For much of human history, the process of manufacturing parts involved subtraction. Unformed materials underwent cutting to remove sections to achieve the intended results. However, in the 1970s, a new manufacturing revolution was beginning.
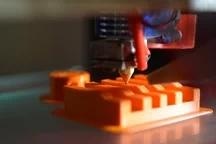
Image Credit: LECO Corporation
Computer-aided designs (CAD) directed lasers toward powdered metal, melding it into a solid form. For the first time, this process introduced additive manufacturing, where ultrafine layers were applied to generate the final product.
Analytical techniques such as glow discharge spectroscopy can facilitate bulk elemental analysis and quantitative depth profiling of materials, offering insights into elemental composition and composition gradients.
A well-equipped metallographic laboratory is also a key resource for assessing the layer morphology and quality of additive samples during both the development and production stages.
Additive manufacturing found its niche in rapid prototyping, crafting scale models or limited quantities of parts for design testing before transitioning to large-scale production.
As time progressed, additive manufacturing underwent refinements and iterations. This evolution enabled incorporating a broader range of materials, unlocking various possibilities.
Prominent technology companies developed tools capable of handling additive printing or made with parts produced through additive methods.
With the expiration of early patents, many other companies entered the additive manufacturing business, resulting in a surge in development and understanding. The term "3D printing" became commonplace among the general public, and additive manufacturing gained widespread acceptance.
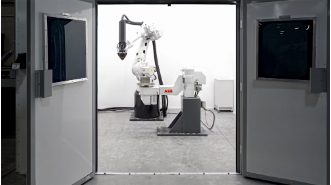
Image Credit: LECO Corporation
Like with most technologies, as additive manufacturing progressed, it became more affordable and user-friendly for production lines. Certain industries, such as aviation, found the advantages of additive manufacturing particularly appealing.
The technology enabled the production of previously impractical parts, like hollow components with internal support trusses. This innovation significantly reduced weight without compromising strength or integrity, enhancing the efficiency of applications like jet engines.
Despite its advantages and growth, additive manufacturing is not flawless; maintaining stringent quality control for the manufactured parts remains as crucial as ever.
Analytical techniques such as glow discharge spectroscopy can facilitate bulk analysis and quantitative depth profiling of materials, offering insights into elemental composition to ensure correct layering.
A well-equipped metallographic laboratory is also a key resource for assessing the strength and quality of material samples during both the development and production stages.
LECO provides a comprehensive solution for your additive manufacturing analysis requirements. From the initial sample cut to the final sputter in a GDS900, LECO's integrated solutions work seamlessly to ensure a smooth transition for your additive manufacturing products from inception to completion.

Image Credit: LECO Corporation
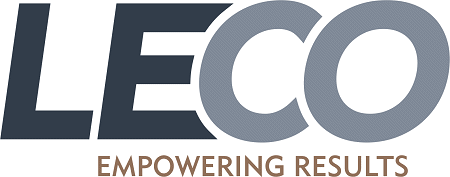
This information has been sourced, reviewed and adapted from materials provided by LECO Corporation.
For more information on this source, please visit LECO Corporation.