Companies are increasingly prioritizing the energy optimization of their production. The scrutiny of technical facilities and procedures is integral to reducing costs and increasing the sustainability of operations through more efficient resource utilization.
Operators with high energy consumption possess an exceptionally potent tool for achieving greater efficiency.
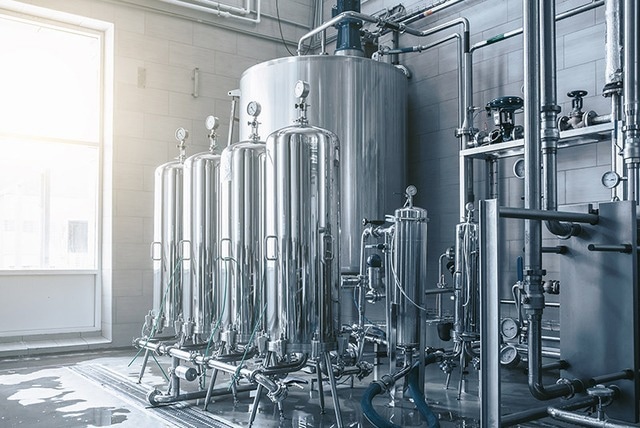
Image Credit: Aerzener Maschinenfabrik GmbH
In addition to employing smart plant control and highly efficient compressors and blowers, the focus shifts toward heat recovery systems. A substantial portion of the energy in generating compressed air naturally transforms into heat.
However, companies can extract substantial heat energy from the air for various purposes with minimal capital investment. Heat is used for heating, hot water preparation, and immediate production needs in the food industry.
You can achieve maximum efficiency increases by implementing a comprehensive heat concept for your compressed air plant with the solutions from AERZEN. This works for new plants but can also be realized for existing systems with only minimal effort and expenditure.
Compressed Air Generation Heat Development Unavoidable
Energy efficiency plays a pivotal role in the profitability of compressed air generators. AERZEN, a specialist in process air, addresses this challenge by offering efficient consulting and service solutions, ensuring cost-effective operation throughout the products' lifecycle.
Strategies for boosting efficiency in process air aim to optimize energy utilization for compression, reduce pressure losses, and adopt cost-effective maintenance approaches.
Monitoring plant performance continuously through smart systems is also crucial, but heat recovery remains the most promising avenue for enhancing efficiency.
Heat Sources in The Compression of Process Air
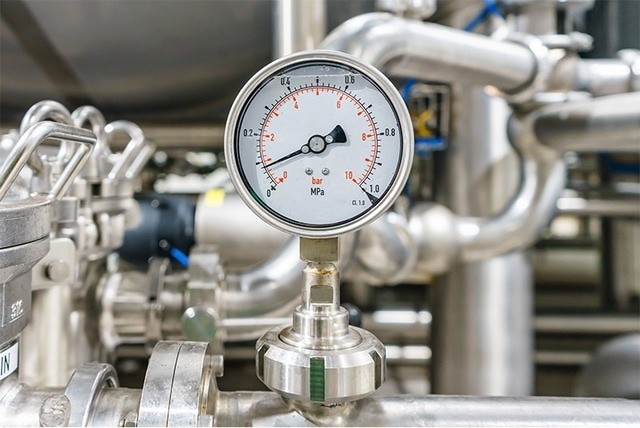
Image Credit: Aerzener Maschinenfabrik GmbH
In the compression of process air, a significant portion of the energy is converted into thermal energy. Air compression generates high temperatures, reaching up to 280 °C using screw compressors. In the absence of heat recovery, fans expelled unnecessary heat into the environment.
A portion of the energy also dissipates from the process air into the surroundings through the pipe system.
Depending on the plant, operators can recover up to 85% of this valuable energy and apply it to various operational uses. Heat transfer from air to water ensures flexibility, realized through special heat exchangers downstream from the compressor stage in the process air system.
These heat exchangers cool the air and transfer the heat to the water, which is used as a conveying medium. Some of the energy used accumulates as heat under the compressor's acoustic hood.
The motor, silencer, and compressor emit heat from friction losses, for example, into the air. The exhaust air reaches temperatures between 30 and 60 °C, which can be used as heat for nearby office premises or production areas without further conversion.
To achieve this, AERZEN equips its blowers and compressors with exhaust ducts to gather the heat, which then enters connected rooms through controlled flaps.
Technical Solutions for Heat Recovery
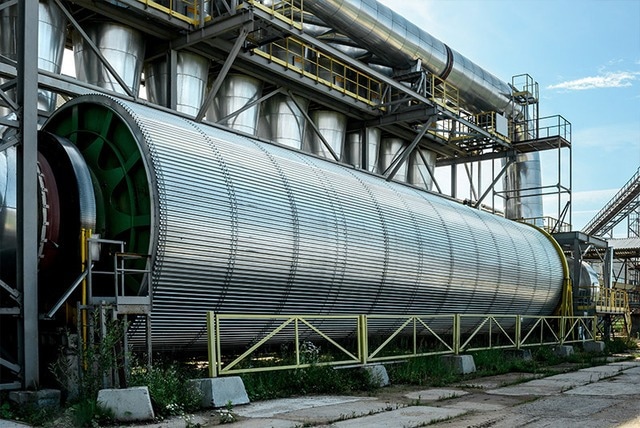
Image Credit: Aerzener Maschinenfabrik GmbH
The process air itself holds significant potential for heat recovery. In many cases, the air undergoes multiple treatment stages following the compressor. Filters, aftercoolers, and dryers align the air's properties with the specific process requirements.
The primary components for heat recovery are the aftercoolers. The hot process air circulates them, and there are water-air design options suitable for high-temperature ranges. These designs transfer heat from the air to the cooler water.
Operators can directly use this heated water for their processes, or transfer the energy to another medium.
Common applications in food companies include room heating, hot water treatment, and process heat. AERZEN relies on compact pipe bundle heat exchangers for its aftercoolers with heat recovery.
The compressed medium passes through the cooler pipes, which are surrounded by cooling water flowing in the opposite direction. This design optimizes flow and minimizes pressure drops in the process air system.
This, in turn, enhances overall efficiency, as blowers or compressors must compensate for pressure loss, which consumes additional energy. Powerful process air circuits reliably provide compressed air of the required quality.
Integrated heat recovery also boosts energy efficiency and sustainability. Precisely adjusting individual components to the overall system is essential for this, and AERZEN uses a design tool for consulting to select the appropriate device for both new and existing plants.
Making Waste Heat Usable
While recovering heat by transferring energy from process air to water is a crucial step, the potential for savings becomes financially and ecologically viable when optimizing the use of the recovered energy.
Identifying the process(s) with the most significant heat demand that can be effectively supplied with energy is essential. Several criteria should be considered during the selection process:
- Spatial proximity between heat source and sink
- Reliable supply of the recipient process
- Synchronization of heat generation and demand
- Sufficient temperature difference between media
Applications for Process Heat
Most plants can employ the reclaimed heat for sanitation or heating purposes. At temperature levels ranging from 70 to 90 °C, water can effectively replace a heating boiler as the heat source. Various processes in the food production industry make use of hot water and steam for tasks like:
- Heating
- Cleaning
- Pasteurization
- Sterilizing
In such cases, the energy harnessed from the process air system typically preheats the medium. However, if the cooling water temperature falls below the desired level for the process medium, it may not fully substitute the primary heat generator.
Significant energy cost savings are promptly realized by utilizing the reclaimed heat. For optimal heat transfer, there should be a temperature difference of at least five, or ideally 10, Kelvin between the water from the heat exchanger and the target medium.
Heat recovery must provide a continuous heat supply to support connected processes. This way, the expenses for installing heat exchangers and pipelines pay off quickly, making the system an appealing option, even for small, continuously operating plants.
The consistent heat flow recovery also has potential benefits in planning new or replacing existing main heat generators for the target process, allowing for the reductions of the capacity reserves for peak heat requirements.
On the other hand, an unstable heat supply from the process air plant may necessitate a more efficient steam generator. Time gaps between heat generation and its usage result in costly intermediate storage and significant energy losses.
The structural conditions are another factor in choosing the heat sink. Longer transport routes between heat recovery and the process increase line costs and energy losses during transportation.
Integrated Solutions Are Called For
Sustainable process air systems now incorporate an integrated heat recovery system. The considerable economic and ecological advantages offset the manageable expenditure in a very short time.
This enables plant operators to continue to reap long-term economic benefits from their older installations. Subsidy opportunities, such as those offered by the Federal Office for Economic Affairs and Export Control (BAFA) with its energy efficiency funding program, can expedite the amortization process.
Eligible measures span from retrofitting master system controls and heat exchangers to designing new installations. Employing high-quality heat exchangers and control systems at the heat source is essential for designing an effective heat recovery system.
The incorporation of user processes is at least equally important. Only the efficient interconnection of sources and sinks will have a conclusive effect on the efficacy of the entire system.
AERZEN provides consultation, accessories, and maintenance from a single source, utilizing the company's own heat recovery devices as a foundation. These devices can be retrofitted flexibly, enabling the energy optimization of older installations.
AERZEN fulfills its commitment to creating lasting value for its clients through its process air systems. The in-house application specialists assist customers in component sizing.
AERZEN also offers the option of installing its system monitoring solution for real-time information crucial for optimal operation and maintenance, should customers request it.
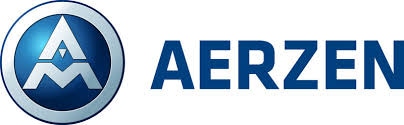
This information has been sourced, reviewed and adapted from materials provided by Aerzener Maschinenfabrik GmbH.
For more information on this source, please visit Aerzener Maschinenfabrik GmbH.