The production of auto-disable (AD) safe-injection devices constitutes a core activity for numerous contract development and manufacturing organizations (CDMOs). Mechanical testing assesses the safety and efficacy of AD syringes before their introduction to the market.
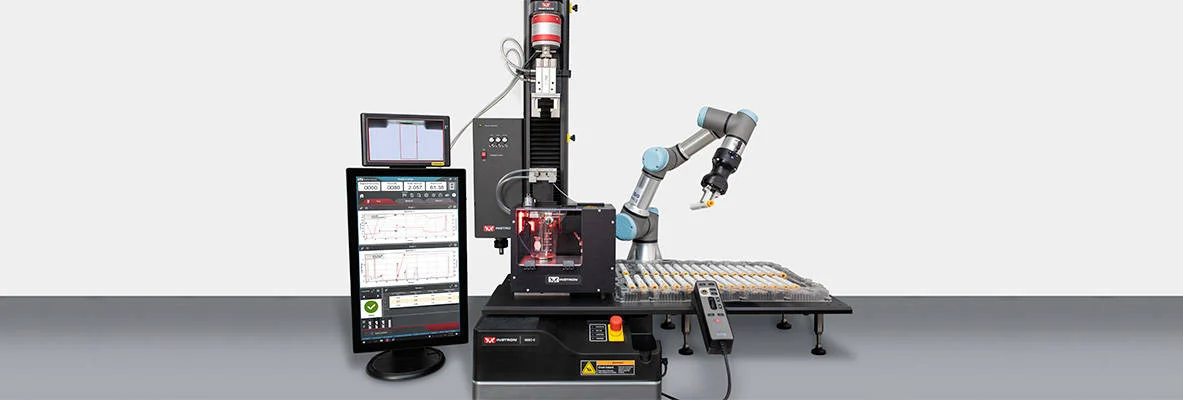
Image Credit: Instron - USA
With the AD device industry anticipated to reach a value exceeding $13.3 billion by 2028, laboratories within CDMOs are poised to conduct more frequent and extensive testing procedures.
In this context, the potential of cobot-based systems is explored in assisting these laboratories to manage expanding workloads efficiently while upholding precision and consistency.
Step 1 – Understand Your Lab’s Needs
Laboratories within CDMOs operate in dynamic settings, dealing with many diverse customer products, each with unique demands.
Flexibility and reliability become pivotal factors when choosing a mechanical testing system. The chosen machine must possess the following attributes:
- Compatibility with multiple testing methods and processes to accommodate varying customer specifications
- Assurance that the samples meet dose accuracy standards such as ISO 11608-1 and internal benchmarks
Discrepancies from human error could instantly halt production, leading to protracted troubleshooting delays.
Given these challenges, transitioning to an automated system, optimizing flexibility, and reducing the risk of human errors appears intuitive. Nevertheless, not all automated solutions are created equal, and a universal approach is unavailable. In light of this, the key factors to evaluate before adopting an automated system include:
- Expected testing volume
- Testing frequency
- Changeover frequency
- Level of production integration
- Data collection and storage
- Specimen/sample information
- Physical space constraints
Step 2 – Choose The Right Automation for Your Lab
Upon a comprehensive assessment of the laboratory's requirements, the next step involves identifying the automation system that aligns with these prerequisites. Automated solutions span from uncomplicated two-axis stages to sophisticated six-axis robotic systems.
Nevertheless, cobot-based systems typically represent the optimal choice for CDMO laboratory environments.
For instance, Instron's CT6 cobot test system offers easy programming and effortless adaptability for testing diverse product specimens. Only a few simple adjustments to the load/unload sequence are required.
Accessories also hold significance. For instance, a pneumatic load-controllable gripper on the cobot proves ideal for managing a broad spectrum of AD devices. This feature ensures consistent handling of every specimen, irrespective of its geometry, during testing, minimizing variations.
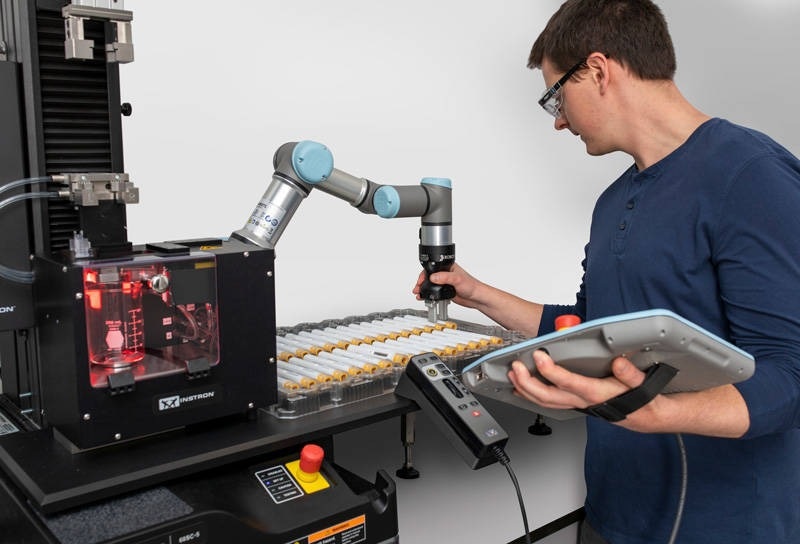
Image Credit: Instron - USA
Step 3 – Set Up for Success
With the selection of the cobot-based testing system complete, the focus now shifts to the setup process. Users should consider the location, including the layout of the laboratory space, and how samples are incorporated into the system.
For instance, if testing is fully integrated into the manufacturing workflow, placing the cobot near the production line may necessitate it.
The loading procedure also warrants careful consideration. Advanced cobot systems like the CT6 allow grips and specimen trays to be customized for multiple AD devices.
The system can be tailored to function seamlessly with device trays directly from the production line, minimizing setup time. All that is required is the provision of the correct tray dimensions to the supplier to ensure the incorporation of features that centralize it within the workspace.
Step 4 – Make The Most of Your Data
The latest mechanical testing automation technology advancements yield a wealth of insightful data. Effective utilization of this data is crucial for enhancing efficiency, throughput, and repeatability over time. Below are some valuable tips for optimizing data usage:
- Utilize barcoding – This method facilitates the automatic entry of relevant data, expediting the entry process and reducing errors.
- Opt for pass/fail criteria – This feature enables easy management of alternate workflows to segregate defective components from the rest of the batch.
- Leverage Bluehill Central – This software, developed by Instron, ensures proper segregation of client data into distinct groups for storing methods, samples, and test reports.
Step 5 – Simplify Maintenance
One advantage of automation in AD device testing is that cobots require minimal maintenance. In a typical syringe testing application, specimens are usually significantly lighter than a cobot's capacity, ensuring the system is not subjected to undue strain.
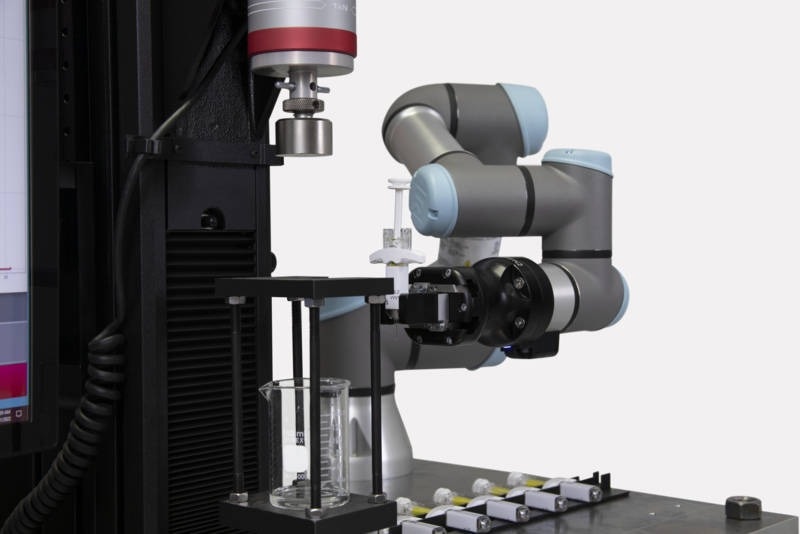
Image Credit: Instron
For instance, many smaller-capacity cobots on the market have a 3 kg capacity, while most AD devices weigh less than 250 g. Specific essential maintenance procedures are necessary to minimize downtime and extend the system's lifespan. Firstly, daily gripper fingers and racking cleaning is vital to ensure proper functioning.
Dust and dirt may accumulate on the gripper fingers, making specimen handling more challenging and increasing the risk of mishandling. Rubber fingers can also cause specimens to adhere and require more frequent cleaning.
Another crucial maintenance routine involves a monthly inspection of all cabling, ventilation, and airflow to assess their condition.
It is advisable to regularly check the tightness of screws and bolts, at least every month. The repetitive motion of automation systems can gradually loosen screws and bolts over time, even those equipped with thread lockers.
Conclusion
Mechanical testing automation is here to stay, with cobot-based systems offering a versatile and efficient solution to various challenges encountered by testing laboratories in CDMOs.
As the demand for AD syringes continues to expand, cobot-based systems can assist laboratories in efficiently handling increased customer requests, maximizing test accuracy and throughput.
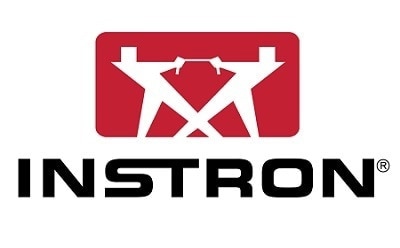
This information has been sourced, reviewed and adapted from materials provided by Instron - USA.
For more information on this source, please visit Instron - USA.