Adhesives are often exposed to variable stresses that impact their behavioral properties and capacity to endure strain without breakage. These features are vital when determining what adhesive will be the most suitable for a specific application.
Tensile testing evaluates the strength of a material when subjected to a load, as well as the strain (elongation) that takes place in the material as it is loaded. The results that tensile testing offers provide information on the strength, stiffness, and deformation at the breaking point of a material suffering from longitudinal stress.
Learning Lab: Assess Ability to Withstand Elongation With the Tensile Test
Assess the resistance of a material under tensile testing. Video Credit: Huntsman Advanced Materials
Testing Procedure
At Huntsman, the tensile properties of an adhesive are primarily established using the ISO 527-2 test standard. The test is performed by positioning cast or machined adhesive specimens in the grips of a universal testing machine and subjecting them to load increasing at a constant rate until the specimens fail.
To establish the overall material stiffness, a relatively slow rate is applied, known as Young’s modulus, followed by a faster rate to acquire ultimate tensile strength (UTS) and fracture elongation. Elongation and tensile modulus are determined using an extensometer.
Test Parameters
Specimens can be molded to fit the required dimensions or machined from cured products, such as cast sheets or moldings. The test specimens are referred to as dog-bone geometries: either Type 1B (4 mm thick) or Type 5A (2 mm thick).
Selection is dependent on the specimen preparation method and material flexibility. At least five specimens are subjected to testing for each required orientation. The results are often influenced by the testing speed of the specimens.
For ISO 527-2, the recommended test speeds are as follows:
- 5 mm/min for elongation < 100%
- 20 mm/min for elongation > 100%
Data Provided
Measuring tensile properties determines the following parameters:
- Tensile Strength - the magnitude of force that a specimen can endure before irreversible stretching or breakage occurs (in MPa).
- Tensile (Young's) Modulus - Young’s modulus is a measurement of the material’s stiffness and refers to the amount of stretching that a specimen experiences in response to an applied stress (in MPa).
- Elongation – how much a specimen increases in length at the point of yield or failure divided by the original length (in %). Greater elongation typically signifies a material with greater flexibility.
Tips for Modeling and Simulation
The following reference points should be taken into account when using tensile test results in numerical modeling:
- The model should consider the temperature dependence of the parameters of both elastic and plastic.
- The complete stress-strain curve at the given temperature should be leveraged for accurate simulation of elastoplastic behavior. When modeling, it should be noted that total elongation at the breaking point in tensile test reports encompasses both elastic and plastic components.
- To quantify stress-based failure criteria, the tensile strength parameter should be subtracted from the tensile test at the relative temperature.
- Potential strain rate has a bearing on the loading response which should be taken into account during analysis of the stress.
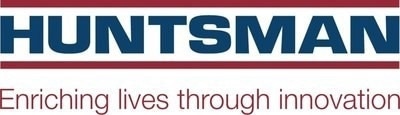
This information has been sourced, reviewed and adapted from materials provided by Huntsman Advanced Materials.
For more information on this source, please visit Huntsman Advanced Materials.