Almost all industrial products have components that must be joined together somehow. Mechanical fasteners like screws, rivets, and spot welds are commonly used, but engineers are increasingly choosing adhesive bonding. This assembly technique has been well-proven and can replace or supplement mechanical fasteners.
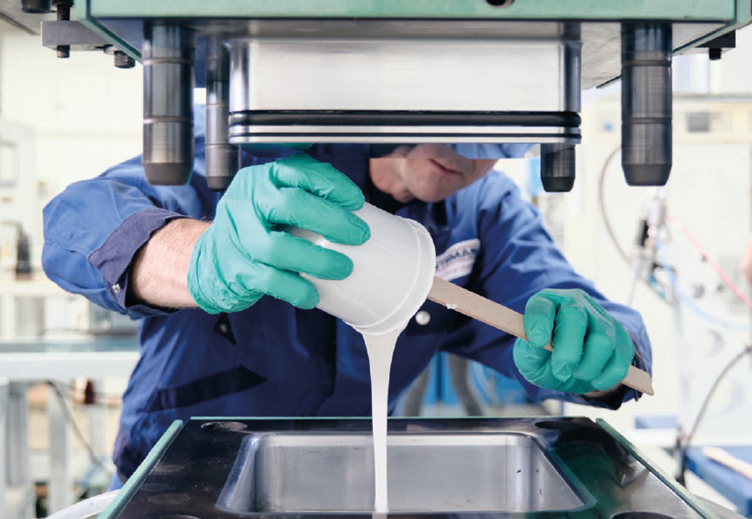
Image Credit: Huntsman Advanced Materials
Adhesive bonding offers several benefits, including:
- High lap shear and peel strength
- Reduced component and/or assembly costs
- Improved product performance and durability
- Enhanced design freedom
- Reduced finishing operations
Adhesive bonding is not a new topic; humans have used adhesives and glues since the beginning of time.
The ancient Egyptians used glue to attach veneers to furniture, and prehistoric man is thought to have used basic glues to attach arrowheads and digging tools. These early glues were derived from plants, tree resins, or animal parts.
Nowadays, synthetic resins and polymers are widely used, achieving far greater performance levels. When two components are linked together, the adhesive thoroughly wets the bonding surfaces, closing the gap between them before hardening to establish the bond.
Once hardened, the bond can endure the stresses that occur during use. High-performance adhesives typically harden through a chemical reaction and have a significant affinity for joint surfaces. Adhesive bonding is often known as chemical joining to distinguish it from mechanical joining.
Huntsman Industrial Adhesives
For many years, adhesives have been utilized successfully in highly demanding industrial applications such as aerospace, automotive, sport and leisure, wind energy, construction railways, and medical equipment.
Huntsman industrial adhesives create incredibly strong and long-lasting bonds with metals, plastics, rubber, glass, and various other materials. Designers in almost every industry have discovered that bonding with Huntsman adhesives can solve design issues posed by novel materials, applications, and manufacturing methods.
Huntsman industrial adhesives are simple to use. However, to ensure high-performance bonding, it is essential to carefully follow the instructions provided with the products.
Key Instructions for a Successful Bond
- Resin and hardener components must be precisely measured in the proper ratio (available in the technical datasheets) and thoroughly mixed together.
- Joint surfaces should be degreased and, if necessary, pre-treated.
- The minimum curing temperature and curing time must be observed (data provided in the technical datasheets)
- Jigs or other fixtures should be used to prevent the bond surfaces from moving relative to one another during the curing process
- Although only light pressure is required, it should be applied as uniformly as possible across the entire bond region. Excessive pressure could leave the joint with insufficient adhesive
Huntsman's Expertise in Adhesive Bonding
At Huntsman we develop adhesives that meet the needs of many industries and we focus on one goal: making our customers' ideas possible. Video Credit: Huntsman Advanced Materials
Designing to Bond
To get the best performance out of an adhesive bond, the component should be designed for a bonded joint rather than simply bonding parts designed for mechanical fastening. Methods for applying the adhesive and assembling the components should always be considered during the design stage.
These factors, along with the curing conditions, determine the type of adhesive used. Computer simulations are increasingly being used to design adhesively bonded structural joints. Simulations provide engineers with a reliable assessment of joint deformation and strength.
Comprehensive Material Models are available for the ARALDITE® adhesive range. Based on laboratory material characterization, the Material Models offer a wealth of information on the mechanical, physical, and thermal behavior of Huntsman products.
Material Models provide precise experimental data on adhesive mechanical properties (tensile and fracture), adhesion qualities (lap shear, peel), and curing phenomena (glass transition temperature, shrinkage, density, and hardness).
The use of ARALDITE® Material Models enables engineers to create robust adhesive joint simulations, assisting with adhesive selection and joint design while significantly lowering the amount of physical part testing required during the design process.
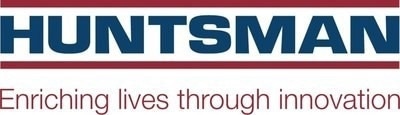
This information has been sourced, reviewed and adapted from materials provided by Huntsman Advanced Materials.
For more information on this source, please visit Huntsman Advanced Materials.