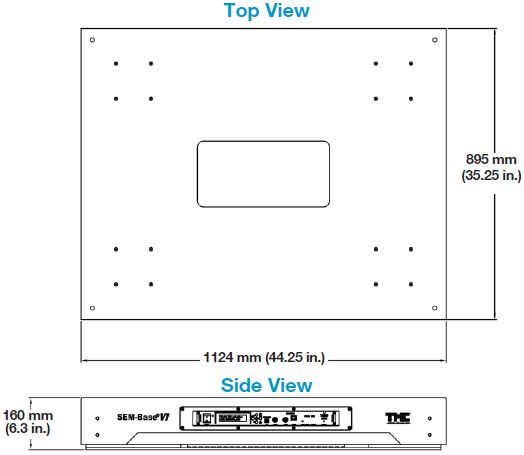
Image Credit: TMC Vibration Control
Accessories
Helpful Options that Ensure a Smooth SEM-Base® Installation
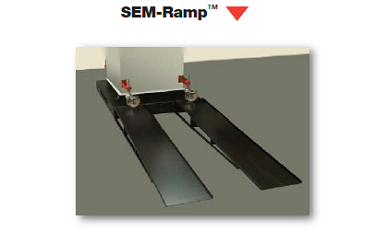
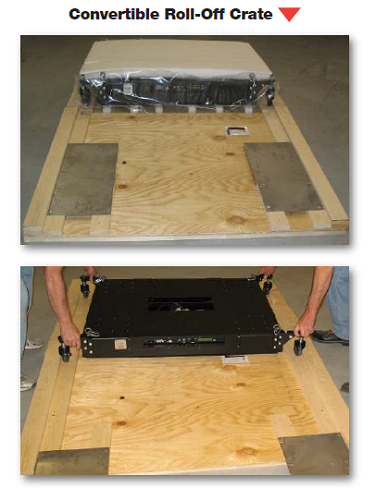
SEM-Base® (shown with optional retractable casters) is provided with a convertible roll-off crate. The crate cover converts to a sturdy ramp and the cover slats form a guide for the wheels. Image Credit: TMC Vibration Control
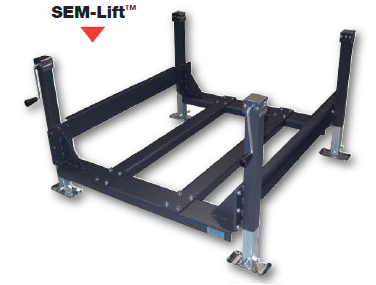

SEM-Lift™ is a safe and sturdy lifting device for scanning electron™ installation on a previously installed SEM column. SEM-Lift raises the column several inches, allowing SEM-Base® to be rolled into place. Image Credit: TMC Vibration Control
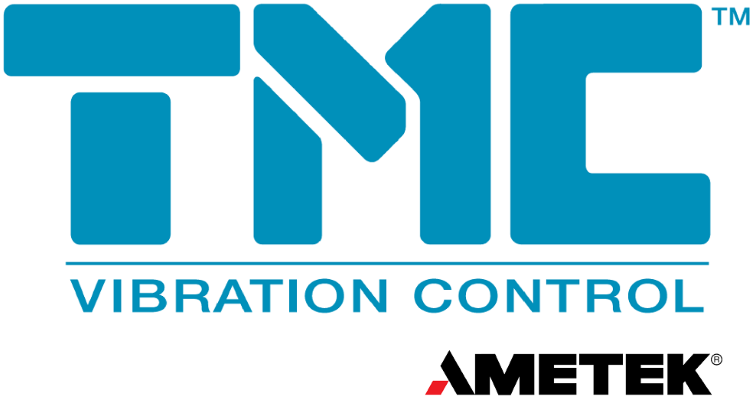
This information has been sourced, reviewed and adapted from materials provided by TMC Vibration Control.
For more information on this source, please visit TMC Vibration Control.