Advanced powder metallurgy (PM) techniques are utilized to synthesize high-performance components, such as high-performance alloys, with precise tolerances and complex shapes. High-performance alloys are used in applications requiring good fracture resistance and high strength. This article discusses advanced PM techniques and their impact on high-performance alloys.
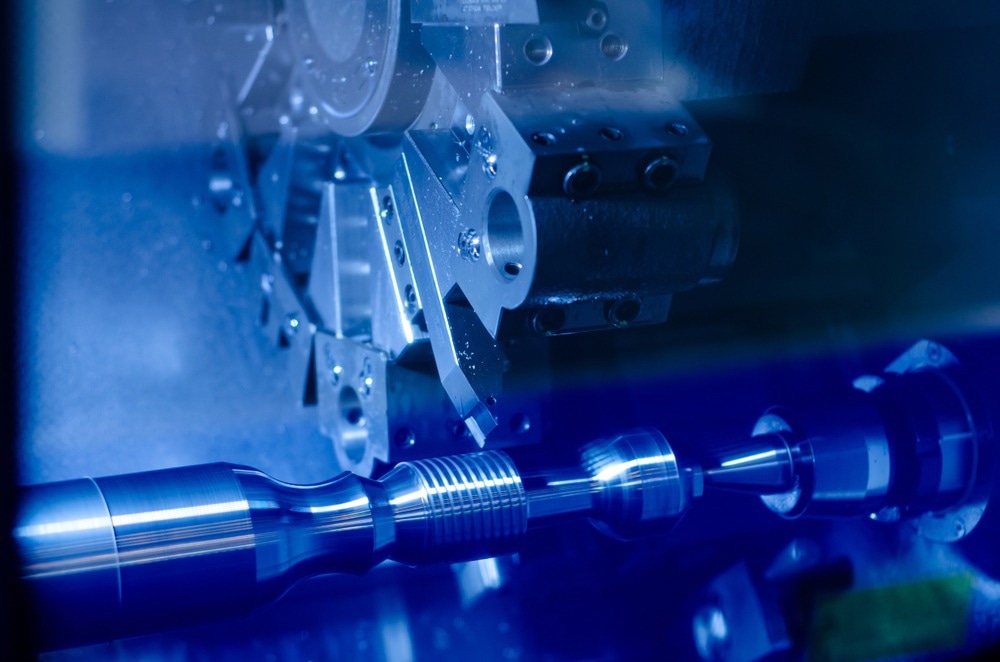
Image Credit: Lutsenko_Oleksandr/Shutterstock.com
Advanced PM Techniques
Advanced PM techniques, such as metal injection molding (MIM), spark plasma sintering (SPS), and hot isostatic pressing (HIP), are referred to as PM processes that employ advanced technologies to synthesize high-performance components.
SPS/pulsed electric current sintering (PECS)/ field assisted sintering technique (FAST) is an advanced PM technique that employs pressure and electric current to synthesize new or traditional materials in a single step.
The technique completes a sintering process within a few minutes compared to hours or even days required in conventional sintering. In SPS, high heating rates above 300 oC/min can be attained easily owing to the internal heating of the sample in place of external heating in conventional sintering, leading to a high sintering rate and a substantial reduction in sintering time.
Additionally, the simultaneous application of pressure and temperature leads to high densification. Thus, a dense compact can be easily obtained at significantly lower sintering temperatures compared to conventional sintering.
In SPS, high relative densities can be achieved within a very short time, and nano-sized powders can be sintered without significant grain growth as no grain growth and coarsening occur during the process. Thus, high-performance alloys can be prepared easily using SPS with fewer defects and more densification.
MIM has been developed by combining traditional PM and plastic injection molding (PIM) methods and is used to synthesize complex shapes in large quantities. The process uses fine metal powders that are custom formulated with a binder, such as different thermoplastics and waxes, into a feedstock.
The feedstock is then fed into a cavity of a conventional injection molding machine, where it cools and hardens to the mold die cavity shape. Most of the binder is extracted by solvent or thermal processing, while the rest is removed when the component is sintered in a controlled atmosphere furnace.
MIM is a net-shape process technology with good dimensional tolerance control, which makes it excellent for making parts with an intricate design with high precision. However, the process requires high temperatures to sinter, which is a major disadvantage as these heating requirements can substantially increase the manufacturing cost.
In HIP, high temperatures of up to 2200 oC and an isostatic pressure of 200–500 MPa are applied uniformly to the powder compact at the same time in all directions through an impermeable membrane to consolidate powder particles into a solid form. Argon is primarily used as the pressure medium in this process.
Components with full density with no open porosity and limited grain growth can be directly realized using HIP without encapsulation. However, potential surface contamination, distortion, and batch-to-batch variability of distortion and contamination are the major disadvantages of this advanced PM process.
Impact of Advanced PM Techniques
In a paper published in the journal Materials Chemistry and Physics, researchers investigated the feasibility of using the field-assisted PM techniques to synthesize high entropy alloy (HEA) FeCoNiCrAl containing iron (Fe), cobalt (Co), nickel (Ni), chromium (Cr), and aluminum (Al) at equimolar composition starting from metal powders mixture.
Researchers selected FeCoNiCrAl for field-assisted processing owing to its unique precursor composition that includes at least one ferromagnetic element and one highly reactive element couple, such as Al-Ni.
The exothermic reaction between the highly reactive element couple can provide additional heat to the system during the sintering process sintering, which can reduce the overall sintering time and temperature.
Mechanically alloyed, mechanically activated, and mixed powders were used in this study. The powders obtained only by mechanical alloying were synthesized using SPS, while the remaining powders were sintered either using SPS or microwave heating. The use of FASTs resulted in negligible contamination by the surrounding environment, extremely short alloying time, and high energy density on the load.
In the X-ray diffraction patterns of the FeCoNiCrAl synthesized using the SPS technique at several temperatures, including 1000 °C and 1250 °C, and with different precursor preparations, including mixed, mechanically activated, mechanically pre-alloyed, all samples after sintering demonstrated the mixed face-centered cubic/body-centered cubic structure.
The microstructure displayed a lack of compositional homogeneity due to the fast consolidation and synthesis of FeCoNiCrAl HEA. No pores were present in the synthesized samples due to the use of the pressure-assisted sintering technique.
Although the utilization of high-temperature SPS and mechanically pre-alloyed powders led to better homogeneity of the resulting HEA, some partially reacted Cr particles were still present due to their larger particle size.
Both the elastic modulus and hardness of the microwave-processed samples were lower compared to the SPS-processed samples, owing to the significantly higher porosity of the microwave-processed samples.
In another study published in the journal Materials, researchers synthesized FeAl20Si20Mo20-XNiX (X corresponding to 5–15 wt %) alloy containing Fe, Al, silicon (Si), molybdenum (Mo), and Ni using short-term mechanical alloying and SPS for compaction.
The synthesized alloy displayed an ultrafine-grained microstructure with 200 nm or smaller dimensions of phases. Moreover, the addition of Ni and Mo to the FeAl20Si20 alloy led to the formation of the AlMoSi phase in the FeAl20Si20 alloy, which initially contained three phases, including Fe3Al2Si3, Fe3Si, and FeSi.
All alloys demonstrated a higher hardness, with the hardness of the FeAl20Si20Mo5Ni15 alloy reaching up to 1401 HV 1. The FeAl20Si20Mo5Ni15 alloy contained 58.5% of the FeSi and Fe3Al2Si3 phases.
Thus, all synthesized alloys demonstrated one order magnitude lower wear rates, ranging from 3.14 to 5.97 10−6 mm3 N−1 m−1, and substantially lower friction coefficients compared to two reference tool steels.
Although the alloys realized high compressive strengths of up to 2200 MPa, they displayed high brittleness even after long-term annealing, which decreased their strength below 1600 MPa.
Additionally, the alloys showed ductile behavior when compressively evaluated at a high temperature of 800 °C, and a superior oxidation resistance due to the formation of a compact aluminum oxide protective layer.
More from AZoM: How Does Stainless Steel Compare to Carbon Steel?
References and Further Reading
Průša, F., Proshchenko, O., Školáková, A., Kučera, V., Laufek, F. (2019). Properties of FeAlSi-X-Y Alloys (X,Y=Ni, Mo) Prepared by Mechanical Alloying and Spark Plasma Sintering. Materials, 13(2), 292. https://doi.org/10.3390/ma13020292
Colombini, E., Rosa, R., Trombi, L., Zadra, M., Casagrande, A., Veronesi, P. (2018). High entropy alloys obtained by field assisted powder metallurgy route: SPS and microwave heating. Materials Chemistry and Physics, 210, 78-86. https://doi.org/10.1016/j.matchemphys.2017.06.065
Novák, P. (2019). Advanced Powder Metallurgy Technologies. Materials, 13(7), 1742. https://doi.org/10.3390/ma13071742
Koss, D. A. (1985) Advanced Processing And Properties Of High Performance Alloys [Online] Available at https://apps.dtic.mil/sti/pdfs/ADA163469.pdf (Accessed on 30 October 2023)
Spark Plasma Sintering [Online] Available at https://www.iitk.ac.in/biomaterialslab/Spark%20Plasma%20Sintering.pdf (Accessed on 30 October 2023)
Metal Injection Moulding [Online] Available at https://www.sciencedirect.com/topics/engineering/metal-injection-moulding (Accessed on 30 October 2023)
Metal Injection Molding [Online] https://www.mpif.org/IntrotoPM/Processes/MetalInjectionMolding.aspx (Accessed on 30 October 2023)
Hot Isostatic Pressing [Online] Available at https://www.sciencedirect.com/topics/materials-science/hot-isostatic-pressing (Accessed on 30 October 2023)
Disclaimer: The views expressed here are those of the author expressed in their private capacity and do not necessarily represent the views of AZoM.com Limited T/A AZoNetwork the owner and operator of this website. This disclaimer forms part of the Terms and conditions of use of this website.