Adhesive bonding can provide reduced stress, increased stiffness, a more aesthetic appearance, and lower complexity for parts. All of these advantages can lead to several financial benefits, including simplified design, straightforward assembly, less weight (lower energy consumption), and longer service life.
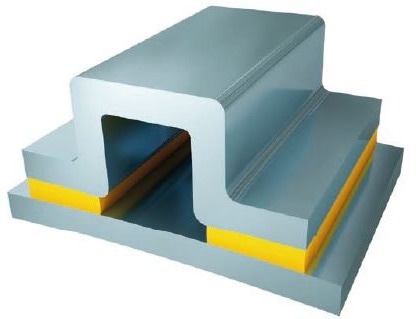
Figure 1A. Stiffening effect with bonding. The diagram shows how a joint may be designed to take advantage of the stiffening effect of bonding. Adhesive forms a continuous bond between the joint surfaces. Image Credit: Huntsman Advanced Materials
Advantages of Adhesive Bonding
Continuous Bond
When a load is applied, the stress is evenly distributed across the entire bond region. However, when spot welding or mechanical fasteners are used, the stress is highly concentrated in a few locations. Therefore, bonded assemblies typically have a longer service life under load.
Improved Appearance
Adhesive bonding makes parts appear smoother. There are no protruding fasteners, such as rivets or screws, and no spot weld marks.
Stiffer Structures
The continuity of a bonded assembly results in stiffer structures. On the other hand, if a higher stiffness is not required, the weight of the structure can be reduced while maintaining the necessary stiffness (Figures 1A and 1B).
Complex Assemblies
Other fastening techniques are often ineffective for joining complex assemblies. Composite sandwich structures are a common example of this phenomenon.
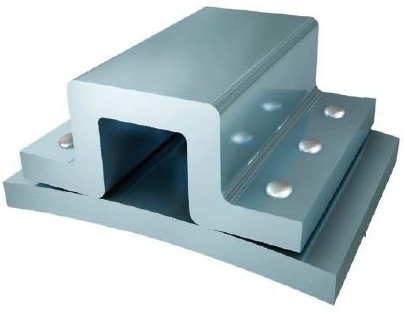
Figure 1B. Stiffening effect with riveting. Rivets and spot welds pin the surfaces together only at specifi c points. Bonded structures are consequently much stiffer and loading may be increased (by up to 30 - 100%) before buckling occurs. Image Credit: Huntsman Advanced Materials
Dissimilar Materials
Adhesives can join materials with different compositions, stiffnesses, coefficients of thermal expansion, or thicknesses.
Heat Sensitive Materials
Adhesive bonding does not need high temperatures, making it ideal for joining heat-sensitive materials susceptible to distortion or property changes (e.g. from the heat of brazing or welding procedures).
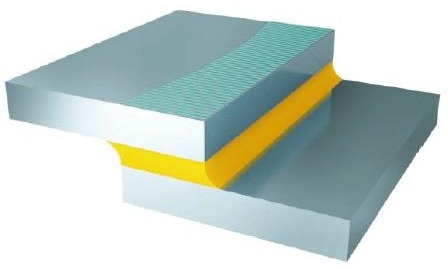
Figure 2A. Stress distribution in loaded joints with bonding. The bonded joint shown here is uniformly stressed. A welded joint would also show good stress distribution, but the heat of welding may reduce the metal’s properties in the vicinity of the weld, reducing overall strength. Image Credit: Huntsman Advanced Materials
Reduced Corrosion
The continuous adhesive bond creates a seal. As a result, the joint is leak-proof and corrosion-resistant.
Electrical Conduction
Some adhesives are specially designed to provide high electrical conductivity. This is particularly useful in electronic applications.
Electrical Insulation
Adhesive bonds can act as an electrical insulator between components.
Vibration Dampening
Adhesive bonds have excellent dampening characteristics, which can help reduce sound transmission or vibration.
Reduced Stress Concentration
A bonded joint may result in a fundamentally safer structure, as decreased stress concentration makes fatigue cracking less likely to occur. Fatigue cracks propagate more gradually in a bonded structure than in a riveted structure, or even in a solid machined part, because the bond lines typically prevent crack formation. (Figures 2A and 2B)
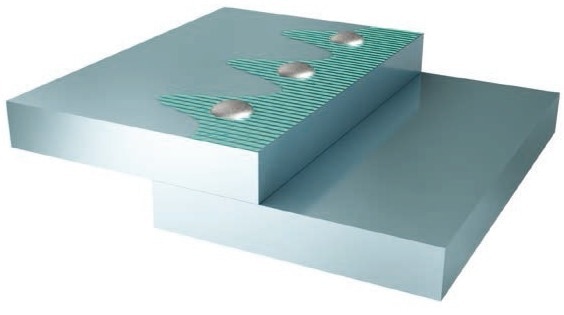
Figure 2B. Stress distribution in loaded joints with riveting. The riveted joint is highly stressed in the vicinity of the rivets. Failure tends to initiate in these areas of peak stress. A similar distribution of stress occurs with spot welds and bolts. Image Credit: Huntsman Advanced Materials
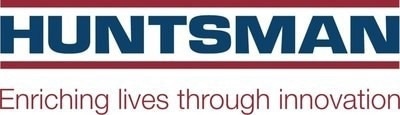
This information has been sourced, reviewed and adapted from materials provided by Huntsman Advanced Materials.
For more information on this source, please visit Huntsman Advanced Materials.