The ISO 15630-3, ASTM A416 and ASTM A1061 test standards offer guidelines for testing steel strands. Manufacturers of steel strands are required, through product standards, to test their products using both static and dynamic conditions.
To minimize equipment costs, these tests are frequently outsourced to a service provider. The manufacturers are also externally monitored by independent institutes.
One of the primary quality assurance tests involves static tensile testing with strain measurement. ZwickRoell provides a standard configuration tensile testing machine capable of exerting forces up to 600 kN.
Due to the tendency of steel strands to unwind under tension, ZwickRoell employs special specimen-grip inserts to avert premature failure at unwanted locations.
In the high-cycle fatigue test, the steel strand must endure two million test cycles at a maximum frequency of 20 Hz. Specimen clamping poses a unique challenge in this scenario, as clamping fractures can easily occur.
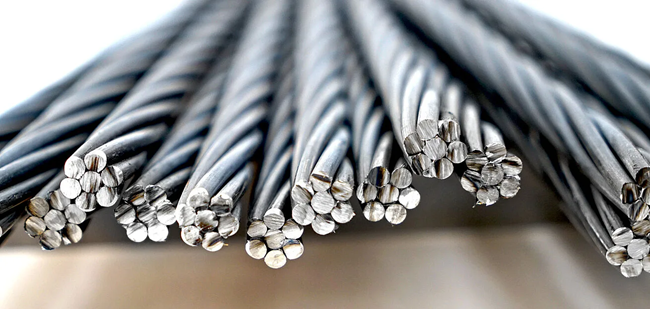
Image Credit: ZwickRoell GmbH Co. KG
Static Tensile Tests on Steel Strands to ISO 15630-3/ ASTM A416/ ASTM A1061

Image Credit: ZwickRoell GmbH Co. KG
In static tensile tests according to ISO 15630-3, ASTM A416, and ASTM A1061, the steel strand undergoes elongation until it fractures. Steel strands are composed of multiple wires twisted together, and they tend to untwist when subjected to tensile loads.
Throughout the tensile test, both the force applied to the specimen and its elongation are measured. Testing machines designed for high test loads are predominantly utilized because prestressing steel is a high-strength steel.
Tensile tests can be conducted on steel strands ranging from 3 to 20 mm in diameter. Depending on the product or test standard, the gauge length L0 can be, for example, 500 mm or 610 mm. The total elongation can reach values of up to 20 %.
Deflected tensile tests, as outlined in EN ISO 15630-3, can also be performed. In these tests, the moving crosshead of the testing machine is equipped with a through-hole.
Key Characteristic Values From Tensile Testing on Steel Strands to ISO 15630-3 and ASTM A416
- The yield point, often referred to as offset yield (Rp0.2), is typically determined as the replacement yield point at 0.2 % plastic elongation
- The yield point elongation, more precisely known as yield point extensometer elongation, can only be determined by using an extensometer (Ae)
- Tensile strength (Rm)
- Uniform elongation (Ag)
- Strain at break (A), with normative specifications concerning the gauge length being of significant importance
Tensile Test on Steel Strands and Prestressing Steel
Tensile test on rebars and strand wires: non-contact measurement with videoXtens
Video Credit: ZwickRoell GmbH Co. KG
Dynamic Tests on Prestressing Steel Strands
In the high cycle fatigue test (for example, according to ISO 15630-3, XP A 35-045-2011, FprEN 10138-3:2009) on steel strands, the specimen must withstand two million test cycles at a maximum frequency of 20 Hz without fracturing.
If the specimen fractures near or in the grip, the test is considered invalid and needs to be repeated. Invalid tests are very costly, as the fatigue test lasts several days. Prestressing steel strands, being highly stiff, are particularly sensitive to notching.
The gripping force imposes an additional load in the clamping area on top of the dynamic test load, which may result in premature specimen failure.
For classic tensile specimens made of solid material, the ends often have larger cross-sections to ensure that the specimen fractures in the ungripped section between the grips. This is not so simple with wire strands.
ZwickRoell has established a specialized specimen grip for steel strands, allowing high-cycle fatigue tests to be conducted without the need for specially attached gripping elements.
These high-cycle fatigue tests are generally carried out using an HA series servohydraulic testing machine.
Specimen Clamping
It is crucial to prevent specimen damage from clamping (such as a pyramid pattern on the jaw inserts) because of the high tensile strength of the individual steel strand wires, reaching up to 2000 MPa, and their smooth surface.
Hydraulic, parallel-closing specimen grips with adaptable clamping pressure are, therefore, necessary. The geometry of the jaws must be designed to ensure dependable and homogenous gripping of the specimen, preventing slippage of the specimen during the test.
The product quality of the steel strand specimen is also essential to prevent breakage of the specimen outside the gauge length L0.
During a tensile test, only specimen tears or breaks within the gauge length can be considered a reliable test result. A damaged specimen surface or significantly inhomogeneous tensile strength of the individual wires can result in specimen breakage outside L0, near the jaws.
Clamping the specimen in a high cycle fatigue test on steel strands, following ISO 15630-3, poses a specific challenge due to the relatively easy occurrence of clamping fractures.
The gripping force introduces an additional load in the clamping area to be superimposed on the dynamic test load, which can result in premature failure of the specimen.
For classic tensile specimens made of solid material, the ends often have larger cross-sections to guarantee that the specimen breakage occurs in the ungripped section between the grips. This is not so simple with wire strands. To achieve accurate test results, extensive specimen preparation, including sealing, is necessary.
ZwickRoell addresses this challenge with specially developed specimen grips for steel strand testing, offering the option to test strands without the need for specially attached gripping elements. This development significantly decreases the necessary handling, time, and expense for the user.
The grips incorporate hydro-mechanical and purely mechanical gripping. The latter comprises a conical sleeve into which each end of the strand is fed, along with a counter-cone, and clamped. Much of the gripping force is applied through this method.
The remaining force still needed for the specific test is supplied by classical hydro-mechanical clamping via jaws. Combined, these two gripping principles allow the gripping force to be applied in such a way that clamping fractures are eradicated and steel strands can be tested without being pretreated.
The specimen grips are highly flexible and suitable for a broad range of applications. The variably adjustable hydraulic gripping force can be simply modified from test to test by regulating the oil pressure accordingly.
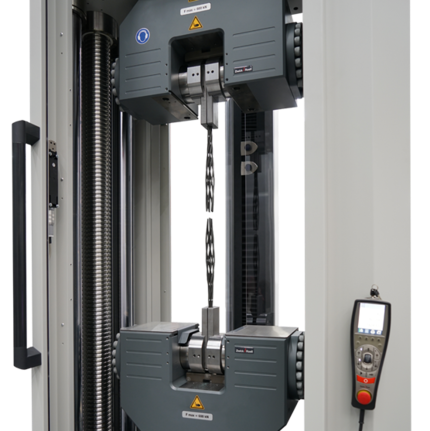
Image Credit: ZwickRoell GmbH Co. KG
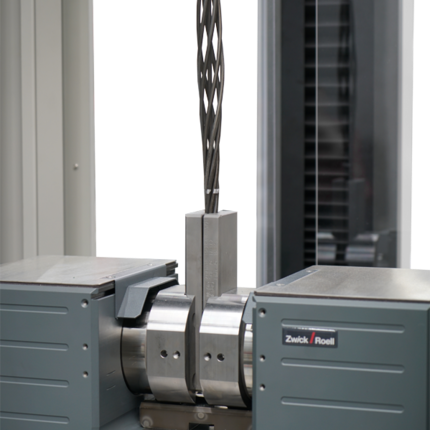
Image Credit: ZwickRoell GmbH Co. KG
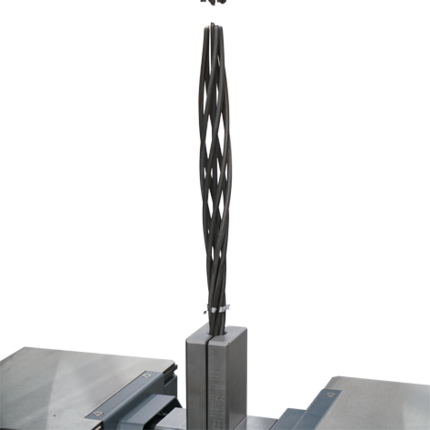
Image Credit: ZwickRoell GmbH Co. KG
Strain Measurement
A fracture in the steel strand commonly causes the deflection of individual wires, posing a risk of damaging a sensor arm extensometer. To ensure safe, reliable, and accurate measurements on highly extensible and elastic materials, ZwickRoell chooses optical extensometers.
The videoXtens 6-680 extensometer, with a field of view of 680 mm and a resolution of 0.6 µm, enables precise strain measurements, even in cases involving long gauge lengths, as seen in tests on steel strands. Key features include:
- Determination of yield strength according to ASTM A1061
- No risk of extensometer damage at the point of fracture, as the extensometer measures without direct contact
- Automatic calculation of strain at break
- Through a connection to the crosshead, the gauge marks consistently remain at the center of the field of view (FOV), ensuring optimal utilization of the measurement range
Additional benefits of this extensometer include automatic recognition of gauge marks on the specimen and the initial gauge length, coupled with the transmission of all data to the testXpert testing software.
What Is Prestressing Steel?
Prestressing steel, a high-strength steel, is mainly utilized in the construction of prestressed concrete. The application of prestressing steel facilitates a significant increase in the properties of concrete components for both static and dynamic loads.
The manufacturing of prestressing steel involves a long steel product, and its surface shape varies based on the manufacturing standard. For instance, an individual wire is designed as per the manufacturer standard DIN EN 10138-1, while a steel strand may be designed according to DIN EN 10138-3.
The individual wire exhibits strength values of up to 2000 N/mm² and is typically designed in a round shape, whereby trapezoidal cross-sections, referred to as compact strands, are also possible.
Within the general heading of prestressing steel, there are three forms, depending on the product standard:
- Bar steel (diameter 15 to 36 mm)
- Wire (diameter 5 to 16 mm)
- Steel strands composed of 3, 7, or more twisted individual wires (three-wire strand: 5.2 to 7.5 mm, seven-wire strand: 7 to 18 mm)
These diverse forms necessitate high demands on materials testing, and, as a result, various test standards (for example, ISO, ASTM, and so on) are employed to ensure adherence to the required quality standard.
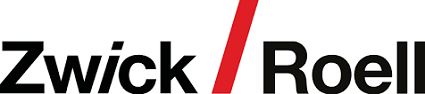
This information has been sourced, reviewed, and adapted from materials provided by ZwickRoell GmbH Co. KG.
For more information on this source, please visit ZwickRoell GmbH Co. KG.