The biomedical device industry is experiencing growth, leading to increased demand for mechanical testing equipment. Manufacturers have had to expand their production to meet the rising need for medical consumables and safety equipment, which tripled during the COVID-19 pandemic.
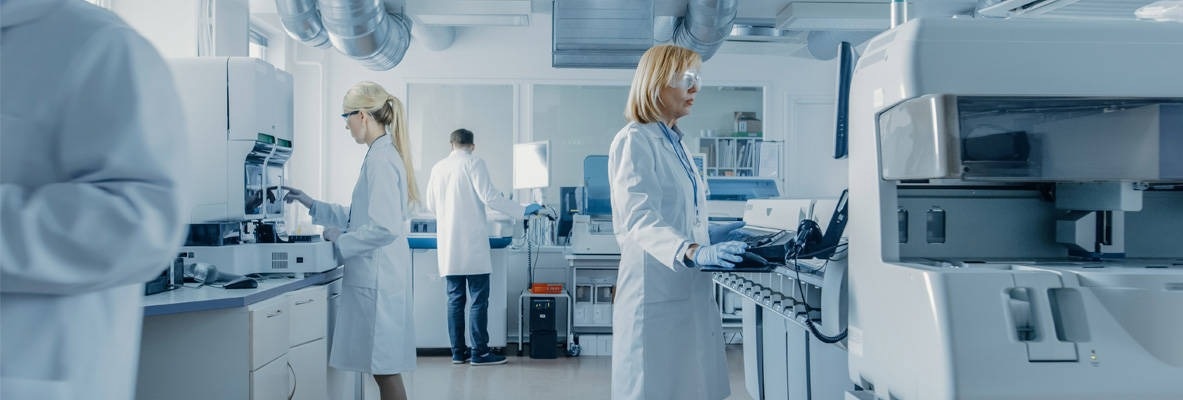
Image Credit: Instron - USA
The greater need for laboratory efficiency requires technicians to conduct more tests. However, variations introduced by human operators, such as differences in device insertion and alignment, can vary from one operator to another and from one test to another.
These individual disparities can significantly impact the consistency of test results. Automated testing systems can provide a solution in such cases.
What Do the Standards Say?
To demonstrate compliance with requirements established by governing bodies like ASTM and ISO, medical devices' mechanical properties and functionality must be evaluated in laboratory settings.
For instance, Luer connections must undergo torsion testing to ensure their strength for intended applications. Autoinjectors must pass various mechanical tests, including the needle shield's activation force, injection time, and lock-out force.
Mechanical tests applied in biomedical contexts are subject to stringent international standards based on various classifications. Examples include:
- ISO 80369 for torsion testing of Luer locks
- ISO 11608 for pen and auto-injectors
- ASTM F3014 for penetration testing of curved needles
- Functional testing of syringes to ISO 11040
- Residual seal force testing of vials
- EN 455-2 to determine the tensile properties of medical gloves
These standards are dynamic and subject to ongoing enhancements by regulators to improve safety and test method quality and to adapt to new technologies and materials.
For instance, the Directorate-General for Health and Food Safety introduced Regulation (EU) 2017/746, ensuring the safety and performance of medical devices within the European Union (EU) market.
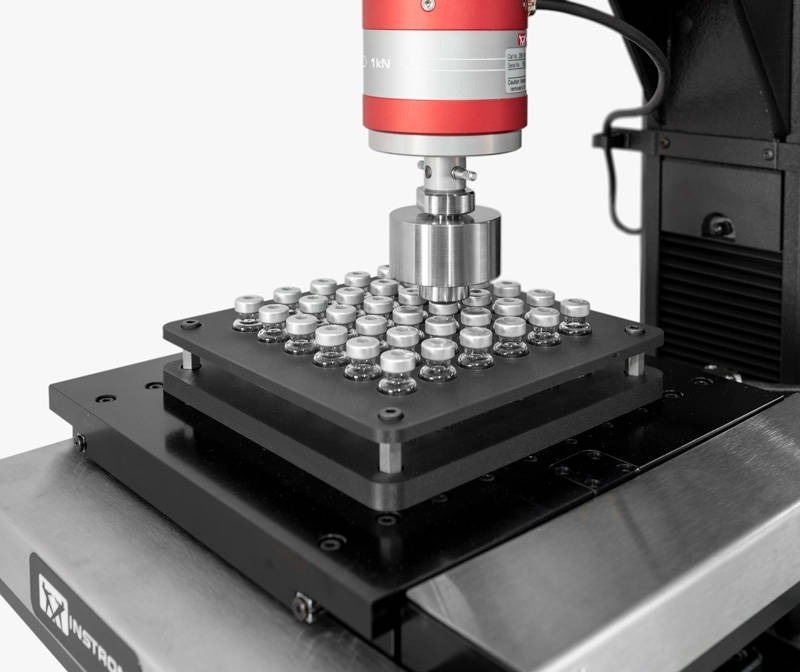
Residual Seal Force Testing Using the AT2 Automated XY Stage. Image Credit: Instron - USA
Key Mechanical Testing Challenges
Meeting the rigorous quality and safety standards of biomedical device manufacturing presents significant challenges. Aside from variability in results due to human errors, regulations and test standards undergo frequent updates.
Therefore, technicians must continuously train to maintain proficiency with the latest approved methods.
Biomedical device manufacturers face occupational health concerns, including potential exposure to hazardous materials. For example, test specimens like syringes can break or shatter during testing, leading to cuts and abrasions.
Ergonomic issues arise when repetitive actions such as loading and unloading specimens are performed, potentially leading to musculoskeletal disorders if the test station's ergonomics are inadequately designed. Automating some or all of the mechanical testing processes can effectively address these challenges.
Automation Is Here to Stay
Numerous factors propel the current surge in automation within the expansive biomedical device sector, a trend substantiated by market research reflecting its swift growth. Researchers anticipate an annual growth rate exceeding 9% from 2023 through 2030.
A prominent instance of this trend emerged during the COVID-19 pandemic when the imperative to bolster manufacturing capacity became evident. Biomedical companies, in response to the pandemic's peak, tripled their production of auto-disable (AD) safe-injection devices to support widespread vaccination efforts in various nations.
The pandemic's supply chain disruptions prompted certain manufacturers to re-evaluate the geographical locations of their production facilities. While reshoring addresses this challenge, it can elevate manufacturing expenses due to increased labor and energy costs.
For this reason, companies embracing reshoring strategies tend to integrate higher levels of automation. As a result, the biomedical device sector is beginning to adopt technologies already prevalent in other industries. For instance, the automotive industry extensively employs robots and collaborative robots (cobots).
This technological shift bears substantial potential for biomedical laboratories, as robots and cobots excel in executing repetitive tasks with remarkable consistency. Leveraging this technology enhances the reliability of test results in biomedical laboratories.
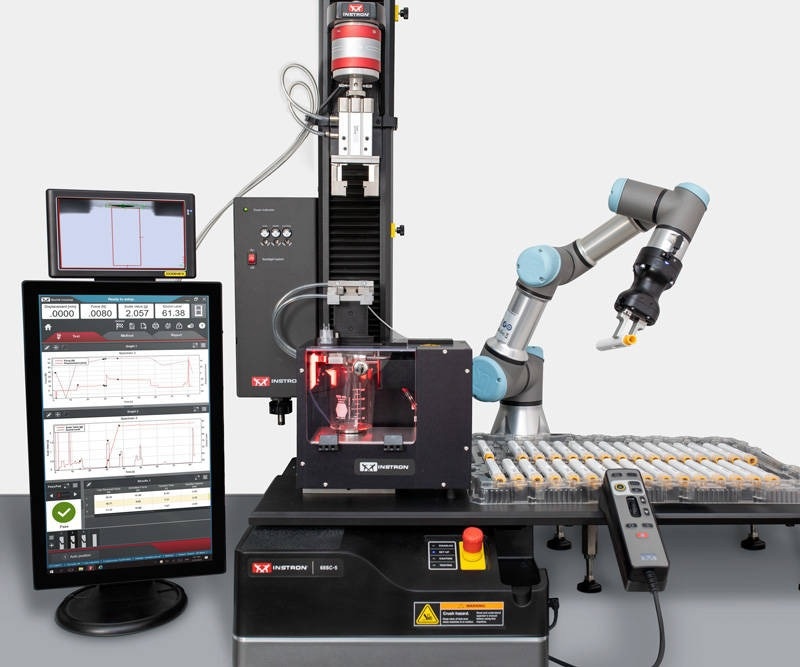
Testing Auto-Injectors on a CT6 Cobot Testing System. Image Credit: Instron - USA
Conclusion
The growth of the biomedical device industry places heightened demands on manufacturers and laboratories to enhance their production capabilities. Nonetheless, the industry operates within a framework of rigorous international standards and regulations that impose stringent criteria for both quality and safety.
The pursuit of increased throughput challenges the biomedical industry in meeting these demanding standards. The automation of mechanical testing in laboratories can provide valuable assistance to the biomedical industry in surmounting these challenges and satisfying the escalating demands of the market.
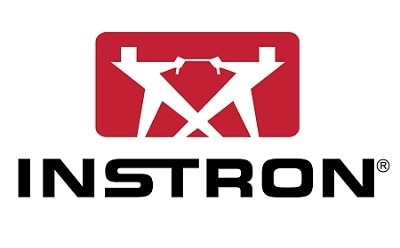
This information has been sourced, reviewed and adapted from materials provided by Instron - USA.
For more information on this source, please visit Instron - USA.