Industrial food production heavily relies on using process air to handle and process raw materials, intermediate products, and end products.
Compressed air also plays a vital role in various other processes, including loading and unloading transport equipment, storage, loosening and sorting operations, and packaging.
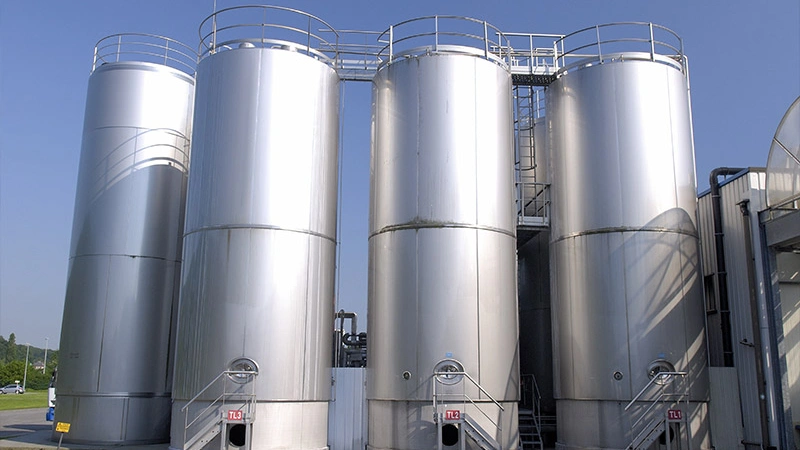
Image Credit: Aerzener Maschinenfabrik GmbH
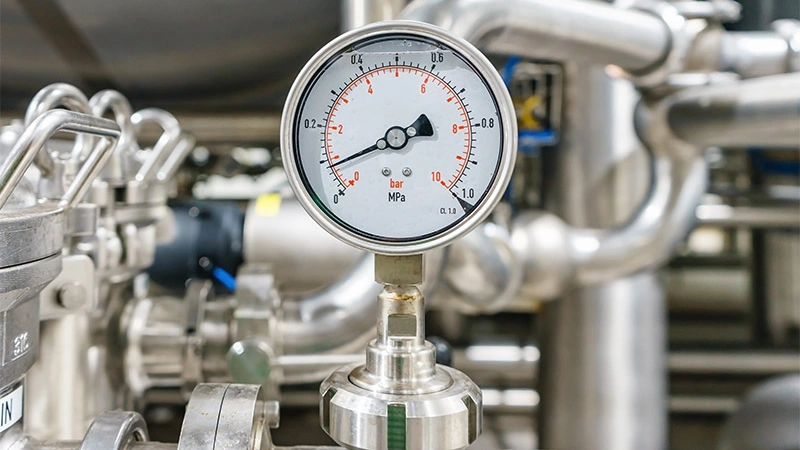
Image Credit: Aerzener Maschinenfabrik GmbH
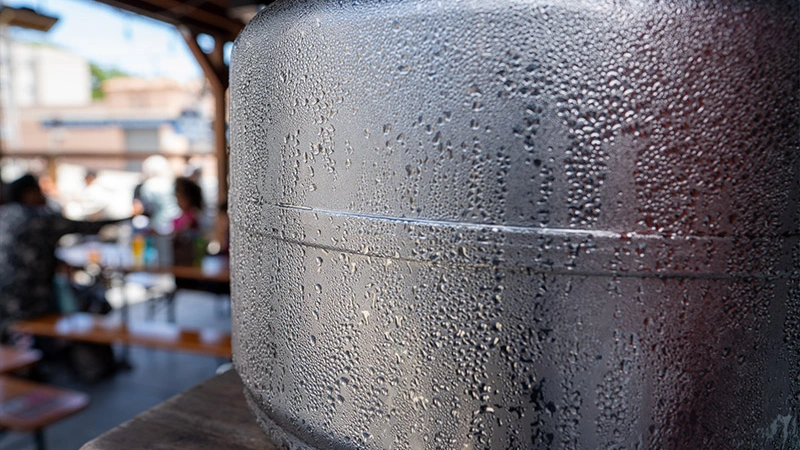
Image Credit: Aerzener Maschinenfabrik GmbH
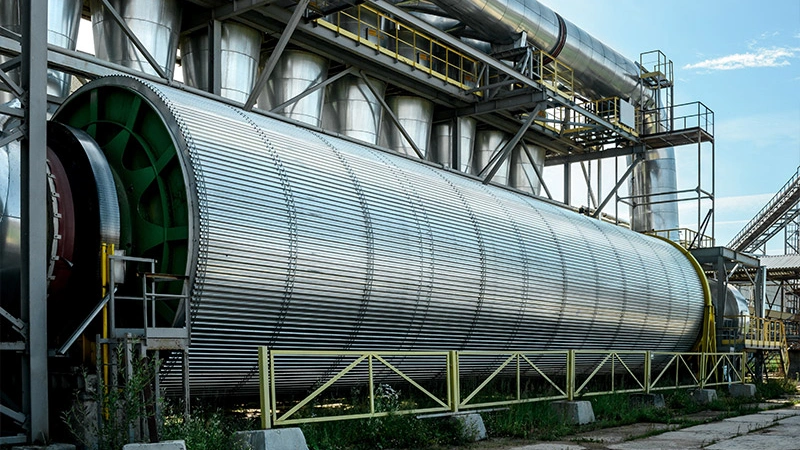
Image Credit: Aerzener Maschinenfabrik GmbH
The Challenge of Humidity in Process Air
In pneumatic handling processes, excessive humidity in the process air can cause multiple issues because the process air frequently comes into direct contact with the product. Within the food processing industry, they work with hygroscopic items like sugar, cocoa, starch, and spices.
When these absorb moisture, it promotes bacterial growth and can result in losses depending on how long the materials are stored. The material can harden in silos' corners. Elevated humidity significantly hampers material handling.
Humid bulk material has a lower flow rate, leading to potential blockages in delivery pipes and causing production downtime or delays. Product build-ups on system components make processing more challenging, directly increasing user production costs.
Temporary solutions to manage materials that tend to stick together include using mechanical devices like hammers or vibration plates.
However, these measures typically offer only short-term relief, and the adverse effects caused by moisture absorption during storage, transport, and processing persist.
To address the issue, ventilated containers and drum dryers are employed for food drying. The basic principle involves passing drying air over the materials and extracting moisture from the bulk material. When the air cools down, condensate forms, which can be intentionally removed from the process.
In a closed system, much of the heat generated during process air compression can be effectively recovered.
Devices for process air drying either upstream or downstream of the blower or compressor present an efficient solution, especially when moisture infiltrates during pneumatic conveying. These devices can adjust humidity per the user's process requirements or lower the dew point.
These machines must operate flexibly, as the atmospheric air's humidity content varies throughout the day and across seasons.
Process Air Drying in Detail
The process air dryer fine-tunes the relative humidity and dew point of the compressed medium. It is important to understand that the ability of the air to absorb a certain quantity of water vapor depends on the air temperature and pressure.
The relative humidity indicates how saturated the air is with water vapor, based on its maximum capacity. If the temperature decreases while air moisture stays constant, relative humidity goes up. Once the temperature hits the dew point, relative humidity reaches 100%.
Further temperature drops can lead to water vapor condensation. Low dew points and low relative humidity are the goals of process air drying.
Plants for Drying Process Air
When relative humidity hits 65%, the risk of mold developing in bulk materials due to process air increases. This is when drying equipment is necessary, preferably at the material acceptance stage.
Dried air, free from moisture, ensures bulk materials remain dry. During storage in the silo or storage room, dehumidified air prevents the raw material from clogging.
Condensation dryers are adequate for applications with less stringent humidity requirements. In these cases, water vapor in the air condenses on cooling surfaces or heat exchangers.
A condensation dryer cannot achieve relative humidity below 50% at room temperature or dew points below 10 °C. For process air applications handling moisture-sensitive hygroscopic substances, like those in the pharmaceutical industry, sorption or refrigeration drying is needed.
Sorption-based air drying requires minimal air temperatures. It involves a sorbent that removes moisture from the air. After compression, the air goes through a precooler, which brings the air temperature to the lower set level.
The process air then flows through a rotating rotor coated with the hygroscopic sorbent. This binds the water vapor so that the escaping medium has a reduced moisture content. Without sorbent regeneration, the rotor would become permeable to water vapor over time.
Therefore, another airflow releases the water molecules stored in the rotor, using temperatures of up to 130 °C, albeit at a lower volume flow.
Energy Efficiency with Process Air Drying
Energy efficiency is a critical aspect of sorption-based process air drying, particularly during regeneration, which demands high temperatures. Heat energy typically comes from electrical heating registers or gas burners.
To lower energy loss to the greatest possible extent, modern plants use warm exhaust air to preheat the newly supplied sorption air in process air drying.
The design principles for drying components align with those for blowers or compressors. They must be sized according to system requirements to reduce internal pressure losses through optimal airflow.
These must otherwise be compensated with increased energy expenditure. During the drying process, it is vital to ensure the rotor does not release any sorbent into the air, potentially compromising purity.
Air Supply Decisive for Efficiency
The generation and drying of process air consume a significant amount of energy. Nevertheless, it is not the sole determining factor in the operational efficiency of a pneumatic conveying system.
While optimizing system configurations can boost efficiency by carefully choosing components and planning pipework routes, it is equally important to prevent energy loss.
This is where heat recovery systems come into play. They can harness the waste heat from ongoing processes and utilize it to enhance sustainability.
The foundation for achieving this lies in efficient overall concepts. Therefore, AERZEN does not merely provide a broad range of products and services for generating process air. Its application experts also concentrate on seamlessly integrating their components into complex process air circuits.
Integrated Planning is Key to Success
Proper blower and compressor design can significantly reduce a plant's energy requirements for process air supply. Inappropriate components or incorrect settings not only lead to increased energy consumption but also result in higher long-term production costs due to malfunctions and wear and tear.
AERZEN offers three product series: positive displacement blowers (Delta Blower), rotary lobe compressors (Delta Hybrid), and screw compressors (Delta Screw) tailored to various applications.
These encompass compact assemblies for mobile use on self-unloading silo trucks and stationary plants for unloading bulk materials from transport ships. There is also the Alpha Blower modular system, capable of reliably providing large food companies with process air, boasting a maximum volume flow of 77,000 m³/h.
All these technologies operate oil-free and meet ATEX conformity, making them suitable for use in potentially explosive atmospheres.
Solutions for the Treatment of Process Air
Contaminants like dirt or dust particles, excessive air temperatures, and humidity can negatively impact product quality. On the outlet side of assemblies, other components step in to handle air treatment:
- Process air filter
- Aftercooler
- Dryer
In its accessory lineup, AERZEN offers complete, connectable filter elements ranging from separation classes F7 to H13. These filters can also be retrofitted into the plant before process air drying. Specifically designed for ambient air conditions, these filters remove dust and dirt, creating a particle-free environment.
During compression, temperatures can reach up to 280 °C. Such high-temperature air can harm bulk materials and system components, which is why cooling is achieved through coolers placed before the dryers.
Supported by a proprietary software solution, AERZEN selects aftercoolers from its delivery program and verifies the selection by simulating the operating data.
These components are available in air-to-air or water-to-air configurations. Special varnishes, unique motors, condensate separators, and intelligent controls provide flexibility to meet custom requirements.
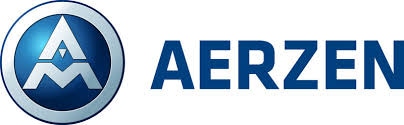
This information has been sourced, reviewed and adapted from materials provided by Aerzener Maschinenfabrik GmbH.
For more information on this source, please visit Aerzener Maschinenfabrik GmbH.