The properties of both the adhesive and the joined materials determine the long-term performance of a bonded joint.
High temperatures, as well as exposure to water or chemicals, are all agents that can affect the adhesive direclty. But, the durability of the joint will also be influenced by the extent to which these agents impact the materials being joined.
Most importantly, joint durability will be determined by the conditions of the joint surfaces at the time of bonding. The best joints are formed when the surfaces are completely clean and wetted with the adhesive.
To ensure the durability of bonded joints, surface pretreatment must be carefully controlled. A poor surface condition typically results in a relatively low initial strength and decreased durability. A thick bond line reduces initial strength (Figure 1).
Heat is used to complete the curing process in most reactive adhesives, which enhances both initial strength and durability.
The user must assess the level of control required for these factors to create a bonded joint that meets the expected service conditions. For many applications, surface pre-treatment, bond-line thickness control, and cure-schedule monitoring provide adequate durability.
Shear strength decreases as the bond line thickens. The diagram shows the effect of increasing bond line thickness in simple lap joints made with cured epoxy adhesives (Figure 1).
The optimal bond line thickness ranges from 0.1 to 0.5 mm. In very thin bond lines, there is a risk of insufficient joint filling due to contact between high points on the joint surfaces.
The bonded joints may have to withstand sustained loads, either static or cyclical. Joint designs that minimize peel stresses provide the best durability. Cyclical fatigue testing of simple lap shear joints made with epoxy adhesives typically yields failure values of around 30% of the static breaking load (Figure 2).
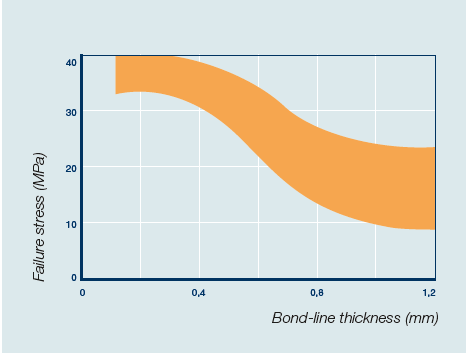
Figure 1. Bond line thickness vs. Shear strength. Image Credit: Huntsman Advanced Materials
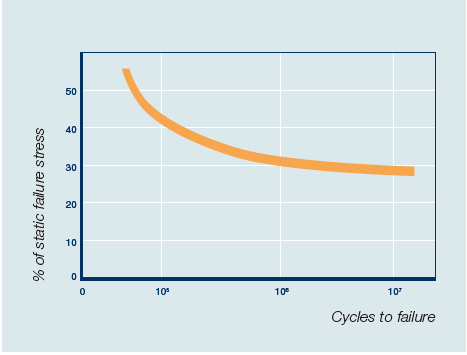
Figure 2. Fatigue strength (Tensile) of lap joints. Image Credit: Huntsman Advanced Materials
The adhesive strength at the interface is inherently greater than the cohesive strength within the adhesive. The diagram demonstrates that this adhesive's strength decline occurs between 0.4 to 1.0 mm. Shear strength is approximately constant for thicknesses greater than 1.0 mm.
The exact shape of the curve is determined by the characteristics of the adhesive. Toughened adhesives will sustain higher values in thicker bond lines, while more rigid adhesives will decline faster.
Adhesives are frequently used in applications involving both dynamic and static stresses. Small, repeated loads can cause fatigue cracking. These cracks may propagate over multiple load cycles, eventually leading to joint failure.
Cyclical lap shear testing can be used to assess the fatigue resistance of an adhesive joint. A load is applied repeatedly, and the number of cycles until failure is recorded. The load can be adjusted to provide a complete picture of fatigue performance.
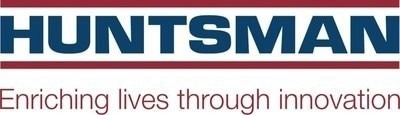
This information has been sourced, reviewed and adapted from materials provided by Huntsman Advanced Materials.
For more information on this source, please visit Huntsman Advanced Materials.