Slightly abraded surfaces offer superior bonding for adhesives compared to highly polished ones. After substrates are lightly abraded, thorough cleaning is necessary to eliminate all traces of dust or particles. Recommended cleaning methods post-abrasion include:
- Employing a suitable industrial vacuum cleaner to clean the surface (excellent choice)
- Gently brushing with a clean, soft brush (highly recommended)
- Repeating the degreasing process with clean degreasing liquids (recommended)
Plastics and Composites Surfaces
The top layer of molded plastic surfaces must be removed to guarantee that all traces of the release agent are eliminated. Like for metals, abrasion is often the preferred method, although grit blasting is frequently substituted with sanding, whether done manually or with the aid of a sanding machine.
Following abrasion, it is imperative to eliminate any loose particles. Peel (or tear) plies are commonly utilized on composite parts to achieve a surface primed for bonding: these are specialized fabrics applied onto the composite surface during molding and subsequently peeled off just before bonding, leaving behind a roughened and clean surface ideal for bonding.
Note:
It is best to use brushing, tack cloths or vacuum cleaning for the removal of loose particles from plastic surfaces. Plastics are known to carry static electrical charge, so care should be taken to avoid recontamination following cleaning. Bonding of the parts should occur as soon as possible.
Using degreasing liquids on specific plastics can adversely affect the abrasion treatment. Plastics are poor heat conductors, so care must be taken to ensure that grit blasting or sanding times are as short as possible to avoid overheating.
If pre-treating composites, cryo-blasting may be used. Cryo-blasting involves the use of solid carbon dioxide pellets as the blasting medium. This results in a clean, abrasive-free surface while avoiding heating.
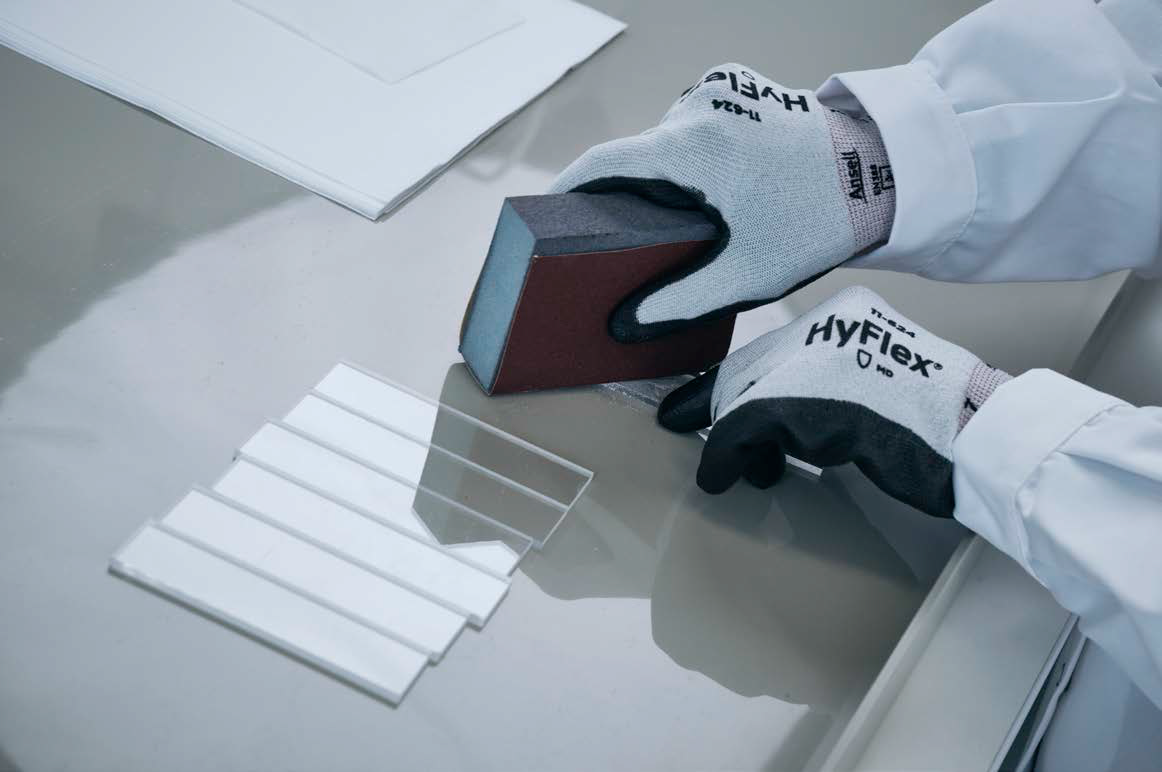
Image Credit: Huntsman Advanced Materials
Metal Surfaces
Remove surface deposits, such as oxidation, mill scale, or corrosion, by grit blasting with a suitable abrasive media. For most materials, fused alumina is the preferred choice, with silicon carbide being used less frequently. It is important to note that ferrous grits like chilled iron should only be used on mild steels and cast irons to prevent corrosion promotion on other metals.
Fused alumina is commonly used for aluminum alloys and stainless steels, while silicon carbide, although sharper, is more expensive and more prone to fracturing. However, Silicon carbide may be used on certain special alloys that are likely to react adversely with any residual fused alumina at temperatures they may encounter during service conditions. Its use may also be preferable for abrading materials that are either soft or extremely hard.
When choosing grit size, several factors should be considered, including the metal being grit blasted, the type of grit blasting equipment used, the pressure and angle of blast impact, and the duration of treatment.
Grit sizes ranging from 46 to 120 mesh (350 to 125 μm) are typically sufficient for most applications; however, the ideal grit size for specific applications may need to be determined through experimentation. Generally, for softer materials, the optimal grit size tends to be towards the finer end of the range.
Where grit blasting equipment is unavailable or where the metal is too fine to survive blasting treatment, joint surfaces can be cleaned using a wire brush or with abrasive cloth or paper (alumina or silicon carbide abrasive). A wet wire brush, abrasive cloth, or paper helps to remove contaminants and reduces dust. If necessary, dry the material and remove all loose particles.
Note:
Painted surfaces should be stripped of paint prior to bonding to avoid limiting the strength of the joint, as the adhesion of paint to metal is typically lower compared to that of the bonding material.
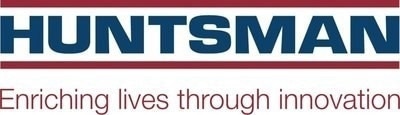
This information has been sourced, reviewed and adapted from materials provided by Huntsman Advanced Materials.
For more information on this source, please visit Huntsman Advanced Materials.