Sponsored by QATMReviewed by Emily MageeSep 27 2023
A complete metallographic preparation for achieving quality control on different parts of a lithium-ion battery (LIB).
Introduction
From the early Li-metal anodes to the commercial Li-ion batteries today, the evolution of Li-based battery technologies has undergone significant advancements over the last 30 years. The developmental narrative of Li-based batteries is rich with pivotal moments and historical breakthroughs.1
The history of lithium-ion batteries dates back to 1962 when the initial batteries, which were non-rechargeable after a single discharge (primary battery), featured lithium as the negative electrode material and manganese dioxide as the positive electrode material. This battery was introduced to the market in 1972 by the company Sanyo.
In 1985, the company Moli Energy achieved a significant milestone by creating the first rechargeable battery (secondary battery) using lithium as the negative electrode and molybdenum sulfide as the positive electrode. However, this design posed safety problems due to the use of lithium on the negative electrode.
The next step toward developing lithium-ion batteries involved the introduction of coatings on both sides of the electrodes, enabling the lithium to be stored and removed and have a high voltage potential. In 1991, Sony developed and launched the first rechargeable lithium-ion battery, which used carbon as the active material of the negative electrode and lithium cobalt dioxide as the positive electrode.2
Throughout this journey, one of the biggest challenges was the selection of optimal compounds for the electrodes, particularly the cathode. The criteria of achieving high cycle stability and acceptable specific capacity significantly narrowed the choices of electrode materials to a select few.
One of the most common combinations involves using aluminum foil coated with metal oxide particles in the cathode and copper foil coated with graphite in the anode. Figure 1 illustrates the structure of a typical LIB, where the foils can be coated on one or both sides.
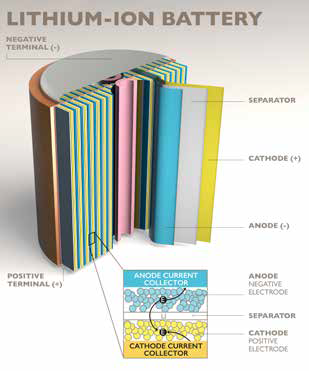
Figure 1. The structure of a conventional LIB. Image Credit: QATM
Various lithium-metal-oxide compounds are used in the cathodes, with layered oxides, such as Li(Ni1/3Co1/3Mn1/3)O2, for example, offering high specific capacity. Given cost conditions, the lowered price Mn-rich compounds tend to be favored by manufacturers over Ni/Co-rich compound alternatives.3 Figures 7 and 11 showcase the primary candidates for anode and cathode materials, respectively.
Quality control of LIBs involves metallographic investigation of the battery’s cap and case, and the spot welding or the electrodes. As these components comprise various materials, they require distinct preparation methods. These various preparation techniques, as well as the target of each preparation, are discussed in the following paragraphs.
Metallographic Preparation of Cap and Casing of the Battery
The battery casing houses both the active and passive components of a battery system, playing a decisive role in determining the energy storage system's functionality, safety, and longevity. Its primary function is to shield these components, some of which are sensitive, from potentially detrimental external factors such as water, moisture, or dust. This safeguarding is essential to ensure the safe and reliable operation of the battery over extended periods of time.
Due to the location of car batteries, often located outside the vehicle cabin usually in the floor area, the housing is exposed to extreme environmental influences, including temperature fluctuations, humidity, splashes of water, salt spray, dust, and even stone chips. Therefore, it is crucial that the housing exhibits high mechanical stability and corrosion resistance, even in the face of harsh external conditions.2
One of the quality control procedures employed for assessing the integrity of the battery casings is metallographic preparation and examination of these components using optical and scanning electron microscopes. The battery cap can be precisely cut using a rotational clamping tool on the cut-off machine Qcut 200 A. Figure 2 illustrates how a sample can be clamped in the machine, permitting the cap cutting and removing the jelly roll.
The preparation method for the casing and the cap of the LIB is detailed in Table 1. The battery cap is often constructed from ferritic steel with nickel-base coating. Proper preparation is essential to eliminate potential artifacts such as edge rounding, damage to the coating due to improper forces or orientations, smearing of the base material, and disruptions to nickel coating, among other possible artifacts. The preparation method outlined in Table 1 is a specialized preparation approach developed by QATM, leveraging specific machines and consumables to ensure the most accurate results following preparation.
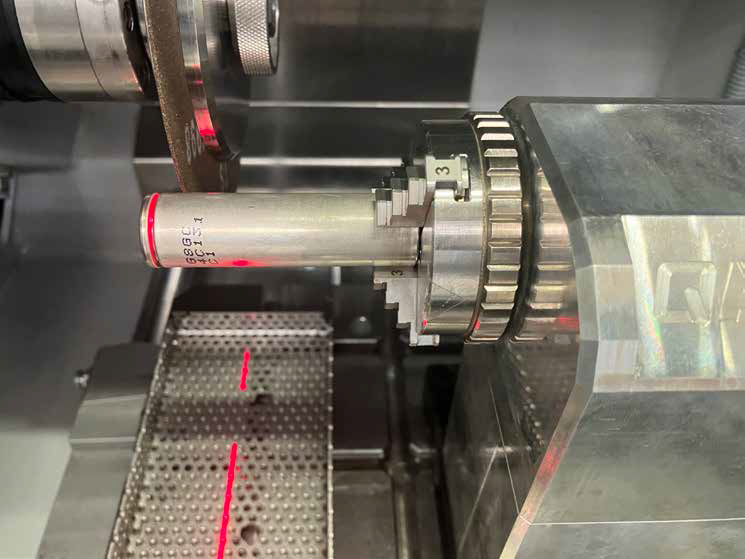
Figure 2. How to clamp the LIB in rotational clamping tool to cut the cap and take the jelly roll out. Image Credit: QATM
Table 1. The developed parameters for grinding and polishing the cap and the casing of LIBs. Source: QATM
EQUIPMENT |
SAMPLE HOLDER |
PRESSURE MODE |
|
|
|
|
Qpol 300 A1 ECO+ |
|
Individual |
STEP |
MEDIUM |
 |
rpm |
 |
Single Pressure N |
min |
Planar grinding |
VEGA 54
μm |
H2O |
SH:
120
WP:
200 |
►► Synchronous
Rotation |
25 |
Till flat surface
(≈1:00) |
Pre-polishing |
BETA |
Dia suspension Poly, 9 μm
+ Lubricant (alcohol-base) |
SH:
120
WP:
150 |
►► Counter
Rotation |
25 |
5:00 |
Polishing |
SIGMA |
Dia suspension Poly, 3 μm
+ Lubricant (alcohol-base) |
SH:
120
WP:
150 |
►► Synchronous
Rotation |
25 |
4:00 |
Final polishing |
OMEGA |
Eposil F 0.1 μm |
SH:
80
WP:
100 |
►► Counter
Rotation |
30 |
1:30
(H2O during final 0:30) |
Etching (electrolyt.) |
Klemm I
3% alcoholic nitric acid |
|
|
|
|
40 s
5 s |
Notes |
SH: The rotational speed of the sample holder
WP: The rotational speed of the working plate
Pre-dosing time for diamond suspension 9 μm and 3 μm and lubricant: 3 s
The dosing interval for dia. suspension 3 μm and 1 μm: each 30 s for 1.5 s
The dosing interval for lubricant 3 μm and 1μm polishing: each 60 s for 1.5 s |
Figures 3 and 4 provide the microstructure of a LIB cap. These caps are composed of coated ferritic steel, as noted in Figure 2. Achieving accurate results requires meticulous attention to meeting correct parameters and the use of appropriate consumables, as improper or wrong forces or consumables can lead to edge rounding and ultimately affect the measurement outcomes.
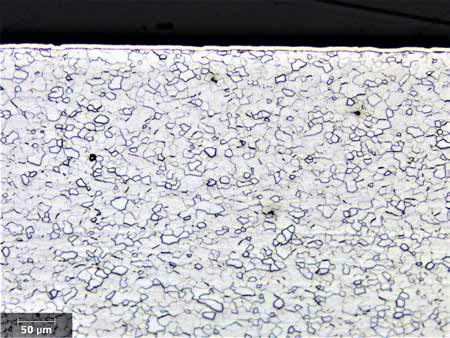
Figure 3. The microstructure of the cap of a LIB after etching with 3% alcoholic nitric acid. Image Credit: QATM
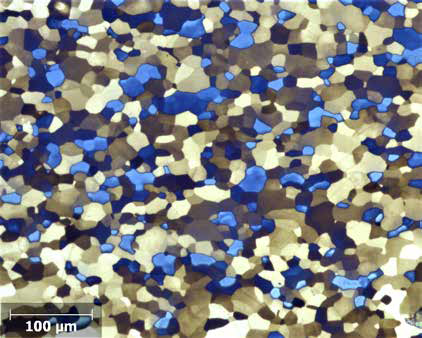
Figure 4. The microstructure of the cap of a LIB after etching with Klemm I. Image Credit: QATM
Figure 5 displays the backscattered electron image from the cap using a scanning electron microscope. An EDS detector in a scanning electron microscope (SEM) can be used to analyze the chemical composition of the coating. Figure 6 illustrates the coating-thickness measurement which was performed using the “QPIX Control 2” software.
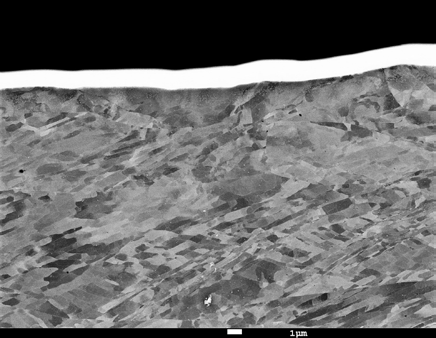
Figure 5. The BSE image of the cap, the coating can be clearly seen on the top. Image Credit: QATM
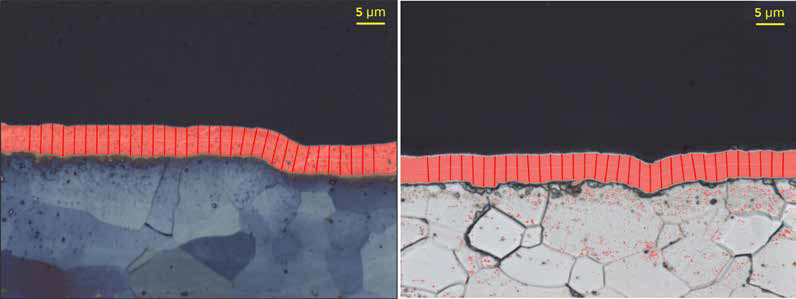
Figure 6. Thickness measurement by QPIX control 2. The final thickness is 5.1 μm. Image Credit: QATM
Further aspects of quality control involve hardness testing of the cap and casing of the LIBs. QATM’s Qness 60 A+ Evo hardness tester can be used to perform hardness testing HV1, as seen in Figure 7, which demonstrates the hardness test results and the locations of the indentations.
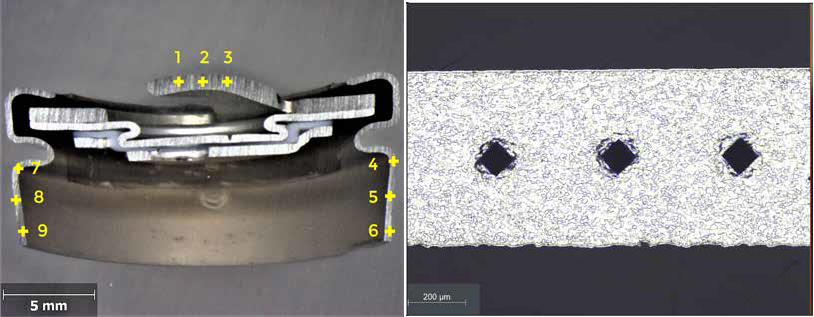
Figure 7. The HV1 hardness test on the cap and the casing of LIB. Hardness of the cap: 117.3 HV / Hardness of the casing: 210.6 HV. Image Credit: QATM
Metallographic Preparation of Anode Foils
Figure 8 illustrates the possible materials used for anodes. In modern LIBs, the standard anode consists of a copper foil acting as the current collector, coated with graphite on one or both sides. This presents a challenge during the preparation of samples, as it is essential to avoid damaging the foil or coating and prevent smearing effects.
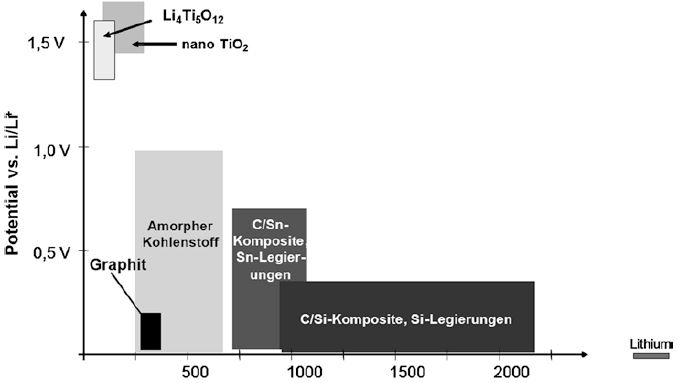
Figure 8. Specific storage capacity and potential versus Li/Li+ of the main anode materials. Image Credit: QATM
Smearing distorts the apparent thickness of the copper foil under the microscope, causing it to appear thicker than it is, and can thus lead to erroneous decisions. Incorrect metallographic preparation can detach the graphite layer from the coating.
The most effective approach for mounting the anode or cathode foils is to utilize Epoxy-resin-base mounting materials. KEM 92, a mounting material from QATM, incorporates epoxy resin. The slow chemical reaction between the resin and the hardener in this cold mounting material ensures the most minimal spacing between the samples and the mounting material. Cold mounting accessories enable the simultaneous mounting of multiple foils in a single sample.
QATM formulated the preparation method outlined in Table 2, which uses specific machines and consumables to ensure the highest level of accuracy in anode foil preparation.
Table 2. The developed parameters for grinding and polishing
of LIBs-anode foils. Source: QATM
Figures 9 and 10 detail the structure of anode foils when examined under an optical microscope. During the metallographic analysis of LIB-anode foils, the connection between coating and foil, the straightness of the copper foil, and other possible manufacturing defects can be investigated.
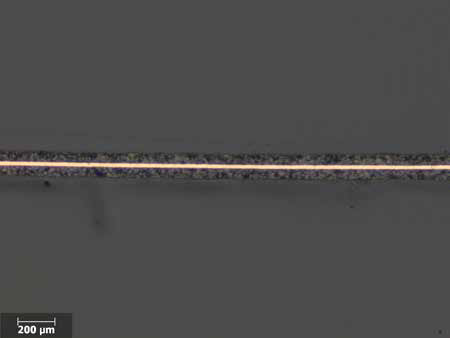
Figure 9. The structure of anode with low magnification. Here the straightness of the copper foil can be investigated. Image Credit: QATM
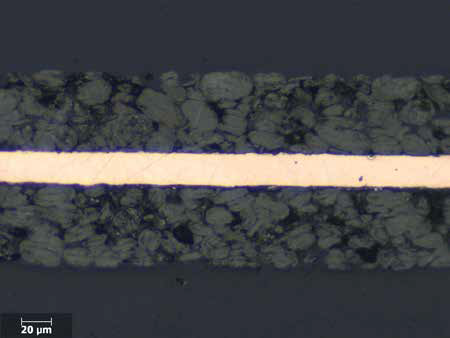
Figure 10. Figure 8 with higher magnification. Image Credit: QATM
Figure 11 illustrates the result of an analysis using an EDX-detector, which allows for the determination of the contained elements.
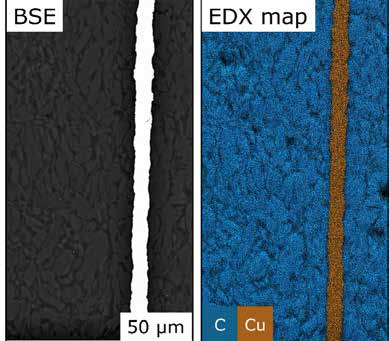
Figure 11. The result of the analysis with the EDX detector. As can be seen, Cu element is determined with orange color and graphite (carbon element) with blue color. Image Credit: QATM
Metallographic Preparation of Cathode Foils
One of the most commonly adopted configurations for cathode materials involves utilizing an aluminum foil as the current collector, which is coated on one or both sides with metal oxide particles such as LiNiMnCo oxides. A visual representation of various cathode materials and their respective properties is shown in Figure 12.
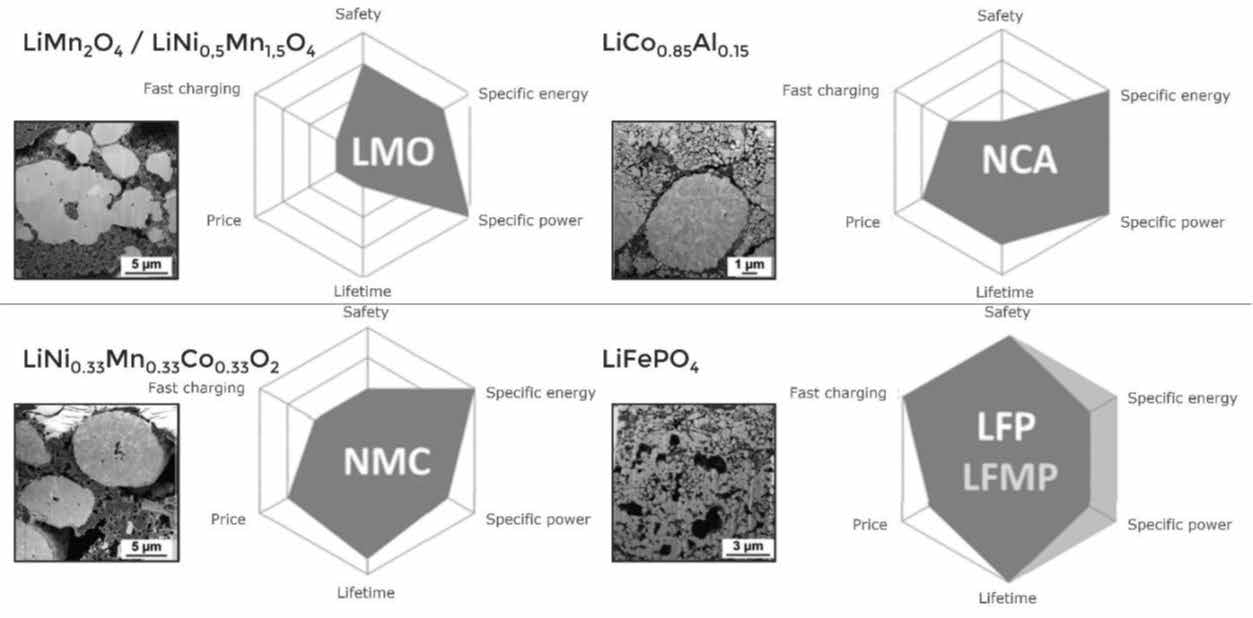
Figure 12. Comparison and FIB cut on different active materials for cathode coating 2,4. Image Credit: QATM
The preparation method outlined in Table 3 is a specialized procedure developed by QATM, utilizing specific machinery and consumables to ensure the utmost accuracy in results following the preparation of cathode foils.
Table 3. The developed parameters for grinding and polishing of LIBs-cathode foils. Source: QATM
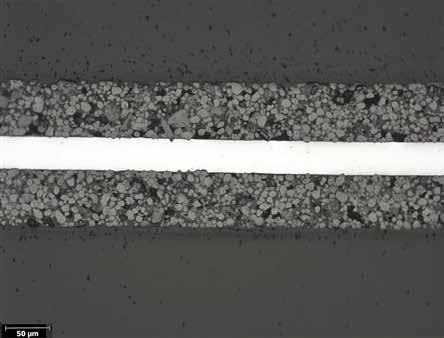
Figure 13. Aluminum foil coated on both sides with metal-oxide particles. Image Credit: QATM
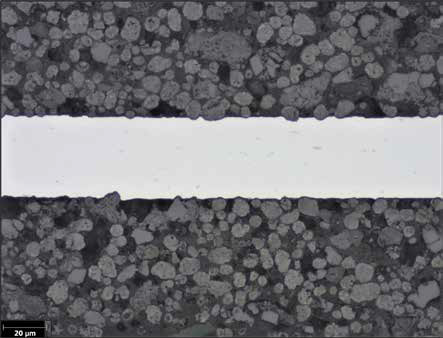
Figure 14. Figure 13 with higher magnification. Image Credit: QATM
The EDX-detector also offers the capability to ascertain the elemental composition of both the current collector and the coating, with the results following EDX analysis presented in Figure 15.
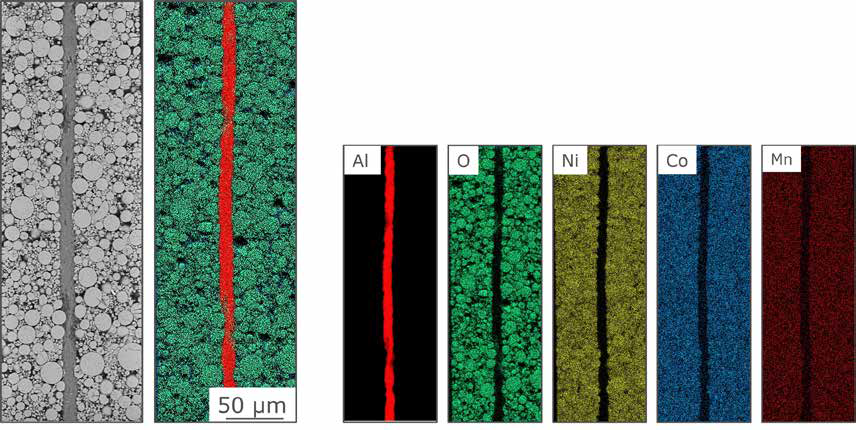
Figure 15. The EDX results for the cathode foil. Image Credit: QATM
Metallographic Preparation of Resistance Spot Welding
Finally, the metallographic preparation of spot weld on the battery cap is paramount, particularly in the aerospace industry. The space flight environment involves inherent sensitivities and risks, particularly concerning the potential for fires within the confined space of the International Space Station (ISS).
In larger battery packs, such as Robonaut 2 (R2), numerous Li-ion cells are arranged in parallel-series configurations to achieve the required stack voltage and desired run-time or to meet specific power requirements. Examining the spot welds in these LIBs is critically significant for upholding safety standards within the ISS.
In this context, the primary concern is avoiding covering pores due to incorrect metallographic preparation. Incorrect parameters can result in the smearing of the material and closure of the surface of the pores.
Table 4 lists the appropriate parameters to be employed during the preparation of these spot welds, while Figure 16 showcases some measurements on these spot welds.5
Table 4. The developed parameters for grinding and polishing of resistance spot welds on the LIBs. Source: QATM
EQUIPMENT |
SAMPLE HOLDER |
PRESSURE MODE |
|
|
|
|
Qpol 300 A1 ECO+ |
|
Individual |
STEP |
MEDIUM |
 |
rpm |
 |
Single Pressure N |
min |
Planar grinding |
SiC paper P320
+ Quick-Tap |
H2O |
SH:
120
WP:
200 |
►► Synchronous
Rotation |
25 |
Till flat surface
(≈1:00) |
Planar grinding |
SiC paper P600
+ Quick-Tap |
H2O |
SH:
120
WP:
200 |
►► Synchronous
Rotation |
25 |
0:45 |
Planar grinding |
SiC paper P1200
+ Quick-Tap |
H2O |
SH:
120
WP:
200 |
►► Synchronous
Rotation |
25 |
0:45 |
Polishing |
SIGMA |
Dia suspension Poly, 3 μm
+ Lubricant (alcohol-base) |
SH:
120
WP:
150 |
►► Synchronous
Rotation |
25 |
5:00 |
Polishing |
ZETA |
Dia suspension Poly, 1 μm
+ Lubricant (alcohol-base) |
SH:
120
WP:
150 |
►► Synchronous
Rotation |
25 |
2:00 |
Notes |
SH: The rotational speed of the sample holder
WP: The rotational speed of the working plate
Pre-dosing time for diamond suspension 3 μm and 3 μm and lubricant: 3 s
The dosing interval for dia. suspension 3 μm and 1 μm: each 30 s for 1.5 s
The dosing interval and length for lubricant: each 60 s for 1.5 s |
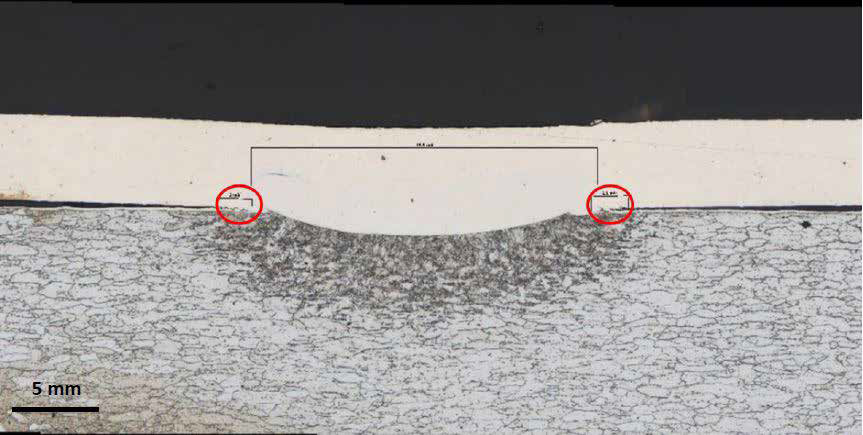
Figure 16. The spot welds on the cap of the battery. The red circles show tiny cracks on both ends of the spot weld. 3 % alcoholic nitric acid has been used as etchant 5. Image Credit: QATM
References and Further Reading
- Matthew Li, Jun Lu, Zhongwei Chen, Khalil Amine. 30 Years of Lithium-Ion Batteries. First published: 14 June 2018 https://doi.org/10.1002/adma.201800561
- Hrsg. Reiner Korthauer. Handbuch Lithium-Ionen-Batterien. Springer-Vieweg Heidelberg 2013. ISBN 978-3-642-30653-2
- Electrochemical characterization and post-mortem analysis of aged LiMn2O4-NMC/ graphite lithium-ion batteries part II: Calendar aging. Barbara Stiaszny, Jörg C. Ziegler, Elke E. Krauß, Mengjia Zhang, Jan P. Schmidt, Ellen Ivers-Tiffée. Journal of Power Sources 258 (2014) 61-75
- Li-Ionen Batterien – ein Blick durchs Mikroskop. Andreas Kopp, Jan Niedermeier, Andreas Jansche, Florian Trier, Olatomiwa Badmos, Timo Bernthaler, Gerhard Schneider, Hochschule Aalen, Institut für Materialforschung (IMFAA). Hochschule Aalen.
- Metallography of Battery Resistance Spot Welds. James E. Martinez, Lucie B. Johannes, Sandeep Yayathi, Joshua M. Figuered, Zoran M. Bilc. National aeronautics and space administration.
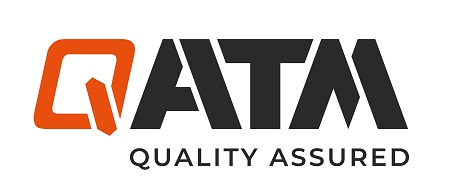
This information has been sourced, reviewed and adapted from materials provided by QATM.
For more information on this source, please visit QATM.