Frequent flyers often underestimate how much engineering goes into making sure that the welded components of the aircraft they are boarding stay together.
The aluminum-based alloys used for most aerospace applications are specifically designed to weld together in a reliable way, and different welding techniques have been invented to improve weld reliability.
In this article, we will highlight the methods that Yanan Hu et al. used to investigate the performance of a hybrid welding technique on 7000-series aluminum alloys,1 along with their resulting design improvements for a hybrid welding technique.
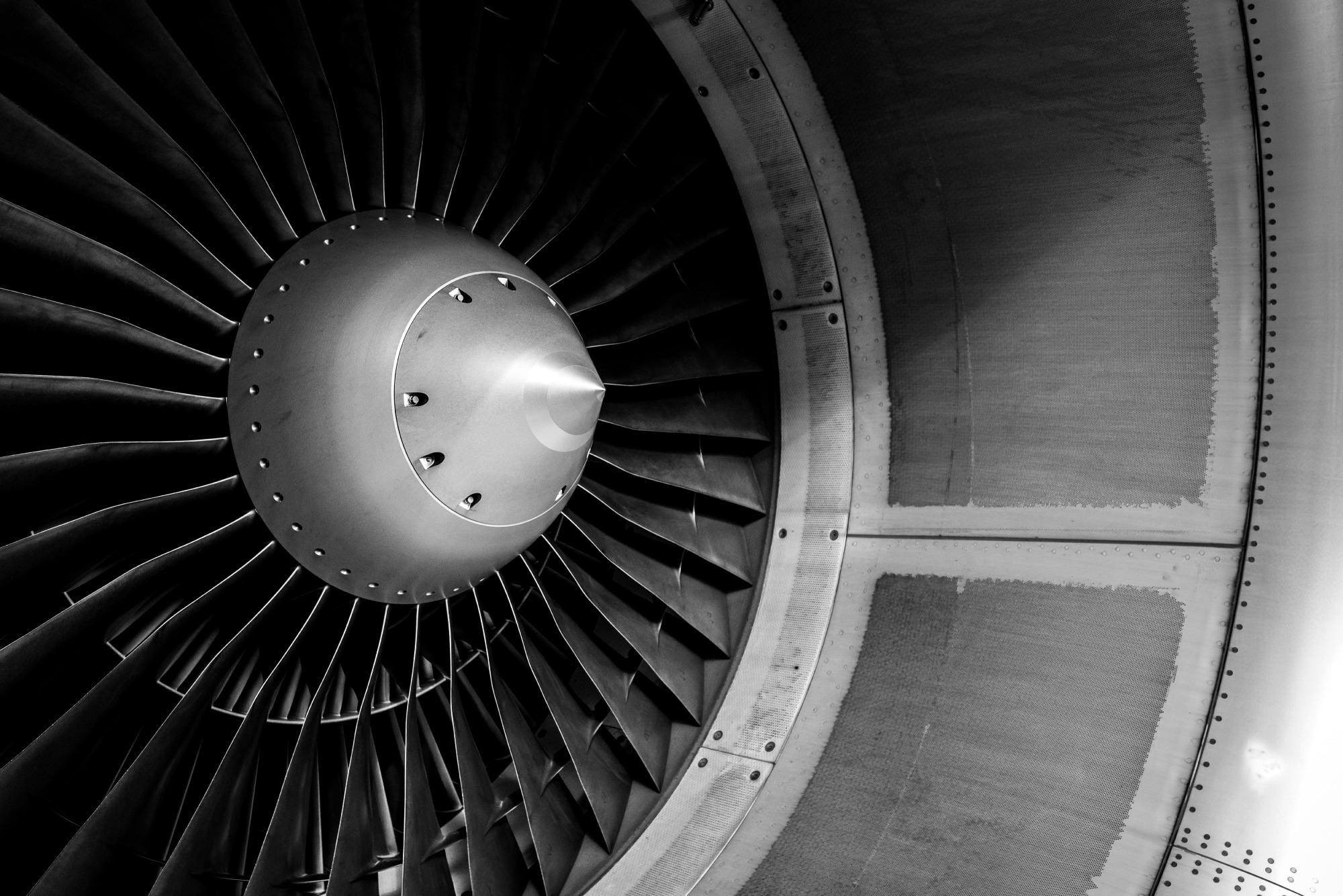
Image Credit: Bychykhin Olexandr/Shutterstock.com
How and Where to Measure Crack Formation
The focus of this study was primarily on the behavior of the fine equiaxed zone (FQZ), which displayed strength reduction over prolonged material usage. To observe the formation of damage in the region of interest and to assess the material crystallography after welding, a wide range of techniques were utilized:
- Micro-computed tomography (µCT) and synchrotron radiation imaging provided visual data on the region of interest
- Electron backscatter diffraction (EBSD) and electron-probe micro-analysis (EPMA) were used to characterize the crystallography of the region
- Transmission electron microscopy (TEM) provided images of the precipitates in the FQZ
- Finally, image processing software was used to identify and measure features of interest
To clearly observe the damaging mechanism, two microcylinders of material were extracted from the core sample, which underwent an applied stress of 270 MPa. The cylinders had a diameter of ~40 micrometers, which allowed them to be imaged at high resolution with synchrotron X-Ray nano-CT; samples of this size required plasma-focused ion beam (PFIB) milling for sample preparation.
X-Ray nano-CT enabled the observation of nanopores, ranging between 100–500 nm in equivalent diameter. These pores preferentially nucleate and grow perpendicular to the stress along the direction of the weld.
Image processing tools were then used to identify and measure the pores, as well as to create a surface mesh. The models could then be transferred to multi-physics software for material stress-response modeling.
The regions of the sample that could not sustain the plastic transformation were further inspected with spectroscopic techniques to assess their chemical composition. A large number of MgCuAl phases were observed, which were characterized by increased brittleness compared to neighboring areas. This is what eventually led to cracking when stress was applied.
Currently, there is no method to remove the FQZ entirely, but there are ways to mitigate its negative effects.
A New Welding Procedure
A novel welding technique was developed that utilizes an oscillating laser beam immediately followed by a pulsed magnetic field (OSHW + m). This produces a more fragmented FQZ, with individual pieces displaying a curved shape.
A 20% increase in tensile strength was observed for this newly welded material compared to HLAW methods. This is a 60% increase compared to GMAW methods. The weld can resist up to 470 MPa, which is slightly better than the resistance of comparable modern stir welding (at 450 MPa) when subjected to comparable aging treatments (3,000 hours).
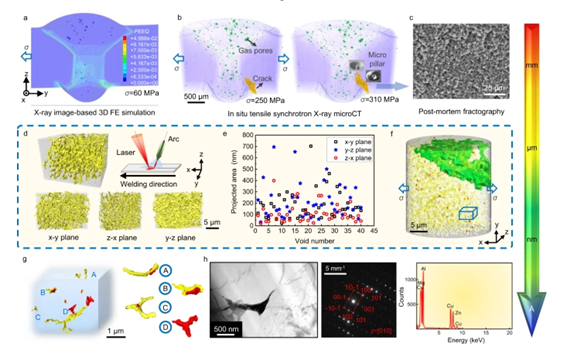
Multiscale correlative tomography workflow used to detect damage nucleation and evolution inside the FQZ.1 Image Credit: Hu, Y, et al. https://doi.org/10.1038/s41467-022-33188-x
From Imaging Data to Numerical Conclusions
Combining multiple imaging and spectroscopy techniques produces large volumes of different data. Image processing software is often crucial for making sense of all this information, providing a clearer view of the bigger picture.
Thermo Scientific™ Avizo™ Software offers a range of visualization and data analysis tools to correlate multiple data types, generating a comprehensive picture of the analyzed material.
Yanan Hu et al. utilized the segmentation tools of Avizo Software to identify and measure their features of interest (pores, particles, fibers, cracks, layers, etc.) in a time-effective manner, in multiple dimensions and using multiple data sources as input.
Learn more: Introduction to Avizo Software for metals and alloys characterization
References and Further Reading
- Yanan Hu, et al. Inhibiting weld cracking in high-strength aluminium alloys. Nature Communications 13(1), 1–9 (2022). doi: 10.1038/s41467-022-33188-x
- Kumar Rajak, D, et al. Friction-based welding processes: friction welding and friction stir welding. Journal of Adhesion Science and Technology 34(24), 2613–2637 (2020). doi: 10.1080/01694243.2020.1780716
- Lohwasser, D and Chen, Z. (Editors). Friction Stir Welding: From Basics to Applications. Elsevier (2009). https://www.elsevier.com/books/friction-stir-welding/lohwasser/978-1-84569-450-0
- Yanan Hu, et al. Review on failure behaviors of fusion welded high-strength Al alloys due to fine equiaxed zone. Engineering Fracture Mechanics 208, 45-71 (2019). doi: 10.1016/j.engfracmech.2019.01.013
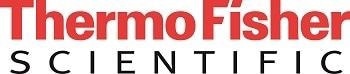
This information has been sourced, reviewed and adapted from materials provided by Thermo Fisher Scientific - Software.
For more information on this source, please visit Thermo Fisher Scientific - Software.